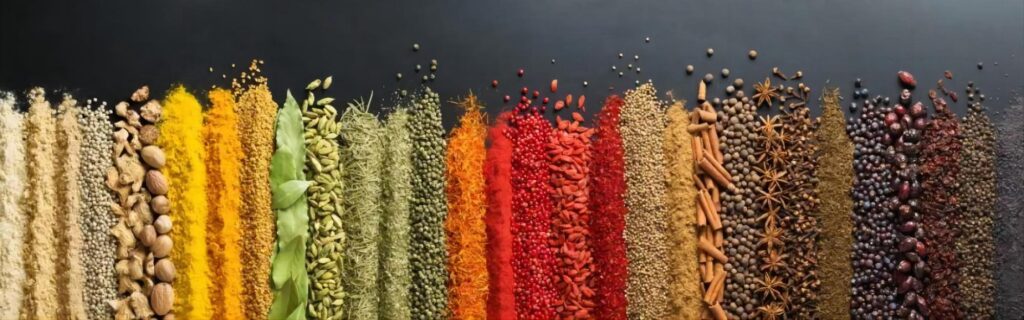
The new Euroma project is located in Zwolle, the Netherlands. The factory has taken over the company Intertaste and has successfully built the most innovative herb and spice factory in Europe.
As one of the leading producers of high-quality herb and spice blends and texturing solutions, they guided Daxner from Wels (Austria) in the design, manufacture and installation of fully automated factory solution systems around the well-proven Daxner Container Handling system distributed control system.
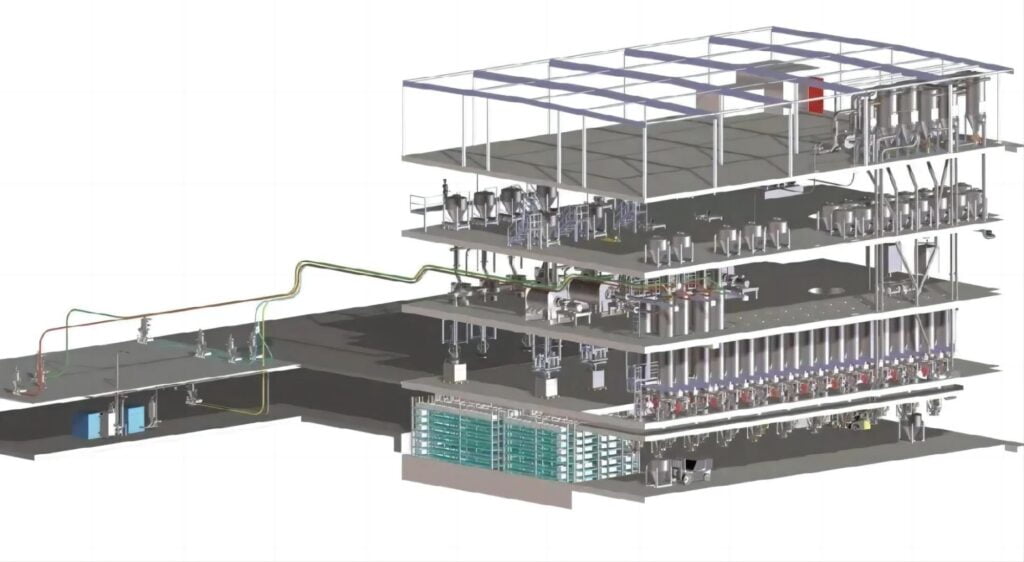
Cross-contamination control: batch design of turnover boxes to avoid cross-contamination
Dust control: production status after food grade dust control
Intelligence: Automatic guided vehicles replace manual labor
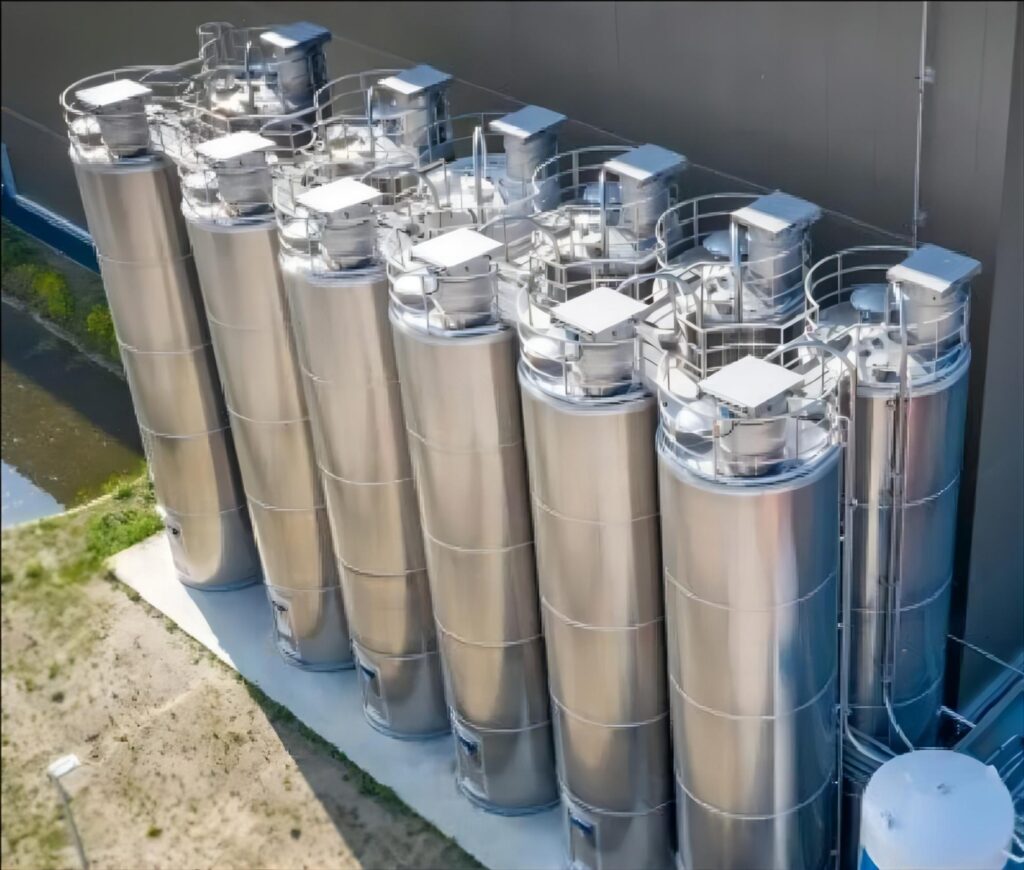
Herbal Flavors Producer
The spice factory became operational in 2019. Firstly, the plant enables Euroma, known as a pioneer in gentle herb processing, to increase production and reach new levels of food safety. Euroma’s goal is to unify the entire drying process at all existing plants at its new production site in Zwolle.
Mr. Teun van Veen, the Project Manager at Euroma, still clearly remembers the beginning of the project: “Euroma was preparing a visit to Powtech. By preparing a visitor list, we discovered that the company Daxner offered a complete concept for spices and herb plants. We found this on Daxner’s website A reference article was made. We were enthusiastic about what was written in that article. The first contact was made and we filled out our requirements on Daxner’s questionnaire and sent some additional information.” Subsequently at Powtech An initial meeting was held and Euroma placed its first factory pre-engineering order.
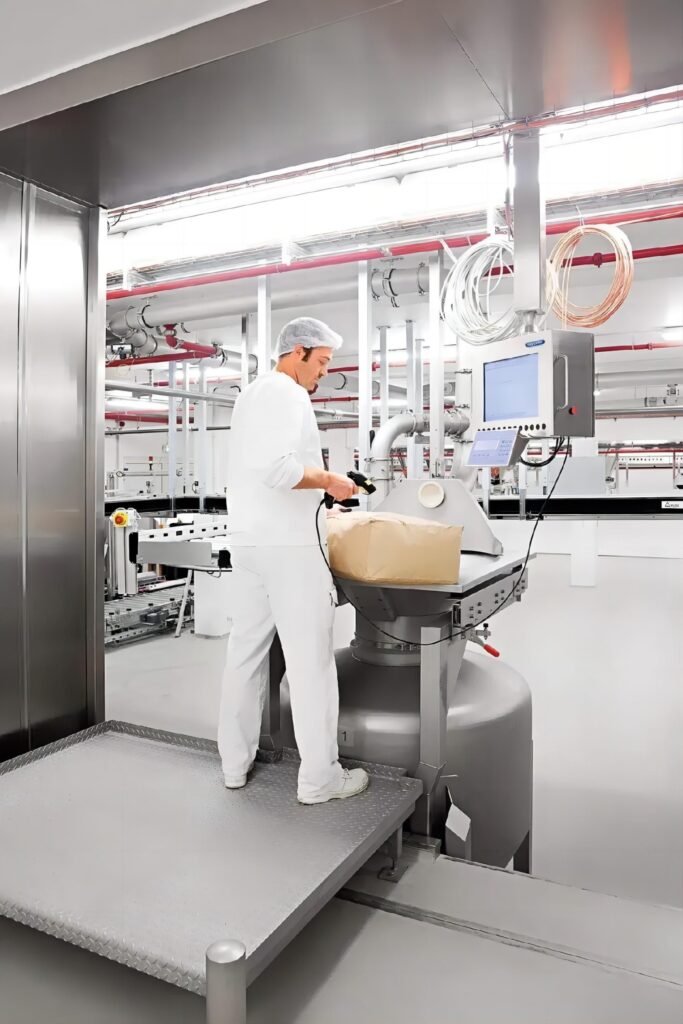
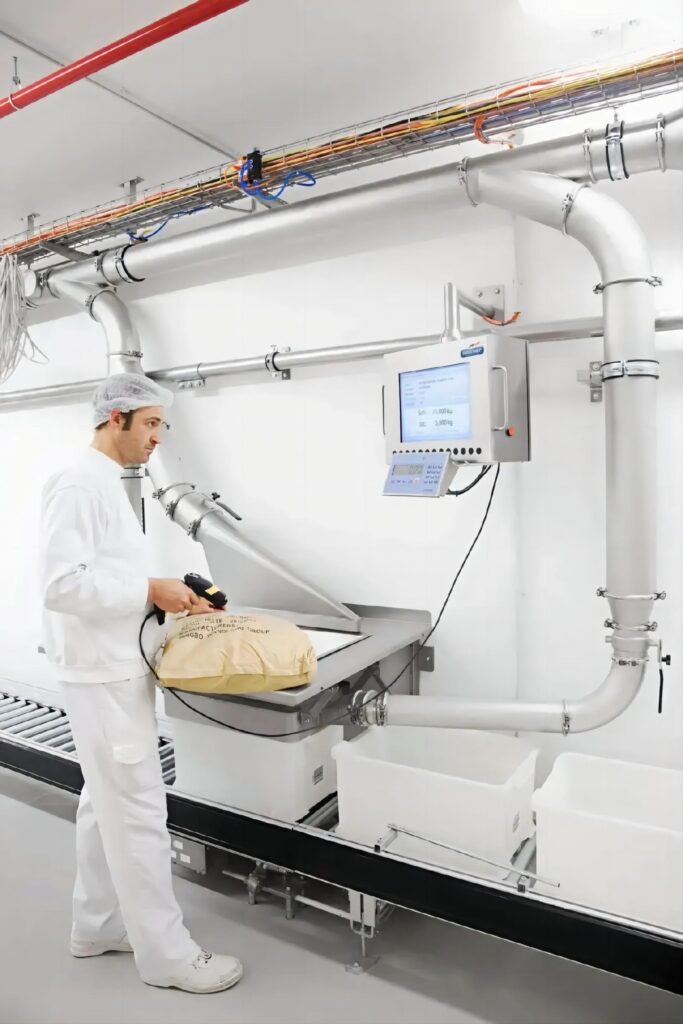
Fully automatic container handling system DCS
The technically impressive plant design guarantees high throughput performance and metering accuracy. The possibility of cross-contamination and dust formation is minimized.
In accordance with hygienic design requirements, all parts are made of stainless steel and are easy to clean. Laser-operated automated guided vehicles AGVs, perfectly synchronized with the fully automated Daxner container handling system DCS, move through the production facility to collect valuable dry parts. The raw material ingredients are divided into large ingredients, medium ingredients and small ingredients. Large proportions of carrier ingredients, such as wheat flour or potato and corn starch, are transported by tanker trucks and stored in 12 large outdoor silos. A pneumatic vacuum conveyor system transports them to daily totes within the factory.
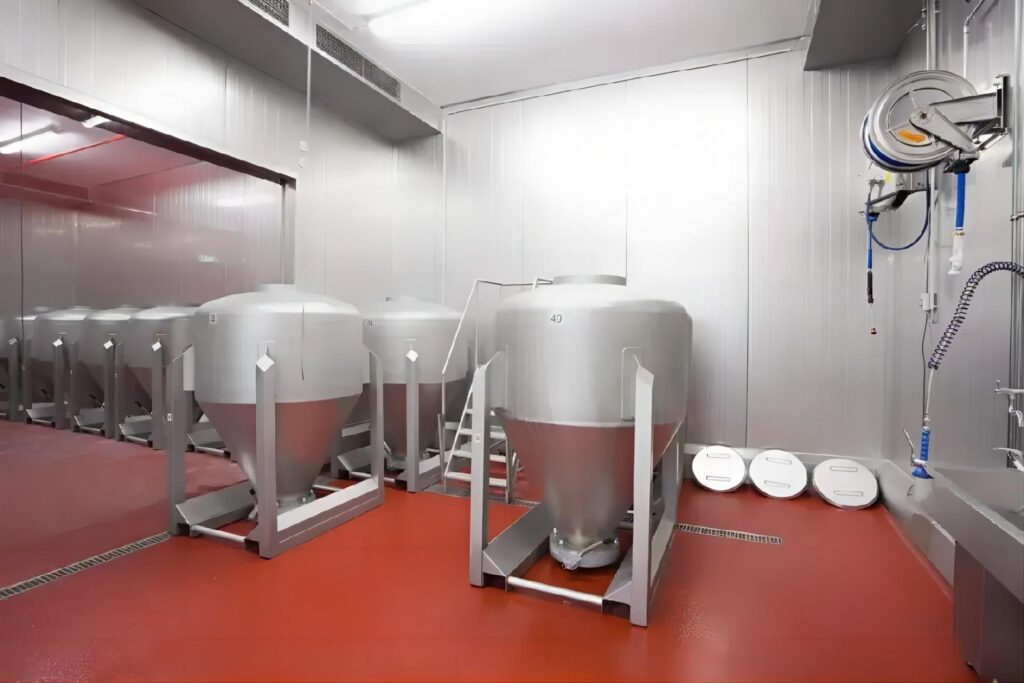
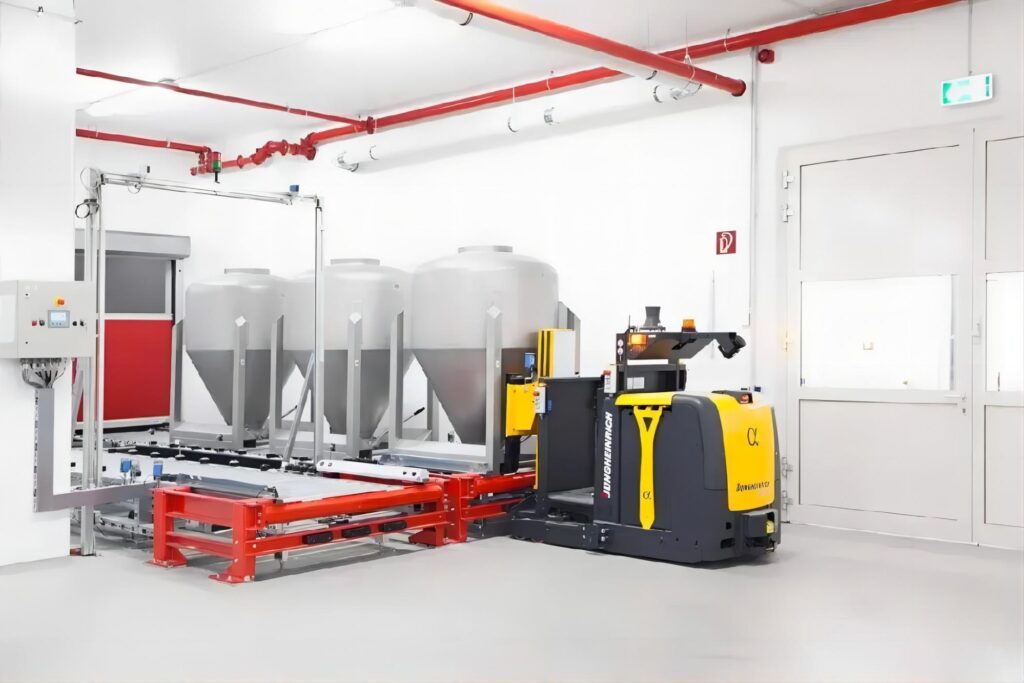
Mobile bag and ton bag import station
Filling of large and medium-sized parts into day totes is carried out via mobile bag and tote bag feeding stations. A high-precision scale is installed below the daytime turnover box. Depending on the quality of the product, separate daytime totes and weighing systems are assigned accordingly. This precise dispensing avoids cross-mixing with any allergenic raw materials.
Once all individual raw materials have been metered into weighing bins, the collection process of the Daxner Container Handling System DCS in combination with an automated guided vehicle AGV begins. An AGV loaded with a 1,500-liter container travels from weigh bin to weigh bin and fills itself with pre-weighed raw materials. This concept saves time: as soon as a raw ingredient is picked up, the weighing bin can immediately batch the next container.
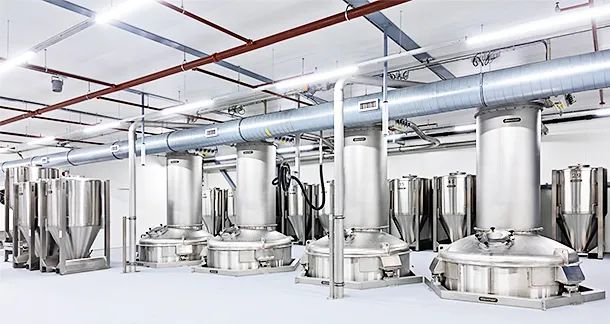
Supply of small and minor parts
Manual feeding of containers of small and minor parts takes place on the ground floor. According to the goods-to-person concept, all ingredients are brought to the operator: containers with AGVs, small parts in bags on pallets and pre-commissioned small parts in crates from the small parts storage (MCS). The system therefore achieves a time-optimized supply of all components without requiring the operator to act in unnecessary ways.
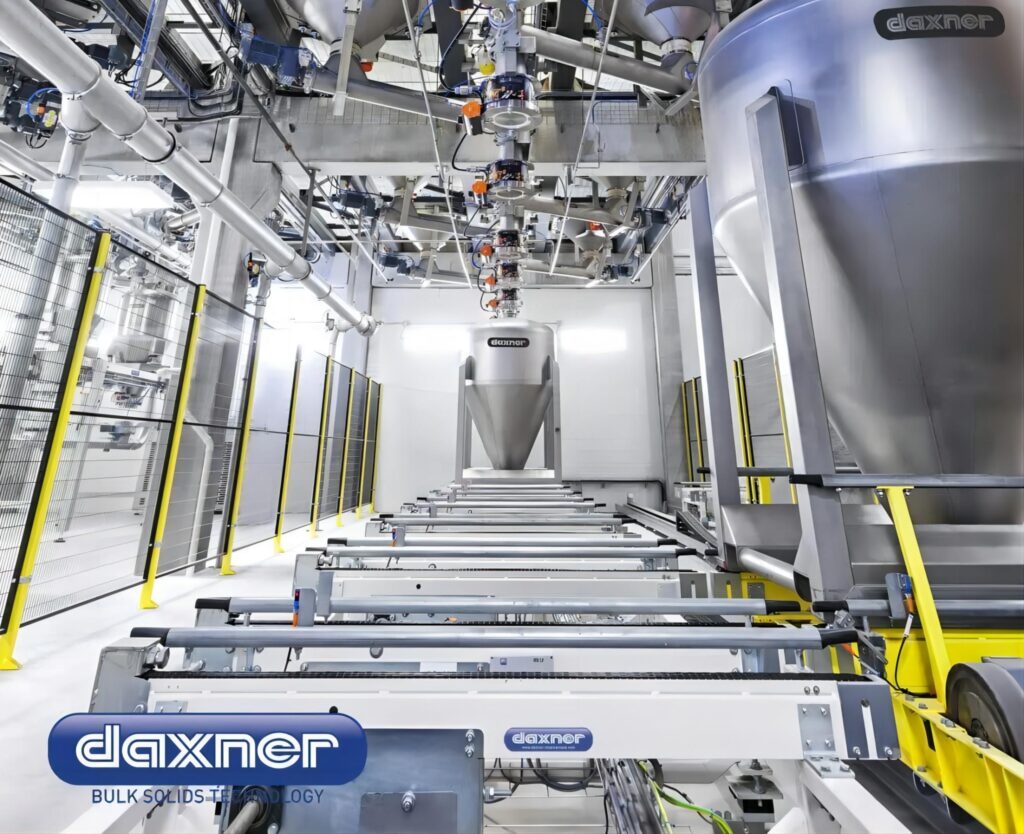
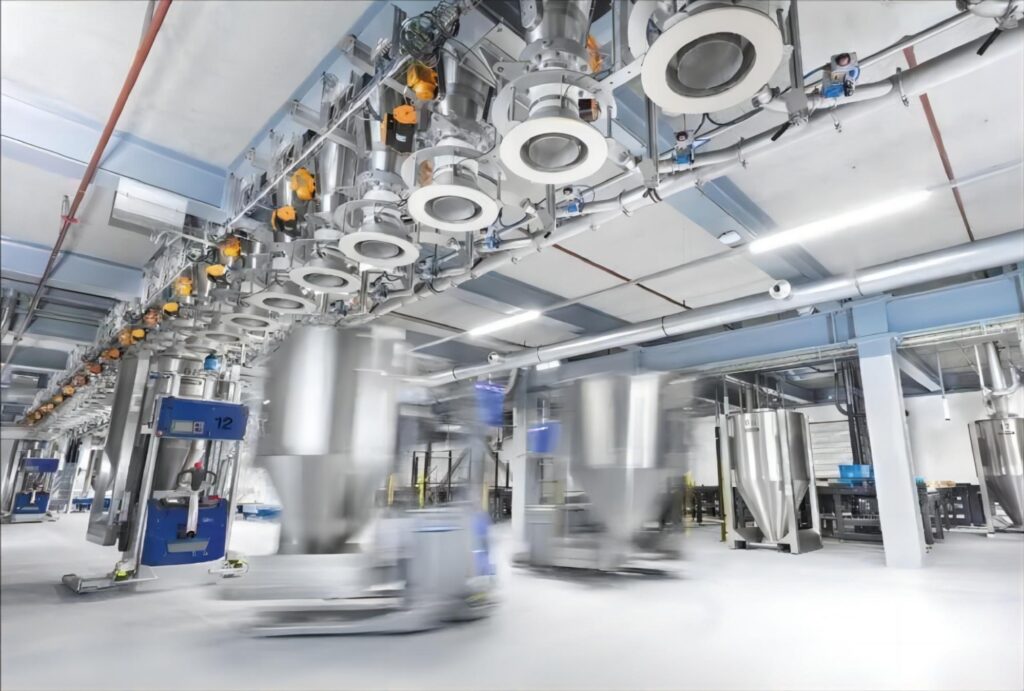
Once all ingredients are fed into the container, it continues its fully automated path to the designated mixing line. The containers are transported to the container lift with the help of AGVs and lifted to the floor above the mixer. From there, another AGV picks it up and places the container precisely above the corresponding mixer. Not only can the latch be opened, but the mixer can also be emptied without operator assistance. All products are quality controlled after the herbs, spices and other ingredients are blended. The finished mixture is weighed and packed into installed large bags and then fed to the corresponding packaging lines.
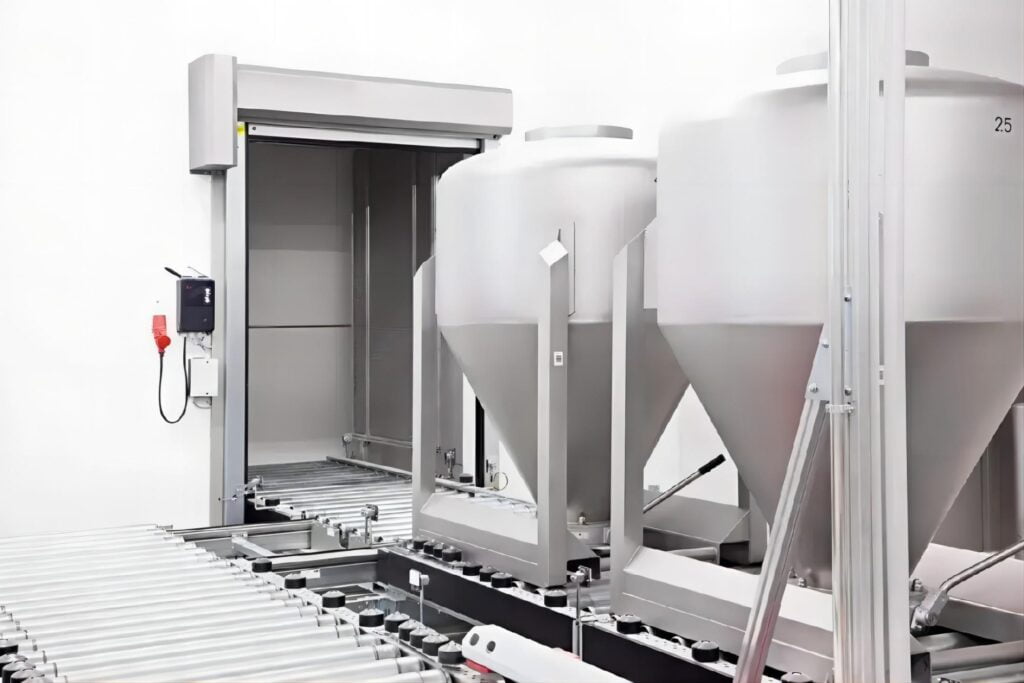
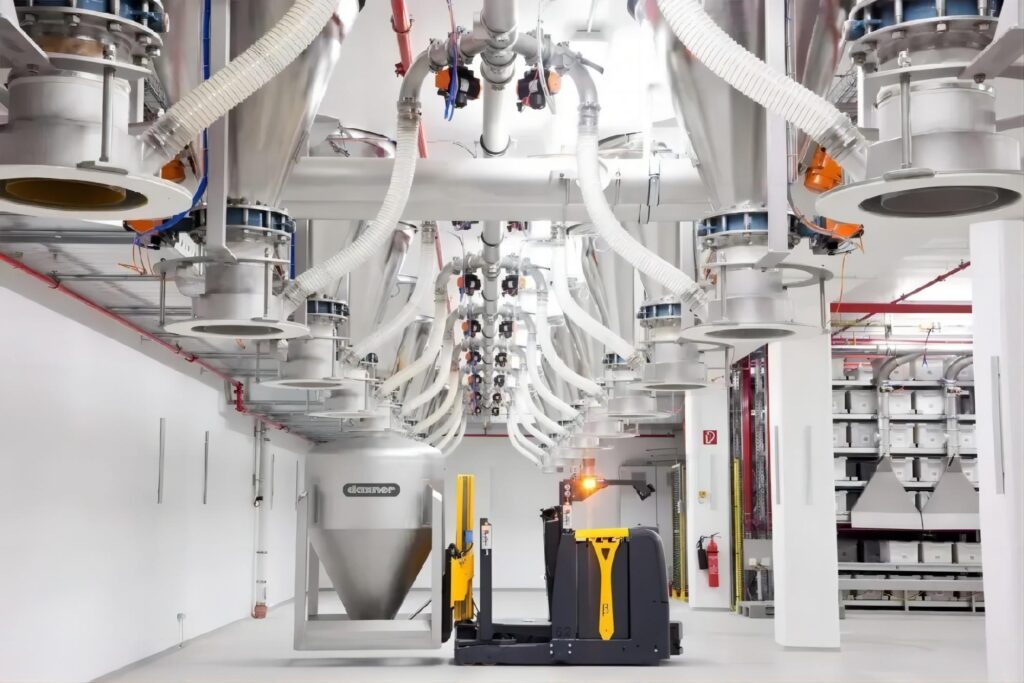
Various herbal mixer types offer great flexibility
Use a mixer with a capacity of 1500L to 10 cubic meters. Mixers can be supplied in various ways: directly from an outdoor silo, in a container or via liquid metering. After mixing, the product is poured directly into one of the downstream containers. The mixer and container dimensions are optimally matched and offer great flexibility in terms of possible batch sizes.
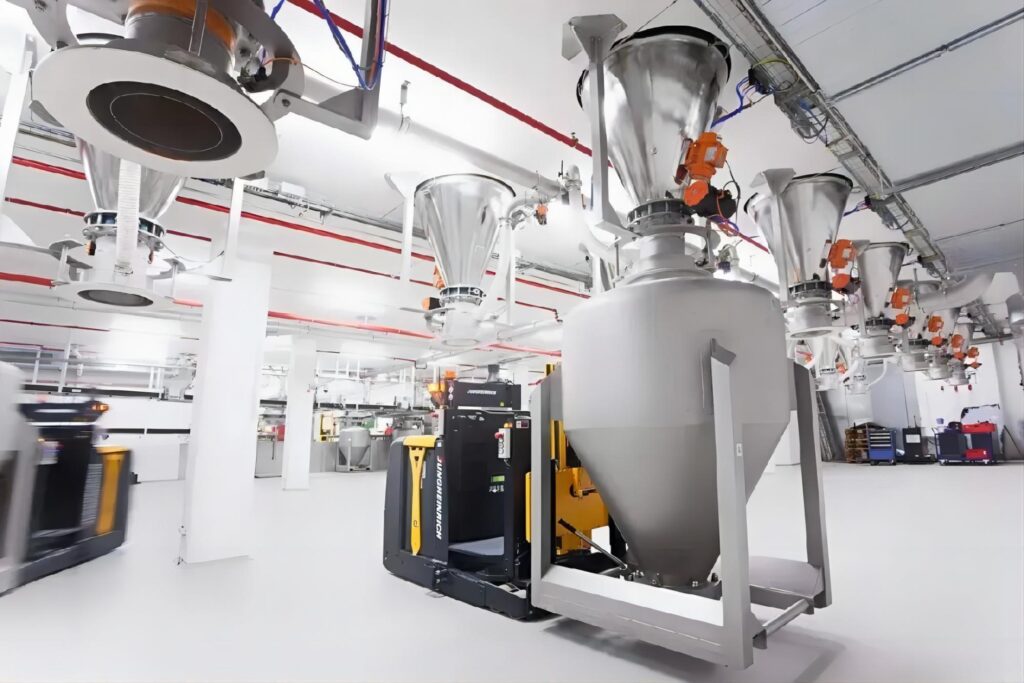
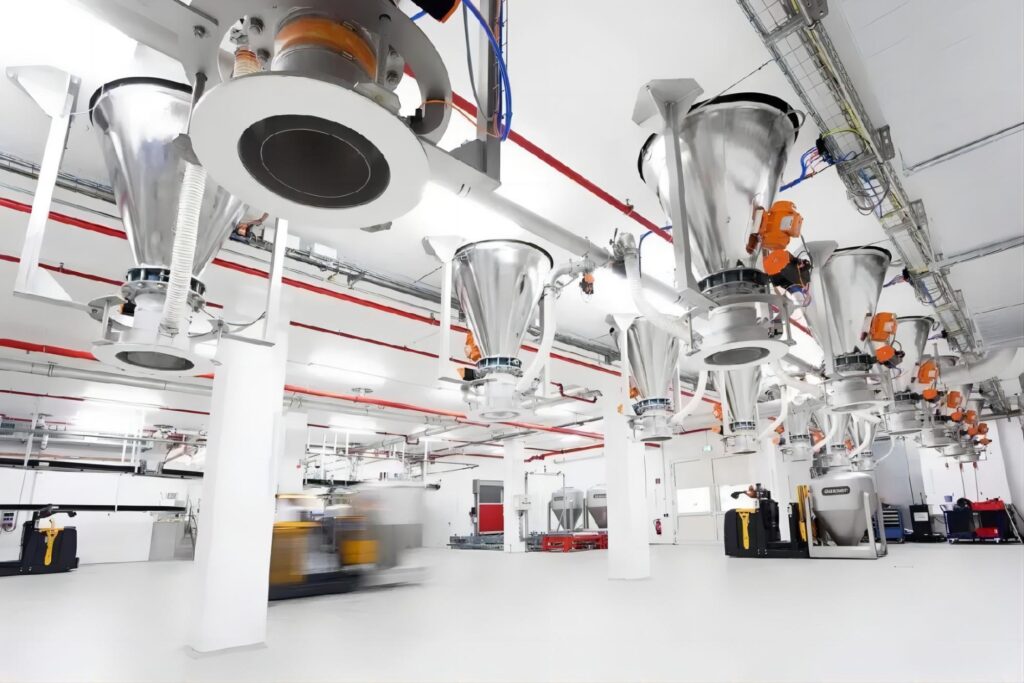
This freedom of design emphasizes another highlight of the plant: the mixer with a capacity of 1500 liters, where mixing takes place directly in the vessel. The benefit to the user is: since the feeding process of the mixer is completely omitted, the entire process step can be saved.
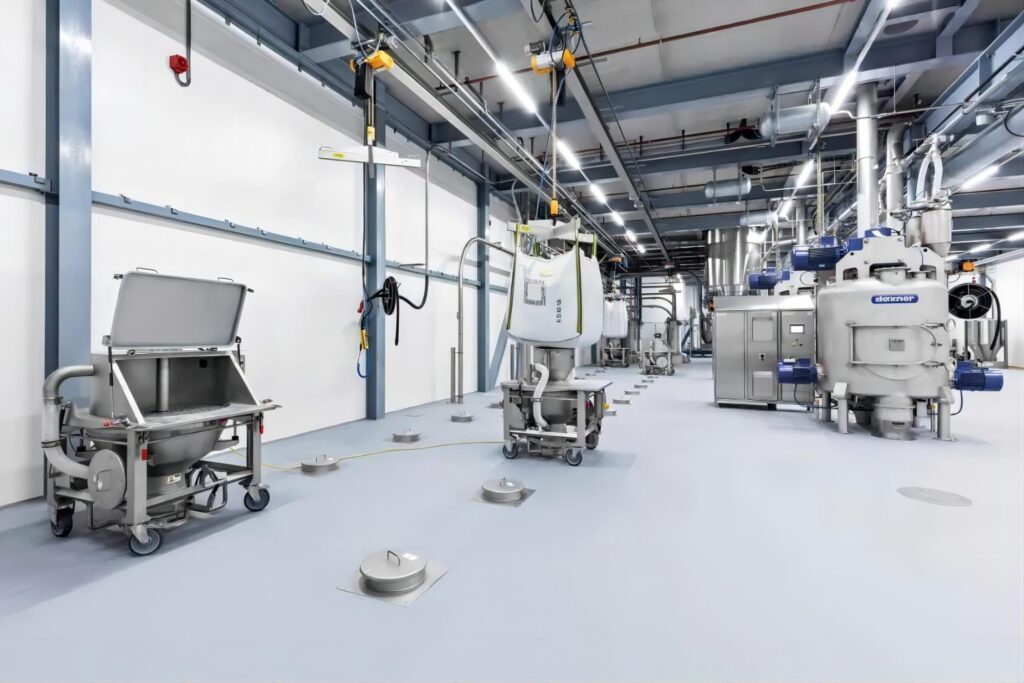
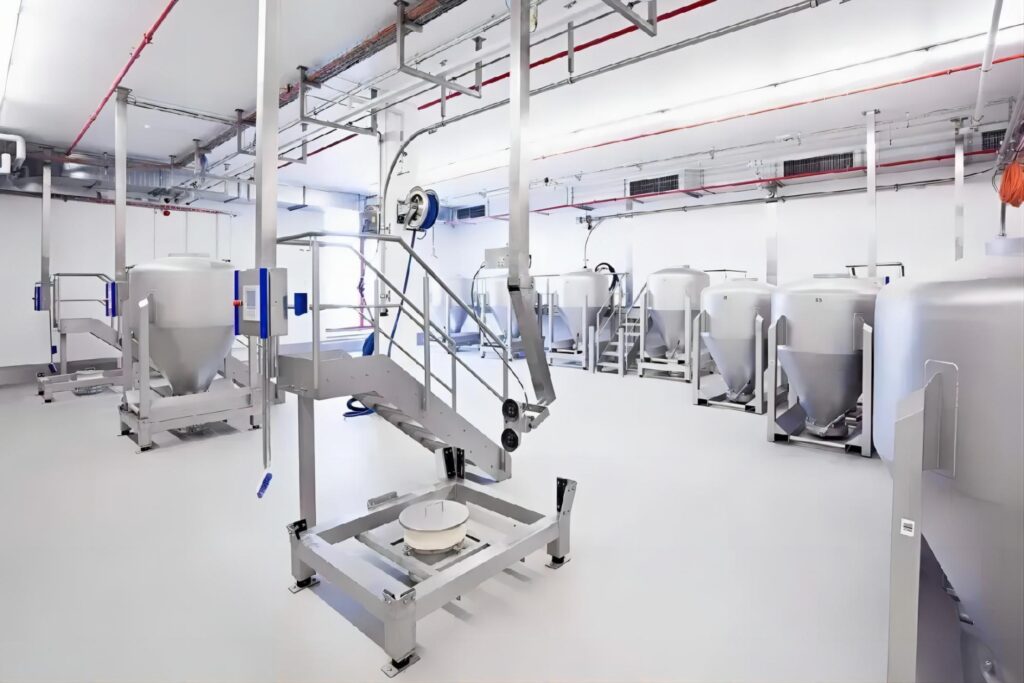
Herbal Packaging
After the mixing process, automated guided vehicles collect the containers containing the finished mixture and transport them without human assistance to an unloading station located next to the bagging station. The gravity bag filling and weighing system DAX-PVS (Pinch Valve System) fills the finished mixture into sales packaging. The core component of the DAX-PVS system is the pneumatic pinch valve, which ensures precise dosing of the product.
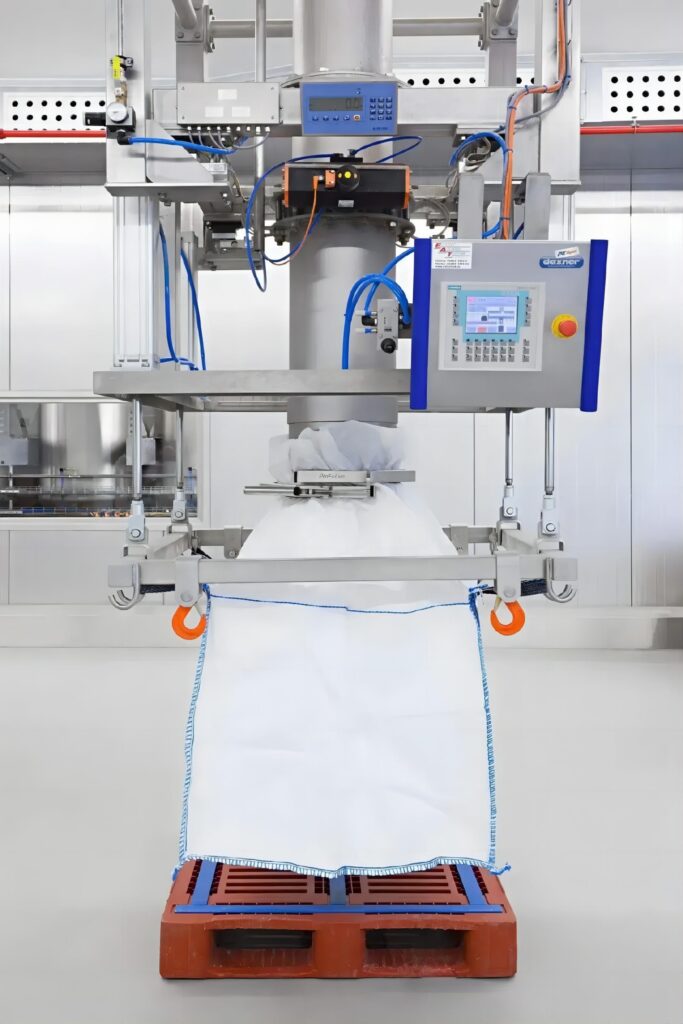
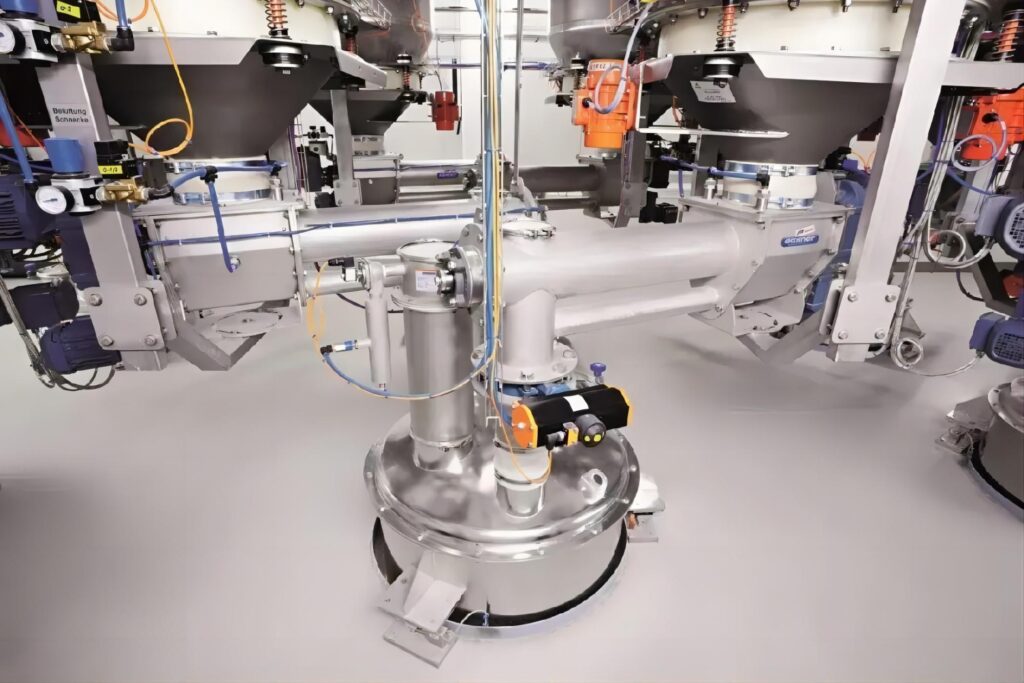
Compliant with HACCP and IFS
The complete mixing and packaging line is equipped with a negative pressure suction system to minimize dust formation. Central dust extraction system guarantees ease and comfort.
DAXNER GMBH
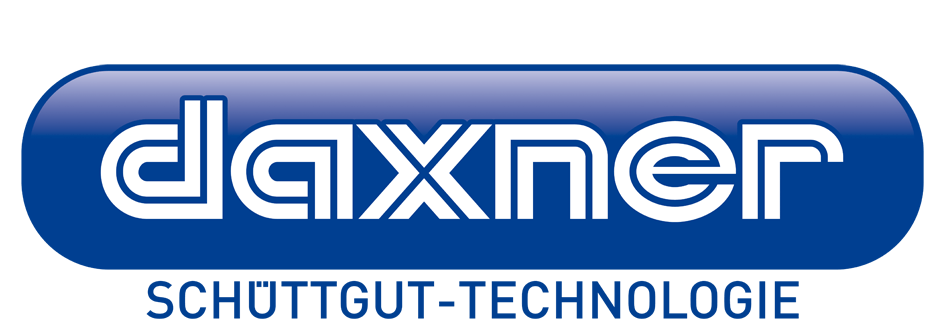
DAXNER International is an international material handling company established in Wels, Austria in 1984. It focuses on the food, brewing, baking, feed, chemical and other industries.
DAXNER International’s performance is built on three cornerstones: knowledge, competence and creativity. The company’s strength lies in the complete concept of innovative development and customized design. Can provide turnkey solutions for high-tech production equipment.
DAXNER International is headquartered in Wels, Wales, Austria, and its equipment manufacturing base is located in Lauda-Königshofen, Germany. The company has seamless service and support, and a strong network of international subsidiaries, such as Daxner Germany, Daxner SOUTH EAST ASIA, Daxner LATAM, Daxner RUSSIA, Daxner UK and Daxner USA, the company has numerous sales and service partners worldwide.
Company Overview
Founded in: 1984
Location: Wels / Austria
Employees 2019: 110
Legal form: GmbH
Managing Directors / CEO:
Dipl.-Ing. (M.S.) Christian Daxner, Ing. Johann Daxner
Industries:
Food & Beverage industry,
Spices and Herbs,
Bakery and Pastry ingredients,
Bakeries,
animal feed industry,
Industry (Chemical, pharmaceutical, plastics, building materials)