Candy packaging isn’t just about wrapping sweets in pretty paper. It’s a complex mechanical process that ensures the quality, hygiene, and visual appeal of confectioneries. This guide will take you behind the scenes of candy packaging machinery, explaining its workings, benefits, maintenance, challenges and advancements.
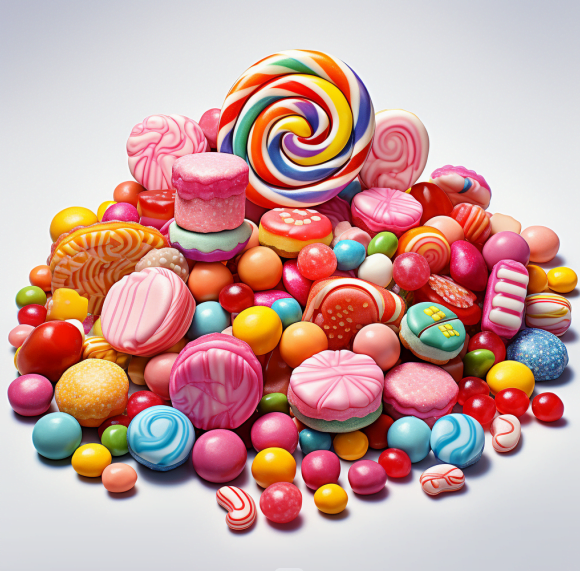
Introduction to Candy Packaging Machinery
Candy packaging machinery (also called candy wrapping machine)is essential equipment for candy makers to efficiently package their products for distribution and sale. An efficient and innovative packaging system not only guarantees product protection but also enhances its visual appeal, extending shelf life and ensuring the product reaches the consumer in excellent condition.
How Does Candy Packaging Machinery Work?
Candy packaging machinery employs various processes to package candies efficiently. It begins with feeding the candies into the machine, followed by accurate counting to configure the amount in each pack. The candies are then wrapped, sealed, and labelled, ready for distribution.
- Feeding – Loose candies are introduced into the packaging machine via hoppers, chutes, conveyors or conveyor belts. For uniformly shaped candies, vibratory feeders ensure a steady and even flow into the machine.
- Counting – The candies pass through photoelectric, weight or mechanical counters that determine the exact amount for each pack. The counters signal the packaging equipment when the required count is reached.
- Wrapping/Sealing – The candies are dropped into bags, boxes, cartons or other packaging formats. A film or sheet is then wrapped around the package and heat sealed to enclose the candies. For pre-formed bags, the machine simply fills and seals the opening.
- Labelling – Labels containing relevant information like brand, flavor, weight, expiry date and barcodes are automatically applied to the packaged products. This finalizes the pack and makes it ready for distribution.
- Ejection – The finished packs are ejected from the packaging line via a star wheel, conveyor belt or chute to the next stage of production or for packing into cases. Any rejects are separately ejected for disposal.
- Integration – Advanced lines integrate counting, wrapping/sealing and labelling processes into a single, high-speed packaging line for maximum efficiency and minimal manual handling.
What Types of Candy Packaging Machines are Available?
Several types of candy packaging machines cater to different packaging styles and candy types:
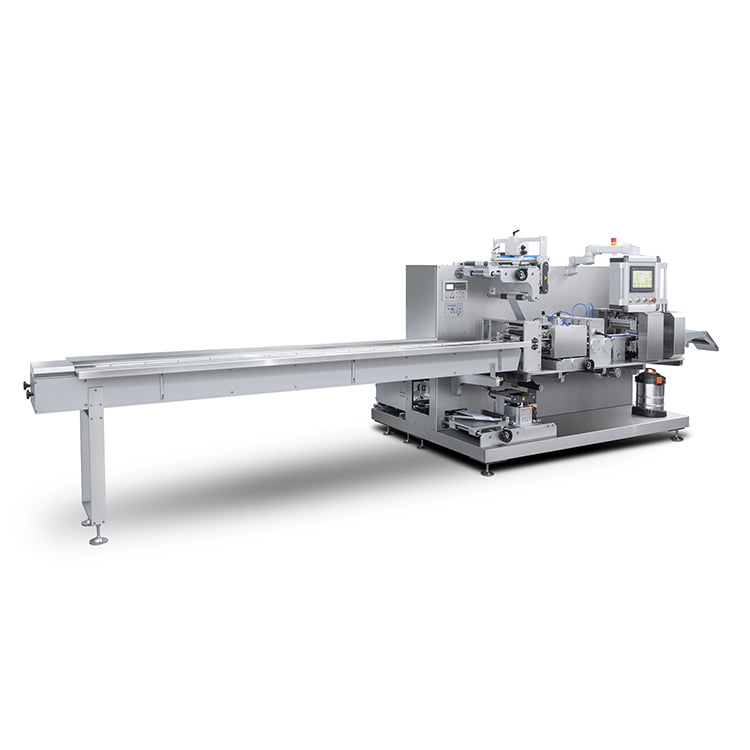
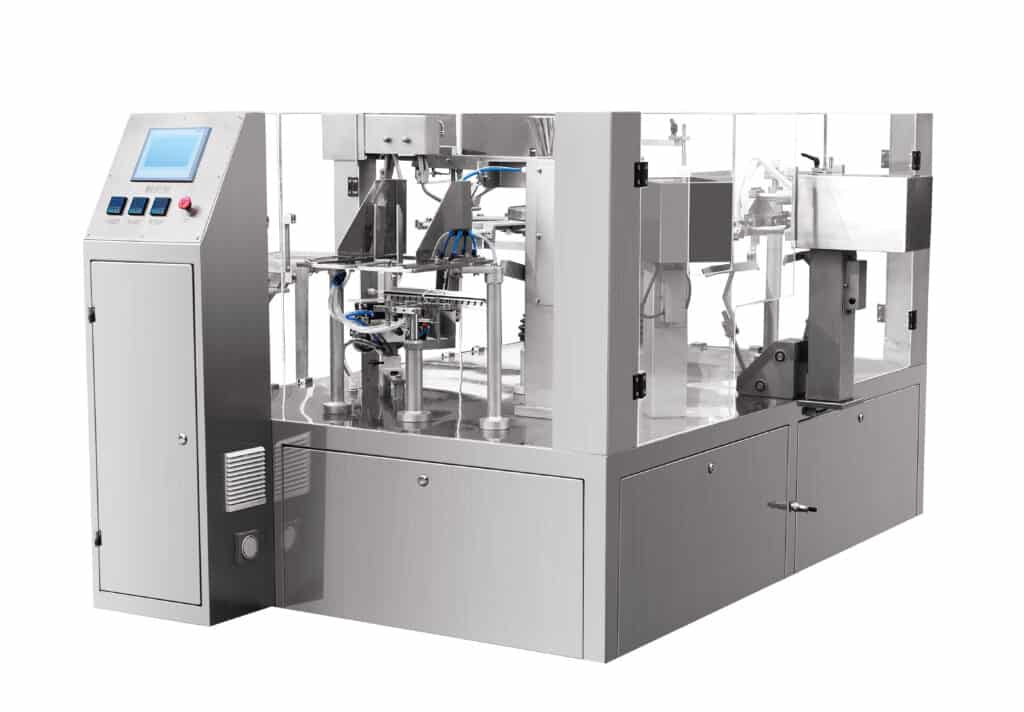
- Flow wrappers: Ideal for individually wrapped candies.
- Cut and Twist Wrapping Machine: Suitable for candies that require twisted ends.
- High Speed Pouch packaging machines: Perfect for packing multiple candies in one pouch.
- Automated candy sorting systems: These separate candies by type or color before packaging.
What Are the Benefits of Using Candy Packaging Machinery?
Benefits | Description |
---|---|
Improved Product Protection | Packaging machinery ensures the candy is well protected from environmental factors, maintaining its quality. |
Extended Shelf Life | Proper packaging can help extend the product’s shelf life by limiting exposure to air and moisture. |
Enhanced Visual Appeal | Professionally packaged candies are more visually appealing, attracting more customers. |
What Factors Should Be Considered When Choosing Candy Packaging Machinery?
When selecting candy packaging machinery, consider the following factors:
- Candy types and shapes
- Desired packaging styles
- Production volume
- Flexibility to handle different types of candies
- Hygiene standards and regulatory compliance
- Cost-effectiveness
How to Maintain and Clean Candy Packaging Machinery?
Daily/Between Runs Sanitation:
- Wash conveyor surfaces, chutes and hoppers with cleaners specifically for food contact surfaces.
- Wipe down all product contact surfaces, rollers, belts, guides and tooling.
- Use a brush to loosen any buildup.
- Vacuum or blow out debris from hard-to-reach areas.
- Check for signs of leaks or product buildup.
Periodic Deep Cleaning (Monthly or Quarterly):
- Do a thorough disassembly and cleaning of major components.
- Remove parts like dies, nozzles, and sensors and wash thoroughly.
- Use appropriate detergents for machine components like frames, motors and gears.
- Steam clean or pressure wash any remaining debris from hard surfaces.
- Re-lubricate moving parts as specified in the maintenance manual.
- Check for excess wear and damage that could compromise performance.
Maintenance:
- Follow the manufacturer’s recommended schedule for:
- Replacing filters
- Greasing bearings and chain drives
- Tightening belts
- Checking motor brushes and electrical connections
• Check for proper alignment of shafts, guides and tooling.
• Track run hours and part replacement cycles to plan necessary repairs.
Additional Tips:
- Use sanitary design machinery with IP-rated motors, washdown-duty components, and easy-clean surfaces.
- Require staff to follow hygienic practices like proper hand-washing and use of hair nets/gloves.
- Validate the effectiveness of your sanitation procedures through product and surface testing.
If you bought from Lintyco Machinery, please check our maintenance list
Common Challenges Faced with Candy Packaging Machinery and Their Solutions
Challenges | Solutions |
---|---|
Misalignments | Regular calibration and checks can minimize misalignments. |
Wrapper tears | Ensure the right tension settings and replace worn out parts. |
Miscounts | Regular maintenance of counting mechanisms can prevent miscounts. |
How to Enhance Candy Packaging Efficiency and Productivity?
Integrate packaging lines. Connect bagging, wrapping, and cartooning machines into fully integrated lines that feed directly into one another. This reduces material handling and the need for manual transfers between machines.
Automate production processes. Fully automated packaging lines can run 24/7 with minimal operator input, maximizing utilization of equipment and labour. Automation can also improve consistency and reduce errors.
Reduce product giveaways and waste. Implement optimal controls and sensors to minimize overfilling of bags, cartons and other packaging. Also, detect and reject defective candies before packaging.
Optimize line speeds. Select machines with the highest possible output to match production demands. Balancing line speeds across all packaging processes helps maintain the highest overall efficiency.
Maintain equipment uptime. Implement preventative maintenance programs and use durable, hygienic machine designs to minimize unplanned downtime. Spare parts inventory can also reduce repair time.
Use packaging materials efficiently. Select materials that are precisely sized for the application with minimal excess. Automated cutters and dispensers can reduce material waste.
Integrate with upstream processes. Connect packaging lines to cooling conveyors, weighers, drop formers and other candy production equipment for streamlined product transfer. This eliminates bottlenecks and buffers between stages.
Future trends in candy wrapping machines
Technological advancements, such as smart sensors, automated quality control systems, and customizable packaging designs, are revolutionizing candy packaging
- Use of candy wrapping machines to create candy packages in various shapes, such as star, heart or animal shapes.
- Designing a machine that can automatically sort candies by colour for faster packaging.
- Create a machine that can wrap many different flavours of candy at the same time so people can try many different flavours.
- Make reusable candy wrappers using a candy wrapping mechanism to reduce waste.
- Use a candy wrapping machine to add personalized labels to candies, such as names or photos.
- Utilize machines to make creative candy wrappers, such as wrappers that can morph or light up.
- Use candy wrapping machines to customize exclusive candy packaging for large events, such as weddings or birthday parties.
- Designing a machine that can automatically perform candy quality checks to ensure that each candy meets standards.
- Utilize a candy wrapping machine to design exclusive packaging for seasonal candies, such as Christmas or Halloween.
- Utilize the machine to add music or sound effects to the candy packaging to create a more interesting experience of use
Frequently Asked Questions about Candy Packaging Machinery
Q: What types of candy packaging machines are available?
A: There are several main types of candy packaging solutions depending on the packaging format needed:
- Bagging machines – For packing candies into bags of various sizes. These range from simple manual bag fillers to high-speed automated bagging lines.
- Boxing machines – For packing candies into boxes. These can handle both rigid and flexible boxes in various shapes and sizes.
- Wrapping machines – For wrapping individual pieces of candy or clusters in foil, paper, or cellophane. These provide an attractive and sanitary enclosure for the candy.
- Cartoning machines – For packing candies into folding cartons, rigid boxes, or trays. High-speed cartoners maximize efficiency for high-volume candy production.
- Bottling and Jarring machines – For packing candies into glass or plastic bottles, jars, and tubs. These lines can accommodate a range of container sizes.
Q: What factors are important in selecting equipment?
A: Key factors to consider include packaging format needs, production volume, candy types, hygienic design, changeover time, and total cost of ownership. Candy makers should consult with packaging machinery suppliers to determine the optimal solutions for their specific requirements and budget.
Q: Does packaging machinery help reduce product waste?
A: Yes, automated packaging lines with infeed and rejection systems can help minimize product waste by detecting and rejecting candies that do not meet quality standards before they reach the packaging stage. This results in fewer defects exiting the line and lower waste of usable product.
From understanding the types of machinery to the challenges faced, It’s a sweet blend of knowledge, designed to help you make informed decisions in the confectionery industry.
And if you have any questions, Do not hesitate to contact us.
Lintyco is a pioneer and leader in automated Candy Wrapping Machines and end-to-end packaging systems. Lintyco’s innovative packaging solutions for food, pharma, and other applications are complemented by advanced solutions for secondary packaging, wrapping & cartoning, bulk packaging, and more. Whether you are looking for a new machine or a complete line, or if you just want to upgrade your current packaging machine, talk to Lintyco. As experts of the industry with over three decades of proven expertise, Lintyco will provide the optimal solution backed by excellent consultancy and support.