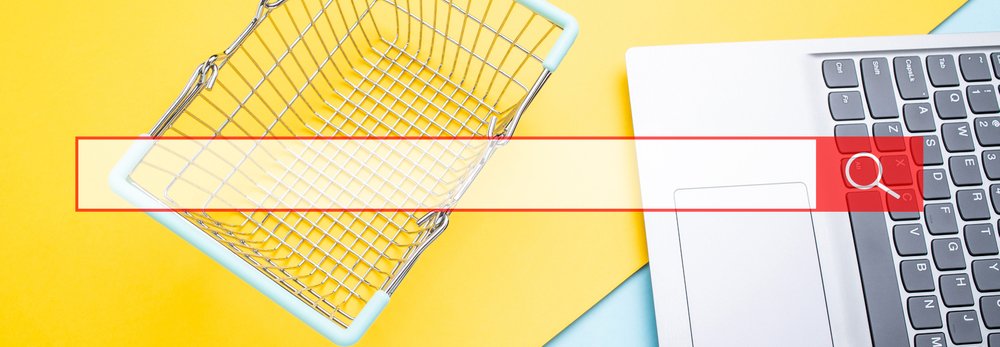
As a business owner, you’re always looking for ways to improve your operations and grow your revenue. One way to achieve this is by using a nuts-packing machine. A nuts-packing machine is a specialized piece of equipment that can streamline your packaging process, increase your productivity, and reduce your costs. In this blog, we’ll explore the benefits of using a rice packing machine and provide you with a comprehensive guide on how to choose, use, and maintain one for your business. Let’s get started!
Packaging and distributing nuts like almonds, cashews, walnuts and peanuts can be a lucrative business opportunity. However, efficiently packing and handling bulk quantities of nuts) can present operational challenges. Using automated nuts packaging equipment can help nut businesses increase output, reduce costs and improve packaging quality – fuelling business growth.

What is nuts packaging equipment?
Nuts packaging equipment is an automated industrial machine used to fill and seal bags of nuts like almonds, cashews, peanuts, walnuts,etc. for sale and distribution. nuts packaging equipment can fill bags at rates far exceeding what can be achieved manually. This high efficiency allows nut businesses to scale up rapidly to meet higher demand. nut packaging equipment clear polyester sealed bag. By accurately controlling the weight and amount of nuts filled in each bag, packing machines also provide greater consistency in products – satisfying customers and regulations. The labour cost savings from automation and reduced waste can further improve profitability.
The machines work by first weighing the required amount of nuts using an electronic scale. The nuts are then dispensed into bags through nozzles or filling chambers. The filled bags are then sealed automatically.
There are mainly two types of nuts packaging equipment:
Vertical machines): Nuts are fed from the top and bags are lifted up to the filling chamber. They tend to operate faster but require more floor space.
Horizontal machines): Bags are fed horizontally on a conveyor belt and filled from the side. They have a smaller footprint but operate at a lower speed.
- Within these categories, machines vary based on:
- Number of filling heads (1 to 4) and bags processed per minute (speed)
- Weight accuracy (down to 0.1 grams)
- Size of bags handled (from 1kg to 50kg)
- Fully automatic machines can open bags, fill them and seal them without human assistance.
- Semiautomatic machines require some manual loading of bags but are more affordable.
Benefits of Using a nuts packaging equipment
• Increased productivity and scale: nuts packaging equipment can fill bags at high speeds of hundreds per minute. This allows businesses to rapidly scale up operations to meet greater demand compared to manual methods. For example, nut processing companies and retail stores have been able to significantly expand their customer base after automating packaging with machines.
- Labour cost savings: The automation of nuts packaging equipment means they require minimal human supervision and labour to operate compared to manual methods. This often translates into substantial reductions in labour costs, freeing up workers for more value-added tasks. Many companies report labor cost savings of 30-50% after implementing machines.
- Improved accuracy and consistency: nuts packaging equipment can precisely control and monitor the weight in each bag, ensuring accurate and uniform fills that meet regulations and customer expectations. This improves product quality and consistency compared to manual packing methods.
- Reduced waste: Since machines can control the weight in each bag more precisely, they waste less nuts compared to manual methods that often result in overfilling and underfilling of bags. This leads to lower operational costs.
- Higher output per square foot: Due to their automated and compact design, nuts packaging equipment utilize less floor space but generate significantly higher output per square foot than manual packing lines. This makes machines suitable even for businesses with space constraints.
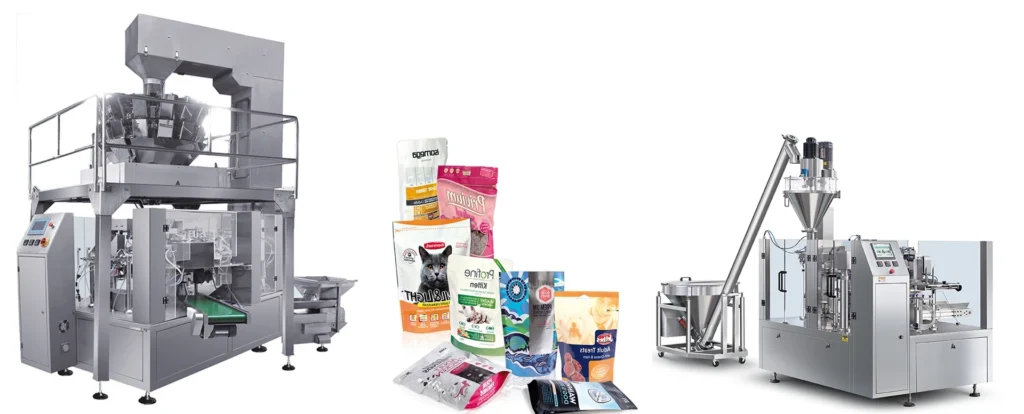
Factors to Consider When Choosing a nuts Packaging Equipment
- Production capacity – Determine your required output in bags per hour and per shift. Select a machine that can meet this output, preferably with some extra capacity for future growth. Faster bag per minute (BPM) rates indicate higher production capacity.
- Packaging material – Consider what type of bags you will use – paper, plastic or laminate. Choose a machine that is compatible with the size and material of your bags.
- Automation level – Fully automatic machines) require less labor but cost more. Evaluate your budget, labor pool and business goals to determine if full automation is warranted. Otherwise a semi-automatic machine may suffice.
- Weight range – Select a machine that can accurately weigh and handle the full range of bag weights you require. Higher precision machines provide better control over small variations in weight.
- Ease of maintenance – Simple machine designs that are easy to maintain generally provide higher uptime and lower downtime. Consider the service and support available from the manufacturer.
Tips for selecting:
- List your required output, target weight accuracy and packaging details. Prioritize features based on these needs.
- Consult other nut businesses using packing machines. Learn about the machines they recommend and why.
- Narrow your options to machines within +/- 10% of your minimum required output. Consider higher capacity machines for future growth.
- Ask suppliers about service plans and support. Reliable after-sales support is important to minimizing downtime.
- Check safety certifications to ensure the machine meets your standards.
- Trial the finalist machines if possible. This will provide valuable insights before committing to a purchase.
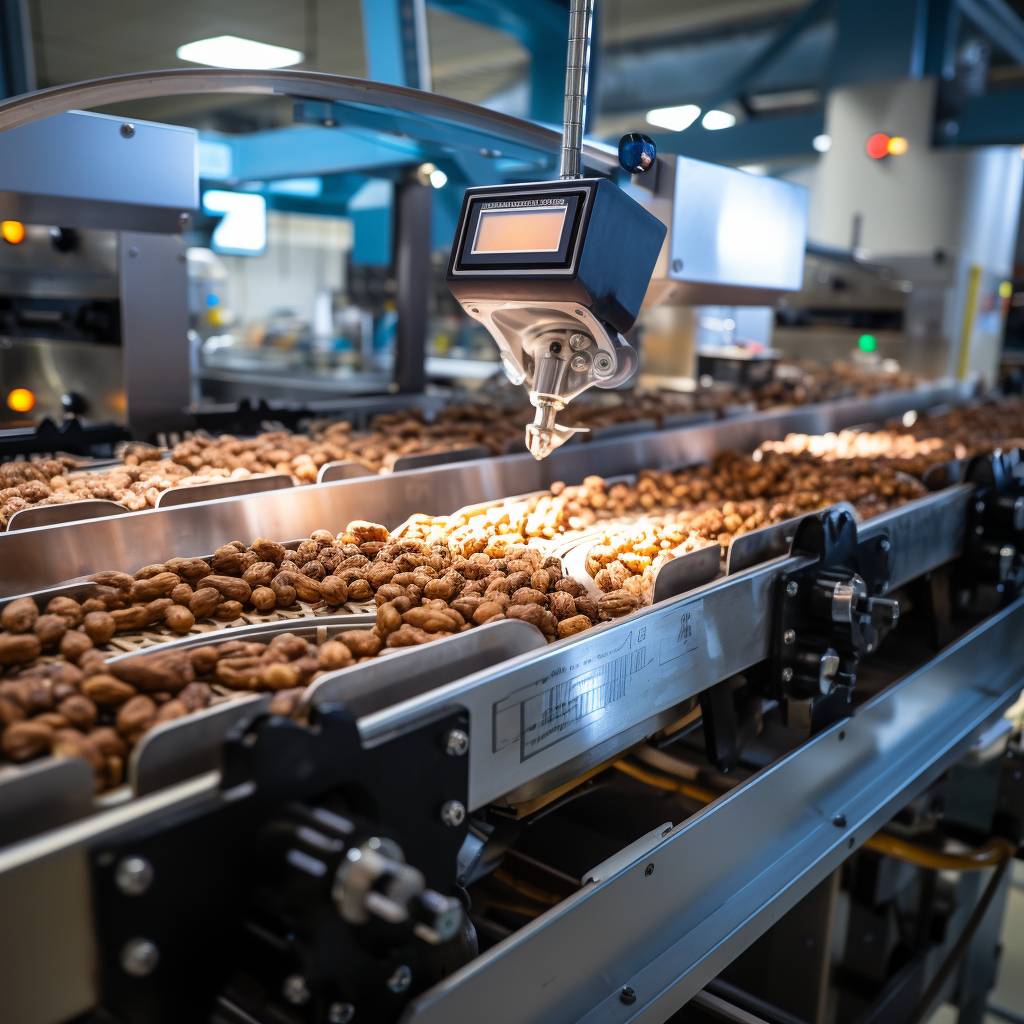
How to Use a Nuts Packing Machine
- Inspect the machine – Check all parts for wear, damage or loose fittings. Replace or tighten as needed. Ensure all guards and covers are secure.
- Load bags – Place the desired bags on the feeder and stacker trays. Position them correctly for smooth feeding through the machine.
- Set parameters – Input the target weight, bag size and feed rate on the control panel. Set the interval for automatically dropping filled bags.
- Run a test fill – With the machine not fully installed, run a test cycle to confirm settings are correct and bags are feeding properly. Adjust settings as needed.
- Install the machine – Bolt the machine securely to the floor or work surface. Double check all settings and parameters.
- Power on – Turn on the main power and control panel. Make sure all machine parts are moving as intended.
- Start filling – Press the start button to begin the automatic filling cycle. The machine will feed bags, fill them with nuts and seal them.
- Monitor output – Periodically check the filled bags to ensure the weight is correct and bags are sealing properly.
- Turn off machine – Press the stop button. Wait for all moving parts to come to a full stop before opening the machine.
Safety precautions:
- Wear protective equipment like gloves, steel toe shoes and eye protection.
- Do not touch moving parts while the machine is operating.
- Secure long hair and loose clothing.
- Keep others away from the machine while running.
- Turn off and unplug the machine before performing any maintenance or cleaning.
- Only make adjustments or repairs as specified by the manufacturer to avoid compromising safety features.
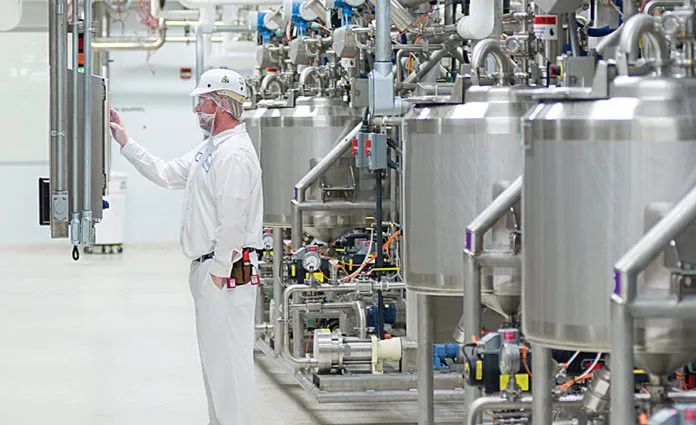
Maintenance and Troubleshooting of a Nuts Packing Machine
Importance of maintenance:
- Regular maintenance and thorough cleaning is essential to keep nuts packaging equipments running efficiently and prolonging their lifespan. Neglecting maintenance can cause parts to wear out faster and lead to more breakdowns.
- Over time, nuts particles and dust can accumulate on moving parts, rollers, and sensors, impacting performance and accuracy. Proper cleaning removes this accumulation and restores efficiency.
- Worn conveyor belts, rollers, seals, and other parts need to be promptly replaced to avoid issues like jamming, bag tearing and inconsistent fills.
- Lubricating moving parts periodically reduces friction that could cause parts to overheat and fail.
Common troubleshooting tips:
- For inaccurate bag filling, first check the weight calibration and adjust the settings if needed. Then inspect the filling chamber and nozzles for any clogs.
- If bags are jamming, first look for any debris or nuts stuck in the feeder, conveyor belts or roller surfaces. Then check rollers, belts and idler pulleys for wear.
- For conveyor belts that slip or walk, first tighten any loose belt tensioners. Then inspect the belt and pulleys for damage or debris trapped in between.
- When parts appear worn or damaged, refer to the manufacturer’s manual for recommended replacement parts and procedures. Use identical manufacturer parts for safety.
- For complex or persistent issues, contact the machine manufacturer or a trained technician for diagnosis and repairs. Avoid unauthorized modifications that could compromise safety.
Regular maintenance involves:
- Daily cleaning of filling chambers, conveyors and sensors
- Weekly lubrication of moving parts and roller surfaces
- Monthly checks of conveyor belts, rollers, seals and fittings
With proper care and maintenance following the manufacturer’s guidelines, nuts packaging equipments should deliver many years of reliable performance. Let me know if you have any other questions!
Conclusion
nuts packaging equipment can fill bags at high speeds of several hundred bags per minute. When choosing a nuts packaging equipment, businesses should consider factors like the required production capacity, type of packaging material, desired automation level, weight range and ease of maintenance. The selected machine should closely match the specific nuts packaging needs.
Lintyco is a pioneer and leader in automated Nuts Bagging Machines and end-to-end packaging systems. Lintyco’s innovative packaging solutions for food, pharma, and other applications are complemented by advanced solutions for secondary packaging, wrapping & cartoning, bulk packaging, and more. Whether you are looking for a new machine or a complete line, or if you just want to upgrade your current packaging machine, talk to Lintyco. As experts of the industry with over three decades of proven expertise, Lintyco will provide the optimal solution backed by excellent consultancy and support.