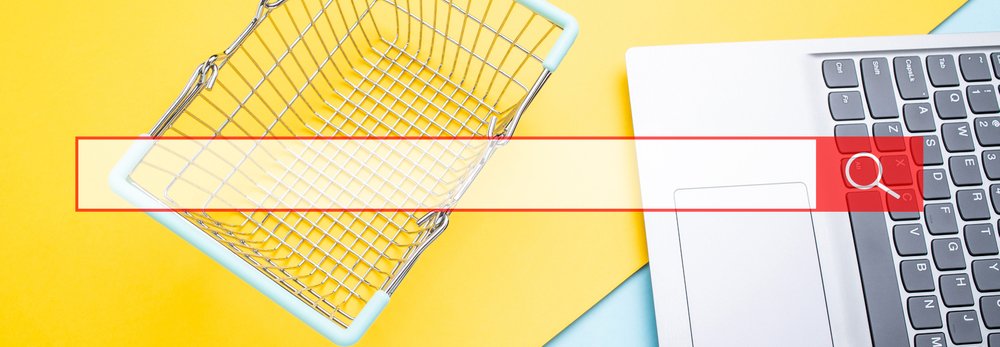
Follow Lintyco mechanical engineer with 20 years of experience, We will examine various aspects of detergent powder filling, including the types of machines available, their benefits, optimization techniques, quality control measures and market trends. Case studies demonstrate how manufacturers have leveraged new filling solutions to gain real competitive advantages. Let’s get started!
Introduction
A detergent powder filling machine is used by Laundry detergent manufacturers to automatically fill packets and containers with the correct amount of powdered detergent.
Filling machines help detergent manufacturers increase their production speed and consistency. They ensure that each detergent pack contains the precise amount of detergent needed, saving on materials and costs. Having an accurate and reliable filling process is critical for detergent manufacturers to maintain product quality.
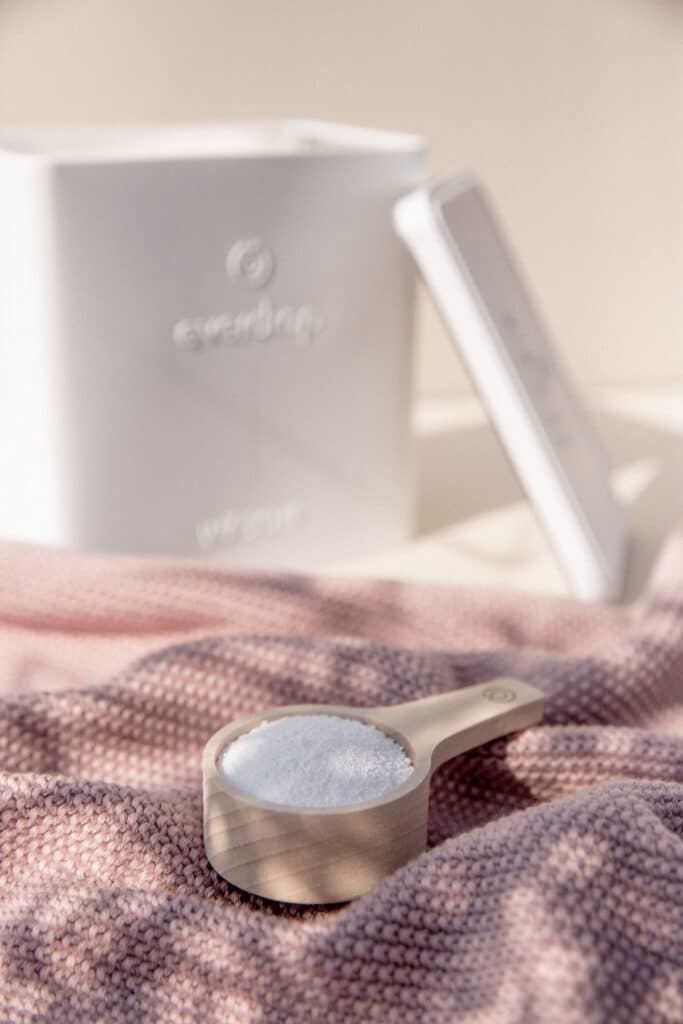
Detergent Packaging ideas
Detergent powders can be filled into a variety of packaging materials:
Bags: Paper and plastic bags are common choices. They are inexpensive but not resealable.
Pouches: Flexible pouches are another option. They are easy to use and resealable but more expensive. In the long term, smart manufacturers choose it.
Bottles and cartons: These options are good for larger volumes but cost more. Some countries do not allow using pouches and bags, detergent manufacturers will choose it more, or fill liquid laundry detergent in bottles.
![[premade bag powder packing machine 1.jpg]]
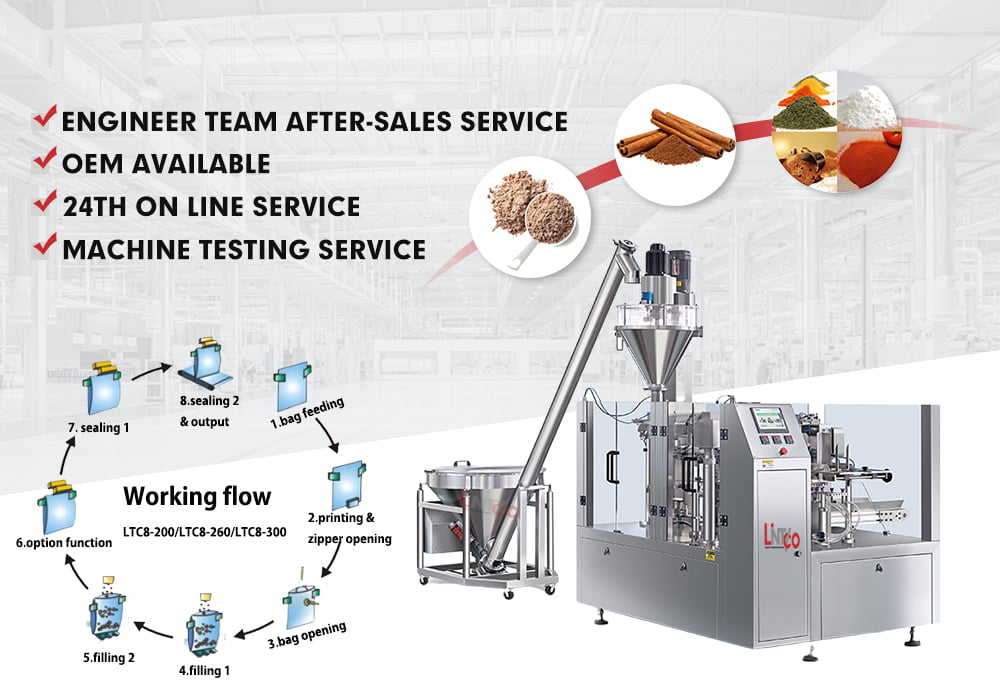
Types of Detergent Powder Filling Machines
Auger powder fillers: These use an auger mechanism to convey powder into packs. They are best for bags and flexible pouches.
Volumetric filling machines: They use rotating drums or cups to hold a determined volume of powder which is then dispensed. Simple design but less accurate.
Weighing filling machines: They weigh the pack before and after filling to determine the exact amount of powder filled. More precise and suitable for bottles and cartons.
Loss-in-weight filling machines: The hopper that holds the powder is weighed continuously during filling. The most accurate type but more expensive.
Advice: auger fillers and volumetric machines are best for pouches and bags due to their design while weighing and loss-in-weight machines offer greater precision and are suitable for bottles and cartons. The type of packaging and required filling accuracy determine the most suitable machine.
Benefits of Using a High-Quality Filling Machine:
Higher Production Output and Efficiency
Filling machines can fill packets much faster than manual filling, often achieving rates of 100-200 packets per minute. This significantly increases production output and efficiency. The machines reduce the time required to fill each packet, allowing manufacturers to produce more units in less time.
Increased Accuracy and Consistency of Filled Amounts
Filling machines use precise mechanisms to dispense the exact amount of powder required in each packet. This results in much higher accuracy and consistency compared to manual filling. Powder weights typically vary less than 1% with filling machines. The precise and consistent filling helps ensure a quality product.
Reduced Wastage of Detergent Powder
Since filling machines dispense the exact amount needed, there is minimal excess detergent left in the hopper or spilt during filling. This significantly reduces material wastage. The consistent filling action of the machines limits the chances of overflowing packets or underfilled units.
Lower Labor Costs
Filling machines reduce or eliminate the need for manual filling workers. This can substantially lower overall labour costs for detergent manufacturers. Manufacturers no longer need to pay wages and benefits for the manual labour required for filling large volumes of packets.
Easy to Automate and Integrate into Production Lines
Filling machines can be easily automated and integrated into fully automated production lines. This allows manufacturers to achieve higher levels of automation. The machines can be connected to conveyors, packagers and other elements to create an integrated, automated filling solution.
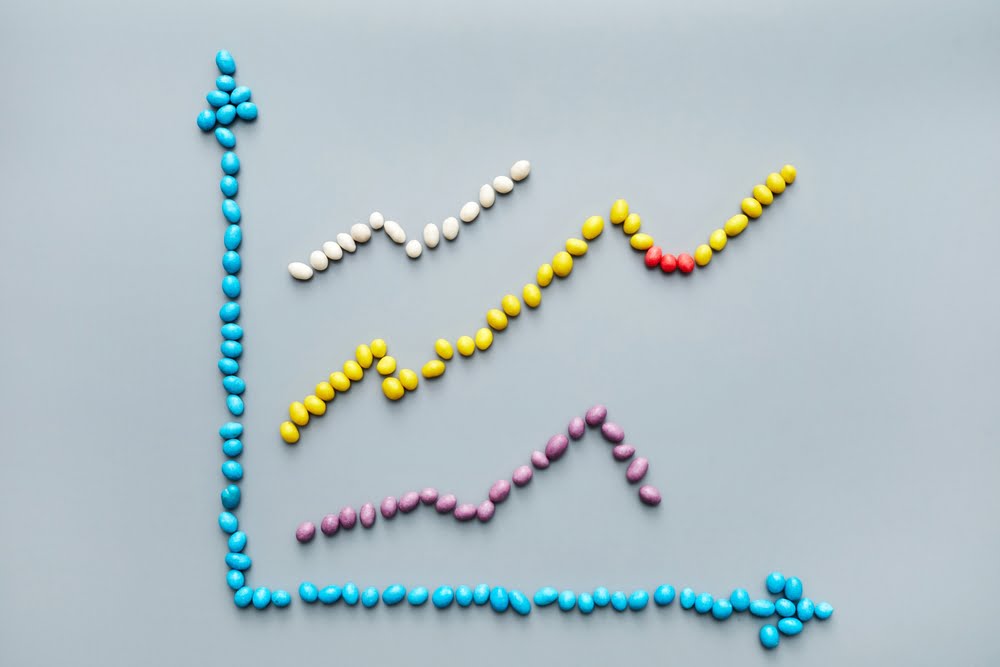
How to Choose the Right Machine for Your Needs
Higher production output and efficiency: Filling machines can fill packets much faster than manual filling, often achieving rates of 100-200 packets per minute. This significantly increases production output and efficiency.
Increased accuracy and consistency of filled amounts: Filling machines use precise mechanisms to dispense the exact amount of powder required in each packet. This results in much higher accuracy and consistency compared to manual filling. Powder weights typically vary less than 1%.
Reduced wastage of detergent powder: Since filling machines dispense the exact amount needed, there is minimal excess detergent left in the hopper or spilt during filling. This significantly reduces material wastage.
Lower labour costs: Filling machines reduce or eliminate the need for manual filling workers. This can substantially lower overall labor costs for detergent manufacturers.
Easy to automate and integrate into production lines: Filling machines can be easily automated and integrated into fully automated production lines. This allows manufacturers to achieve higher levels of automation.
Download Your Free Machine Roi Calculator FIle
Production efficiency optimization&Automation and integration options
Production efficiency optimization
Proper maintenance: Regular maintenance of all parts is essential to ensure the filling machine runs efficiently. This includes lubricating moving parts, clearing blockages, and replacing worn components.
Calibration: The dispensing mechanisms should be calibrated regularly to ensure the filled amounts remain accurate. This involves adjusting settings and checking the weights of filled packets.
Workflow optimization: The layout and workflow around the filling machine can be optimized to minimize downtime and bottlenecks. This includes efficient powder hopper refilling and packet disposal.
Automation and integration options
Conveyor systems: Conveyors can automatically feed empty packets to the filling machine and transport filled packets away. This achieves a fully automated process with no manual handling of packets.
Robotic arms: Robotic arms can be used to load empty packets onto conveyors, remove filled packets, and stack them onto pallets. They provide accurate, efficient handling of packets.
PLC controls: Programmable logic controllers can be used to automate and coordinate the entire filling and packaging process. They integrate conveyors, robotic arms and other equipment.
To maximize the efficiency of detergent powder-filling machines, it is important to implement proper maintenance routines, calibration checks and optimize the broader workflow. Fully automating the process through the use of conveyors, robots and PLC controls can further improve efficiency, consistency and reduce costs. With advanced automation, detergent manufacturers can achieve high throughput and maximize the impact of their filling machine investments.
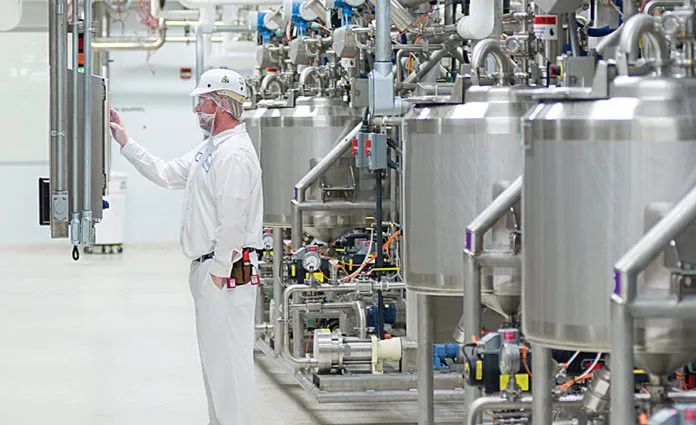
Quality control&roubleshooting common issues
Quality control
Weight verification: Filled packets should be randomly checked to verify their weight matches the target filling weight. This ensures the machine is filling accurately.
Sealing integrity checks: The seals of a sample of filled packets should be inspected to ensure there are no leaks. Leaks can cause quality issues and waste of powder.
Batch tracking: Each batch of filled packets should be assigned a unique identifier so any issues can be traced back to a specific filling machine and time. This helps identify potential machine faults early.
Troubleshooting common issues
Jamming: Powder can sometimes clump and cause the filling mechanisms to jam. To fix, clear any blockages and increase powder flow rates to prevent further jamming.
Leaking: Leaks from packet seals are common and can be caused by damaged seals or improper sealing. Inspect seals and adjust or replace them.
Inconsistent weights: Inconsistent packet weights indicate a problem with the dispensing mechanism. Calibrate the machine and check for any wear and tear.
Component wear: Over time, moving parts can wear out, impacting filling accuracy. Replace worn components like augers and metering drums as needed.
Conducting regular quality checks through weight verification, sealing integrity inspections and batch tracking helps ensure a consistent quality of filled detergent packets. Meanwhile, common filling machine issues like jamming, leaking, inconsistent weights and component wear can usually be resolved through troubleshooting procedures ranging from calibrating and adjusting the machine to replacing worn parts.
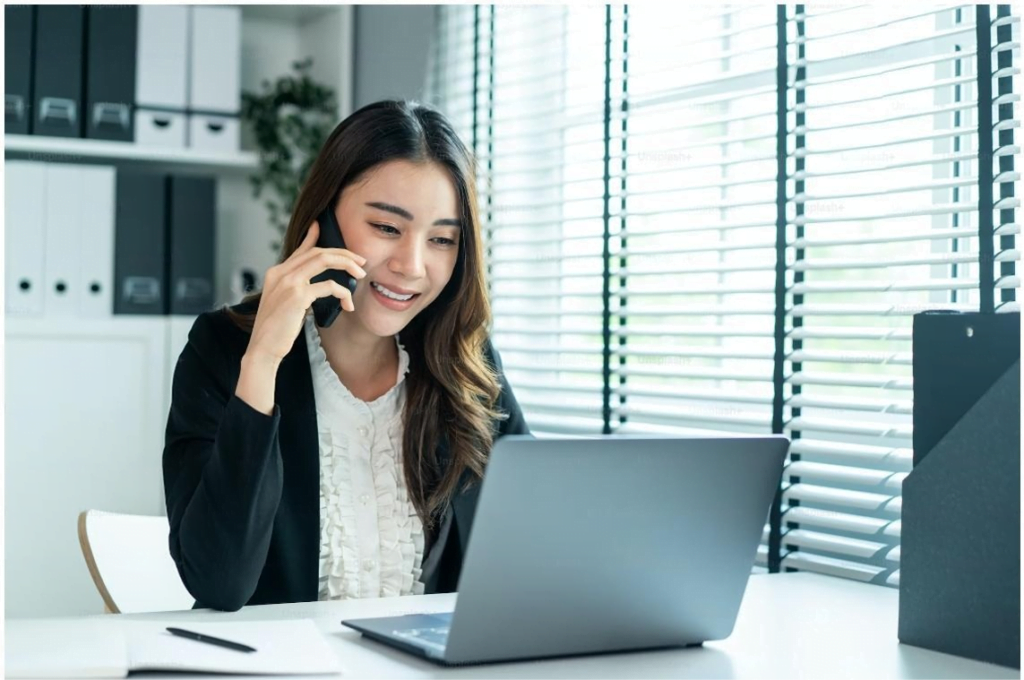
Market trends and innovations
Control systems: There is a trend toward more advanced automation and control systems for filling machines. This includes the use of Industrial Internet of Things (IIoT) technologies, predictive analytics, and machine learning to optimize performance.
Packaging automation: Manufacturers are integrating filling machines with more automated packaging solutions like robotic palletizing and case packing to create fully automated production lines.
Sustainability: There is a push for more sustainable filling machine designs that use less material, energy and water. Some manufacturers are developing systems to recover powder from the filling process for reuse.
Material handling: Improved material handling solutions are being developed to efficiently feed powder hoppers and convey away filled packets. This includes vibratory feeders, automated bag openers and improved conveyor systems.
Precision and accuracy: Manufacturers are achieving ever higher levels of filling accuracy through advances in weighing technologies, sensor feedback, and machine calibration systems. Some machines can fill within +/- 0.1% accuracy.
Safety: Safety features are becoming more advanced with interlocking guards, light curtains, emergency stop buttons and other solutions to protect operators near filling machines.
Case studies and success stories

This case studies demonstrate how detergent manufacturers are leveraging automated filling solutions to improve their efficiency, output and costs. Features like higher speeds, greater precision and enhanced accuracy help companies optimize their operations, strengthen their brands and remain competitive. Implementing the right filling machine solutions can have a significant positive impact on business performance.
•Unilever implemented automated powder filling lines for its Surf Excel and Omo detergent brands in India. The new lines increased production capacity by 30% while reducing wastage by 20%. Production costs per unit fell by over 10%.
•Henkel invested in high-speed automated filling machines for its Persil detergent brand. The machines can fill up to 250 bags per minute, double the output of the previous machines. Henkel was able to increase Persil production by 40% to meet growing demand.
•Procter & Gamble adopted automated auger filler machines for its Tide pods and detergent powder range. The machines improved filling accuracy to within +/- 0.5% while increasing throughput by 60%. This helped P&G maintain a competitive advantage through product quality and efficiency.
FAQ
Q: What is a Detergent Powder Filling Machine? A: A detergent powder filling machine is an automated system designed for packaging powdered detergent. It is used to precisely fill packets and containers with the correct amount of detergent, enhancing production speed, consistency, and accuracy.
Q: How does a Detergent Powder Filling Machine improve production efficiency? A: These machines increase production efficiency by automating the filling process. They can fill packets much faster than manual filling, often achieving rates of 100-200 packets per minute, significantly increasing production output and efficiency.
Q: What types of Detergent Powder Filling Machines are available? A: Types of machines include auger powder fillers, volumetric filling machines, weighing filling machines, and loss-in-weight filling machines. Each type offers varying levels of precision and suitability for different packaging types.
Conclusion
In summary, choosing the right detergent powder-filling machine depends on factors like your required filling accuracy, production output needs, packaging type and automation goals. To make the optimal choice for your specific requirements, it is best to consult experienced suppliers in the field. Click Here to Contact us.
I would encourage readers to contact different powder-filling machine suppliers to learn about their solutions and get recommendations tailored to their production needs. A proper consultation can help you identify the filling machine features that matter most to your business, maximize the return on investment and improve your overall production efficiency.
Lintyco is a pioneer and leader in automated Detergent Powder Filling Machines and end-to-end packaging systems. Lintyco’s innovative packaging solutions for food, pharma, and other applications are complemented by advanced solutions for secondary packaging, wrapping & cartoning, bulk packaging, and more. Whether you are looking for a new machine or a complete line, or if you just want to upgrade your current packaging machine, talk to Lintyco. As experts of the industry with over three decades of proven expertise, Lintyco will provide the optimal solution backed by excellent consultancy and support.