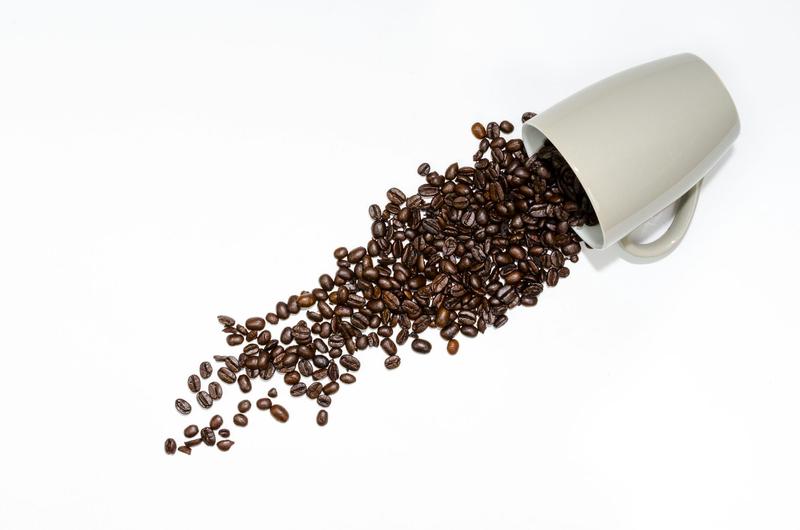
The coffee industry’s shift toward single-serve convenience meets sustainability through drip coffee bag packing machines. This guide explores cutting-edge packaging solutions balancing operational efficiency, product freshness, and environmental responsibility—critical knowledge for roasters aiming to compete in the $12.6B premium coffee market.
Why This Article Is Worth Reading
This comprehensive guide delves into the intricacies of drip coffee bag packing machines, exploring their functionality, benefits, and the factors to consider when selecting the right machine for your business. Whether you’re a coffee roaster aiming to diversify your product line or a packaging professional seeking to understand the latest advancements in coffee packaging technology, this article provides valuable insights to inform your decisions.
What Are Drip Coffee Bags?
Drip coffee bags are single-serve packets filled with ground coffee, designed to be hung over a cup and brewed with hot water. Originating in Japan in the 1990s, these convenient brewing solutions have gained global popularity due to their ease of use and portability. They offer coffee enthusiasts a way to enjoy freshly brewed coffee without the need for specialized equipment.
How Do Drip Coffee Bag Packing Machines Work?
Drip coffee bag packing machines automate the process of creating and packaging these single-serve coffee bags. The process typically involves several key steps:
- Bag Formation: The machine forms the filter bag from suitable materials, such as non-woven fabric or nylon.
- Filling: A precise amount of ground coffee is dispensed into the formed bag.
- Sealing: The bag is sealed using ultrasonic or heat sealing methods to ensure freshness and prevent contamination.
- Outer Packaging: The filled and sealed drip coffee bag is then enclosed in an outer sachet or overwrap for additional protection and branding.
This automated process ensures consistency, reduces labor costs, and enhances production efficiency.
Key Features of Drip Coffee Bag Packing Machines
When selecting a drip coffee bag packing machine, consider the following features:
- Automation Level: Machines range from semi-automatic to fully automatic, with fully automatic machines offering higher efficiency and consistency.
- Sealing Technology: Ultrasonic sealing provides a clean and efficient method, while heat sealing is more cost-effective.
- Material Compatibility: Ensure the machine can handle the specific materials used for the filter bags and outer packaging.
- Production Capacity: Choose a machine that aligns with your production volume requirements.
- Ease of Maintenance: Opt for machines with user-friendly interfaces and accessible components for easier maintenance.
Drip Coffee Bag Materials: Choosing the Right Option
The choice of materials for drip coffee bags and their packaging is crucial for product quality and sustainability:
- Filter Materials: Common options include non-woven fabric, nylon, and biodegradable materials.
- Outer Packaging: Materials such as laminated films, kraft paper, and recyclable plastics are used for outer sachets.
Selecting the appropriate materials impacts the brewing experience, shelf life, and environmental footprint of the product.
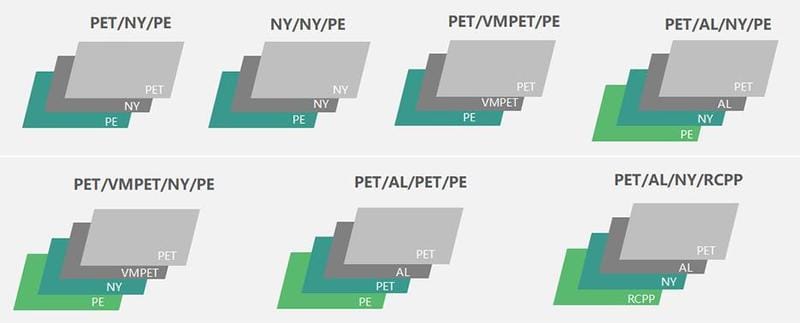
Material Comparison Table
Layer | Traditional Option | Sustainable Alternative | OTR (cc/m²/day) |
---|---|---|---|
Outer | PET 12μm | PLA 20μm | 80 vs 150 |
Middle | Aluminum 7μm | SiO₂-coated PET 12μm | 0.05 vs 0.5 |
Inner | LDPE 50μm | PBAT/PLA 60μm | 15 vs 25 |
While aluminum foil provides superior oxygen barrier properties (OTR <0.1), many roasters now opt for recyclable mono-material structures like OPP/EVOH/PP or home-compostable films meeting TUV OK compost HOME standards. Critical considerations:
- Degradation Time: Certified compostable films break down in 180 days vs 450+ years for conventional plastics
- Print Compatibility: Water-based inks required for eco-films to maintain recyclability
- Machine Compatibility: Coefficient of friction (COF) must be 0.2-0.4 for smooth operation on VFFS machines
Can Your Packaging Machine Handle Biodegradable Films?
Material Compatibility Checklist
Film Type | Max Sealing Temp | Recommended Jaw Pressure | Pre-Heating Needed? |
---|---|---|---|
PLA/PBAT | 130°C | 0.4-0.6 bar | Yes (50°C) |
Cellulose Acetate | 150°C | 0.3-0.5 bar | No |
AlOx-coated PET | 180°C | 0.8-1.2 bar | Optional |
Upgrading for biofilms often requires:
- Ceramic-coated sealing jaws (prevents sticking)
- Teflon feed rollers (reduce static on PLA)
- Humidification chambers (maintain 45% RH for cellulose films)
Pro Tip: Always conduct differential scanning calorimetry (DSC) tests to identify film melting points before production runs.
Drip Coffee Bag Packing Machine Manufacturers: Leading the Industry
Several manufacturers specialize in drip coffee bag packing machines, offering a range of models to suit different production needs:
- Lintyco Pack : Known for their ultrasonic drip coffee bag packing machines, offering high-speed and efficient solutions.
- Spackmachine: Provides comprehensive guides and machines for drip coffee bag packaging, focusing on user-friendly designs.
- ACMA Machinery: Offers machines with ultrasonic sealing and cutting systems, emphasizing safety and efficiency.
Evaluating these manufacturers based on your specific requirements can help in selecting the right equipment for your business.
Vertical Form Fill Seal (VFFS) vs. Horizontal Form Fill Seal (HFFS) Machines
When selecting a drip coffee bag packing machine, understanding the differences between Vertical Form Fill Seal (VFFS) and Horizontal Form Fill Seal (HFFS) machines is crucial.
Vertical Form Fill Seal (VFFS) Machines
VFFS machines operate by pulling a roll of film through a tube, forming a bag vertically, filling it with the product, and sealing it at the top. They are ideal for free-flowing products like coffee grounds. The vertical orientation allows for efficient use of floor space and is suitable for high-speed operations. However, VFFS machines may have limitations in handling irregularly shaped or delicate products.
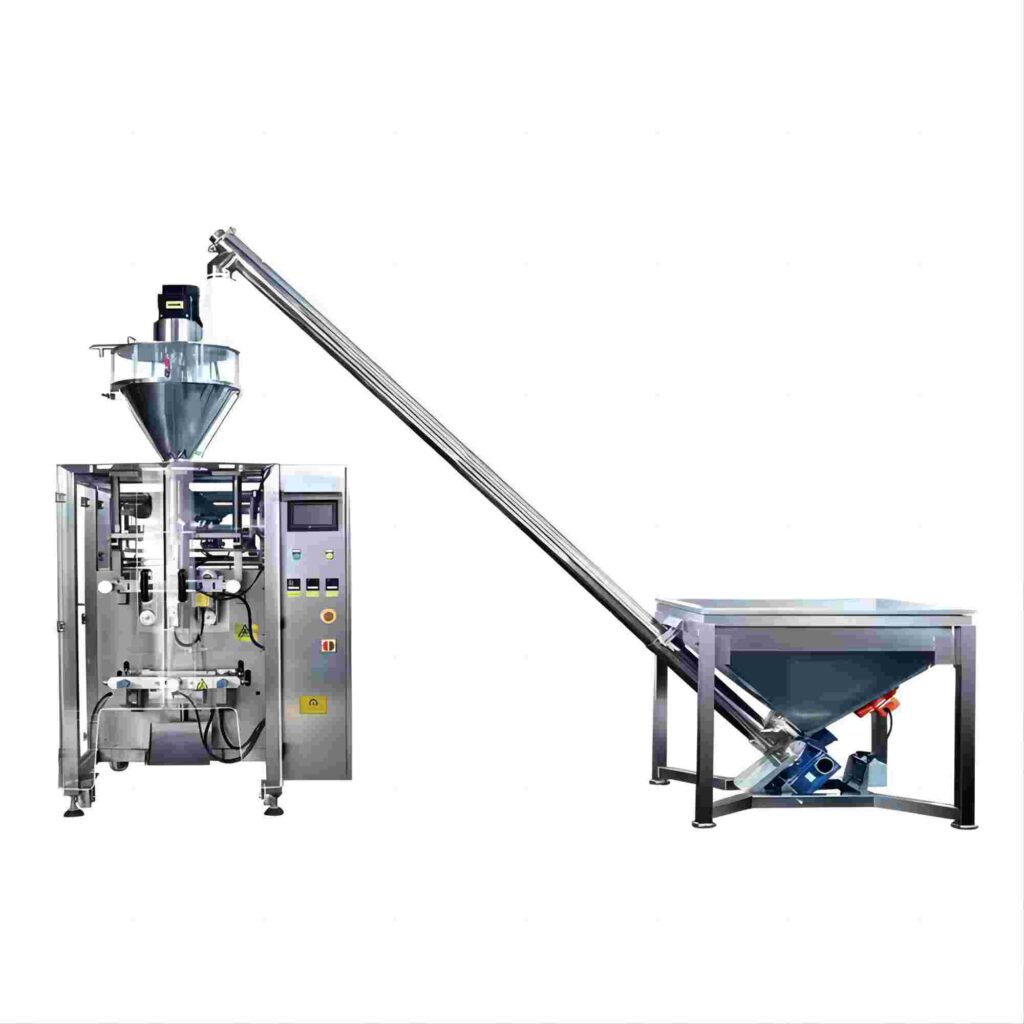
Horizontal Form Fill Seal (HFFS) Machines
HFFS machines feed the packaging film horizontally, forming a pouch, filling it with the product, and sealing it. They are versatile and can handle a wide range of products, including solid, semi-solid, or irregularly shaped items. HFFS machines are ideal for packaging products that require gentle handling or have complex shapes. However, they may require more floor space and can be more complex to operate compared to VFFS machines.
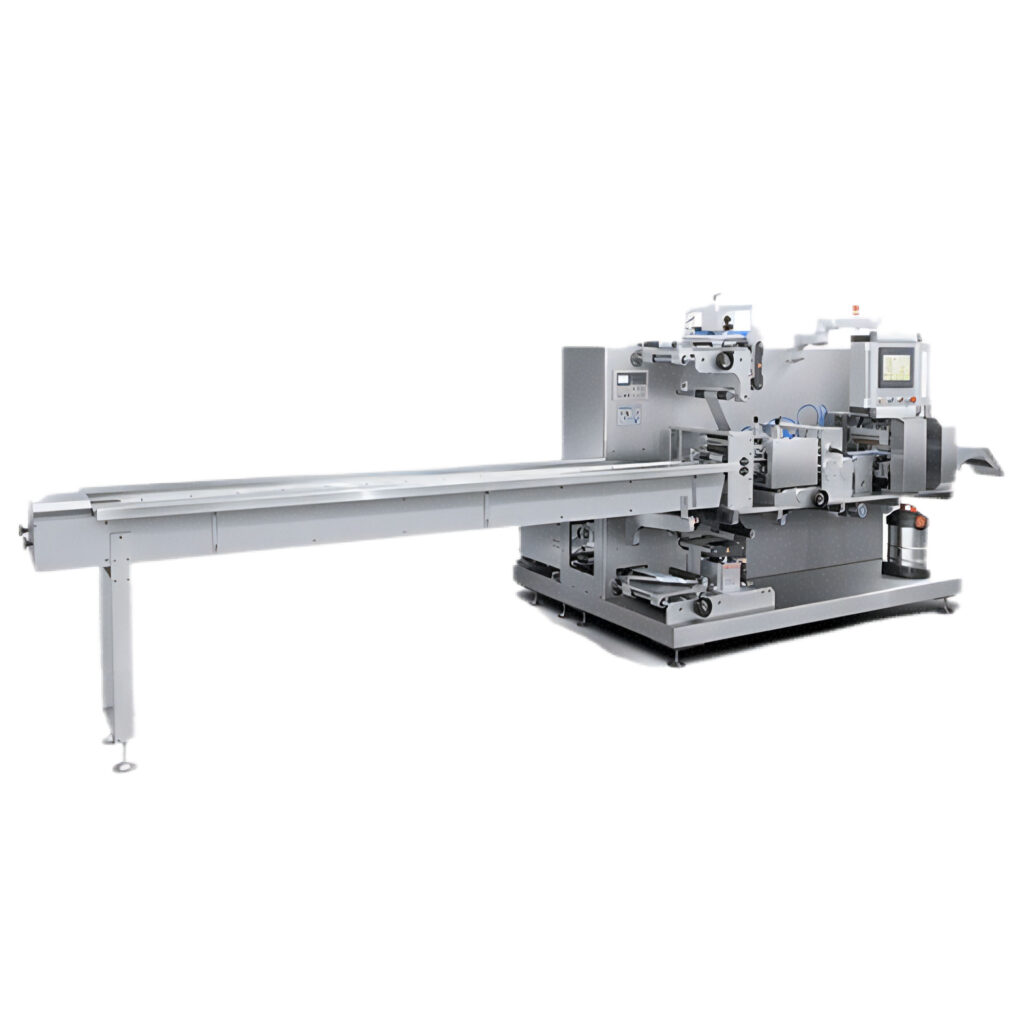
Key Differences at a Glance
Feature | VFFS Machine | HFFS Machine |
---|---|---|
Orientation | Vertical product flow | Horizontal product flow |
Floor Space | 15-20 sq. ft | 30-40 sq. ft |
Speed Range | 40-120 bags/min | 20-180 bags/min |
Material Thickness | Handles 60-120μm films | Optimal for 80-200μm films |
Best For | Small-to-medium roasters | Large-scale production |
Vertical Form-Fill-Seal (VFFS) machines dominate drip coffee packaging due to their compact footprint and high-speed operation. Their gravity-assisted filling system ensures precise 10g±0.2g dosing – critical for single-serve consistency. However, Horizontal Form-Fill-Seal (HFFS) machines excel in handling thick biodegradable materials like PLA/PBAT blends, which often jam in vertical systems.
Choosing the Right Machine
The decision between VFFS and HFFS machines depends on several factors:
- Product Characteristics: Consider the flowability, shape, and fragility of your coffee grounds.
- Production Speed: VFFS machines typically offer higher speeds, suitable for large-scale operations.
- Floor Space: VFFS machines are more compact, making them suitable for facilities with limited space.
- Packaging Complexity: HFFS machines offer more flexibility in creating complex packaging designs.
Sustainable Practices in Drip Coffee Bag Packaging
Sustainability is a growing concern in the coffee industry. Implementing eco-friendly practices in drip coffee bag packaging can enhance brand reputation and appeal to environmentally conscious consumers.
Eco-Friendly Materials
Opting for biodegradable or recyclable materials for both inner and outer packaging can significantly reduce environmental impact. Materials such as PLA (Polylactic Acid) and other biodegradable films are gaining popularity.
Energy-Efficient Machines
Investing in energy-efficient packing machines can lower operational costs and reduce carbon footprint. Machines with advanced control systems and energy-saving features contribute to sustainable production practices.
How to Pack Coffee in Drip Bags: A Step-by-Step Guide
Packing coffee into drip bags involves several key steps:
- Preparation: Select high-quality coffee beans and grind them to the desired consistency.
- Filling: Use a precise filling system to ensure consistent weight and volume in each bag.
- Sealing: Employ ultrasonic or heat sealing methods to securely close the bags, preserving freshness.
- Packaging: Place the sealed drip bags into outer packaging, such as envelopes or boxes, for protection and branding.
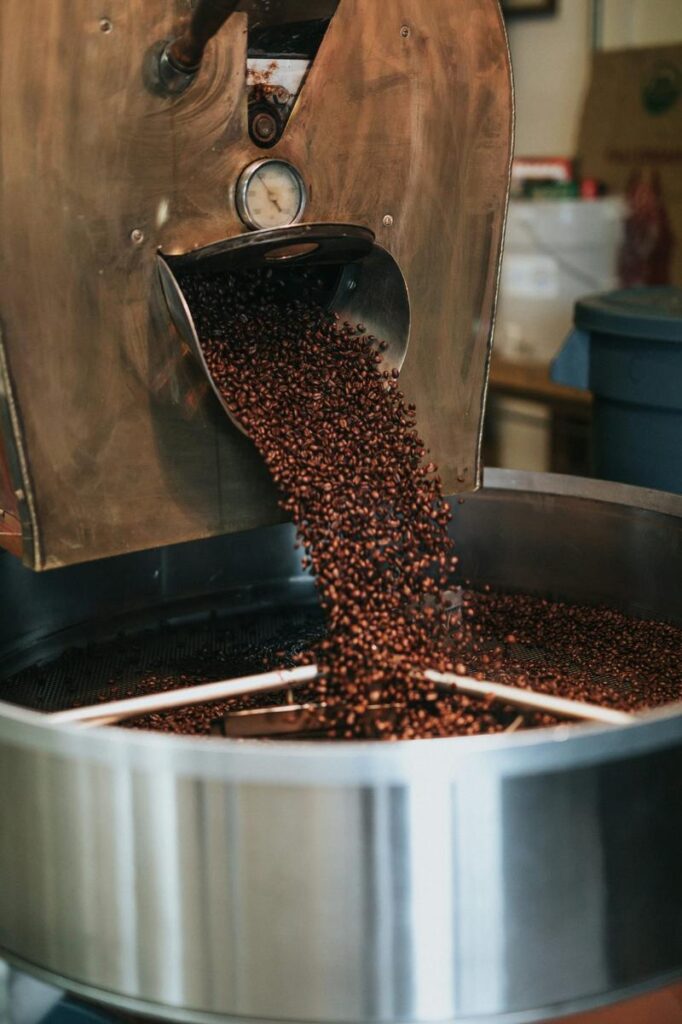
Future Trends in Drip Coffee Bag Packaging
The drip coffee bag packaging industry is evolving with several notable trends:
- Smart Packaging: Integration of QR codes and NFC technology allows consumers to access information about the coffee’s origin, brewing instructions, and sustainability practices.
- Personalization: Customization options for packaging designs and flavors cater to diverse consumer preferences.
- Automation: Advancements in automation are leading to more efficient production lines, reducing labor costs and increasing consistency.
Do not hesitate to contact us if you have any question.