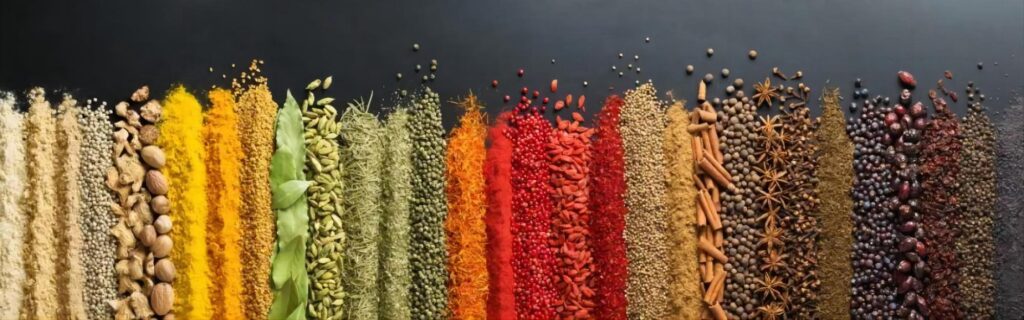
Das neue Euroma-Projekt befindet sich in Zwolle, Niederlande. Die Fabrik hat die Firma Intertaste übernommen und erfolgreich die innovativste Kräuter- und Gewürzfabrik Europas aufgebaut.
Als einer der führenden Hersteller hochwertiger Kräuter- und Gewürzmischungen sowie Texturierungslösungen begleiteten sie Daxner aus Wels (Österreich) bei der Entwicklung, Herstellung und Installation vollautomatischer Fabriklösungssysteme rund um das bewährte Daxner Container Handling System zur verteilten Steuerung System.
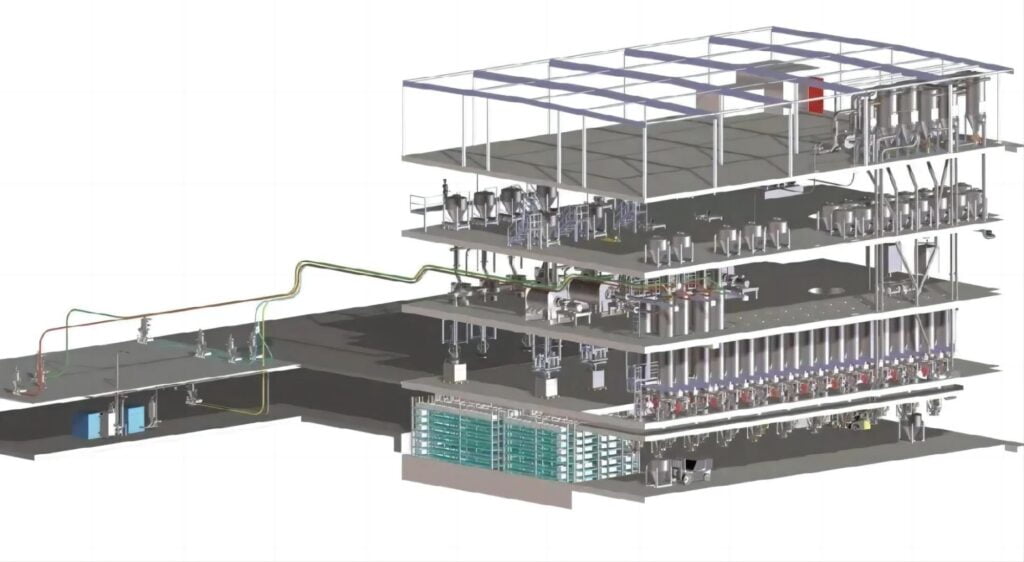
Kontrolle der Kreuzkontamination: Chargendesign von Wendeboxen zur Vermeidung von Kreuzkontaminationen
Staubkontrolle: Produktionsstatus nach Staubkontrolle in Lebensmittelqualität
Intelligenz: Automatisch geführte Fahrzeuge ersetzen Handarbeit
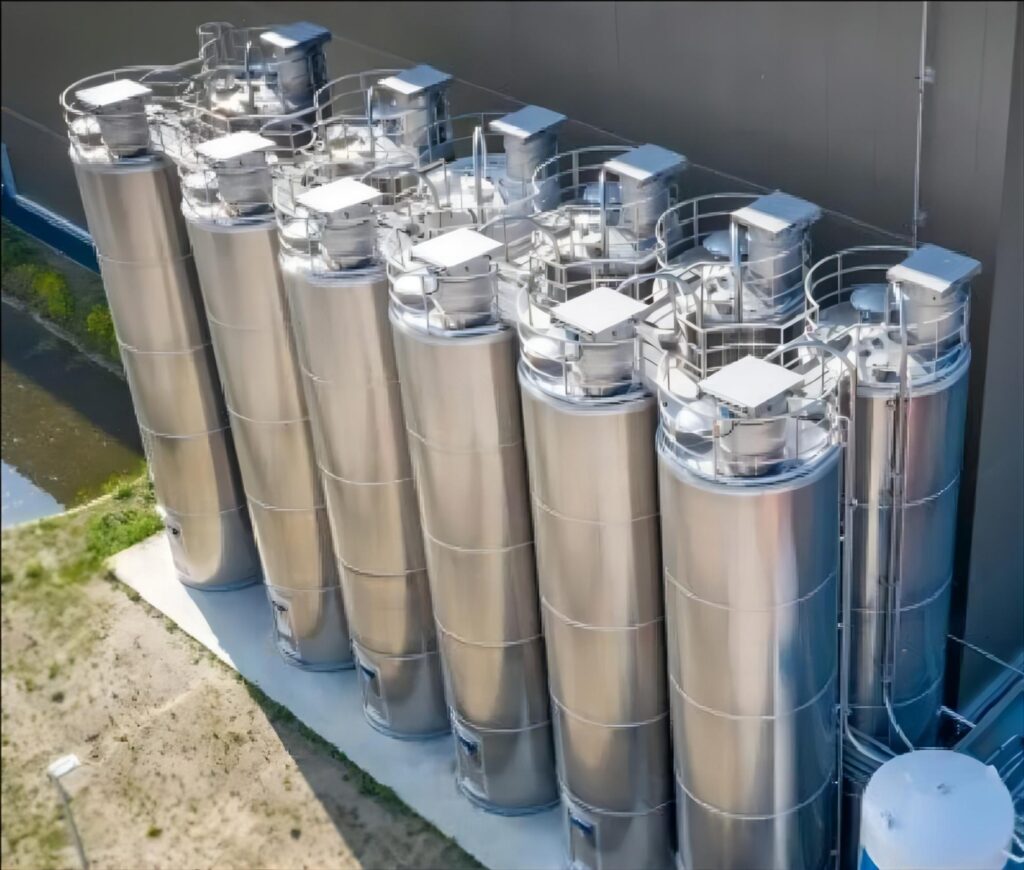
Hersteller von Kräuteraromen
Die Gewürzfabrik wurde 2019 in Betrieb genommen. Erstens ermöglicht die Anlage Euroma, bekannt als Pionier der schonenden Kräuterverarbeitung, die Produktion zu steigern und ein neues Niveau der Lebensmittelsicherheit zu erreichen. Ziel von Euroma ist es, den gesamten Trocknungsprozess in allen bestehenden Anlagen am neuen Produktionsstandort in Zwolle zu vereinheitlichen.
Herr Teun van Veen, Projektmanager bei Euroma, erinnert sich noch gut an den Beginn des Projekts: „Euroma bereitete einen Besuch bei Powtech vor. Durch die Erstellung einer Besucherliste stellten wir fest, dass die Firma Daxner ein Gesamtkonzept für Gewürze und Kräuterpflanzen anbot. Wir haben dies auf der Website von Daxner gefunden. Es wurde ein Referenzartikel erstellt. Wir waren begeistert von dem, was in diesem Artikel geschrieben wurde. Der erste Kontakt wurde hergestellt und wir füllten unsere Anforderungen auf Daxners Fragebogen aus und schickten einige zusätzliche Informationen.“ Anschließend fand bei Powtech ein erstes Treffen statt und Euroma erteilte seinen ersten Werks-Pre-Engineering-Auftrag.
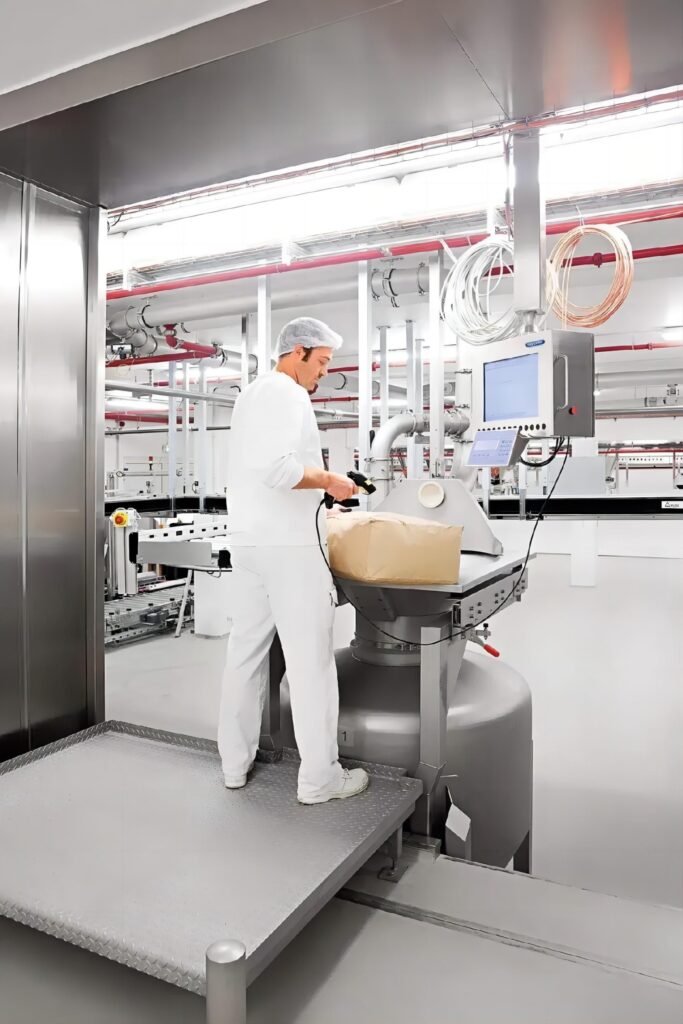
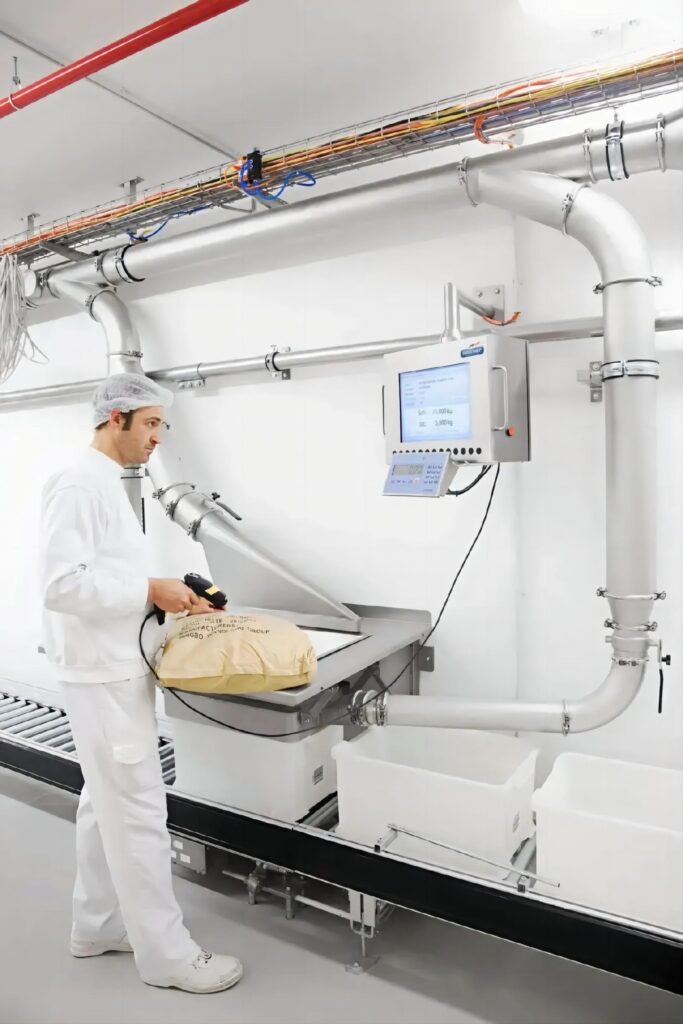
Vollautomatisches Containerhandlingsystem DCS
Das technisch überzeugende Anlagendesign garantiert eine hohe Durchsatzleistung und Dosiergenauigkeit. Die Möglichkeit einer Kreuzkontamination und Staubbildung wird minimiert.
Gemäß den Anforderungen des Hygienic Design sind alle Teile aus Edelstahl gefertigt und leicht zu reinigen. Laserbetriebene Fahrerlose Transportfahrzeuge (FTF), perfekt synchronisiert mit dem vollautomatischen Daxner-Containerhandlingsystem DCS, bewegen sich durch die Produktionsanlage, um wertvolle Trockenteile einzusammeln. Die Rohstoffzutaten werden in große Zutaten, mittlere Zutaten und kleine Zutaten unterteilt. Große Anteile der Trägerstoffe wie Weizenmehl oder Kartoffel- und Maisstärke werden mit Tankwagen transportiert und in 12 großen Außensilos gelagert. Ein pneumatisches Vakuumfördersystem transportiert sie in Tagesbehälter innerhalb der Fabrik.
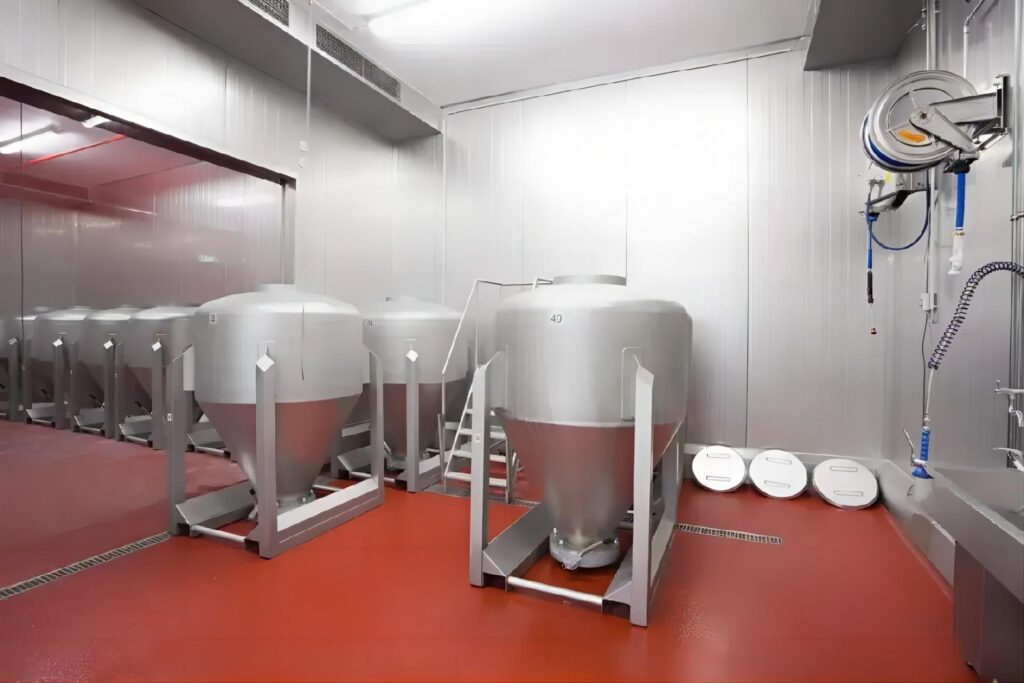
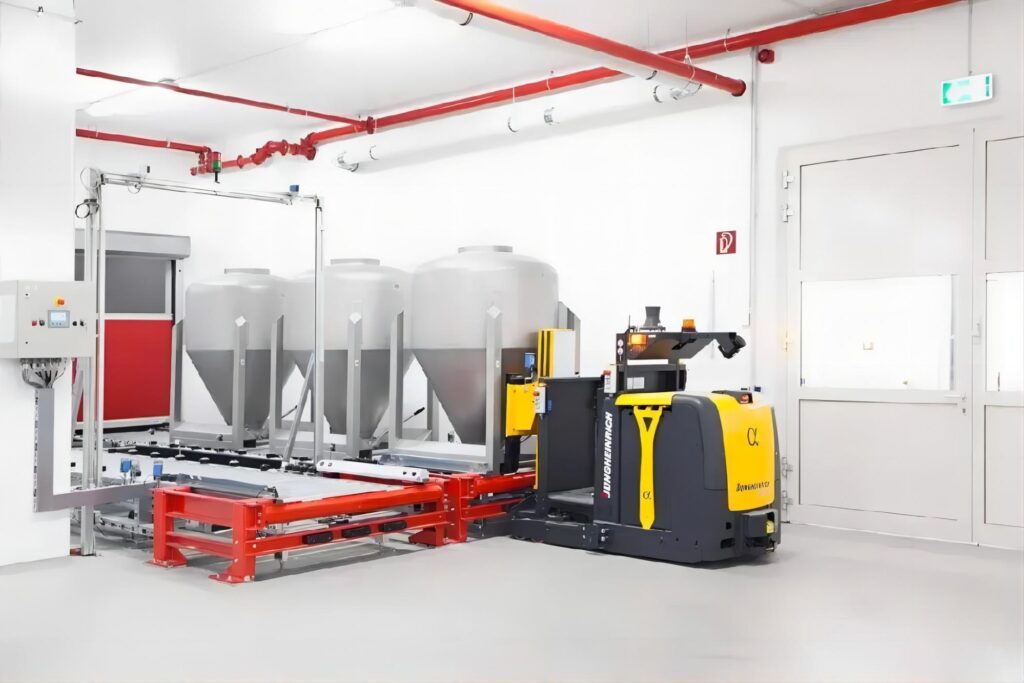
Mobile Sack- und Tonnensack-Importstation
Die Abfüllung großer und mittelgroßer Teile in Tagesbehälter erfolgt über mobile Beutel- und Beutelaufgabestationen. Unterhalb der Tagesumschlagsbox ist eine hochpräzise Waage installiert. Je nach Qualität des Produktes werden dementsprechend separate Tagesbehälter und Wiegesysteme zugeordnet. Durch diese präzise Dosierung wird eine Kreuzvermischung mit allergenen Rohstoffen vermieden.
Sobald alle einzelnen Rohstoffe in die Wiegebehälter dosiert sind, beginnt der Sammelvorgang des Daxner Container Handling Systems DCS in Kombination mit einem Fahrerlosen Transportsystem (FTF). Ein mit einem 1.500-Liter-Behälter beladenes AGV fährt von Wiegebehälter zu Wiegebehälter und befüllt sich mit vorab abgewogenen Rohstoffen. Dieses Konzept spart Zeit: Sobald eine Rohzutat aufgenommen wird, kann der Wiegebehälter sofort den nächsten Behälter anfüllen.
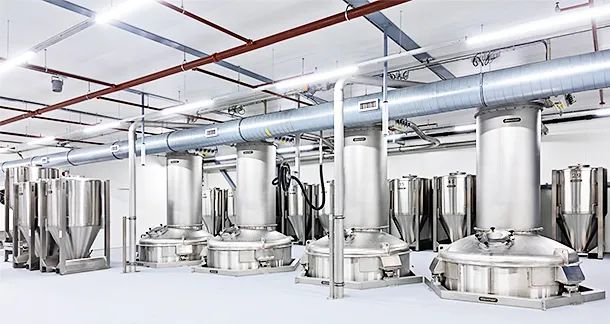
Lieferung von Klein- und Kleinteilen
Die manuelle Beschickung der Klein- und Kleinteilebehälter erfolgt im Erdgeschoss. Nach dem Ware-zur-Person-Konzept werden alle Zutaten zum Betreiber gebracht: Container mit AGVs, Kleinteile in Säcken auf Paletten und vorkommissionierte Kleinteile in Kisten aus dem Kleinteilelager (MCS). Dadurch erreicht das System eine zeitoptimierte Versorgung aller Komponenten, ohne dass der Bediener unnötige Eingriffe vornehmen muss.
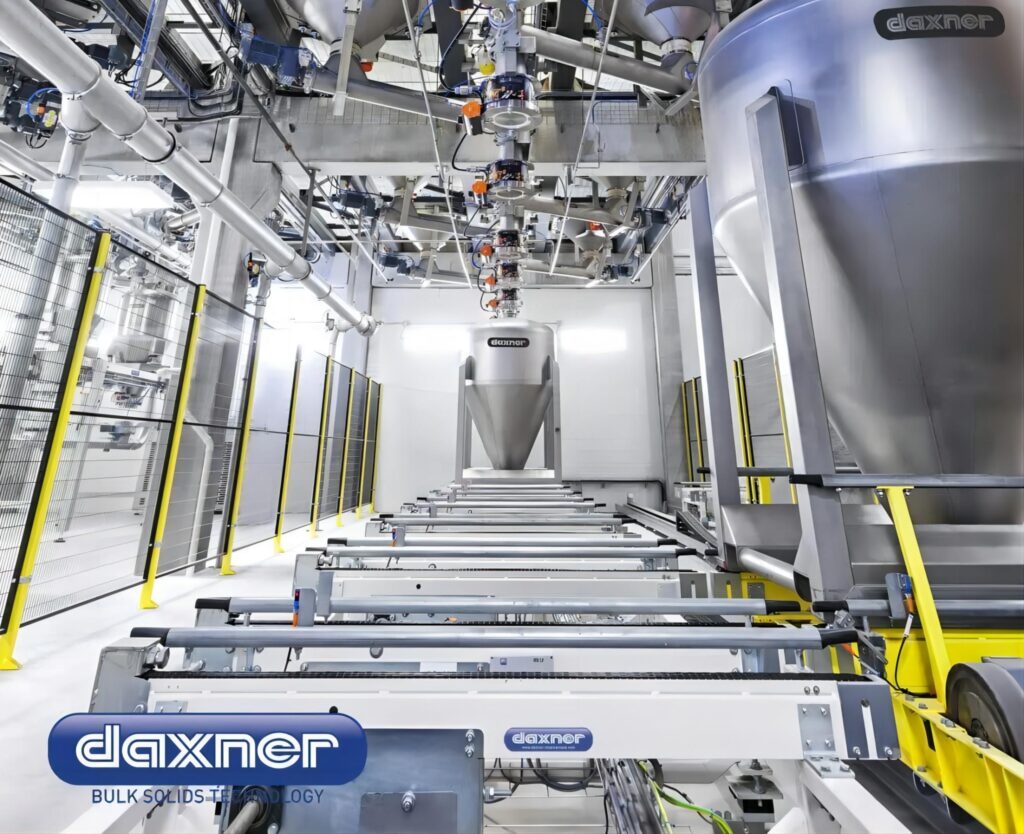
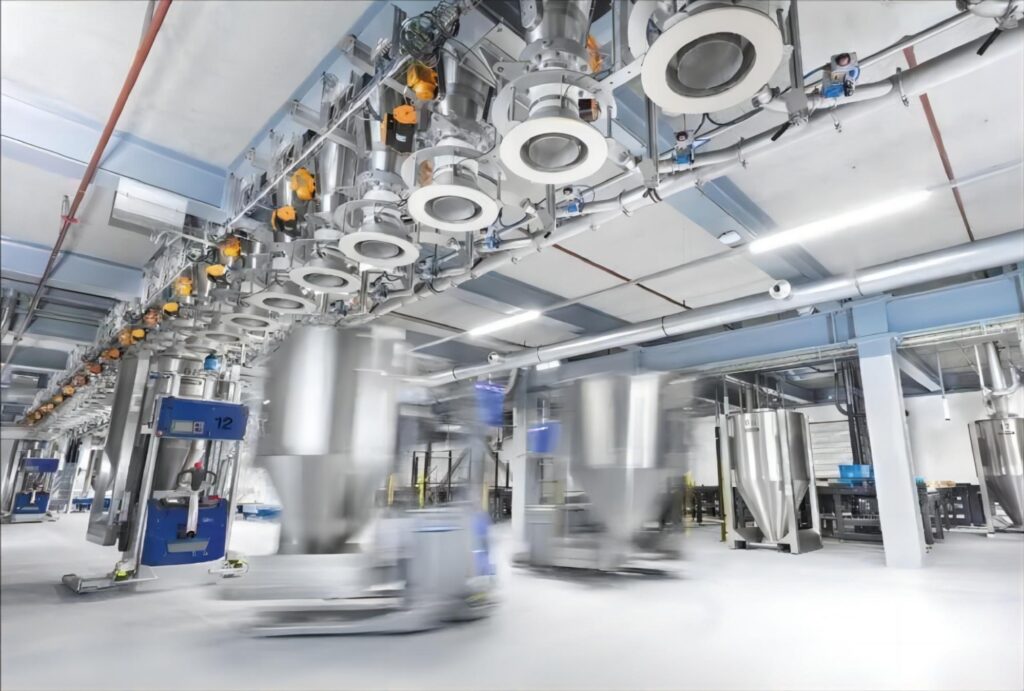
Sobald alle Zutaten in den Behälter gefüllt sind, setzt dieser seinen vollautomatischen Weg zur vorgesehenen Mischlinie fort. Die Container werden mit Hilfe von AGVs zum Containerlift transportiert und auf den Boden über dem Mischer gehoben. Von dort holt ihn ein weiteres FTS ab und platziert den Behälter genau über dem entsprechenden Mischer. Es lässt sich nicht nur der Riegel öffnen, sondern der Mischer kann auch ohne Bedienerhilfe entleert werden. Alle Produkte werden nach der Mischung der Kräuter, Gewürze und anderen Zutaten einer Qualitätskontrolle unterzogen. Die fertige Mischung wird abgewogen, in installierte Großbeutel verpackt und anschließend den entsprechenden Verpackungslinien zugeführt.
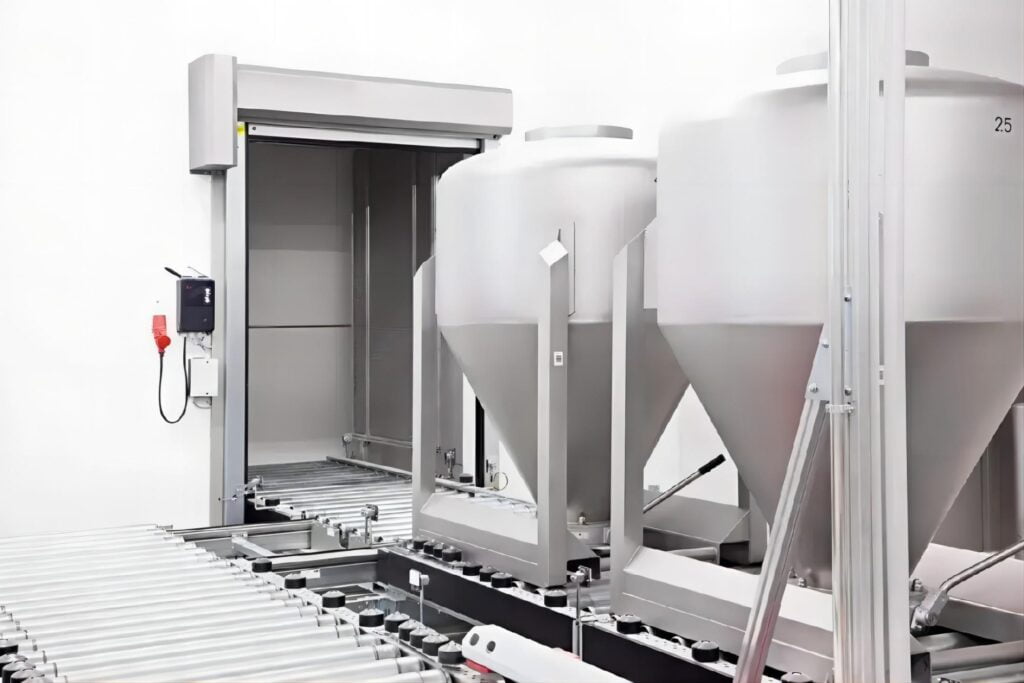
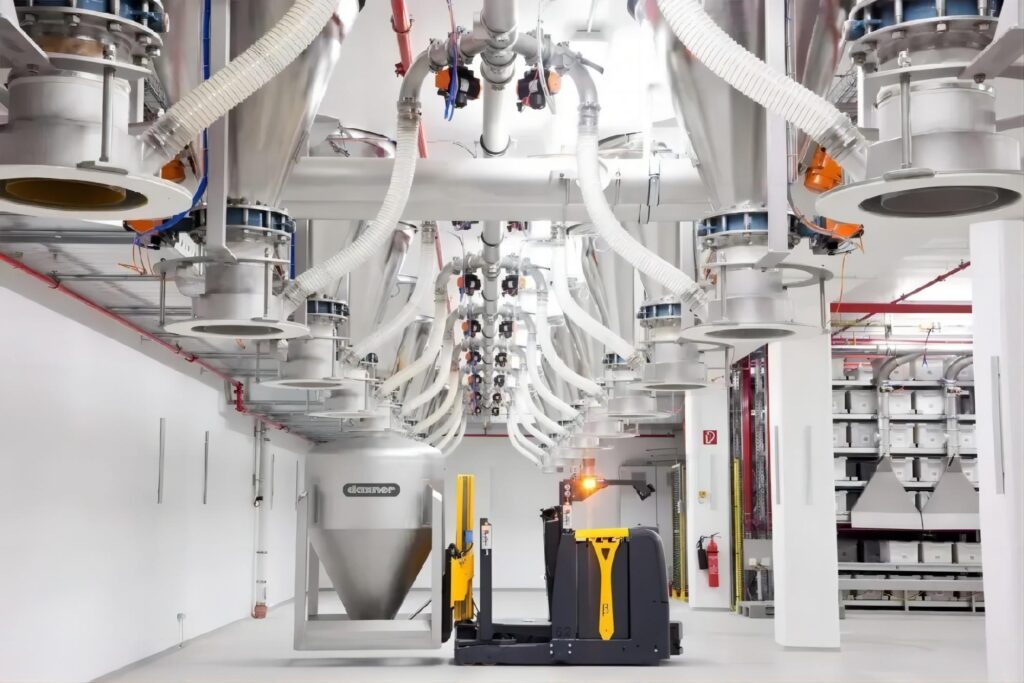
Verschiedene Arten von Kräutermixern bieten große Flexibilität
Verwenden Sie einen Mischer mit einem Fassungsvermögen von 1500 l bis 10 Kubikmetern. Die Versorgung der Mischer kann auf verschiedene Arten erfolgen: direkt aus einem Außensilo, im Container oder per Flüssigkeitsdosierung. Nach dem Mischen wird das Produkt direkt in einen der nachgeschalteten Behälter gefüllt. Die Mischer- und Behälterabmessungen sind optimal aufeinander abgestimmt und bieten große Flexibilität hinsichtlich möglicher Chargengrößen.
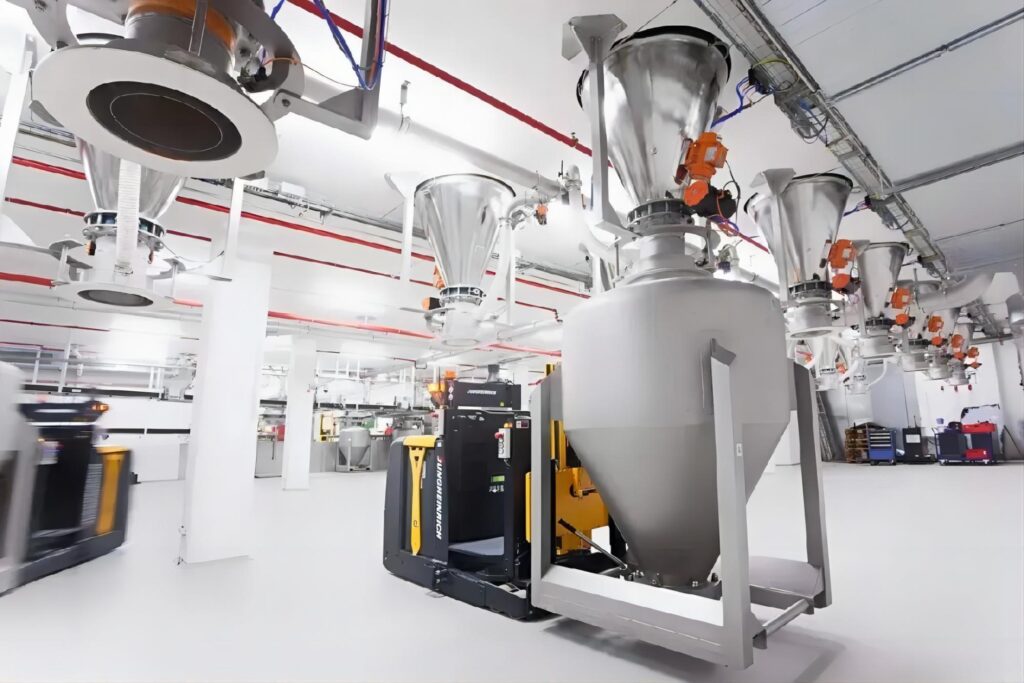
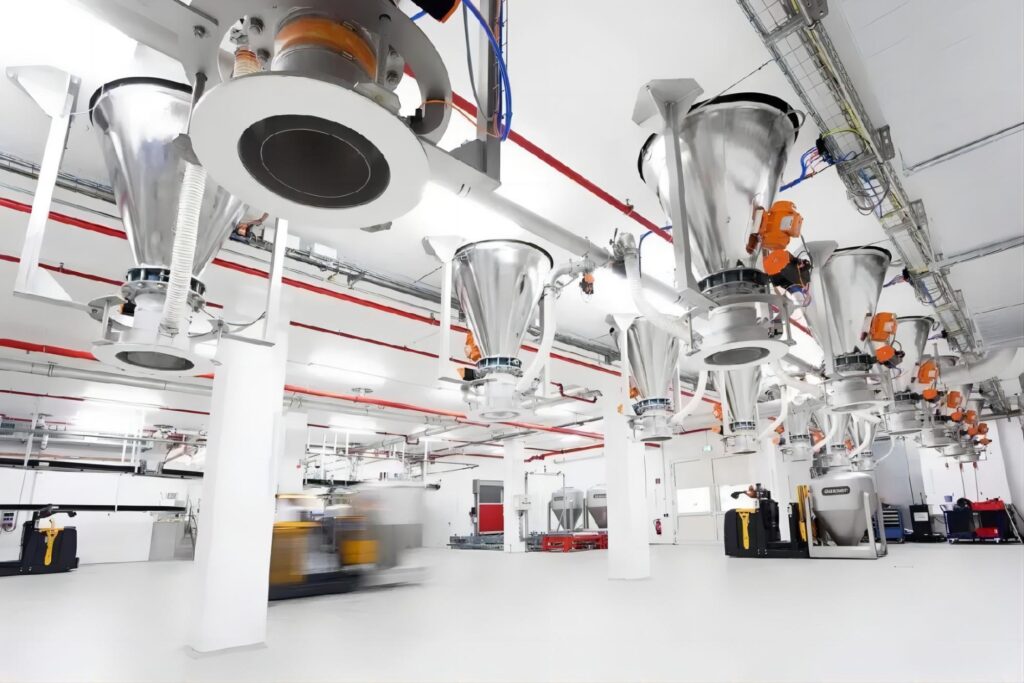
Diese Gestaltungsfreiheit unterstreicht ein weiteres Highlight der Anlage: den Mischer mit einem Fassungsvermögen von 1500 Litern, bei dem das Mischen direkt im Behälter erfolgt. Der Vorteil für den Anwender: Da der Beschickungsprozess des Mischers komplett entfällt, kann der gesamte Prozessschritt eingespart werden.
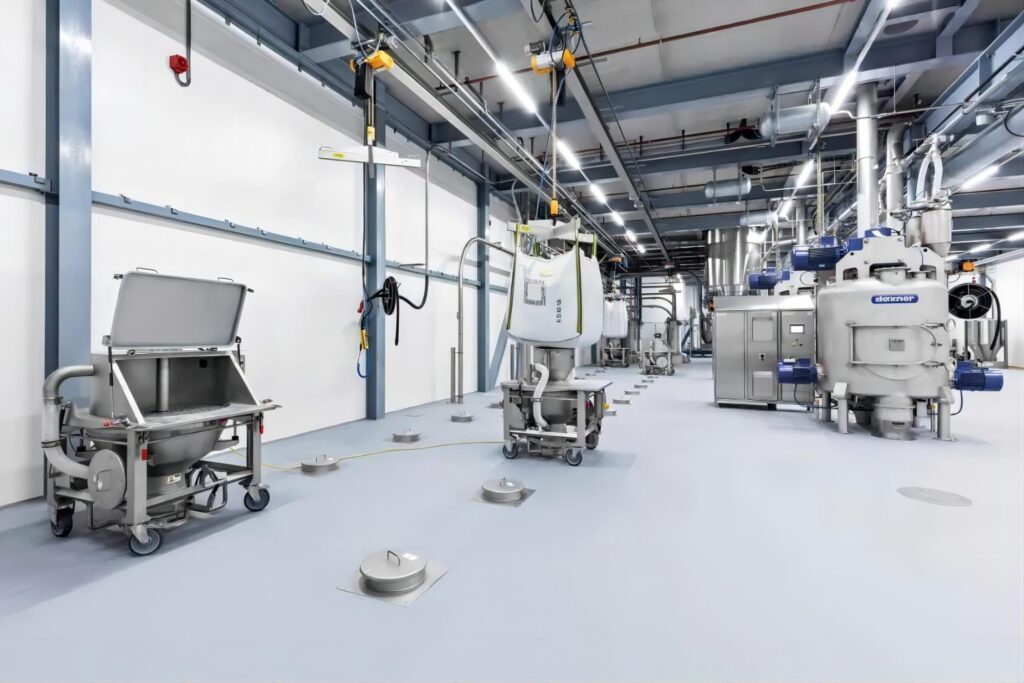
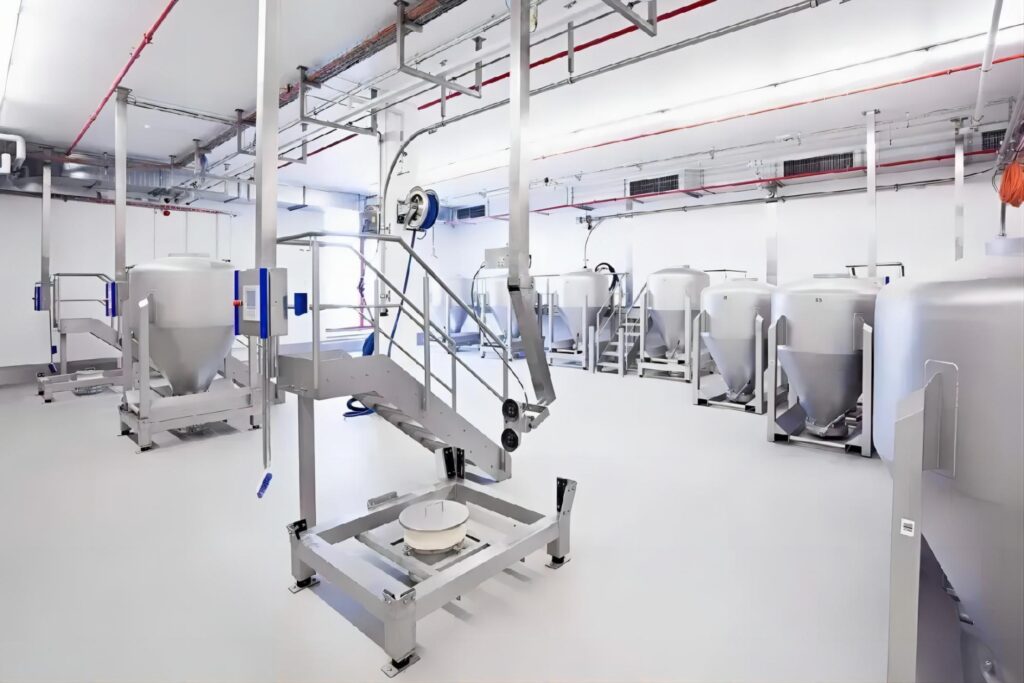
Kräuterverpackung
Nach dem Mischvorgang sammeln fahrerlose Transportfahrzeuge die Behälter mit der fertigen Mischung ein und transportieren sie ohne menschliches Zutun zu einer Entladestation neben der Absackstation. Das Fallsackfüll- und Wiegesystem DAX-PVS (Pinch Valve System) füllt die fertige Mischung in Verkaufsverpackungen ab. Herzstück des DAX-PVS-Systems ist das pneumatische Quetschventil, das für eine präzise Dosierung des Produkts sorgt.
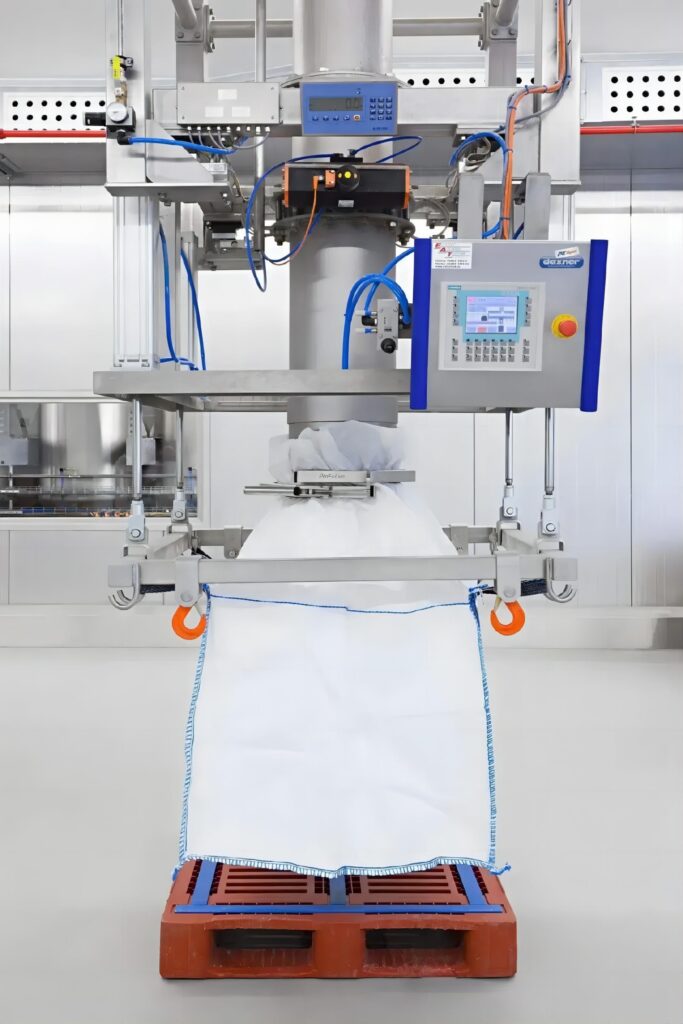
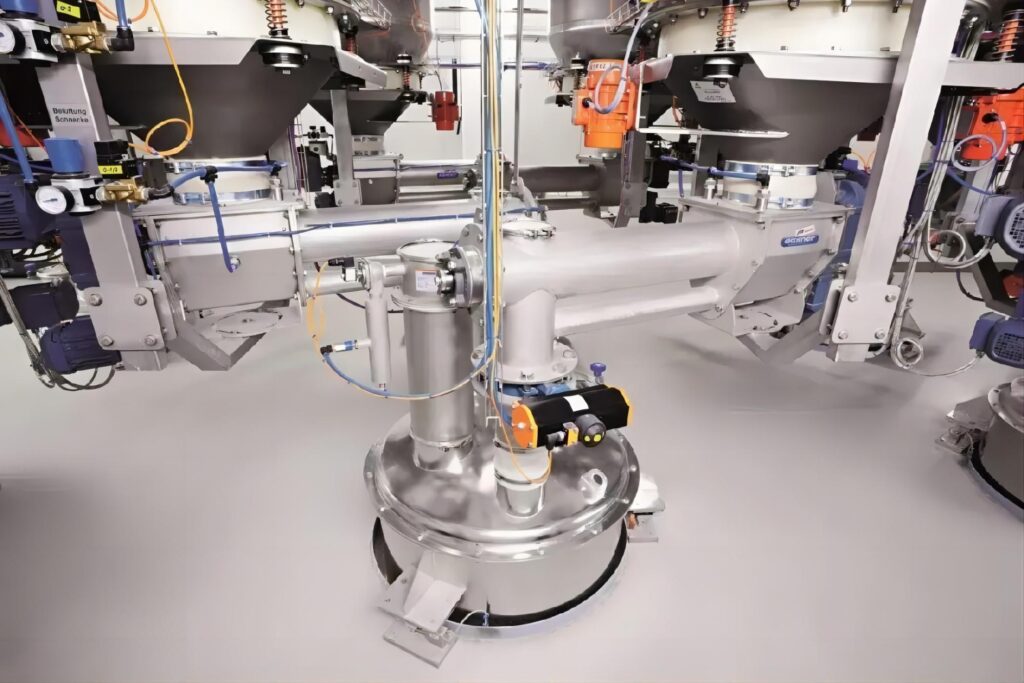
Konform mit HACCP und IFS
Die komplette Misch- und Verpackungslinie ist mit einem Unterdruck-Saugsystem ausgestattet, um die Staubbildung zu minimieren. Eine zentrale Staubabsauganlage garantiert Komfort und Komfort.
DAXNER GMBH
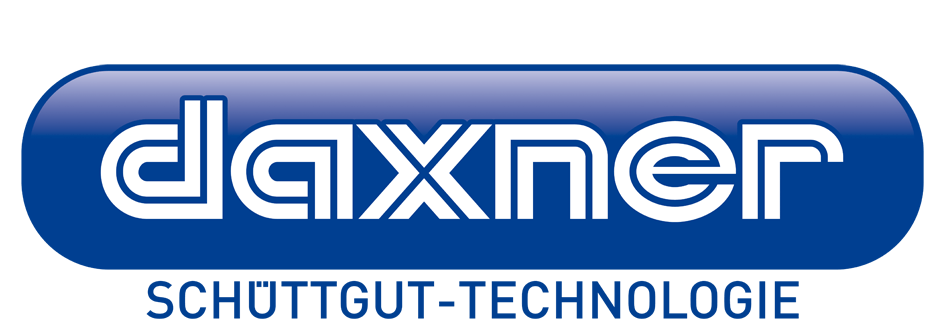
DAXNER International ist ein internationales Materialtransportunternehmen, das 1984 in Wels, Österreich, gegründet wurde. Der Schwerpunkt liegt auf der Lebensmittel-, Brau-, Back-, Futtermittel-, Chemie- und anderen Industrie.
Die Leistung von DAXNER International basiert auf drei Eckpfeilern: Wissen, Kompetenz und Kreativität. Die Stärke des Unternehmens liegt im Gesamtkonzept innovativer Entwicklung und maßgeschneidertem Design. Kann schlüsselfertige Lösungen für High-Tech-Produktionsanlagen anbieten.
DAXNER International hat seinen Hauptsitz in Wels, Wales, Österreich, und seine Ausrüstungsproduktionsbasis befindet sich in Lauda-Königshofen, Deutschland. Das Unternehmen verfügt über einen nahtlosen Service und Support sowie ein starkes Netzwerk internationaler Tochtergesellschaften wie Daxner Deutschland, Daxner SOUTH EAST ASIA, Daxner LATAM, Daxner RUSSIA, Daxner UK und Daxner USA. Das Unternehmen verfügt weltweit über zahlreiche Vertriebs- und Servicepartner.
Firmenüberblick
Gegründet: 1984
Standort: Wels / Österreich
Mitarbeiter 2019: 110
Rechtsform: GmbH
Geschäftsführer / CEO:
Dipl.-Ing. (MS) Christian Daxner, Ing. Johann Daxner
Branchen:
Lebensmittel- und Getränkeindustrie,
Gewürze und Kräuter,
Back- und Konditorzutaten,
Bäckereien,
Tierfutterindustrie,
Industrie (Chemie, Pharma, Kunststoffe, Baustoffe)