¿Alguna vez ha deseado poder probar una nueva solución de automatización antes de comprarla? Esta es la idea detrás de la puesta en marcha virtual... y puede que sea el futuro de la automatización.
Con la puesta en marcha virtual, usted crea un modelo virtual de sus soluciones de automatización ideales. Puede probar esas soluciones, modificarlas y ver cómo funcionará la tecnología de automatización con su proceso específico.
La puesta en marcha de cualquier solución de automatización puede ser un proceso complejo y que requiere mucho tiempo. Con la puesta en marcha virtual, puede utilizar tecnología de simulación robótica para reducir tanto la complejidad como el tiempo. Evita tiempos de inactividad innecesarios porque no es necesario desconectar las máquinas existentes para probar la solución de automatización.
Parece probable que a partir de ahora la puesta en marcha virtual siga siendo un paso fundamental en el proceso de automatización. Si está buscando una manera de agilizar su proceso de implementación, esta opción puede ser la respuesta.
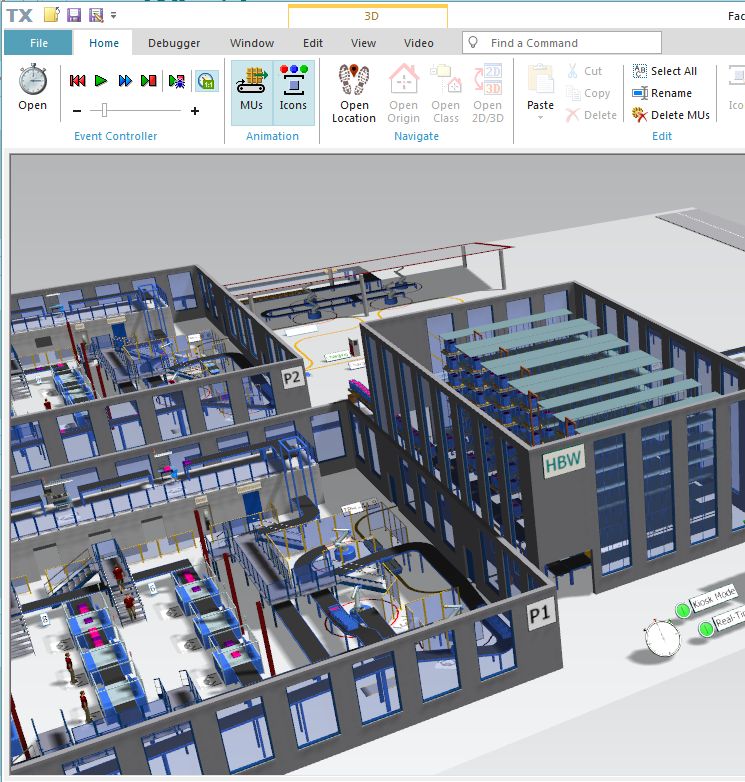
¿Qué es la puesta en marcha virtual?
La puesta en servicio virtual es el uso de tecnología de simulación para diseñar, instalar y probar soluciones de automatización antes de implementar el hardware físico en un entorno de fabricación. Por ejemplo, el software de simulación robótica puede optimizar la implementación de un robot sin tiempos de inactividad innecesarios.
En el centro de cualquier proyecto de puesta en marcha virtual se encuentra el software de simulación. Este software incluirá modelos virtuales de cualquier tecnología de automatización que pueda usarse, así como algoritmos y funcionalidades para probar el funcionamiento de su sistema.
Con las soluciones robóticas, puede utilizar el mismo software de simulación para programar el robot físico. RoboDK incluye funcionalidades de simulación y programación fuera de línea. Una vez que haya terminado de probar su implementación en el simulador, puede conectar su robot físico y descargar el programa directamente al hardware robótico.
La diferencia entre la puesta en servicio virtual y tradicional
¿Es realmente tan diferente la puesta en marcha virtual de la puesta en marcha tradicional?
Existen algunas diferencias clave entre los dos enfoques para encargar un proyecto de automatización.
La puesta en servicio tradicional generalmente ocurre en el lugar físico donde implementará la solución de automatización, como la planta de su fábrica. Trae varias herramientas físicas y equipos de prueba para la resolución manual de problemas. Esto significa que es posible que tenga que cerrar algunos o todos sus procesos de fabricación existentes mientras dure el proyecto de puesta en marcha, lo que puede resultar costoso.
Con la puesta en marcha virtual, usted realiza la mayor parte de la implementación de forma remota y solo llega al sitio al final.
Además, el proceso de puesta en marcha tradicional suele llevar más tiempo y requiere un equipo más grande para la implementación in situ. Con la puesta en marcha virtual, un equipo pequeño o incluso una sola persona puede realizar la mayor parte de la implementación de forma remota.
¿Cómo funciona la puesta en marcha virtual?
La idea básica es crear una simulación o un gemelo digital de su solución de automatización. Este es un modelo virtual que muestra cómo funcionará la máquina (o máquinas) en su proceso.
Utilice este modelo virtual para probar diferentes escenarios y ver cómo afectará esto a la solución de automatización. Esto le ayuda a optimizar la solución antes de llevarla al entorno físico.
La puesta en marcha virtual con un simulador de robot implica:
- Crear o importar modelos virtuales de las partes relevantes de su línea de producción.
- Cargando modelos de su robot desde la Biblioteca de robots, junto con cualquier otro equipo.
- Crear un programa de robot para su aplicación específica.
- Optimizar los diversos aspectos de su solución robótica antes de implementarla en su fábrica.
Al abordar la puesta en marcha de esta manera, puede probar su solución en un entorno controlado y libre de riesgos.
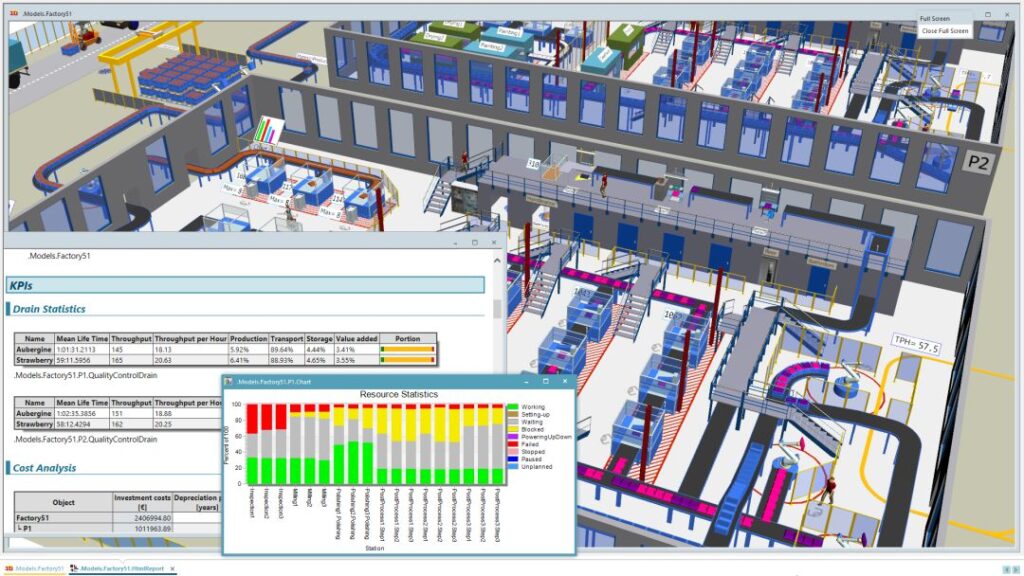
5 beneficios únicos de la puesta en marcha virtual
Aquí hay 5 beneficios únicos de la puesta en servicio virtual:
1. Implementaciones eficientes
Dado que la puesta en marcha virtual reduce significativamente la necesidad de realizar actividades in situ que consumen mucho tiempo, mejora la eficiencia operativa de su implementación. Esto le ayuda a evitar costosos tiempos de inactividad y hace que su proceso sea más eficiente en general.
2. Automatización más segura
Al simular su proyecto de automatización en un entorno virtual, puede probar peligros potenciales de forma segura y controlada. Esto le ayuda a evitar accidentes y lesiones que pueden ocurrir en un proceso de puesta en marcha física tradicional. También le permite probar casos límite peligrosos que serían imposibles de probar con hardware físico.
3. Comunicación del equipo mejorada
Un simulador puede proporcionar una plataforma común para que todos los miembros de su equipo vean, comprendan y sugieran cambios en su solución de automatización. Esto puede ayudar a mejorar la comunicación y evitar posibles malentendidos. Con RoboDK para Web, sus colegas ni siquiera necesitan instalar el software para ver la simulación.
4. Flexibilidad a los cambios
Un beneficio importante de la puesta en marcha virtual es que es fácil realizar cambios o ajustes en su proceso de producción. Puede probar rápidamente nuevas ideas en el simulador, sabiendo con seguridad que no está interrumpiendo su producción.
5. Mejor comprensión de la solución
Finalmente, desarrollar su solución de automatización en un simulador le permite comprender mejor cómo funciona. Al “jugar” con la tecnología en el entorno virtual, rápidamente obtendrá un conocimiento práctico de sus posibilidades y limitaciones. Esto le ayuda a hacer un mejor uso de la tecnología en el mundo real.
¿La puesta en servicio virtual cambiará la automatización?
Con la popularidad cada vez mayor de las herramientas digitales, parece probable que la puesta en marcha virtual haya llegado para quedarse.
La puesta en servicio virtual ayuda a derribar las barreras de entrada a la automatización que han restringido la adopción de robots por parte de muchos fabricantes. Puede permitir que cualquier persona implemente de manera rápida y eficiente tecnologías de automatización en sus procesos de fabricación y, al mismo tiempo, reduzca los riesgos asociados con tiempos de inactividad innecesarios.
Cuando implementa su tecnología robótica con puesta en marcha virtual, aumenta sus posibilidades de que el proyecto de automatización sea un éxito. Esto hace que la robótica como solución sea menos riesgosa y más valiosa.
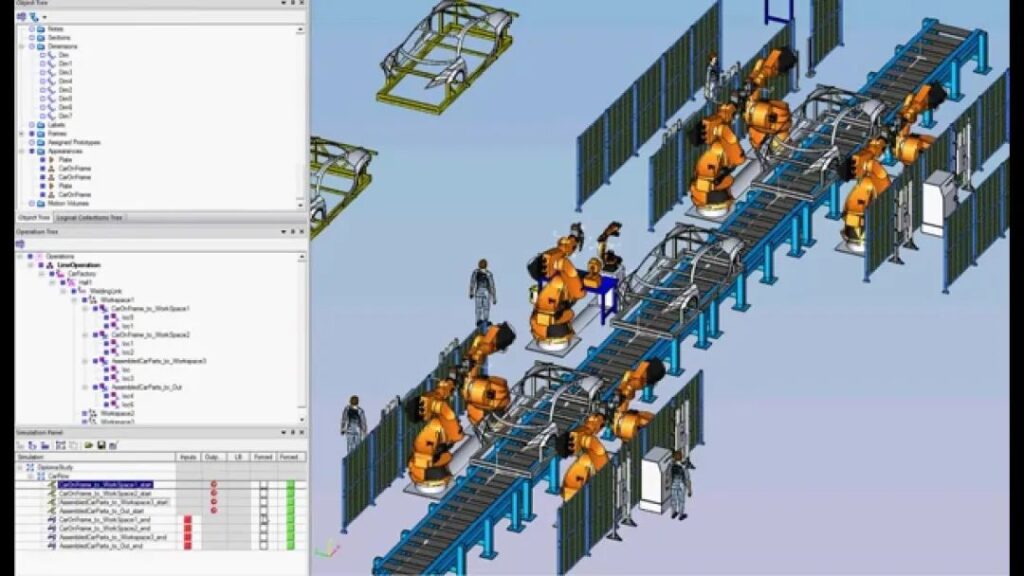
Tendencias tecnológicas en el diseño e ingeniería de instalaciones farmacéuticas.
La fabricación farmacéutica evoluciona continuamente al ritmo de los avances tecnológicos, a medida que las empresas buscan reducir costos, optimizar completamente los recursos y agilizar las operaciones. Esto se extiende al diseño e ingeniería de instalaciones. Este artículo explora varias tendencias tecnológicas emergentes relacionadas con el diseño y la ingeniería de instalaciones que benefician significativamente a las empresas farmacéuticas.
Puesta en marcha virtual
La construcción y puesta en marcha de nuevas instalaciones farmacéuticas requiere mucho tiempo y dinero. PhRMA estima que construir una nueva instalación puede costar hasta $2 mil millones y tardar entre 5 y 10 años en completarse. Teniendo esto en cuenta, es fundamental que cada paso del proceso de puesta en servicio y construcción se ejecute sin problemas, de manera eficiente y rentable para que las operaciones estén en marcha y generen un retorno de la inversión lo más rápido posible.
A menudo, una parte importante de ese costo en términos de tiempo y capital proviene directamente de la puesta en servicio de las instalaciones, líneas y equipos. Los cambios o retrasos en las últimas etapas en el diseño, los requisitos y las configuraciones de las instalaciones o equipos deben minimizarse o, idealmente, eliminarse por completo para reducir el costo general de la puesta en servicio de las instalaciones. Para resolver esto, los fabricantes farmacéuticos pueden recurrir a la puesta en marcha virtual, un enfoque que combina el desarrollo y las pruebas tradicionales y virtuales mediante la emulación. A diferencia de la puesta en servicio física, la puesta en servicio virtual puede comenzar mucho antes de que se compre o construya cualquier hardware. Este enfoque permite ahorrar hasta 40% en tiempo de puesta en servicio en comparación con la puesta en servicio convencional, lo que reduce el riesgo y la incertidumbre, ofrece mayor seguridad y agilidad y reduce los costos de los cambios de diseño.
Simulación, emulación y gemelos digitales
Un gemelo digital es una representación virtual de una entidad, sistema o proceso físico del mundo real que está sincronizado con la entidad física. El gemelo digital y el elemento de fabricación observable (OME) generalmente se sincronizan mediante la propagación de los datos del sensor desde la entidad física al gemelo digital. Los gemelos digitales se pueden crear a partir de simulaciones o emulaciones, pero deben estar sincronizados con OME. La frecuencia y fidelidad de las emulaciones/simulaciones sincronizadas deben ser apropiadas para la tarea para la que están diseñadas.
Los gemelos digitales se pueden construir a partir de varios paquetes de software comerciales o de código abierto diferentes, pero siempre incluyen el elemento físico, un mecanismo de sincronización y un paquete de software utilizado que ejecuta el modelo/representación virtual (generalmente derivado de CAE/software multifísico). La creación de un gemelo digital requiere que los elementos de interés para la OME se repliquen con precisión en la representación virtual. Para los equipos de producción, esto generalmente implica la definición de sistemas de proceso o mecatrónicos, incluidos motores, actuadores e instrumentación, conectados a un sistema de automatización que ejecuta software de aplicación específica.
El valor de implementar gemelos digitales con equipos de producción es la posibilidad de estimar el estado del sistema físico más allá de lo que es inmediatamente observable. Las aplicaciones típicas de esto incluyen detección suave, corrección adaptativa de fallas, control predictivo de modelos y mantenimiento predictivo. Los equipos de producción pueden encajar en un gemelo digital más grande de un proceso de fabricación completo para respaldar la fabricación puntual impulsada por la demanda.
En aplicaciones de puesta en servicio virtual, es posible que no sea posible un gemelo digital ya que es posible que el equipo físico no exista. En su lugar, se implementa un modelo del equipo de producción junto con el sistema de control, de modo que ambos puedan desarrollarse conjuntamente. El sistema de control considera el modelo del equipo de producción como una emulación, ya que el sistema de control puede interactuar naturalmente con el modelo a través de salidas de comando y retroalimentación de estado (conocido como Hardware-In-the-Loop). Para que esta técnica tenga éxito, el modelo del equipo de producción debe representar con precisión el comportamiento concreto del sistema físico.
La puesta en marcha virtual basada en emulación conduce a una valiosa reducción del riesgo del proyecto desde la perspectiva de evitar errores y cumplir los plazos del proyecto. Como los escenarios y las opciones de diseño se pueden probar minuciosamente sin equipo físico, los ingenieros pueden probar y verificar varios elementos del sistema, incluidos módulos de software específicos de la aplicación, configuración de recetas, modos de falla y recuperación, y eficacia de la interfaz de usuario sin depender del equipo de prueba programado o estar encendido. sitio. Como resultado, los proyectos que emplean la puesta en marcha virtual a menudo se implementan con menos tiempo de puesta en marcha en persona y, en general, son más seguros para las personas y las propiedades.
Una vez puesto en marcha y validado el equipo, la emulación de puesta en marcha virtual puede continuar su uso como gemelo digital sincronizado al equipo físico. Como el modelo ya está construido, resulta inmediatamente útil como representación idealizada del sistema físico. Los ingenieros pueden utilizar este gemelo digital para optimizar el diseño de instalaciones, el diseño de sistemas, las operaciones de la línea de producción y los requisitos de plantas y maquinaria, entre otros elementos.
Infraestructura como código
Desde un ángulo de convergencia de TI/OT, la puesta en marcha virtual permite el uso de conceptos de TI ágiles para desarrollar procesos como la infraestructura como código en el espacio OT, con el objetivo de avanzar hacia la automatización del desarrollo de código y la configuración de la infraestructura.
La adopción de estos conceptos de TI cambiará fundamentalmente los flujos de trabajo de los ingenieros de OT. En lugar de crear sistemas y códigos desde cero, como era el caso de los sistemas de control distribuido (DCS) heredados, el proceso se parecerá mucho más a una función de desarrollo de software ágil, en la que los ingenieros se centrarán más en mantener los sistemas de software automatizados que en desarrollar la aplicación. código e infraestructura. Para los usuarios finales, esto podría significar que las arduas tareas de instalar, configurar y parchear la infraestructura para los sistemas de control se convertirían en un flujo de trabajo automatizado. Para los fabricantes de máquinas, esto podría resultar en un sistema de procesamiento de pedidos que envía una configuración para construir dinámicamente infraestructura de automatización y código de aplicación según las opciones seleccionadas por el cliente sin la participación de un ingeniero.
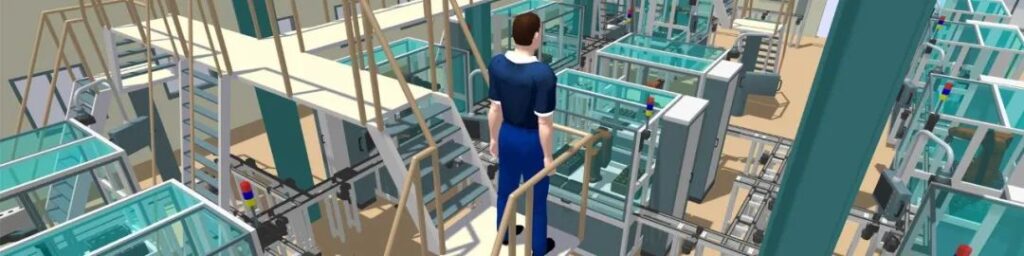
Orquestación de equipos OEM
Los equipos OEM forman la base de las modernas plantas modulares de fabricación farmacéutica al brindar la flexibilidad de elegir y combinar las mejores soluciones de equipos para procesos específicos. La puesta en marcha y validación de equipos OEM es generalmente un proceso más rápido ya que los fabricantes reciben unidades preensambladas y programadas específicamente. Además, los OEM suelen suministrar equipos en un estado listo para la validación, lo que facilita la calificación del equipo para su uso en las instalaciones de CGMP. No es necesario depender de recursos internos o de terceros para la construcción de equipos y el desarrollo de códigos de aplicaciones. Sin embargo, pueden surgir desafíos debido a los diferentes estándares de conectividad e interfaces entre varios proveedores de equipos, lo que dificulta la integración de múltiples equipos en un sistema de control unificado. Aquí es donde entra en juego la orquestación de equipos OEM.
La necesidad de una estrategia de orquestación
Sin un enfoque estratégico y especificaciones claras, el uso de equipos OEM da como resultado islas de automatización fragmentadas. Esta falta de estrategia suele deberse a una colaboración tardía con los proveedores de equipos por parte del usuario final. Cuando la automatización no se considera en el proceso inicial de adquisición de equipos, los ingenieros a menudo tienen dificultades para integrar los equipos o dependen de empresas de ingeniería para manejar la integración. Este proceso de última etapa de ensamblar equipos como una ocurrencia tardía puede llevar, en el mejor de los casos, a una capacidad de interfaz limitada dentro de la planta. En el peor de los casos, todo el proceso puede resultar contraproducente al consumir mucho tiempo y ser costoso sin aumentar la madurez digital.
Para resolver estos problemas, los fabricantes farmacéuticos pueden adoptar un plan holístico para la orquestación de equipos OEM para automatizar y coordinar varios componentes para que funcionen juntos sin problemas desde las fases tempranas de especificación y diseño de las instalaciones. Tener estándares integrales establecidos antes de comprar cualquier equipo permite al usuario final trabajar en colaboración con los proveedores de sus equipos, lo que brinda al OEM la oportunidad de diferenciarse en cómo sus equipos pueden encajar en una plataforma de automatización unificada. Para el usuario final, esto simplifica la capacitación cruzada y estandariza las interfaces, los sistemas de alerta, los diagnósticos y la gestión de recetas. Esto reduce los costos, agiliza las operaciones y da como resultado una construcción, puesta en servicio y calificación de las instalaciones más rápidas.
Aprovechando las interfaces estandarizadas
Los usuarios finales exigen equipos OEM que vengan con capacidad plug-and-produce para integrarse con cualquier sistema de control distribuido (DCS) o sistema de supervisión, control y adquisición de datos (SCADA). Esta capacidad de conectar y producir estandariza los servicios principales de automatización, como interfaces de equipos y gestión de recetas, pantallas de interfaz de usuario, pistas de auditoría y gestión de alarmas en equipos dispares. Un estándar plug-and-produce conecta sistemáticamente todos estos elementos y los coordina utilizando interfaces estandarizadas, como el paquete de tipo de módulo NAMUR (MTP) y protocolos modernos, como OPC Unified Architecture (OPCUA). La integración de todas estas plataformas dispares aporta coherencia, ahorra tiempo y esfuerzo en la integración y hace que plug-and-produce sea una tecnología viable para las instalaciones del futuro.
Estas tecnologías deben verse como un complemento a una estrategia cohesiva para la orquestación de OEM en lugar de reemplazar todo el trabajo realizado con colaboración entre organizaciones y especificaciones integrales. No existe un botón mágico para integrar equipos a la perfección para ofrecer conjuntos comunes de servicios y las relaciones constructivas del usuario final con sus proveedores de equipos y tecnología desempeñan un papel importante en una estrategia de orquestación OEM eficaz. Piense en esta situación: una planta construida enteramente con equipo de caja negra con una interfaz estandarizada podría ser rápida de integrar, pero sería difícil y costosa para un usuario final mantenerla a largo plazo debido a la gestión de numerosos contratos de soporte, piezas de repuesto dispares y la falta de de coherencia o incluso acceso al software de aplicación en el equipo OEM.
Una multitud de beneficios
En pocas palabras, la orquestación de equipos OEM facilita el trabajo de crear una plataforma de automatización unificada para una instalación. En última instancia, esto conduce a un tiempo de comercialización más rápido y a un menor costo total de propiedad para el usuario final. La orquestación efectiva permite la integración de diferentes componentes OEM de una manera que permite una fácil personalización y escalabilidad, la incorporación de nuevos equipos a los sistemas existentes y una integración perfecta de futuras actualizaciones y expansiones. El tiempo de inactividad y el tiempo medio de reparación (MTTR) se reducen mediante una solución de problemas y un mantenimiento simplificados.
Medicamentos de terapia avanzada
Otra tendencia emergente relacionada con la ingeniería de instalaciones es el cambio de la automatización industrial para encajar en el espacio de los productos medicinales de terapia avanzada (ATMP). Muchas de estas terapias son autólogas, lo que significa que provienen de una persona y luego se transmiten a la misma persona. Los volúmenes de producción de estas terapias autólogas son muy pequeños, a menudo en mililitros. Los sistemas de automatización existentes están diseñados para producir a mayor escala, por lo que el concepto aquí es miniaturizar las tecnologías de automatización para que funcionen en unidades o instrumentos de mesa. Estas unidades de mesa pueden luego organizarse en un tren de procesos coordinado para realizar la terapia, y el proceso se puede ampliar para dar cabida a más trenes de procesos para más pacientes individuales.
La clave del éxito de esta estrategia estará en la voluntad del proveedor de automatización de reducir su tecnología para ofrecer las mismas capacidades comerciales de software y hardware disponibles para equipos de mesa. Esto será vital para limitar la cantidad de retrabajo necesario para la transferencia de tecnología desde el espacio de desarrollo de procesos (PD) a la fabricación cGMP para estas terapias avanzadas. La colaboración con un proveedor de automatización que tenga la capacidad de reducir y operar de manera flexible en estos trenes dispares de equipos industriales y de laboratorio para garantizar la precisión y la seguridad del paciente es crucial.
Desde el inicio hasta la finalización
Las empresas farmacéuticas están adoptando activamente tecnologías para mejorar la productividad, la eficiencia y el retorno de la inversión y mantener una ventaja competitiva. Se están adoptando iniciativas como la puesta en marcha virtual y la orquestación de equipos OEM para acelerar la introducción de nuevas capacidades y capacidades, así como para optimizar las operaciones de las instalaciones para eventualmente llegar a una instalación adaptable.
Utilizando la puesta en servicio virtual, las instalaciones se pueden diseñar, modelar, diseñar y probar antes de que comience el trabajo físico. Este enfoque permite la optimización de diversos aspectos como el diseño, la productividad, el rendimiento, el flujo y la eficiencia energética. La orquestación de equipos OEM automatiza los procesos y estandariza las interfaces, lo que facilita el trabajo de crear una plataforma de automatización unificada para una instalación que, en última instancia, conducirá a un tiempo de comercialización más rápido y un menor costo total de propiedad para el usuario final.
Las empresas farmacéuticas que aprovechen el poder de las nuevas tecnologías estarán mejor equipadas para optimizar los procesos de sus instalaciones desde el inicio hasta su finalización.
Conclusión
La puesta en marcha virtual está a la vanguardia de los avances tecnológicos en automatización y ofrece un enfoque transformador para las industrias que buscan integrar soluciones de automatización de manera más efectiva. Al aprovechar la tecnología de simulación, la puesta en servicio virtual permite a las empresas diseñar, probar y perfeccionar sistemas de automatización en un entorno digital antes de la implementación física. Este proceso no solo mejora la eficiencia y la seguridad, sino que también fomenta una mejor colaboración en equipo y la adaptabilidad a los cambios, lo que garantiza una comprensión integral de las capacidades y limitaciones de la solución.
La distinción entre puesta en servicio virtual y tradicional subraya los avances y eficiencias obtenidas a través de simulaciones digitales. La puesta en servicio virtual minimiza la necesidad de realizar extensas actividades in situ, reduce los riesgos asociados con las pruebas físicas y acelera el proceso de implementación, lo que la convierte en una estrategia fundamental para las industrias que buscan adoptar tecnologías de automatización.
Con la creciente integración de herramientas digitales en la fabricación y la continua evolución del software de simulación, la puesta en marcha virtual está preparada para convertirse en un componente integral de los proyectos de automatización. Derriba las barreras para la adopción de la automatización al mitigar los riesgos y reducir el tiempo de inactividad, democratizando así el acceso a tecnologías de fabricación avanzadas.
A medida que las industrias continúan enfrentando los desafíos de adoptar nuevas tecnologías, no se puede subestimar el papel de la puesta en servicio virtual para facilitar una integración más fluida, segura y rentable de las soluciones de automatización. Es un testimonio del poder de la transformación digital en la fabricación, y ofrece una visión de un futuro en el que los ámbitos virtual y físico convergen para optimizar los procesos de producción e impulsar la innovación.
Gracias por que Alex Owen-Hill y John Hatzis compartan la idea.