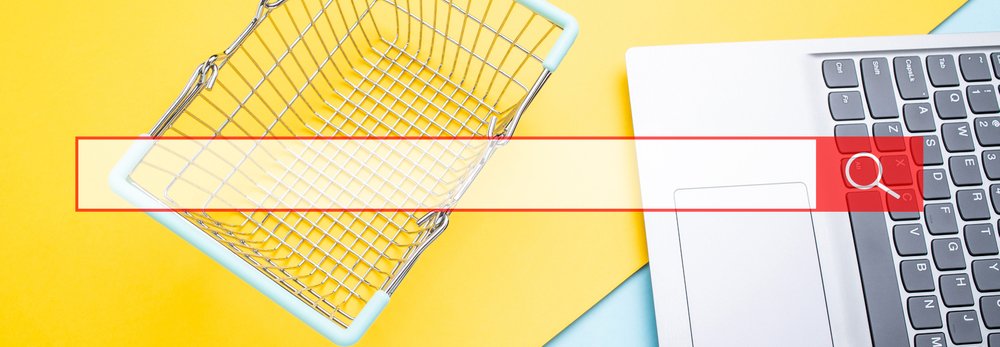
Packaging machinery has evolved tremendously over the last century to meet the demands of the modern food and consumer goods industry. Originally, packaging was done manually by skilled workers but early machines soon came into use to automate and speed up the process. Over time, machinery has become more complex, precise, and automated with the help of robotics and sensors.
One important type of packaging machine is the flow wrapper. Flow wrappers wrap products in film and seal them to create pouches or bags. They work by continuously feeding film from a roll while conveying individual products into the film to be wrapped. The film is then sealed on all sides to form a package around the product.
Flow wrappers offer several advantages over manual or other types of packaging. They can achieve very high speeds of up to 200 packages per minute, providing significantly higher output. They also offer consistency in package quality and shape with precision controls and settings. Flow wrapping is suitable for a wide range of products from snacks and confectionery to pharmaceuticals. It helps protect products, extend shelf life, and provide an appealing presentation for retail.
What is a Flow Wrapper?
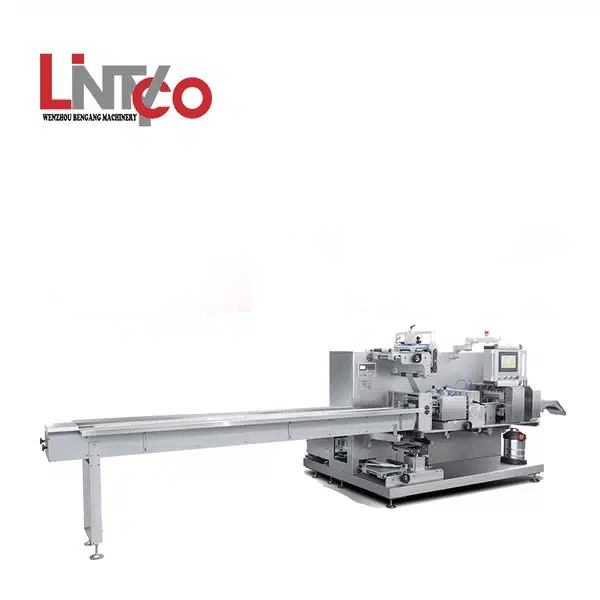
A flow wrapper is a type of packaging machine that wraps products in film to form pouches or bags. In simple terms, a flow wrapper continuously feeds web film from a roll while conveying products into the moving film to be wrapped.
The basic components and functioning of a flow wrapper are as follows:
โขFilm roll โ The film roll contains the plastic or foil sheet that will form the package.
โขConveyor belt โ The conveyor belt intermittently moves products into the film wrapping area.
โขWrapping section โ As the film moves continuously, individual products are conveyed into the wrapping section where the film is wrapped around the product and sealed.
โขSealing section โ After the product is wrapped, the film edges are sealed together using heat, ultrasonic energy, or adhesive to form a finished pouch or bag.
โขCutting section โ The new package is then cut away from the rest of the film using blades or hot-wire cutting.
Based on configuration, there are 3 main types of flow wrappers:
โขTube flow wrappers form a tubular package around the product.
โขBack wrap flow wrappers feed film from the rear and wrap the product from behind.
โขSide wrap flow wrappers feed film from one side and wrap the product laterally.
Flow wrappers offer a versatile packaging solution that can handle a wide range of product types and shapes at high speeds. The choice of flow wrapper type depends on factors like product dimensions, required package style, and output goals.
How Does a Flow Wrapper Work?
The working of a flow wrapper can be explained in 6 main steps:
Unwinding of film โ The process begins with a roll of packaging film which is unwound continuously from the roll. The film is pulled forward by rollers at a controlled speed.
Product feeding โ Using an intermittent conveyor belt, individual products to be wrapped are fed into the film wrapping section at precise timings.
Wrapping โ As the film moves continuously, the product is inserted into the wrapping area. The moving film wraps around the product from all sides and is pulled taut.
Sealing โ The edges of the film are secured together using one of the sealing methods. This forms an airtight seal around the product, completing the pouch or bag.
Cutting โ The new package is cut away from the rest of the film using blades, hot wires or laser cutting. This separates individual wrapped products ready for the next stage.
Dispensing of packages โ The wrapped products are then discharged from the wrapping area onto a conveyor belt for further processing or packaging.
For different flow wrapper types:
In tube flow wrappers, the product drops into a tubular film sleeve which is then sealed at the top and bottom.
Back wrap flow wrappers feed film from behind the product, wrapping the front and sides.
Side wrap flow wrappers feed film from one edge, rotating the product as needed to achieve a complete wrap.
By adjusting the film feeding, wrapping, and sealing controls, flow wrappers can accommodate a wide range of products. The type of film, energy source for sealing, and speed of operation can also be varied as per packaging requirements.
Key Features and Benefits of Flow Wrappers
Speed and Efficiency:
Flow wrappers can operate at very high speeds of up to 200 packages per minute depending on the model and product size. This level of output and efficiency is much higher than manual wrapping methods. The continuous film feeding and automated product insertion allows flow wrappers to maintain a steady wrapping rhythm for high throughput.
Versatility: Ability to Handle a Wide Range of Products
Flow wrappers can accommodate products of various shapes, sizes and weights. They can wrap rectangular blocks, cylindrical shapes, irregular products and even multipacks. The continuous film feeding and adjustable wrapping and sealing parameters make flow wrappers suitable for confectionery, snacks, food pouches, frozen products and more.
Durability and Reliability:
Commercial flow wrappers are built with robust and durable components that can handle the high speeds and repetitive motion involved in packaging operations. Components like the film unwind unit, servo motors, conveyor belts and sealing systems are designed to deliver years of reliable performance with minimum downtime.
Cost-Effectiveness: Reduced Packaging and Labor Costs
Flow wrappers significantly reduce material and labor costs compared to manual packaging. They use film more efficiently with less wasted material. The automated operation requires fewer workers per unit of output. Overall, flow wrappers offer a lower cost per package.
Quality of Packaging: Seal Integrity, Product Protection and Presentation
Flow wrappers provide a consistent, high-quality seal around products using optimized settings. This ensures seal integrity for protecting against leaks, moisture, bacteria and damage. The sealed pouches help extend shelf life by preventing oxygen and humidity from reaching sensitive products. The professional-looking finished packages also offer better product presentation and branding opportunities for retailers.
Other Key Benefits:
- Safety: Automated packaging reduces risks for workers from repetitive tasks.
- Control and Monitoring: Digital controls enable precise adjustments and monitoring of flow wrapper performance.
- Customization: Options for multi-lane, multi-head and tandem configurations based on requirements.
- Service and Support: Comprehensive preventive maintenance and after-sales service by manufacturers.
โขWaste Reduction: Optimized film usage reduces material consumption and waste generation.
โขSanitation: Clean-in-place options for hygienic and FDA-compliant flow wrappers.
Flow wrappers offer numerous benefits through their high-speed, versatile and cost-effective automated packaging function. Compared to manual methods, they deliver higher output, better package quality, lower costs and reduced waste.
Uses of Flow Wrappers across Different Industries
Food and Beverage Industry
Flow wrappers are widely used for packaging various food products like snacks, candies, bakery items, frozen foods and more. Their high speeds, ability to handle irregular shapes and options for heavy-duty configurations make them suitable for different foods.
For example, flow wrappers are used to package:
โขChocolates and confectionery in pouches for better presentation and longer shelf life.
โขPotato chips, nuts and other snacks in air-tight foil bags to keep them fresh.
โขSlices of cake, cookies and pastries individually wrapped to maintain moisture and flavor.
โขMeat products like sausages and patties in high-temperature film to allow for thermal processing.
โขFrozen fruits and vegetables in laminate film with high barrier properties for superior product protection.
Needs and specifications in food packaging include hygienic design, ease of cleaning, FDA compliance, use of food-grade materials, and ability to wrap moist or oily products. High-barrier and extended shelf-life films are also commonly used.
Pharmaceutical Industry
Flow wrappers are utilized for primary and secondary packaging of pharmaceutical products including tablets, capsules ,test kits and medical devices. They offer the precision, consistency and product protection required for medications.
Common applications include:
โขBlister packs containing doses of tablets or capsules formed using PVC film.
โขUnit-dose pouches for single-use sachets of medications like powders and syrups.
โขMultipacks of pre-filled syringes and other medical devices for hospital and retail supply.
Pharmaceutical flow wrappers require more stringent specifications like compliance with cGMP guidelines, traceability features, cleanroom-ready design and automatic validation functions. Dedicated cleaning processes are also implemented to avoid cross-contamination.
Consumer Goods Industry
In this sector, flow wrappers package toys, stationery, household items, small appliances and more. Their aesthetic pouches and packs help improve the product experience for consumers.
Common uses include wrapping:
โขBatteries and small electronics in foil packs for component protection.
โขPersonal care and beauty products in laminate film pouches for tamper evidence and longer shelf life.
โขSeasonal products like candles and gift wrap in user-friendly, space-saving packs.
โขToys, games and collectibles individually to prevent scratches and dents during storage and transport.
Product branding and customization possibilities are important considerations for consumer goods flow wrappers. Options for variable data printing, window patching and multi-lane configurations maximize packaging versatility.
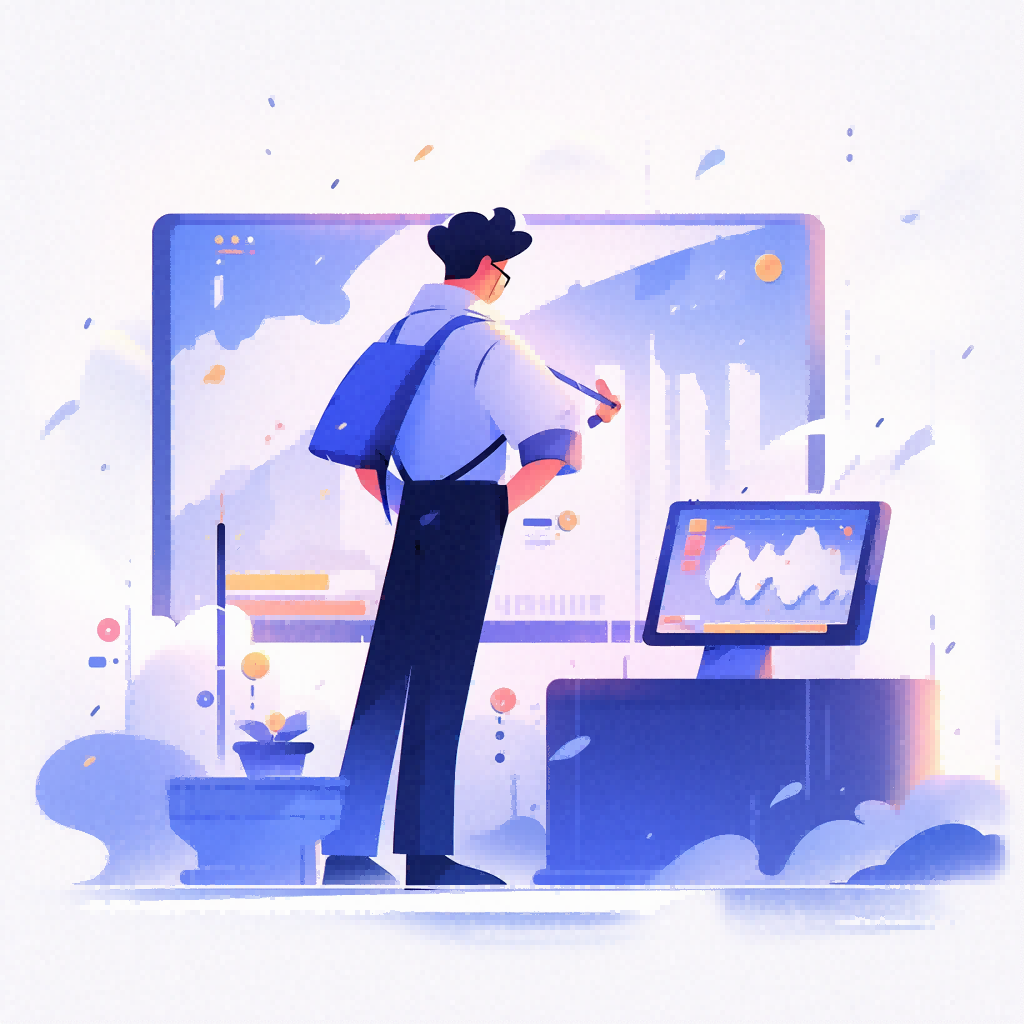
How to Choose the Right Flow Wrapper for Your Business
Understand your product and packaging needs:
The first step is to have a clear idea of your product type, packaging requirements and goals. Consider factors like:
โขProduct dimensions, weight, and shape
โขRequired output or packages per minute
โขPreferred pouch style (tube, side wrap, back wrap)
โขNeed for multi-lane or multi-head configurations
โขType of film (plastic, laminate, foil) and sealing method
โขLevel of customization and automation needed
โขFood safety and regulatory compliance standards (if applicable)
Evaluate the features and specifications of different wrappers:
Once you know your needs, research the specifications of various flow wrapper models available. Compare factors like:
โขMaximum product dimensions and weight limit
โขMaximum output or cycles per minute
โขFilm width and roll diameter
โขTypes of conveyors and feeding systems
โขAvailability of multi-lane and multipack options
โขTypes of sealing systems and cutting methods
โขLevel of programmability and automation
โขSafety and hygiene certifications
Choose a reputable manufacturer:
Go with an established flow wrapper manufacturer with a strong record of reliability, durability and after-sales service. Check online reviews and referrals from other businesses to validate the brandโs reputation.
Consider your budget and maintenance needs:
Commercial flow wrappers come in a wide price range based on features and specifications. Consider your investment budget and the total cost of ownership over the lifecycle. Also factor in the cost of spare parts, consumables and regular preventive maintenance.
Evaluate the after-sales service and support offered:
Manufacturers vary in the level of service, warranty and technical support they provide. Research aspects like:
โขLength of warranty period
โขAvailability of spare parts
โขTurnaround time for repairs
โขFrequency of planned maintenance visits
โขRemote technical support options
โขTraining programs for operators
With proper research and planning, you can select a flow wrapper model that precisely matches your production needs in terms of specifications, reliability, service and value for money. An investment in the right machine will help improve your packaging efficiency, output and overall business productivity for many years. Download Your Free Machine ROI Calculator.
Case Study: Success Story of a Business Using Flow Wrapper
Snackco is a small startup company producing organic potato chips and tortilla chips. They offer 7 flavors of chips in 100 gm and 250 gm packets.
Earlier, the chips were packed manually into laminate pouches by workers. This process was slow, inconsistent and generated a lot of waste. Workers could only pack around 400 pouches per hour. The company faced issues like:
โขHigh labour costs due to intensive manpower needs
โขPoor seal quality and leakage issues affecting product life
โขInefficient use of film resulting in 30% wastage
โขInconsistent weights of finished packets.
To resolve these challenges, Snackco invested in a flow-wrapping machine. It helped in the following ways:
โขProductivity increased by 400%. The flow wrapper packs up to 1600 pouches per hour, significantly boosting output.
โขLabor costs reduced by 60% as only 2 operators are needed for the machine.
โขSeal quality and consistency improved greatly. Leakage and expiry issues diminished.
โขPrecise weight control of finished packets via the automatic weighing system.
โขOptimization of film usage reduced material wastage to under 5%.
โขOverall packaging costs were reduced by 45%.
As a result, Snackco managed to increase their snack chip production 4 times without increasing floor space or hiring more workers. Packet quality, shelf life and customer satisfaction also improved tremendously. The enhanced branding offered by professional-looking flow wrapped packets helped the company expand to new retail outlets. Within a year, sales volumes tripled, validating the investment in automated packaging technology.
Future Trends in Flow Wrapping Technology
Increased Automation and Integration with IoT:
Flow wrappers will continue to incorporate more sensors, controls and automated features. They will be connected to the Internet of Things (IoT) for advanced monitoring, remote operation and predictive maintenance. Packaging lines will become more automated through end-to-end integration.
Sustainability Through Eco-friendly Materials and Design:
There will be a growing focus on using sustainable packaging materials like bioplastics, recyclable films and renewable energy sources. Flow wrappers will be designed to maximize material efficiency and minimize waste.
Customization and Personalization in Packaging:
Technologies like digital printing will allow for customized graphics, messages and barcodes on flow wrapped packages. Consumers will demand more personalized packaging that reflects their values and preferences.
Predictive Maintenance and AI in Flow Wrappers:
Sensors, data collection and artificial intelligence will be utilized to detect performance issues, predict faults and recommend maintenance for flow wrappers. AI-powered automation will minimize downtime and optimize machine efficiency.
Robotics and Cobots for Flexible Production:
Robotics and collaborative robots (cobots) may be integrated into flow wrapping lines for flexible production capable of handling different product types and formats. This would enable quick changeovers and smaller batch sizes.
Overall, the trends point to flow wrappers becoming more intelligent, connected, sustainable and customized to meet the evolving needs of customers and businesses. Automation, IoT, AI, predictive maintenance, eco-design and personalization will all play a role in shaping the next generation of flow-wrapping technology.
FAQ
Q: What Is a Flow Wrapper and Its Basic Functioning?
A: A flow wrapper is a type of packaging machine that wraps products in film to form pouches or bags. It operates by continuously feeding film from a roll while conveying individual products into the film to be wrapped, then sealing and cutting to form a package.
Q: What Industries Commonly Use Flow Wrappers? A: Flow wrappers are commonly used in industries such as food and beverage, pharmaceuticals, and consumer goods. They are ideal for packaging snacks, confectionery, pharmaceutical products, and various household items.
Q: How Do You Choose the Right Flow Wrapper for Your Business? A: Choosing the right flow wrapper involves understanding your product and packaging needs, evaluating the features of different wrappers, considering your budget, and assessing after-sales service and support offered by the manufacturer.
Conclusion
Flow wrappers provide an efficient, automated solution for packaging a wide range of products at high speeds. They offer numerous benefits like higher output, lower costs, better seal integrity and reduced waste compared to manual packaging. For businesses, investing in flow wrapping technology can significantly improve packaging efficiency, productivity and cost-effectiveness. As flow wrappers continue to incorporate new technologies, they will enable even higher levels of customization, flexibility and sustainability in the future.
Lintyco is a pioneer and leader in automated Flow Wrappers and end-to-end packaging systems. Lintycoโs innovative packaging solutions for food, pharma, and other applications are complemented by advanced solutions for secondary packaging, wrapping & cartoning, bulk packaging, and more. Whether you are looking for a new machine or a complete line, or if you just want to upgrade your current packaging machine, talk to Lintyco. As experts of the industry with over three decades of proven expertise, Lintyco will provide the optimal solution backed by excellent consultancy and support.