Once upon a time, in the bustling world of manufacturing, a revolutionary piece of technology emerged, destined to redefine the landscape of packaging – the flow wrapping machine. Imagine a world where products, big and small, are not merely wrapped but are bestowed with a protective embrace, ensuring they reach consumers in the pristine condition they were meant to. This isn’t just a story of machinery; it’s a narrative of innovation, efficiency, and the relentless pursuit of perfection in packaging.
The flow wrapping machine, often the unsung hero in the shadows of production lines, has quietly revolutionized how products are presented, protected, and preserved. It’s a tale of transformation, from the rudimentary methods of yesteryears to the high-speed, precision-driven technology we rely on today. Let’s delve into the world of flow wrapping machines, armed with data and insights that illuminate their pivotal role in modern manufacturing.
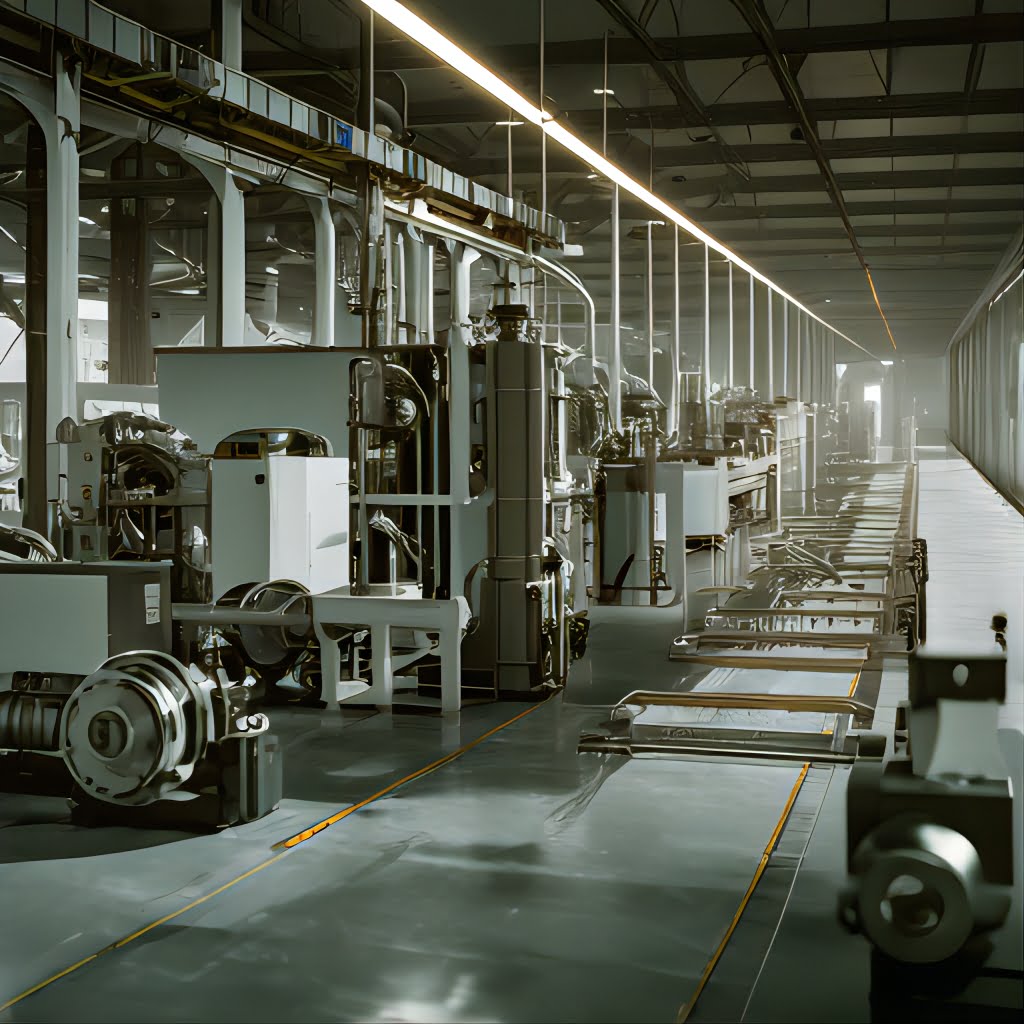
What is Flow Wrapping?
Flow wrapping, commonly known as “Flow wrap packaging,” is a favored packaging approach that stands out for fulfilling key packaging requirements.
According to a market analysis report by Grand View Research, the global packaging machinery market size was valued at USD 43.46 billion in 2020 and is expected to expand at a compound annual growth rate (CAGR) of 5.1% from 2021 to 2028. The flow wrapping machines are a significant contributor to this growth, driven by the escalating needs of the food, pharmaceutical, and consumer goods sectors.
The Fundamentals of Flow Wrapping Machines
Characterized by its flexibility and high efficiency, the flow wrapping machine is employed to encase a diverse array of items.
Often referred to as horizontal form-fill-seal (HFFS Machines), this technique envelops a product in a pliable film, resulting in a securely sealed package that not only displays the product effectively but also offers protection and safeguards against tampering.
This method is a continuous operation where items are transported horizontally through the apparatus, undergoing stages like film unwrapping, item insertion, sealing, and cutting.
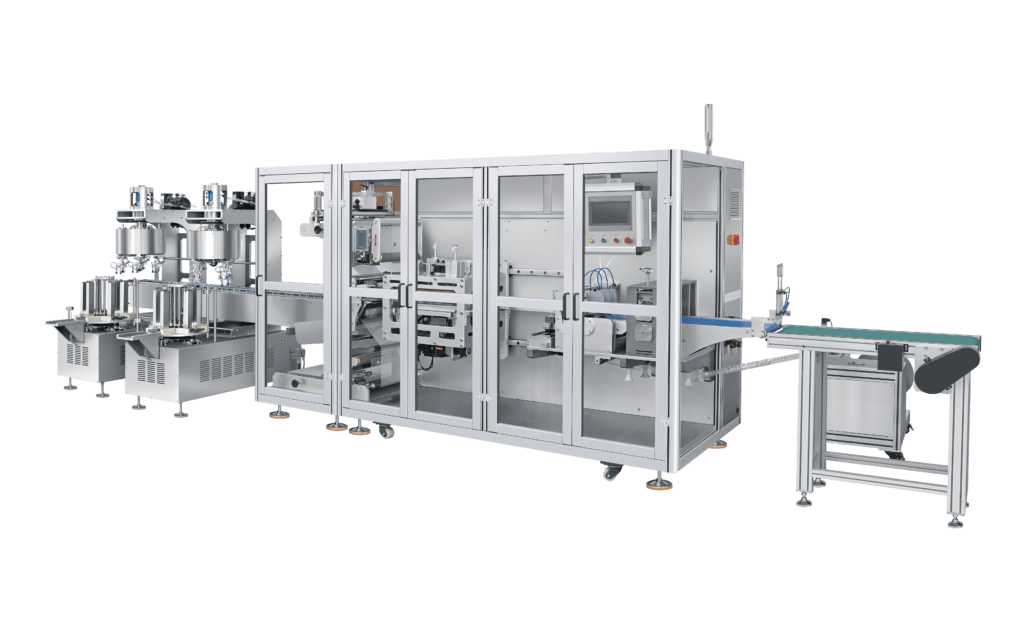
Core Elements of Flow Wrap Packaging
Central to flow wrap packaging are three main components:
Film Roll
The film used in packaging, usually crafted from materials such as polyethylene (PE) or polypropylene (PP), comes in a roll. This film is essential, serving as the protective external layer for the product being packaged.
Product Feeding Zone
This area is designated for placing the product into the flow wrap machinery. It’s versatile enough to accommodate various products, including edible items like candies and snack bars to non-edible goods such as soap bars and disposable razors.
Sealing and Cutting Unit
Here, the film is securely sealed around the item, establishing a tight enclosure. At the same time, any surplus film is trimmed or cut away, ensuring the package has a neat and polished finish.
A Wide Range of Uses
The versatility of flow wrapping machines is unmatched. They can handle a myriad of products, from the delicate whispers of chocolate bars to the robust chorus of household goods. The adaptability to various product sizes and types is instrumental in their widespread application. A study highlighted in Packaging Digest suggests that the adaptability of these machines to packaging design innovations is a key factor in their market dominance, as they can accommodate eco-friendly packaging materials and innovative design formats without compromising speed or efficiency.
The remarkable adaptability of the flow wrapping machines stands out as one of its key attributes.
This packaging method is suitable for a vast variety of items, rendering it a preferred option for producers across multiple sectors. Common uses encompass:
Food Products: Frequently utilized in the packaging of baked goods, energy bars, fresh fruits and vegetables, and sweets, flow wrap is a go-to for many food-related applications.
Non-Food : Flow wrap’s utility extends beyond food, including packaging of products such as personal care items, medical supplies, and various promotional goods.
What are the Most Common Materials Used for Flow Wrapping?
Different products demand specific packaging solutions, and the material selected can significantly influence the package’s functionality and appearance.
Let’s delve into some prevalent types of materials used in flow wrap packaging.
Heat Sealing Film
This type of film, often Polyethylene (PE), is used in heat sealing, where heat and pressure are applied to create seals, forming a secure bag, pouch, or wrapper. It’s the most cost-effective method for producing flow-wrapped packaging for food items. The ideal sealing temperature varies depending on the film material used in flow wrapping.
Cold Sealing Film
Designed for temperature-sensitive items like chocolates and candies, cold sealing employs an adhesive for sealing to avoid heat use. The flow wrap machinery places adhesive at the sealing points needed, and then pressure is applied to ensure the package is properly sealed. Cold-seal films tend to be 5% to 10% pricier than their heat-sealing counterparts.
Composite Film
Composite films are crafted from multiple layers of varying packaging materials, each chosen for its specific benefits, such as enhanced strength, resistance to wear and tear, impermeability, or superior visual qualities. Typically comprising materials like polyethylene (PE), polypropylene (PP), or polyethylene terephthalate (PET), these films offer superior product protection. However, their multi-material composition makes them the most challenging to recycle.
Mono Film
A relatively recent innovation in flow wrap materials, mono films are made from single-material layers but can include a hybrid additive of up to 5% to boost the packaging’s strength and quality. These films are more recyclable due to their singular material composition, although they may offer less robust packaging solutions.
Paper-based Wrap
This packaging combines plastic and a paper coating, like the waxed paper used for wrapping bread. It’s an eco-friendly option that blends the protective qualities of plastic with the natural appeal of paper.
Choosing the right flow wrap packaging material involves considering the product’s specific needs, barrier requirements, and how the product should be presented on the shelf. Our sales team is ready to assist customers with their queries and guide them in selecting a suitable film for their application.
It’s crucial also to ensure that the packaging material meets all regulatory standards pertinent to your industry.
What Types of Packaging Is Suitable for Flow Wrap?
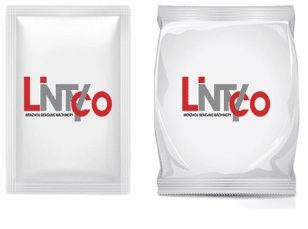
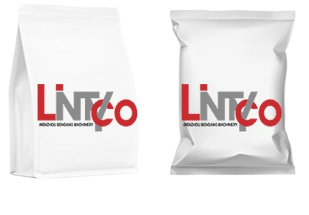
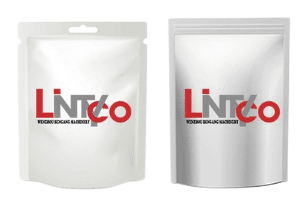
Knowing the most effective packaging types for flow wrap is crucial for enhancing your packaging operations. Below are some typical packaging formats that are well-suited for flow wrapping:
Single-Unit Packaging:
Flow wrapping shines in enclosing single items, offering a secure and aesthetically pleasing solution. It’s ideal for individual products like chocolate bars, soap bars, or mechanical parts, providing a neat and protective packaging solution.
Multi-Pack Packaging:
This method is adept at assembling multipacks or bundles, frequently utilized in the food sector for packaging groups of snack bars or biscuits. Flow wrapping combines several units effectively, preserving the individuality of each item within the pack.
Pillow Bags:
Suitable for a range of small items like sweets, nuts, or toys, pillow bags are crafted by encasing the product with a film sheet and sealing it on both ends, offering a distinctive and noticeable packaging shape.
Gusseted Bags:
Although gusseting may reduce the available space, it enhances the package’s aesthetic appeal. These bags provide additional volume and are perfect for bulkier products such as bread, fresh produce, or apparel, fashioned by shaping a flat film into a voluminous form.
Perforated Tear Strips:
Flow wrap packaging can integrate perforated tear strips for easy opening, eliminating the need for additional opening tools. This convenience is particularly popular in snack packaging, designed for effortless consumer access.
Promotional Packs:
The flexibility of flow wrap allows for innovative promotional packaging, like combining a main product with a complimentary sample or bonus item, serving as a potent marketing tool to entice consumers and elevate sales.
Variety Packs:
Flow wrapping is effective for assembling variety packs that display an assortment of product flavors or types, a common practice in the snack industry to offer consumers a selection of different tastes.
The forthcoming section will provide guidance on initiating your journey with flow wrap packaging, outlining vital steps and factors to consider to ensure a smooth and efficient packaging process.
What Benefits Does Flow Wrapping Machine Offer?
Flow wrapping stands out as a favored packaging method across many industries due to its benefits. Here’s a closer examination of its key advantages:
Cost-Effectiveness & Sustainability
Economical efficiency is where flow-wrapping machines truly shine. They are designed to use the exact amount of packaging material required, reducing waste and saving costs. This precision not only aligns with the financial goals of businesses but also echoes the growing chorus for sustainability. The reduction in material waste contributes significantly to environmental conservation, a sentiment echoed by a report from the Sustainable Packaging Coalition, indicating that optimizing packaging design and materials can lead to substantial reductions in plastic waste.
Item Protection
The secure sealing of flow wrapping machines makes certain superior item protection. It efficiently shields contents from outside impacts, moisture and potential tampering, upholding integrity, quality and freshness particularly important for food items.
Flexibility
The adaptability of flow wrapping can’t be matched, accommodating a range of item sizes and shapes effortlessly. This allows a solitary assembly line to competently deal with various items, streamlining procedures and conserving significant time and assets.
Tampering Detection
Flow wrapping is suitable for items requiring visible tampering detection. The design ensures any unauthorized access is promptly noticeable, giving customers confidence in the security and condition of the item.
Extended Shelf Life
By creating an obstacle against environmental factors like oxygen and moisture, flow wrapping plays a key role in expanding perishable goods’ shelf life, decreasing spoilage, enhancing quality and decreasing waste.
Speed and Efficiency
The high operational velocity of flow wrap machines ensures swift packaging, letting businesses promptly meet demands and maintain competent production lines.
Reduced Labor Requirements
The automation component of flow wrap packaging machines decreases manual labor reliance, bringing cost savings and uniform packaging quality significant to overall production.
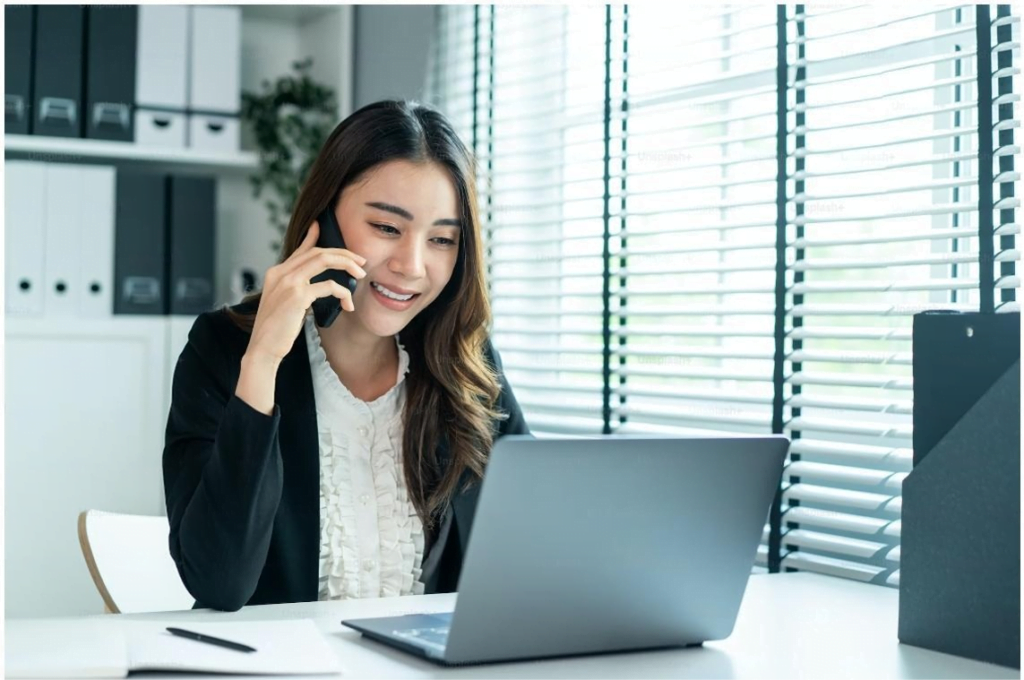
How to Choose Flow Wrapping Machines
Embarking on a flow wrapping initiative involves a series of strategic steps and considerations to ensure its success. Here’s a guide to set you on the right path:
Evaluate Your Product Specifications:
Start with a comprehensive evaluation of your product’s attributes and packaging needs. Consider the size, shape, weight, and shelf life of the product, along with any specific handling or storage prerequisites. This initial step is crucial to ascertain if flow wrap packaging aligns with your product’s requirements.
Choose Appropriate Packaging Materials:
Select the optimal packaging material that suits your product’s needs and complies with industry standards. The selection ranges from materials like polyethylene (PE) and polypropylene (PP) to BOPP and polyester (PET). Consider the sustainability angle by opting for eco-friendly packaging solutions if that aligns with your brand ethos.
Invest in Quality Design and Branding:
The packaging’s visual design is a key factor that influences consumer choices. Collaborate with a skilled graphic designer to develop attractive packaging graphics and branding that not only safeguard your product but also resonate with your target audience. The design should reflect your brand’s identity and values effectively.
Incorporate Sustainability Practices:
If your brand prioritizes environmental responsibility, focus on integrating sustainable practices into your packaging strategy. This could involve utilizing recyclable materials, minimizing packaging waste, or establishing customer-centric recycling initiatives. Sustainable packaging not only benefits the environment but can also enhance your brand’s image and appeal to eco-conscious consumers.
Flow wrap packaging presents numerous advantages, such as cost efficiency, robust product protection, and aesthetic appeal. By comprehensively understanding the available materials and the most effective packaging formats for your items, you can make well-informed decisions that leverage the full potential of this versatile packaging method.
For any further inquiries or specialized assistance with flow wrap packaging, consider consulting with industry professionals or reaching out to packaging vendors who can offer expert advice and solutions tailored to your specific requirements.
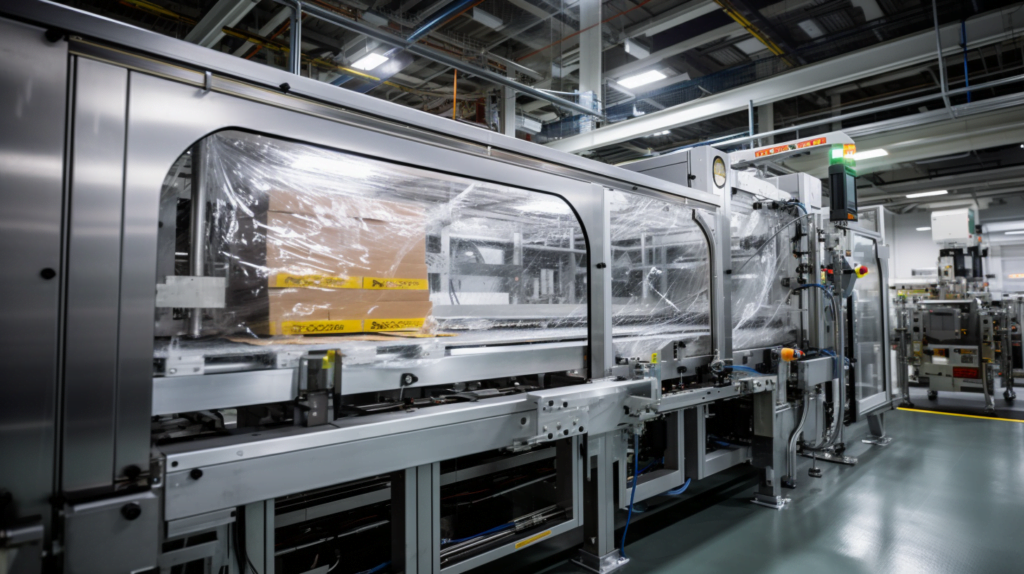
Flow Wrapping Machine vs Overwrapping Machine
When deciding between flow wrapping and over wrapping for packaging needs, it’s crucial to consider various factors such as cost, use cases, industrial benefits, and the specific requirements of your product. Here’s a comparative overview:
Cost Implications
The operational costs of flow wrapping and overwrapping are distinct due to their different material usage and packaging styles:
- Flow Wrapping: Utilizes precisely the amount of material needed to encase the item, creating airtight seals and resulting in minimal waste. This efficiency translates into lower material costs, especially beneficial when scaling up production. Many customers have greatly reduced their costs after purchasing flow-wrapping machines.
- Overwrapping: Typically consumes around 20% more film than flow wrapping because it envelops the product with additional material, akin to gift wrapping. Although the extra cost per item might be small, it accumulates significantly over large production volumes, making overwrapping more expensive overall. Similarly, product design affects the materials used.
Optimal Use Cases
The choice between the two methods often depends on the product type and the desired packaging outcome:
- Flow Wrapping: Ideal for primary packaging needs, especially for products like pharmaceuticals, confectioneries, baked goods, and personal care items, providing a secure, airtight packaging solution.
- Overwrapping: Best suited for secondary packaging, enhancing the aesthetic and protective qualities of primary packages such as tea boxes, hemp, cigarette cartons, or cosmetics, adding a premium feel and additional security.
Technical Advantages
Both packaging methods offer unique benefits that cater to different packaging needs:
- Flow Wrapping: Ensures an airtight environment, efficient material usage, and flexibility in packaging size adjustments, making it a practical choice for ensuring product freshness and longevity.
- Overwrapping: Provides added value through its versatility, superior presentation, ability to lock in odors, and enhanced tamper evidence, making it preferable for products where aesthetic appeal and fragrance preservation are important.
Selecting the Right Method
Your choice between flow wrapping and overwrapping should align with your product’s packaging requirements:
- For primary packaging, particularly with food items, flow wrapping is generally the preferred method due to its speed, efficiency, and hygienic sealing capabilities.Vacuum packaging is particularly used in the food industry.
- Overwrapping, on the other hand, is more fitting for secondary packaging needs, offering aesthetic benefits, odor retention, and tamper resistance, ideal for items where these factors are a priority.
Both flow wrapping and overwrapping have their places in the packaging industry, each with specific strengths suited to different packaging scenarios. Assessing your product’s needs, the desired aesthetic outcome, and the packaging’s functional requirements will guide you in choosing the most suitable method.
For those exploring automated packaging solutions, modern machinery options are available that cater to a wide range of packaging preferences, combining functionality with cost-effectiveness.As industries continue to evolve, the role of these machines will undoubtedly expand, continuing to shape the future of packaging with every product they wrap. The story of flow wrapping is far from over; in fact, it’s just beginning to unfold, promising a future where efficiency and sustainability are wrapped up together, ready for the world to unwrap.

Before you go…
Finding the right machine is just the first step. Even the world’s best machines will break down if you don’t adjust them correctly! Read my next article to ensure that improve efficiency and productivity right now
Unlocking the Potential of Turnkey Packaging Solutions
Get your Packaging Machine Support and Maintenance
HOW TO PROPERLY CLEAN YOUR HORIZONTAL FORM FILL SEAL MACHINE