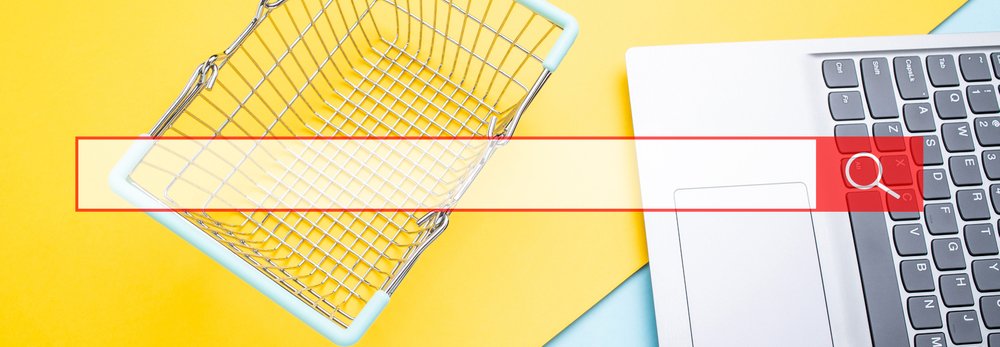
Résumé : La machine d'emballage rétractable entièrement automatique est un dispositif hautement automatisé largement utilisé dans des industries telles que les produits pharmaceutiques, les aliments et boissons, ainsi que les produits chimiques ménagers. L'emballage rétractable peut réduire considérablement l'utilisation de matériaux et les coûts de main-d'œuvre associés à l'emballage en boîte, ce qui le rend économiquement important et essentiel pour le diagnostic des défauts.
Mots clés : machine d'emballage automatique, principe de fonctionnement, diagnostic de panne
L'automatisation dans l'industrie de l'emballage modifie la manière dont les processus d'emballage sont effectués, y compris le mouvement des conteneurs d'emballage et le traitement des matériaux d'emballage. La conception et l'installation de systèmes d'emballage de contrôle automatisés jouent un rôle important dans l'amélioration de la qualité des produits et de l'efficacité de la production, en éliminant les erreurs de traitement et en réduisant l'intensité du travail. La machine d'emballage rétractable entièrement automatique est un appareil hautement automatisé qui met en œuvre un système d'emballage à contrôle automatique, ce qui améliore considérablement l'efficacité de la production et la qualité du produit. C'est particulièrement important dans les industries telles que l'alimentation, les boissons, les produits pharmaceutiques, l'électronique, etc. L'emballage sous film rétractable peut réduire considérablement l'utilisation de matériaux et les coûts de main-d'œuvre associés à l'emballage en boîte, ce qui le rend économiquement important.
Principaux composants et principes de fonctionnement de la machine d'emballage
Une solution structurelle automatisée complète se compose de divers composants, notamment des manipulateurs d'extrémité, des dispositifs de manutention et des systèmes d'identification et de vérification. Les principes de fonctionnement sont les suivants :
Manipulateurs à bras d'extrémité
Ce sont des appareils reliés à l'extrémité d'un bras mécanique qui se déplacent d'une position à une autre. Les manipulateurs à bras d'extrémité sont utilisés pour la préhension des produits, le mouvement directionnel et la détection des paramètres de performance. Ils peuvent être structurés sous forme de ventouses à vide de type unique, de ventouses à vide de type série ou d'un agencement de griffes de serrage. Dans les applications d'emballage, les manipulateurs à bras d'extrémité sont généralement conçus pour utiliser des ventouses, des griffes de serrage ou une combinaison des deux.
Appareils de manutention
Les dispositifs de manutention et de transport sont des types d'équipements nécessaires au transport, au stockage et au contrôle des produits pendant les processus de transmission et de fabrication. Ils comprennent des convoyeurs électriques, des grues monorail, des véhicules à guidage automatique et des bras mécaniques. Un système de manutention typique comprend un convoyeur d'entrée à bande, des machines d'étiquetage, des lecteurs de codes-barres, des dispositifs automatiques et des convoyeurs de sortie. Une interface graphique conviviale fournit une plate-forme facile à utiliser pour représenter l'empilement de palettes. En fonction du nombre d'unités de production contrôlées, le bras mécanique saisit, déplace et place (empile) chaque conteneur de conditionnement (boîte, caisse, fût, canette, etc.) dans la bonne position de palette. Les facteurs à prendre en compte lors de la manutention et du transport des matériaux dans le processus d'emballage comprennent la forme, le poids et les propriétés des matériaux du produit, la vitesse, la distance et la direction du transport, le niveau de contrôle requis lors de la connexion à d'autres appareils et la flexibilité pour la reformation des composants si nécessaire.
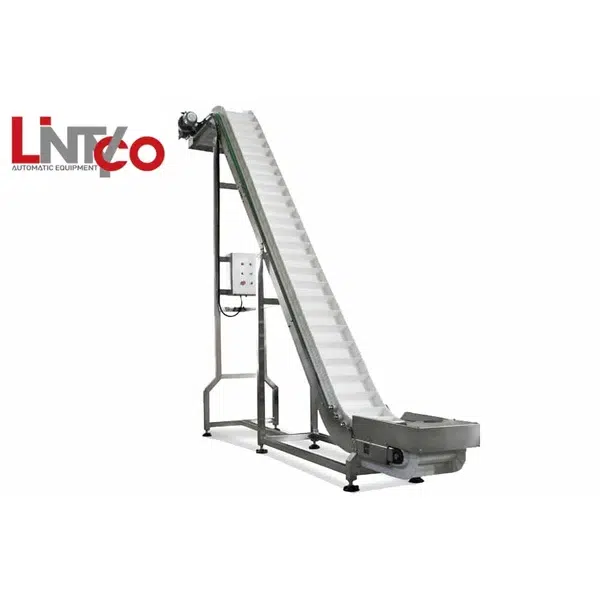
Systèmes d'identification et de vérification
La capacité d’identifier, de vérifier et de suivre avec précision les produits est devenue un élément essentiel de l’ensemble du système d’emballage. Les méthodes d'identification peuvent utiliser des codes-barres traditionnels ou des capteurs radiofréquence (RF), qui peuvent suivre des palettes ou des produits individuels. Une capacité typique de détection visuelle de codes-barres peut confirmer que chaque code-barres correspond à chaque produit. Par conséquent, les lecteurs de codes-barres et les systèmes de reconnaissance vidéo enregistrent et vérifient les étiquettes des produits pour garantir une identification complète. L'impression et la vérification des codes-barres en ligne sont également nécessaires. La technologie de vision, qui fournit des moyens efficaces et fiables pour garantir la qualité des produits, peut être utilisée dans divers scénarios d'emballage, tels que l'inspection et l'orientation des produits, le niveau de remplissage et le comptage, l'étiquetage optique, la reconnaissance de texte, la vérification de la copie des étiquettes, l'enregistrement des étiquettes et le texte global. et vérification graphique (hors ligne de production). Les systèmes de codes-barres identifient les produits en fonction du type de produit, de la date et des codes régionaux, ainsi que des noms des fabricants au cours des processus d'impression prépresse ou en ligne.
Diagnostic et dépannage des pannes courantes
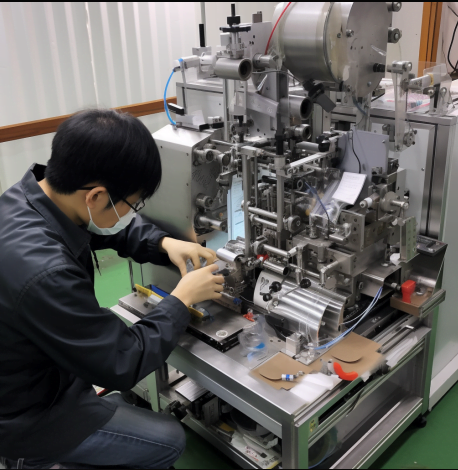
Bris de matériel
Ce défaut est souvent dû à des joints de matériaux d'emballage, à des bavures excessives, à des circuits du moteur d'alimentation en papier défectueux ou à de mauvais contacts du circuit avec le commutateur de proximité d'alimentation en papier.
Dépannage:
(1) Retirez les matériaux d'emballage défectueux.
(2) Vérifiez le circuit du moteur d'alimentation en papier.
(3) Remplacez le commutateur de proximité.
Scellage inadéquat des sacs
Ce défaut est souvent causé par des couches internes inégales des matériaux d’emballage, une pression de scellage inégale ou une basse température de scellage.
Dépannage:
(1) Retirez les matériaux d'emballage défectueux.
(2) Ajustez la pression d’étanchéité.
(3) Augmentez la température de thermoscellage.
Chemin de scellement incorrect
Ce défaut est souvent causé par un mauvais placement de la thermosoudeuse.
Dépannage : Réajustez la position de la thermoscelleuse.
Position de coupe du sac incorrecte ou écart important par rapport à la marque de couleur
Cause : Mauvais positionnement de l'interrupteur photoélectrique (capteur).
Dépannage : Réajustez la position de l'interrupteur photoélectrique (capteur).
Alignement incontrôlé des marques de couleur et suivi photoélectrique
Ce défaut est souvent causé par des joints de matériaux d'emballage avec des coutures ou des bords rugueux, des corps étrangers dans le dispositif de formage provoquant un désalignement du papier, un matériau d'emballage dépassant de la plaque de guidage de l'interrupteur photoélectrique, un désalignement du point lumineux de l'interrupteur photoélectrique avec la marque de couleur, un mauvais alignement du point lumineux de l'interrupteur photoélectrique avec la marque de couleur, un mauvais sensibilité de l'interrupteur photoélectrique et utilisation incorrecte des réglages de luminosité et d'obscurité.
Dépannage:
(1) Retirez les matériaux d'emballage défectueux.
(2) Nettoyez le dispositif de formation pour assurer un mouvement fluide du papier.
(3) Insérez le matériau d'emballage dans la plaque de guidage.
(4) Ajustez la position gauche et droite de la plaque de guidage pour aligner le point lumineux avec la marque de couleur.
(5) Remplacez l'interrupteur photoélectrique et sélectionnez le réglage approprié de la luminosité et de l'obscurité.
Déviation importante de la longueur du sac lorsque le suivi des marques de couleur n'est pas effectué (c'est-à-dire lorsque l'interrupteur photoélectrique est éteint)
Ce défaut est souvent causé par des réglages inappropriés de la longueur du sac, des configurations de roues usées entraînant une friction réduite et une pression insuffisante sur les roues.
Dépannage:
(1) Augmentez le réglage de la longueur du sac pour que la longueur réelle du sac soit égale ou légèrement plus longue que la longueur standard de la marque de couleur.
(2) Remplacez les roues.
(3) Augmentez la pression sur les roues.
Coupe de sac incomplète ou coupe partielle entraînant des sacs connectés
Ce défaut est souvent dû à une pression insuffisante entre les deux lames de coupe ou à des bords de lame émoussés.
Dépannage:
(1) Ajustez la pression entre les lames de coupe.
(2) Aiguisez ou remplacez les lames de coupe.
Le moteur d'alimentation en papier ne tourne pas ou continue de tourner
Ce défaut est souvent dû au blocage du levier de commande d'alimentation en papier, à un endommagement du commutateur de proximité d'alimentation en papier, à un condensateur de démarrage endommagé ou à un fusible grillé.
Dépannage:
(1) Résolvez le problème à l’origine du bourrage.
(2) Remplacez le commutateur de proximité d'alimentation en papier.
(3) Remplacez le condensateur de démarrage.
(4) Remplacez le fusible.
La thermoscelleuse ne chauffe pas ou le contrôle de la température est perdu
Ce défaut est souvent causé par des éléments chauffants endommagés, des dysfonctionnements de circuit, des fusibles grillés, des contrôleurs de température défectueux ou des circuits ouverts dans le thermocouple.
Dépannage:
(1) Remplacez les éléments chauffants.
(2) Vérifiez le circuit.
(3) Remplacez le fusible.
(4) Remplacez le contrôleur de température.
(5) Remplacez le thermocouple.
Omission de tirer le sac (le moteur de traction du sac ne fonctionne pas)
Ce défaut est souvent causé par des dysfonctionnements du circuit, des dommages au commutateur de proximité de tirage des sacs, des défauts dans le contrôleur automatique de la machine d'emballage ou des dysfonctionnements du pilote du moteur pas à pas.
Dépannage:
(1) Vérifiez le circuit et éliminez tout défaut.
(2) Remplacez le commutateur de proximité de tirage du sac.
(3) Remplacez le contrôleur automatique de la machine d’emballage.
(4) Remplacez le pilote du moteur pas à pas.
Conclusion
Pour dépanner rapidement les pannes d'une machine d'emballage automatique, il est essentiel non seulement de comprendre sa structure et ses principes de fonctionnement, mais également d'identifier les causes profondes des pannes et de maîtriser un ensemble de méthodes de dépannage. Cela garantit l’adaptabilité à diverses situations et permet une résolution efficace des défauts. N'hésite pas à Contactez-nous si tu ne peux pas gérer
Lintyco est un pionnier et un leader dans machines de remplissage automatisées et systèmes d'emballage de bout en bout. Les solutions d'emballage innovantes de Lintyco pour les applications alimentaires, pharmaceutiques et autres sont complétées par des solutions avancées pour emballage secondaire, emballage et cartonnage, emballage en vrac, etc. Que vous recherchiez une nouvelle machine ou une ligne complète, ou si vous souhaitez simplement mettre à niveau votre machine d'emballage actuelle, parlez à Lintyco. En tant qu'expert du secteur avec plus de trois décennies d'expertise éprouvée, Lintyco fournira la solution optimale soutenue par d'excellents conseils et support.