Aujourd'hui, je vais parler du dernier projet de notre usine coopérative A'Saffa Foods. Vous découvrirez son histoire et l'usine en ligne d'aliments pour le bétail et la volaille.
Bienvenue à l'usine d'aliments A'Saffa Foods située au cœur de Salalah, Oman. Ici, vous serez témoin du dévouement guidé par l'expertise de Van Alsen. A'Saffa Foods a été créée en 2001 et est devenue l'une des principales entreprises de volaille verticalement intégrées d'Oman. Ses principales activités sont concentrées dans la région de Salalah, qui abrite des installations de production avicole de pointe et entièrement intégrées. L'installation intègre de manière transparente un couvoir, un élevage de poulets de chair, une usine d'aliments pour animaux et une usine de transformation, tous stratégiquement situés sur un seul site.
A'Saffa a pris la décision stratégique d'ouvrir une nouvelle usine d'aliments pour animaux afin d'augmenter la production dans divers secteurs, notamment les fermes, les couvoirs, les usines d'aliments pour animaux, les abattoirs et la transformation des aliments. Lors de la sélection du fournisseur idéal pour son usine d'aliments pour animaux, A'Saffa a donné la priorité à des critères tels que la durabilité, la qualité et l'efficacité énergétique. Dans cette optique, Van Aarsen était le choix idéal pour concevoir et mettre en œuvre une nouvelle usine d'aliments pour animaux de 50 tonnes par heure pour A'Saffa Foods.
Alimentation et dosage
Les matières premières sont reçues dans la trémie d'alimentation et nettoyées par des tamis rotatifs et des aimants. De là, les matières premières peuvent être transportées vers des silos à maïs, des entrepôts de soja ou directement vers des silos à ingrédients. Depuis le bac de dosage, les matières premières sont pesées et dosées dans une macro-balance de 6 000 kg. Le bac de déchargement intégré assure un déchargement rapide des pièces pesées et réduit les temps de cycle des lots. Les minéraux sont reçus dans de grands sacs dans une fosse de décharge séparée dans l'entrepôt adjacent au bâtiment et transportés mécaniquement jusqu'au silo de dosage des minéraux.
Concassage et mélange
Après cette étape, les matières premières entrent dans la ligne de broyage et de mélange. Dans deux broyeurs à marteaux GD1400, les matières premières sont broyées avec précision pour obtenir la taille et la structure requises. Le silo situé sous le broyeur à marteaux est équipé de dispositifs antidéflagrants pour minimiser les risques de poussière et d'étincelles potentiels générés par le marteau afin d'assurer la sécurité. De plus, les ingrédients traces conditionnés dans des sacs sont ajoutés manuellement dans l’un des huit silos. Le poids maximum du lot autorisé pour le système de microdosage est de 200 kg.
Mélange
Ensuite, le micro-ensemble est dosé avec précision à l'aide d'un coulisseau à commande hydraulique, permettant une variété d'ajustements des réglages, des vitesses de coulissement et des ouvertures. Pour les matériaux fluides exigeants, quatre silos sont équipés de dispositifs d'agitation intégrés. De plus, d’autres ingrédients peuvent être introduits via une boîte à additifs manuelle située au-dessus du mélangeur. Tous les ingrédients de la recette sont mélangés de manière transparente dans un mélangeur à palette MultiMix de 10 000 litres, garantissant un mélange homogène. Ajoutez l'huile directement dans le mixeur. Pour éviter toute contamination, le pipeline de liquide est doté d'une fonction de purge d'air qui empêche les gouttes de s'échapper de la buse pendant le dosage du liquide.
Granulation et conditionnement
Le mélange est acheminé du mélangeur vers le silo à poudre de l'une des deux lignes de granulation. La vis doseuse régule le transport du produit en fonction de la demande de charge du granulateur, en l'envoyant à travers le conteneur longue durée jusqu'au mélangeur à vapeur. En gardant le repas à une température d'au moins 85 degrés Celsius pendant au moins 3 minutes, tous les agents pathogènes potentiels tels que la salmonelle sont tués, gardant ainsi le repas hygiénique. Le repas hygiénique et bien conditionné continue vers le granulateur CU900 XL où il est compressé en granulés. Calculés selon la recette d'A'Saffa, les deux granulateurs ont une capacité de près de 30 tonnes par heure.
Rafraîchir
Les pellets sont refroidis jusqu'à une température proche de la température ambiante dans un refroidisseur à contre-courant TK3000. Grâce au distributeur rotatif de pellets, le produit est refroidi uniformément avant de sortir du mécanisme de décharge hydraulique, tandis que le niveau réel de pellets est mesuré par un capteur de niveau continu de type ultrasonique. Si nécessaire, les particules peuvent être broyées. Après le processus de refroidissement, les granulés et copeaux sont tamisés pour éliminer les poussières puis recyclés dans un bac situé au-dessus du granulateur. Enfin, les pellets et les copeaux sont transportés vers le silo d'alimentation final. Ici, ils sont soit chargés dans des remorques en vrac à l'aide de soufflets de chargement, soit envoyés directement à la station-service pour être conditionnés dans des sacs de 50 kg.
Ligne d'emballage alimentaire de Lintyco
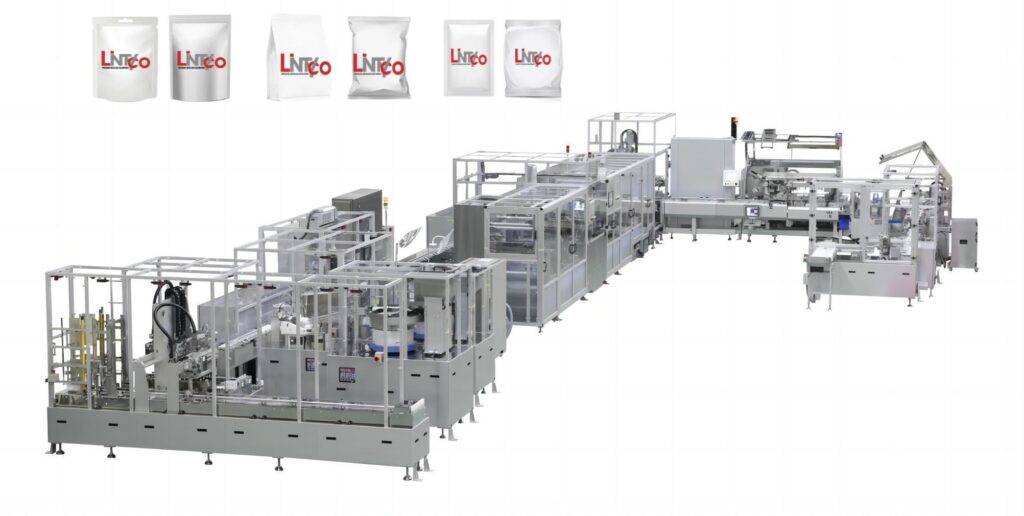
Lintyco est un pionnier et un leader dans Machines d'emballage alimentaire automatisées et systèmes d'emballage de bout en bout. Les solutions d'emballage innovantes de Lintyco pour les applications alimentaires, pharmaceutiques et autres sont complétées par des solutions avancées pour emballage secondaire, emballage et cartonnage, emballage en vrac, etc. Que vous recherchiez une nouvelle machine ou une ligne complète, ou si vous souhaitez simplement mettre à niveau votre machine d'emballage actuelle, parlez à Lintyco. En tant qu'expert du secteur avec plus de trois décennies d'expertise éprouvée, Lintyco fournira la solution optimale soutenue par d'excellents conseils et support.