Avez-vous déjà souhaité pouvoir essayer une nouvelle solution d'automatisation avant de l'acheter ? C’est l’idée derrière la mise en service virtuelle… et c’est peut-être l’avenir de l’automatisation.
Avec la mise en service virtuelle, vous créez un modèle virtuel de vos solutions d'automatisation idéales. Vous pouvez tester ces solutions, les modifier et voir comment la technologie d'automatisation fonctionnera avec votre processus spécifique.
La mise en service d'une solution d'automatisation peut être un processus complexe et long. Avec la mise en service virtuelle, vous pouvez utiliser la technologie de simulation robotique pour réduire à la fois cette complexité et ce temps. Cela évite les temps d'arrêt inutiles, car vous n'avez pas besoin de mettre vos machines existantes hors ligne pour tester la solution d'automatisation.
Il semble probable que la mise en service virtuelle restera désormais une étape essentielle du processus d’automatisation. Si vous cherchez un moyen de rationaliser votre processus de déploiement, cette option peut être la solution.
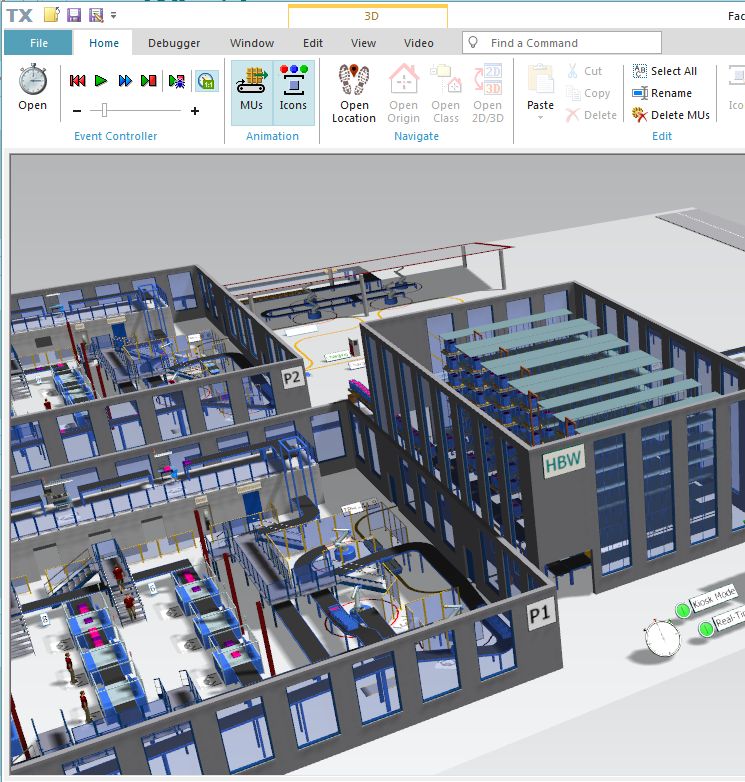
Qu'est-ce que la mise en service virtuelle ?
La mise en service virtuelle consiste à utiliser la technologie de simulation pour concevoir, installer et tester des solutions d'automatisation avant de déployer le matériel physique dans un environnement de fabrication. Par exemple, un logiciel de simulation robotique peut optimiser le déploiement d'un robot sans temps d'arrêt inutile.
Le logiciel de simulation est au centre de tout projet de mise en service virtuelle. Ce logiciel comprendra des modèles virtuels de toute technologie d'automatisation susceptible d'être utilisée, ainsi que des algorithmes et des fonctionnalités pour tester le fonctionnement de votre système.
Avec les solutions robotiques, vous pouvez utiliser le même logiciel de simulation pour programmer le robot physique. RoboDK comprend à la fois des fonctionnalités de simulation et de programmation hors ligne. Une fois que vous avez fini de tester votre déploiement dans le simulateur, vous pouvez connecter votre robot physique et télécharger le programme directement sur le matériel robotique.
La différence entre la mise en service virtuelle et traditionnelle
La mise en service virtuelle est-elle vraiment si différente de la mise en service traditionnelle ?
Il existe quelques différences clés entre les deux approches de mise en service d'un projet d'automatisation.
La mise en service traditionnelle s'effectue généralement sur site, à l'emplacement physique où vous déployerez la solution d'automatisation, comme votre usine. Vous apportez divers outils physiques et équipements de test pour le dépannage manuel. Cela signifie que vous devrez peut-être arrêter tout ou partie de vos processus de fabrication existants pendant la durée du projet de mise en service, ce qui peut s'avérer coûteux.
Avec la mise en service virtuelle, vous effectuez la majeure partie du déploiement à distance, en venant uniquement sur site à la toute fin.
De plus, le processus de mise en service traditionnel prend souvent plus de temps et nécessite une équipe plus nombreuse pour la mise en œuvre sur site. Avec la mise en service virtuelle, une petite équipe ou même une seule personne peut effectuer la majeure partie du déploiement à distance.
Comment fonctionne la mise en service virtuelle ?
L'idée de base est de créer une simulation ou un jumeau numérique de votre solution d'automatisation. Il s'agit d'un modèle virtuel montrant comment la ou les machines fonctionneront dans votre processus.
Vous utilisez ce modèle virtuel pour tester différents scénarios afin de voir comment cela affectera la solution d'automatisation. Cela vous aide à optimiser la solution avant de l'appliquer à l'environnement physique.
La mise en service virtuelle avec un simulateur de robot implique :
- Création ou importation de modèles virtuels des parties pertinentes de votre ligne de production.
- Chargement des modèles de votre robot depuis la bibliothèque de robots, ainsi que de tout autre équipement.
- Création d'un programme robot pour votre application spécifique.
- Optimiser les différents aspects de votre solution robotique avant de la déployer dans votre usine.
En abordant la mise en service de cette manière, vous pouvez tester votre solution dans un environnement contrôlé et sans risque.
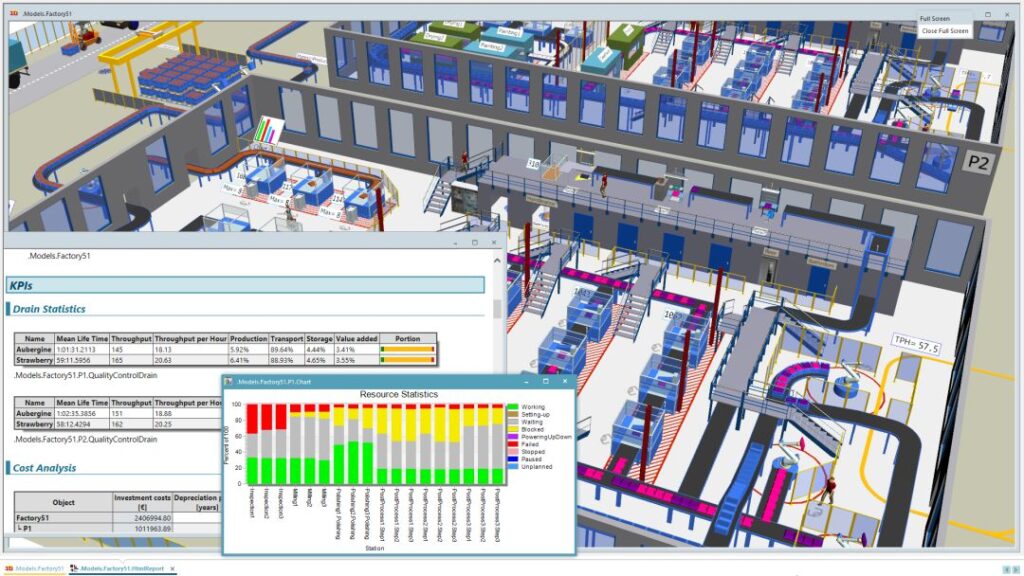
5 avantages uniques de la mise en service virtuelle
Voici 5 avantages uniques de la mise en service virtuelle :
1. Déploiements efficaces
Dans la mesure où la mise en service virtuelle réduit considérablement le besoin d’activités fastidieuses sur site, elle améliore l’efficacité opérationnelle de votre déploiement. Cela vous aide à éviter des temps d’arrêt coûteux et rend votre processus globalement plus efficace.
2. Une automatisation plus sûre
En simulant votre projet d'automatisation dans un environnement virtuel, vous pouvez tester les dangers potentiels de manière sûre et contrôlée. Cela vous aide à éviter les accidents et les blessures qui peuvent survenir lors d'un processus de mise en service physique traditionnel. Il vous permet également de tester des cas limites dangereux qui seraient impossibles à tester avec du matériel physique.
3. Communication d'équipe améliorée
Un simulateur peut fournir une plate-forme commune permettant à tous les membres de votre équipe de visualiser, comprendre et suggérer des modifications à votre solution d'automatisation. Cela peut contribuer à améliorer la communication et à éviter d’éventuels malentendus. Avec RoboDK for Web, vos collègues n'ont même pas besoin d'installer le logiciel pour visualiser la simulation.
4. Flexibilité aux changements
L’un des avantages importants de la mise en service virtuelle est qu’il est facile d’apporter des modifications ou des ajustements à votre processus de production. Vous pouvez tester rapidement de nouvelles idées dans le simulateur, en sachant en toute sécurité que vous ne perturbez pas votre production.
5. Meilleure compréhension de la solution
Enfin, développer votre solution d’automatisation dans un simulateur permet de mieux comprendre son fonctionnement. En « jouant » avec la technologie dans l’environnement virtuel, vous acquerrez rapidement une connaissance pratique de ses possibilités et de ses limites. Cela vous aide à mieux utiliser la technologie dans le monde réel.
La mise en service virtuelle va-t-elle changer l’automatisation ?
Avec la popularité toujours croissante des outils numériques, il semble probable que la mise en service virtuelle soit là pour rester.
La mise en service virtuelle contribue à éliminer les barrières à l’entrée dans l’automatisation qui ont limité l’adoption des robots par de nombreux fabricants. Il peut permettre à quiconque de déployer rapidement et efficacement des technologies d'automatisation dans ses processus de fabrication tout en réduisant les risques associés aux temps d'arrêt inutiles.
Lorsque vous déployez votre technologie robotique avec une mise en service virtuelle, vous augmentez vos chances de réussite du projet d'automatisation. Cela rend la robotique comme solution moins risquée et plus précieuse.
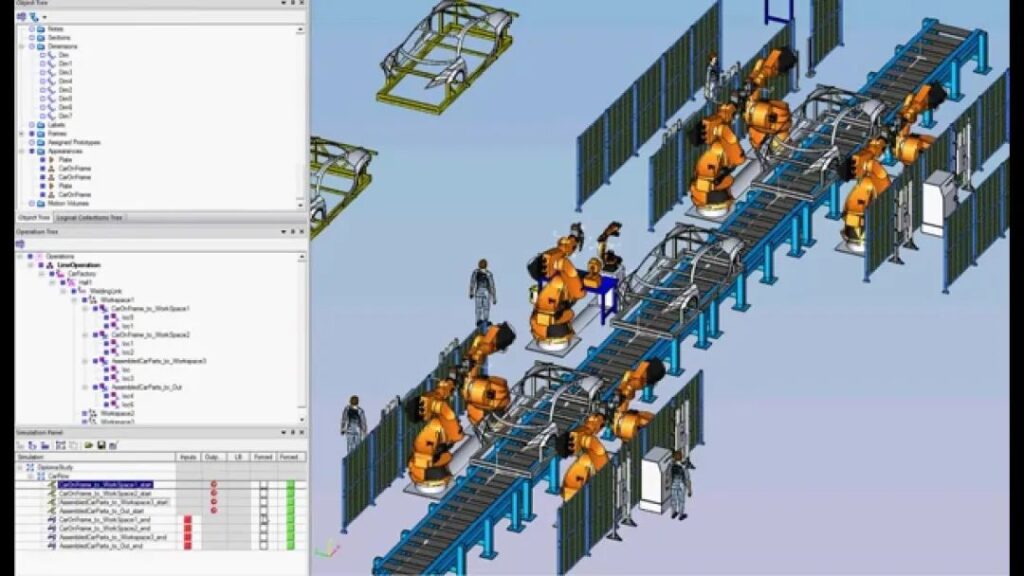
Tendances technologiques dans la conception et l’ingénierie des installations pharmaceutiques
La fabrication pharmaceutique évolue continuellement au rythme des progrès technologiques, alors que les entreprises cherchent à réduire leurs coûts, à optimiser pleinement leurs ressources et à rationaliser leurs opérations. Cela s'étend à la conception et à l'ingénierie des installations. Cet article explore plusieurs tendances technologiques émergentes liées à la conception et à l’ingénierie des installations qui profitent considérablement aux sociétés pharmaceutiques.
Mise en service virtuelle
La construction et la mise en service de nouvelles installations pharmaceutiques nécessitent beaucoup de temps et d'argent. PhRMA estime que la construction d'une nouvelle installation peut coûter jusqu'à $2 milliards et prendre entre 5 et 10 ans. Dans cette optique, il est essentiel que chaque étape du processus de mise en service et de construction soit exécutée de manière fluide, efficace et rentable afin que les opérations soient en cours et génèrent un retour sur investissement le plus rapidement possible.
Souvent, une part importante de ce coût en termes de temps et de capital provient directement de la mise en service des installations, des lignes et des équipements. Les modifications ou retards ultérieurs dans la conception, les exigences et les configurations de l'installation ou de l'équipement doivent être minimisés ou, idéalement, complètement éliminés afin de réduire le coût global de mise en service de l'installation. Pour résoudre ce problème, les fabricants de produits pharmaceutiques peuvent se tourner vers la mise en service virtuelle, une approche qui combine le développement et les tests traditionnels et virtuels par émulation. Contrairement à la mise en service physique, la mise en service virtuelle peut commencer bien avant l'achat ou la construction du matériel. Cette approche permet d'économiser jusqu'à 40% en temps de mise en service par rapport à la mise en service conventionnelle, réduisant ainsi les risques et les incertitudes, offrant une sécurité et une agilité accrues et réduisant les coûts de modifications de conception.
Simulation, émulation et jumeaux numériques
Un jumeau numérique est une représentation virtuelle d’une entité physique, d’un système ou d’un processus réel synchronisé avec l’entité physique. Le jumeau numérique et l'élément de fabrication observable (OME) sont généralement synchronisés en propageant les données du capteur de l'entité physique vers le jumeau numérique. Les jumeaux numériques peuvent être construits à partir de simulations ou d'émulations, mais doivent être synchronisés avec l'OME. La fréquence et la fidélité des émulations/simulations synchronisées doivent être adaptées à la tâche pour laquelle elles sont conçues.
Les jumeaux numériques peuvent être construits à partir de plusieurs progiciels commerciaux ou open source différents, mais incluent toujours l'élément physique, un mécanisme de synchronisation et un progiciel utilisé qui exécute le modèle/la représentation virtuelle (généralement dérivé du logiciel IAO/multiphysique). La création d'un jumeau numérique nécessite que les éléments d'intérêt pour l'OME soient répliqués avec précision dans la représentation virtuelle. Pour les équipements de production, cela implique généralement la définition de systèmes de processus ou mécatroniques, comprenant des moteurs, des actionneurs et des instruments, connectés à un système d'automatisation exécutant un logiciel spécifique à une application.
L’intérêt de la mise en œuvre de jumeaux numériques avec des équipements de production réside dans la possibilité d’estimer l’état du système physique au-delà de ce qui est immédiatement observable. Les applications typiques incluent la détection logicielle, la correction adaptative des défauts, le contrôle prédictif du modèle et la maintenance prédictive. Les équipements de production peuvent s'intégrer dans un jumeau numérique plus vaste de l'ensemble d'un processus de fabrication afin de prendre en charge une fabrication dans les délais et en fonction de la demande.
Dans les applications de mise en service virtuelle, un jumeau numérique peut ne pas être possible car l'équipement physique peut ne pas exister. Au lieu de cela, un modèle de l'équipement de production est déployé aux côtés du système de contrôle, afin que les deux puissent être co-développés. Le système de contrôle considère le modèle d'équipement de production comme une émulation, puisque le système de contrôle peut interagir naturellement avec le modèle via des sorties de commande et un retour d'état (connu sous le nom de Hardware-In-the-Loop). Pour que cette technique réussisse, le modèle d’équipement de production doit représenter avec précision le comportement concret du système physique.
La mise en service virtuelle basée sur l'émulation conduit à une réduction précieuse des risques du projet du point de vue de l'évitement des erreurs et du respect des délais du projet. Comme les scénarios et les choix de conception peuvent être testés de manière approfondie sans équipement physique, les ingénieurs peuvent tester et vérifier divers éléments du système, notamment les modules logiciels spécifiques à l'application, la configuration des recettes, les modes de défaillance et de récupération, ainsi que l'efficacité de l'interface utilisateur, sans dépendre de l'équipement de test programmé ou sans être sous tension. site. En conséquence, les projets qui utilisent la mise en service virtuelle sont souvent déployés avec moins de temps de mise en service en personne et sont généralement plus sûrs pour les personnes et les biens.
Une fois l'équipement mis en service et validé, l'émulation issue de la mise en service virtuelle peut continuer à être utilisée comme jumeau numérique synchronisé avec l'équipement physique. Puisque le modèle est déjà construit, il est immédiatement utile comme représentation idéalisée du système physique. Les ingénieurs peuvent utiliser ce jumeau numérique pour optimiser, entre autres éléments, la conception des installations, la conception des systèmes, les opérations des lignes de production et les exigences des usines et des machines.
Infrastructure en tant que code
Du point de vue de la convergence IT/OT, la mise en service virtuelle permet d'utiliser des concepts informatiques agiles pour développer des processus tels que l'infrastructure-as-code dans l'espace OT, l'objectif étant d'évoluer vers l'automatisation du développement de code et de la configuration de l'infrastructure.
L'adoption de ces concepts informatiques modifiera fondamentalement les flux de travail des ingénieurs OT. Au lieu de créer des systèmes et du code à partir de zéro, comme c'était le cas avec les systèmes de contrôle distribués (DCS) existants, le processus ressemblera beaucoup plus à un rôle de développement logiciel agile, avec des ingénieurs se concentrant davantage sur la maintenance des systèmes logiciels automatisés que sur le développement de l'application. code et infrastructure. Pour les utilisateurs finaux, cela pourrait signifier que les tâches ardues d’installation, de configuration et d’application de correctifs pour l’infrastructure des systèmes de contrôle deviendraient un flux de travail automatisé. Pour les constructeurs de machines, cela pourrait aboutir à un système de traitement des commandes qui envoie une configuration pour créer dynamiquement une infrastructure d'automatisation et un code d'application sur commande en fonction des options sélectionnées par le client, sans l'intervention d'un ingénieur.
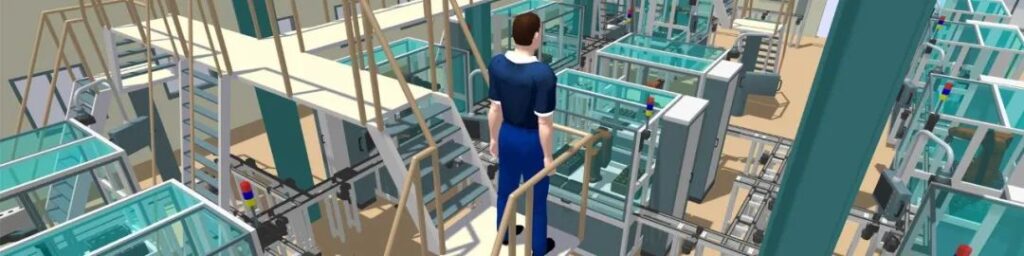
Orchestration des équipements OEM
Les équipements OEM constituent la base des usines de fabrication pharmaceutique modulaires modernes en offrant la flexibilité nécessaire pour choisir et combiner les meilleures solutions d'équipement pour des processus spécifiques. La mise en service et la validation des équipements OEM sont généralement un processus plus rapide, car les fabricants reçoivent des unités pré-assemblées et programmées à cet effet. De plus, les équipementiers fournissent généralement des équipements prêts à être validés, ce qui facilite la qualification de l'équipement pour une utilisation dans les installations CGMP. Il n'est pas nécessaire de recourir à des ressources internes ou à des tiers pour la construction des équipements et le développement du code d'application. Cependant, des défis peuvent survenir en raison des différentes normes de connectivité et interfaces entre les différents fournisseurs d'équipements, ce qui rend difficile l'intégration de plusieurs équipements dans un système de contrôle unifié. C’est là qu’intervient l’orchestration des équipements OEM.
La nécessité d’une stratégie d’orchestration
Sans une approche stratégique et des spécifications claires, l’utilisation d’équipements OEM aboutit à des îlots d’automatisation fragmentés. Cette absence de stratégie est généralement due à une collaboration tardive avec les fournisseurs d'équipements de la part de l'utilisateur final. Lorsque l'automatisation n'est pas prise en compte dans le processus initial d'achat d'équipement, les ingénieurs ont souvent du mal à intégrer l'équipement ou s'appuient sur des sociétés d'ingénierie pour gérer l'intégration. Ce processus avancé d’assemblage des équipements après coup peut conduire, dans le meilleur des cas, à une capacité d’interface limitée au sein de l’usine. Dans le pire des cas, l’ensemble du processus peut se retourner contre lui en étant long et coûteux sans augmentation de la maturité numérique.
Pour résoudre ces problèmes, les fabricants pharmaceutiques peuvent adopter un plan holistique d’orchestration des équipements OEM afin d’automatiser et de coordonner divers composants afin de travailler ensemble de manière transparente dès le début des phases de spécification et de conception des installations. Le fait d'avoir des normes complètes établies avant l'achat de tout équipement permet à un utilisateur final de travailler en collaboration avec ses fournisseurs d'équipement, donnant ainsi à l'OEM la possibilité de se différencier sur la façon dont son équipement peut s'intégrer dans une plate-forme d'automatisation unifiée. Pour l'utilisateur final, cela simplifie la formation croisée et standardise les interfaces, les systèmes d'alerte, les diagnostics et la gestion des recettes. Cela réduit les coûts, rationalise les opérations et accélère la construction, la mise en service et la qualification des installations.
Tirer parti des interfaces standardisées
Les utilisateurs finaux exigent des équipements OEM dotés d'une capacité de plug-and-product pour s'intégrer à n'importe quel système de contrôle distribué (DCS) ou système de contrôle et d'acquisition de données (SCADA). Cette fonctionnalité plug-and-product standardise les services d'automatisation de base tels que les interfaces d'équipement et la gestion des recettes, les écrans d'interface utilisateur, les pistes d'audit et la gestion des alarmes sur des équipements disparates. Un standard plug-and-product connecte systématiquement tous ces éléments et les coordonne à l'aide d'interfaces standardisées, comme le module type package NAMUR (MTP) et de protocoles modernes, comme OPC Unified Architecture (OPCUA). L'intégration de toutes ces plates-formes disparates apporte de la cohérence, permet d'économiser du temps et des efforts d'intégration et fait du plug-and-product une technologie réalisable pour les installations du futur.
Ces technologies doivent être considérées comme un renforcement d’une stratégie cohérente d’orchestration OEM plutôt que comme un remplacement de tout le travail effectué par une collaboration entre les organisations et des spécifications complètes. Il n'existe aucun bouton magique pour intégrer les équipements de manière transparente afin de fournir des ensembles communs de services et les relations constructives de l'utilisateur final avec ses fournisseurs d'équipement et de technologie jouent un rôle important dans une stratégie d'orchestration OEM efficace. Pensez à cette situation, une usine construite entièrement avec un équipement boîte noire avec une interface standardisée pourrait être rapide à intégrer mais serait difficile et coûteuse à prendre en charge à long terme pour un utilisateur final en raison de la gestion de nombreux contrats de support, de pièces de rechange disparates et d'un manque de ressources. de cohérence voire d'accès aux logiciels d'application sur les équipements OEM.
Une multitude d'avantages
En termes simples, l'orchestration des équipements OEM facilite le travail de création d'une plate-forme d'automatisation unifiée pour une installation. Cela conduit finalement à une mise sur le marché plus rapide et à une réduction du coût total de possession pour l’utilisateur final. Une orchestration efficace permet l'intégration de différents composants OEM de manière à faciliter la personnalisation et l'évolutivité, l'ajout de nouveaux équipements dans les systèmes existants et l'intégration transparente des mises à niveau et extensions futures. Les temps d'arrêt et le temps moyen de réparation (MTTR) sont réduits grâce à un dépannage et une maintenance simplifiés.
Médicaments de thérapie innovante
Une autre tendance émergente liée à l’ingénierie des installations est le changement de l’automatisation industrielle pour s’adapter au secteur des produits médicaux de thérapie innovante (ATMP). Beaucoup de ces thérapies sont autologues, ce qui signifie qu’elles proviennent d’une personne et sont ensuite transmises à la même personne. Les volumes de production de ces thérapies autologues sont très faibles, souvent en millilitres. Les systèmes d'automatisation existants sont conçus pour produire à plus grande échelle. Le concept ici est donc de miniaturiser les technologies d'automatisation pour qu'elles fonctionnent sur des unités ou des instruments de table. Ces unités de paillasse peuvent ensuite être orchestrées en un train de processus coordonné pour réaliser la thérapie, le processus évoluant pour s'adapter à davantage de trains de processus pour un plus grand nombre de patients.
La clé du succès de cette stratégie résidera dans la volonté du fournisseur d'automatisation de réduire sa technologie pour offrir les mêmes capacités logicielles et matérielles commerciales prêtes à l'emploi pour les équipements de table. Cela sera essentiel pour limiter la quantité de retouches nécessaires au transfert de technologie depuis l’espace de développement de processus (PD) vers la fabrication cGMP pour ces thérapies avancées. La collaboration avec un fournisseur d'automatisation qui a la capacité de réduire et d'opérer de manière flexible sur ces trains disparates d'équipements industriels et de laboratoire pour garantir la précision et la sécurité des patients est cruciale.
Du début à la fin
Les sociétés pharmaceutiques adoptent activement des technologies pour améliorer la productivité, l’efficacité et le retour sur investissement et conserver un avantage concurrentiel. Des initiatives telles que la mise en service virtuelle et l'orchestration des équipements OEM sont adoptées pour accélérer l'introduction de nouvelles capacités et capacités, ainsi que pour optimiser les opérations des installations afin d'atteindre à terme une installation adaptative.
Grâce à la mise en service virtuelle, les installations peuvent être conçues, modélisées, conçues et testées avant le début des travaux physiques. Cette approche permet d'optimiser divers aspects tels que l'agencement, la productivité, le débit, le flux et l'efficacité énergétique. L'orchestration des équipements OEM automatise les processus et standardise les interfaces, ce qui facilite le travail de création d'une plate-forme d'automatisation unifiée pour une installation, ce qui entraînera à terme une mise sur le marché plus rapide et une réduction du coût total de possession pour l'utilisateur final.
Les sociétés pharmaceutiques qui exploitent la puissance des nouvelles technologies seront mieux équipées pour optimiser les processus de leurs installations, du début à la fin.
Conclusion
La mise en service virtuelle est à la pointe des avancées technologiques en matière d'automatisation, offrant une approche transformatrice aux industries souhaitant intégrer plus efficacement les solutions d'automatisation. En tirant parti de la technologie de simulation, la mise en service virtuelle permet aux entreprises de concevoir, tester et affiner les systèmes d'automatisation dans un environnement numérique avant leur mise en œuvre physique. Ce processus améliore non seulement l'efficacité et la sécurité, mais favorise également une meilleure collaboration des équipes et une meilleure adaptabilité aux changements, garantissant une compréhension globale des capacités et des limites de la solution.
La distinction entre la mise en service virtuelle et traditionnelle souligne les progrès et l'efficacité obtenus grâce aux simulations numériques. La mise en service virtuelle minimise le besoin d'activités approfondies sur site, réduit les risques associés aux tests physiques et accélère le processus de déploiement, ce qui en fait une stratégie cruciale pour les industries cherchant à adopter des technologies d'automatisation.
Avec l’intégration croissante des outils numériques dans la fabrication et l’évolution continue des logiciels de simulation, la mise en service virtuelle est sur le point de devenir une partie intégrante des projets d’automatisation. Il élimine les obstacles à l'adoption de l'automatisation en atténuant les risques et en réduisant les temps d'arrêt, démocratisant ainsi l'accès aux technologies de fabrication avancées.
Alors que les industries continuent de relever les défis liés à l’adoption de nouvelles technologies, le rôle de la mise en service virtuelle pour faciliter une intégration plus fluide, plus sûre et plus rentable des solutions d’automatisation ne peut être surestimé. Il témoigne de la puissance de la transformation numérique dans le secteur manufacturier, offrant un aperçu d'un avenir où les domaines virtuels et physiques convergeront pour optimiser les processus de production et stimuler l'innovation.
Merci à Alex Owen-Hill et John Hatzis de partager l'idée.