L’intelligence artificielle transforme les lignes de production modernes d’une manière que nous n’aurions jamais imaginée. Cet article explique comment les systèmes d’inspection IA optimisent les processus d’emballage tout en minimisant les déchets. Si vous vous souciez de l’efficacité de la fabrication, de la sécurité alimentaire et des solutions respectueuses de l’environnement, continuez à lire. Les informations présentées ici pourraient vous aider à adopter un avenir plus intelligent et plus vert.
Pourquoi se concentrer sur l’inspection par vision IA pour l’emballage en sachet ?
L'emballage en sachet est extrêmement populaire pour les snacks, les liquides, les aliments pour animaux et de nombreux autres produits. Il permet de gagner de la place sur les étagères, est facile à ouvrir et offre un aspect attrayant. D'après mon expérience, l'utilisation de sachets Inspection par vision IA pour emballage en sachet apporte un nouveau niveau de précision. Des caméras automatisées vérifient chaque sachet en temps réel, contribuant ainsi à garantir que chaque joint est étanche et sécurisé. Si un sachet est sous-rempli ou présente un petit défaut, le système peut le signaler instantanément à un station de rejet et l'empêcher d'avancer.
Un terme important à garder à l’esprit est intégrité du joint, c'est-à-dire la résistance et la qualité de l'étanchéité d'un emballage. Les méthodes traditionnelles reposent sur l'échantillonnage et les contrôles visuels par des humains, qui peuvent être lents et sujets à des erreurs. Les systèmes basés sur l'IA analysent les micro-détails que l'œil nu pourrait manquer, tels que tension du film ou de minuscules plis dans le plastique. Cela permet de garantir que les consommateurs reçoivent la bonne quantité de produit, sans risque de fuite ou de contamination.
« La qualité n’est jamais un accident ; elle est toujours le résultat d’un effort intelligent. » — John Ruskin
J'ai déjà expérimenté l'installation d'un dispositif de vision par IA en ligne sur une ligne de remplissage de sachets. La différence était la nuit et le jour. La machine a rapidement détecté les défauts avant même le scellage final, ce qui a permis d'économiser du temps et des matériaux.
Comment l’emballage IA révolutionne-t-il la fabrication ?
Emballage IA modifie la façon dont nous créons, remplissons et distribuons les produits. Les lignes de fabrication traditionnelles s'appuient sur des capteurs fixes qui détectent si un objet est présent, mais pas grand-chose d'autre. En revanche, les capteurs avancés basés sur l'IA reconnaissent des motifs subtils de forme, de couleur ou de taille. capteurs intelligents déclencher des actions correctives en quelques secondes.
Critères | Lignes de conditionnement traditionnelles | Lignes de conditionnement pilotées par l'IA |
---|---|---|
Méthode d'inspection | Vérifications manuelles ou de base des capteurs | Inspection visuelle avec des algorithmes d'IA |
Taux de détection d'erreur | Taux plus élevé de défauts négligés | Précision de détection supérieure à 99% dans de nombreux cas |
Approche de maintenance | Réactif (réparation après panne) | Prédictif (réparation avant panne) |
Utilisation du matériel | Souvent excessif en raison de contrôles moins précis | Optimisé pour la réduction des déchets |
Évolutivité | Flexibilité limitée ; des mises à niveau majeures sont nécessaires | Adaptable et facilement évolutif grâce aux mises à jour logicielles |
Conformité | S'appuie sur des contrôles manuels pour les réglementations | Suivi automatisé des scellés, des étiquettes et des objets étrangers |
Collecte de données | Journaux minimaux ou manuels | Données complètes en temps réel stocké au format numérique |
Un exemple est le système d'alimentation continue: le film d'emballage s'introduit dans une ligne sans interruption et la machine scanne le film pour détecter toute irrégularité telle que des déchirures, des désalignements ou des taches d'encre. L'IA peut même mesurer la précision des couleurs sur les étiquettes ou les images de marque, alertant les opérateurs si quelque chose ne va pas.
Ce niveau élevé d’intelligence artificielle contribue également à réduction des déchets. En détectant les défauts plus tôt, moins de matériaux sont gaspillés sur des emballages défectueux. Au cours d'un essai pilote, j'ai observé une réduction de 25% dans les films et plastiques gaspillés une fois que le criblage par IA était opérationnel. Les fabricants qui souhaitent atteindre des objectifs de développement durable en hausse devraient grandement bénéficier de ces améliorations.
Machine d'emballage avec contrôle qualité par IA
UN Machine d'emballage avec contrôle qualité par IA est souvent accompagné de fonctionnalités essentielles :
- Reconnaissance d'images en temps réel
Des caméras à grande vitesse enregistrent chaque étape, capturant des centaines d’images par minute. Reconnaissance d'image les algorithmes traitent ensuite les données, détectant les distorsions de forme ou de couleur. - Algorithmes adaptatifs
Les algorithmes d'IA apprennent à chaque nouveau cycle de production, en ajustant des paramètres comme la tension ou la pression. Cette nature adaptative permet au système de réagir rapidement lorsqu'un défaut apparaît. - Intégration des métadonnées
Les machines modernes s'intègrent aux systèmes d'entreprise existants, stockant des données cruciales sur les numéros de lots, les vitesses de production et les conditions environnementales.
D'après mes propres expériences pratiques, le plus grand avantage est la confiance qu'il apporte. maintenance prédictive Le module envoie des alertes si quelque chose est sur le point de tomber en panne, réduisant ainsi les temps d'arrêt. Les opérateurs peuvent également suivre les statistiques de la ligne de conditionnement en temps réel, ce qui facilite la planification de l'utilisation des ressources ou des horaires de travail.
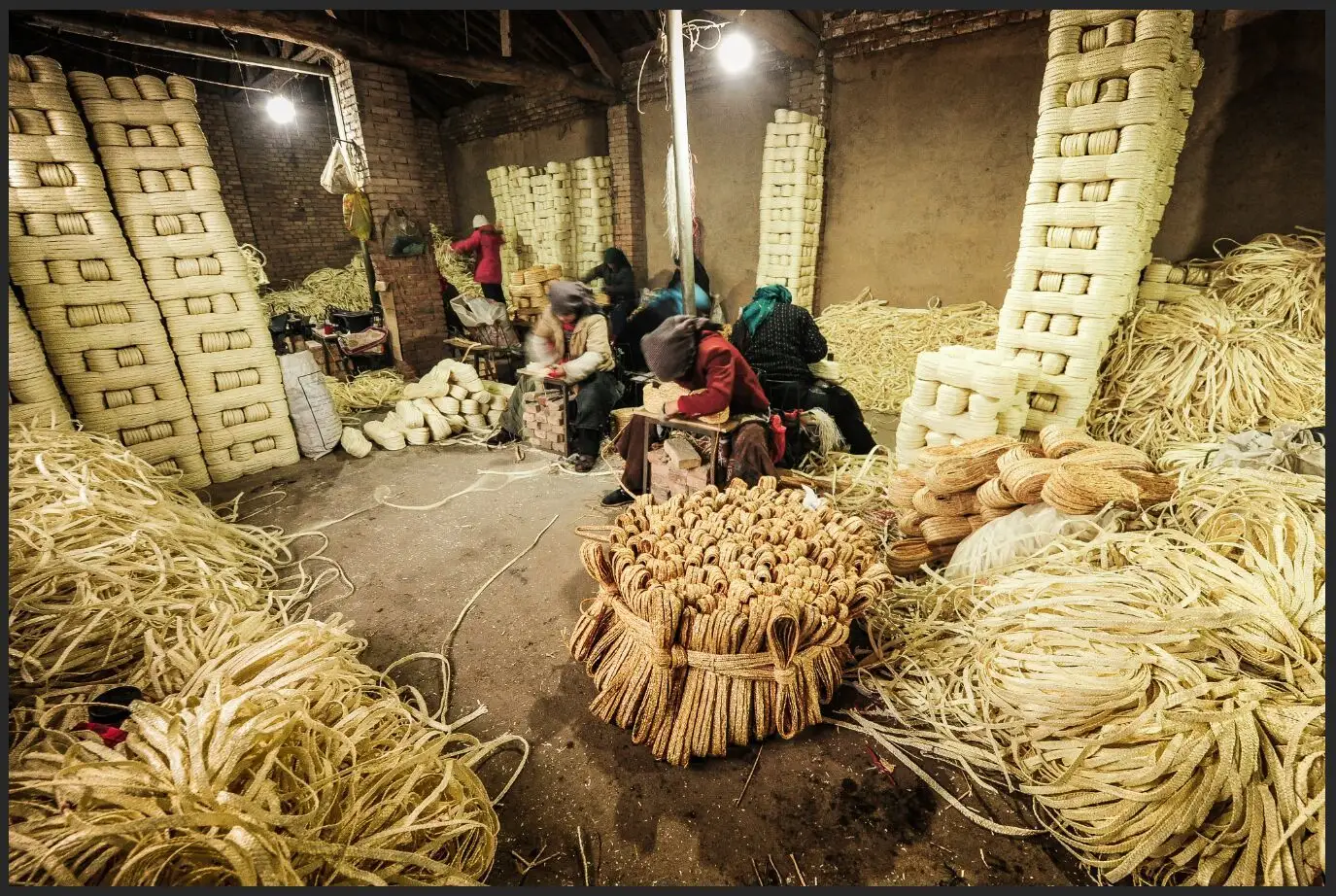
Je me souviens d’un scénario dans lequel une usine de céréales à haut volume est passée de capteurs mécaniques à une solution entièrement basée sur l’IA. Le résultat a été une diminution des retours de produits des centres de distribution et une meilleure fluidité du flux de produits. Les opérateurs m’ont dit que cela ressemblait à une « mise à niveau complète » de leurs routines quotidiennes.
Pourquoi la conformité à la sécurité alimentaire est importante
Conformité à la sécurité alimentaire Il ne s'agit pas seulement d'une obligation légale, mais d'une responsabilité morale. Que vous dirigiez une petite boulangerie ou une grande usine de transformation alimentaire, il est essentiel de garantir que chaque produit est propre à la consommation. Les outils d'IA permettent de suivre la propreté, la cohérence des produits et l'exactitude des étiquettes.
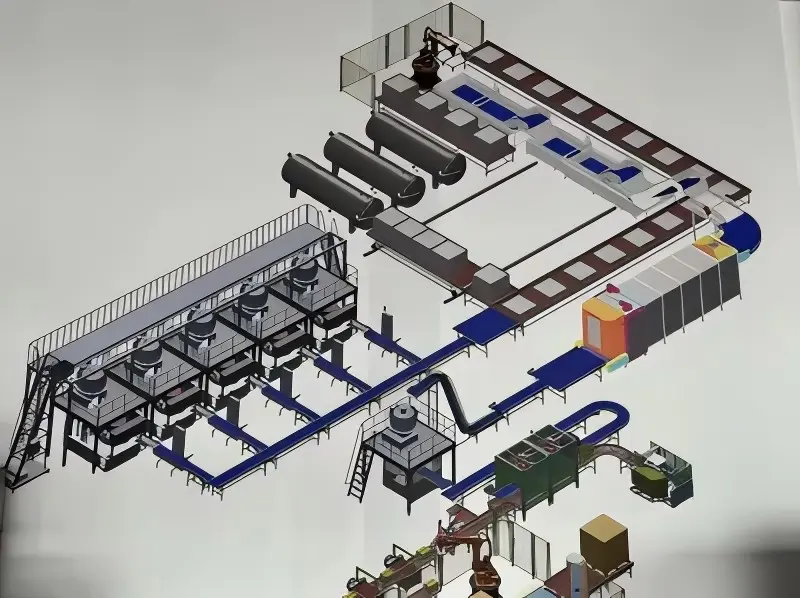
Emballage IA Les lignes de production comportent souvent des contrôles d'hygiène avancés. Des caméras et des capteurs peuvent identifier les contaminants qui s'infiltrent dans les zones de conditionnement. Ce système peut également vérifier l'étiquetage correct des allergènes, des informations nutritionnelles ou des codes de lot.
« En ne vous préparant pas, vous vous préparez à l’échec. » — Benjamin Franklin
Lorsque j'ai commencé à travailler dans une usine, la recherche de contaminants se faisait principalement par des contrôles aléatoires. Il était facile de rater un lot contaminé, surtout en grandes quantités. La technologie d'IA minimise ce risque, en alertant le personnel dès qu'un objet étranger inhabituel apparaît sur un tapis roulant. station de rejet détourne automatiquement l’élément suspect pour une analyse plus approfondie.
Le concept d'emballage antistatique
Emballage antistatique est conçu pour protéger les composants électroniques, les produits pharmaceutiques sensibles et même les produits alimentaires délicats contre les dommages électrostatiques. L'électricité statique, ou une petite charge électrique, peut endommager les micropuces ou dégrader certains produits si elle n'est pas contrôlée correctement. Les lignes d'emballage pilotées par l'IA garantissent que le antistatique la couche est intacte et efficacement scellée.
Dans certaines installations, la sécheresse de l'air ou la friction due aux opérations à grande vitesse peuvent provoquer une accumulation d'électricité statique. Une machine d'emballage intelligente peut mesurer l'humidité et la température tout en vérifiant si les revêtements de protection restent intacts. Lorsqu'elle détecte des pics inhabituels de charge électrique, elle effectue des ajustements immédiats ou alerte l'opérateur.
J'ai observé des machines qui pulvérisent automatiquement une fine brume ou ajustent les ioniseurs d'air en réponse aux données de apprentissage automatique analyse. Cela permet de créer un environnement sûr pour les produits sensibles à l'électricité statique. En se concentrant sur une solution spécialisée comme celle-ci, les usines évitent les rappels coûteux ou les dysfonctionnements des produits en aval.
Méthodes de détection des défauts de cloques à l'aide de l'IA
Inspection des défauts de cloques se concentre sur les emballages transparents ou semi-transparents que l'on trouve dans les produits pharmaceutiques, l'électronique ou les biens de consommation. Les plaquettes thermoformées permettent de séparer les articles individuels et de les protéger de l'humidité. Si la plaquette thermoformée est perforée ou mal formée, le produit peut se dégrader plus rapidement ou devenir dangereux s'il s'agit d'un médicament.
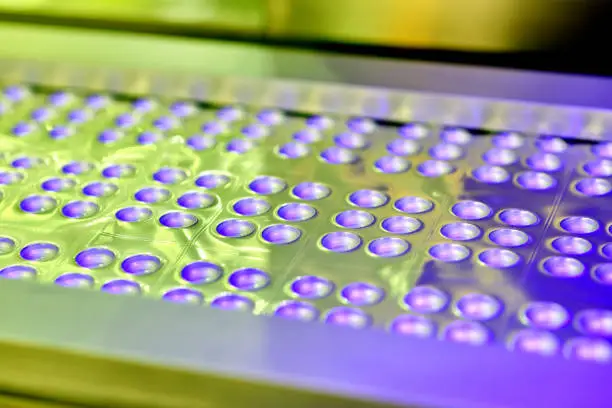
Inspection par vision IA pour emballage en sachet peut également s'appliquer ici. Vous disposez d'une caméra qui scanne chaque cavité du blister pour garantir qu'elle est entièrement formée et scellée. apprentissage automatique L'aspect consiste à mémoriser les formes normales des cloques et à reconnaître même la plus légère déformation.
Il existe deux principales stratégies de détection :
- Profilage optique :
Des caméras examinent la surface et analysent les petites alvéoles ou les bulles d'air. Si la forme est décalée d'une fraction de millimètre, une alerte se déclenche. - Numérisation infrarouge :
Certaines lignes avancées incluent des capteurs infrarouges qui détectent les fuites ou les variations d'épaisseur. Cela est particulièrement utile si le matériau du blister comprend plusieurs couches.
Lorsque j'ai testé ces systèmes, j'ai constaté qu'ils pouvaient traiter de gros volumes sans problème : des milliers de plaquettes par heure. L'analyse est automatique, ce qui permet d'économiser des heures de vérification manuelle. De plus, les données de chaque équipe sont réinjectées dans le modèle d'IA, ce qui améliore la précision de la détection au fil du temps.
Améliorer l'efficacité grâce à la maintenance prédictive basée sur l'IA
Maintenance prédictive utilise des données machine en temps réel pour prédire les pannes d'équipement avant qu'elles ne se produisent. Une ligne de conditionnement comporte de nombreuses pièces mobiles : courroies, engrenages, moteurs, capteurs. Au fil du temps, l'usure est normale. Au lieu d'attendre un dysfonctionnement évident, les systèmes d'IA surveillent la température, les vibrations et d'autres indices pouvant signaler une future panne.
Par exemple, si les niveaux de vibrations d'un moteur dépassent certains seuils de manière répétée, le système envoie une alerte. L'opérateur peut alors programmer un contrôle ou un remplacement, évitant ainsi un arrêt soudain pendant les périodes de pointe. Cette approche permet non seulement d'économiser de l'argent, mais aussi de rendre l'ensemble du pipeline de production plus fiable.
J'ai vu des ateliers d'emballage adopter cette méthode pour réduire les temps d'arrêt imprévus de plus de 40%. Ils avaient l'habitude de réparer les choses après qu'elles se soient cassées. Maintenant, ils les réparent avant qu'elles ne deviennent un problème plus grave. Ce changement est une grande partie de la durabilité Les soins préventifs permettent souvent de réduire la consommation d'énergie et le gaspillage des ressources.
Améliorer l'efficacité grâce à la maintenance prédictive basée sur l'IA
Maintenance prédictive utilise des données machine en temps réel pour prédire les pannes d'équipement avant qu'elles ne se produisent. Une ligne de conditionnement comporte de nombreuses pièces mobiles : courroies, engrenages, moteurs, capteurs. Au fil du temps, l'usure est normale. Au lieu d'attendre un dysfonctionnement évident, les systèmes d'IA surveillent la température, les vibrations et d'autres indices pouvant signaler une future panne.
Par exemple, si les niveaux de vibrations d'un moteur dépassent certains seuils de manière répétée, le système envoie une alerte. L'opérateur peut alors programmer un contrôle ou un remplacement, évitant ainsi un arrêt soudain pendant les périodes de pointe. Cette approche permet non seulement d'économiser de l'argent, mais aussi de rendre l'ensemble du pipeline de production plus fiable.
J'ai vu des ateliers d'emballage adopter cette méthode pour réduire les temps d'arrêt imprévus de plus de 40%. Ils avaient l'habitude de réparer les choses après qu'elles se soient cassées. Maintenant, ils les réparent avant qu'elles ne deviennent un problème plus grave. Ce changement est une grande partie de la durabilité Les soins préventifs permettent souvent de réduire la consommation d'énergie et le gaspillage des ressources.
Bonnes pratiques pour une intégration transparente de l'IA
L'introduction de l'intelligence artificielle dans une chaîne de production peut paraître compliquée. C'est en fait plus simple que la plupart des gens le pensent si vous suivez les meilleures pratiques :
- Projets pilotes :
Commencez par une petite section de la ligne. Concentrez-vous peut-être uniquement sur emballage antistatique ou des contrôles d'étiquettes. Évaluez les performances, collectez des données et utilisez-les pour affiner le modèle d'IA. - Formation des employés :
Certains employés pourraient s’inquiéter des nouvelles technologies. Montrez-leur comment elles facilitent leurs tâches, et non les rendent redondantes. Lorsque j’ai supervisé le déploiement d’une nouvelle IA, les employés ont apprécié le flux de travail plus fluide et le dépannage plus simple. - Sécurité et conformité des données :
Le stockage des données de production est une bonne chose, mais conservez-les en toute sécurité. Assurez-vous de respecter les réglementations locales en matière de confidentialité si des informations personnelles sont concernées. - Rétroaction continue :
Laissez le système d'IA apprendre de ses erreurs. S'il signale trop d'éléments à rejeter, ajustez les niveaux de seuil ou étiquetez les données avec plus de précision.
Ces étapes, combinées à une communication ouverte, peuvent permettre la transition des capteurs mécaniques vers des capteurs basés sur l'IA. inspection en ligne un jeu d'enfant. J'ai guidé quelques lignes à travers ce changement, et à chaque fois, le moral général s'est amélioré une fois que les gens ont vu les avantages tangibles.
Défis communs et solutions pratiques
Aucun système n'est parfait. Les lignes de conditionnement pilotées par l'IA rencontrent parfois des problèmes. Connaître ces défis peut vous aider à les résoudre immédiatement.
1. Surcharge de données
La collecte de millions de points de données par heure est une tâche formidable, mais elle peut submerger un personnel non préparé. La solution ? Utilisez des tableaux de bord conviviaux et limitez les indicateurs à ceux qui sont exploitables. Distiller les big data en informations quotidiennes ou hebdomadaires pour une prise de décision plus simple.
2. Coûts initiaux
Oui, les nouveaux équipements et la formation à l'IA peuvent être coûteux. Cependant, le retour sur investissement grâce à réduction des déchets, mieux conformité à la sécurité alimentaire, et moins de rappels équilibrent généralement la balance. Discutez avec les fournisseurs du financement ou des approches progressives. Mettez en œuvre l'IA par étapes plutôt que de procéder à une refonte complète.
3. Compatibilité des équipements
Parfois, les machines plus anciennes ne disposent pas des capteurs ou des sorties numériques nécessaires pour s'intégrer à l'IA. Il n'est pas toujours nécessaire d'acheter des lignes neuves. Des rénovations ou des mises à niveau partielles peuvent vous aider à fusionner les anciens systèmes avec la nouvelle technologie. Nous avons déjà remis à neuf une ligne vieille de 10 ans en ajoutant des capteurs de caméra et un petit ordinateur pour le traitement des données.
4. Maintenance continue
Même les équipements les plus intelligents ont besoin d'entretien. maintenance prédictive Vérifiez régulièrement la qualité de vos caméras et mettez régulièrement à jour le logiciel. Réétalonnez les capteurs selon un calendrier défini pour garantir l'exactitude de vos relevés.
J'ai personnellement contribué à la mise à niveau d'anciennes gammes. Le principal enseignement est que de petits changements peuvent produire des améliorations majeures. La mise à niveau des caméras, par exemple, ou l'ajout d'une couche logicielle avancée entraîne souvent un énorme bond en avant en termes de cohérence du packaging.