- Home
- Industries
- Granule
- Cheese
Cheese Packaging Machine
Automatic cheese packing machine automatically weighs, fills and seals cheese into packs. Cheese is loaded onto a conveyor, cut into blocks or shreds, and weighed into precise portions. The portions are packed into bags, trays, pouches or wrappers which are then sealed. Some sealers introduce inert gases like nitrogen before sealing to prevent spoilage.
High Speed sliced cheese packaging machines can pack thousands of units per hour. They ensure consistent pack weights and sizes for consumers and commercial use. Proper packing, sealing and sanitation maintain freshness and prolong shelf life. Pre-weighed, pre-packed cheese is convenient and affordable. Automated packaging cheese enables high-volume, efficient production. Machines convey, portion, fill, seal and may print product information on packs.
Sample bag
Machine Choice
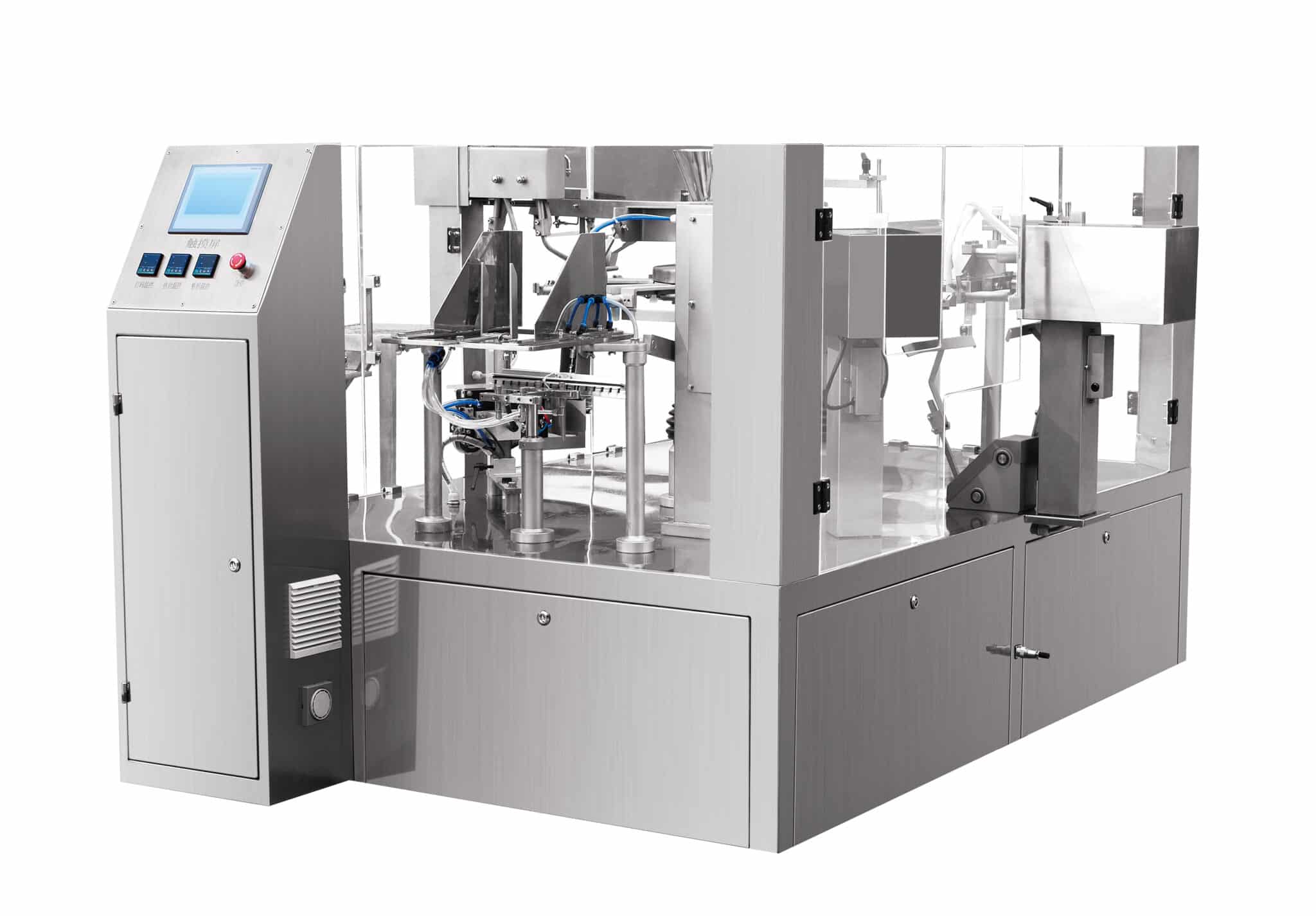
Rotating Premade Pouch Cheese Packaging Machine
Our Premade Bag Packaging Machine covers SS304 and adopts German/Japanese electronic components.Package up to 80 Bags/Min. We provide layout drawing services ,OEM service and decent delivery time.
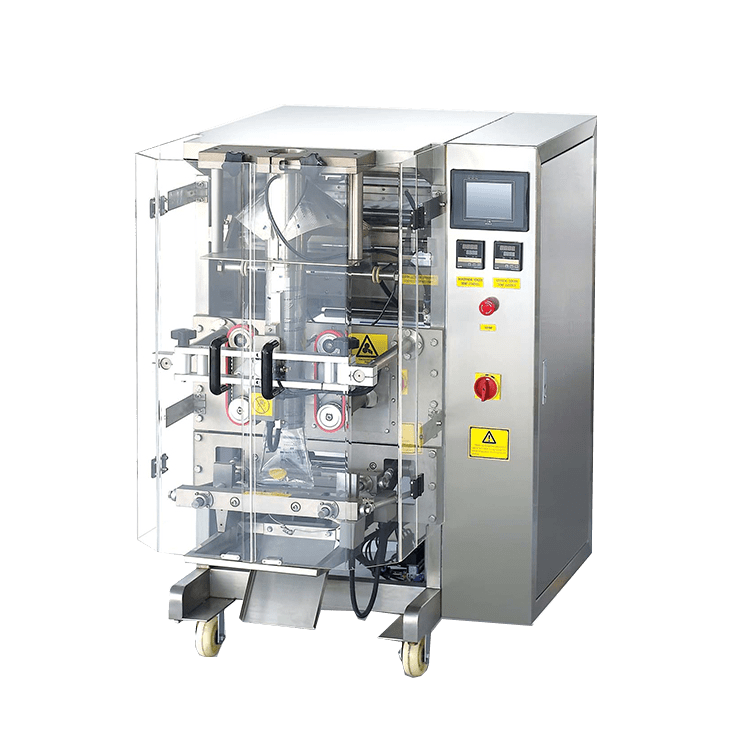
Vertical Form Fill Seal Machines For Cheese
Cheese VFFS Machine, as a classic solution for Granule packaging, is also one of the choices. Package Up to 60 Bags/Min,Low price .If you have no special requirements for the appearance of the product packaging, then it is a good Choice.
Ultimate FAQ Guide
The main components of cheese packing machine include several parts such as motor, transmission system, control system, feeding system, packing system, testing system and safety system.
The working process of cheese packing machine is to input cheese from feeding system to packing system first, after the packing process, cheese will be packed and finally tested by testing system to see if it meets the requirements and rejected if it does not.
Cheese packing machine is mainly used for packing all kinds of cheese products, which can be applied to various sizes and shapes of cheese, etc.
The size and weight of a cheese wrapping machine will vary depending on the specific model and the required production capacity, among other elements.
The price of cheese packaging machine will vary according to different manufacturers and configuration and other factors, specifically between hundreds of thousands of dollars to millions of dollars.
Lintyco offer customer hiqh quality cheese packing machine with affordable price.Contact us ,do not hesitate.
The service life of the cheese packaging machine varies according to the quality and maintenance of the machine and many other factors, generally between 5-10 years.
Cheese packaging machine maintenance issues need to pay attention to include regular cleaning, lubrication equipment, timely replacement of wearing parts, etc..
Learn more please click here
The electrical control system of the cheese packaging machine is mainly composed of the main controller, touch screen, inverter, servo motor, sensors and other major components.
The operation of cheese packaging machine is relatively simple, generally only need to carry out simple operations such as start, stop, adjust the parameters of the machine, also can be operated through the touch screen, the operation is less difficult.
Cheese packaging machine plays an important role in the production process with food, the control of production processes and production processes need to be strictly bound to ensure food safety.
Cheese packing machine can be applied to mass-produced cheese production line, but also can be used in small-scale cheese products processing workshop.
Some of the more well-known brands of cheese packing machines on the market today are Italdibipack, Multivac, PAC, ULMA, etc. Of course, in China we are one of the best cheese packing machine manufacuturer.
Cheese packaging machine power varies depending on the model and configuration, generally ranging from a few kilowatts to more than a dozen kilowatts.
Cheese packaging machine sealing methods are mainly heat sealing, cold sealing and heat pressure sealing.
The output of cheese packaging machine can be adjusted by controlling parameters such as feeding speed and packing speed.
Cheese packaging machine packaging materials mainly include polyethylene, polyester film, compound film, etc.
Cheese packaging machine compression device mainly includes automatic airbag, electric airbag, etc.
Cheese packaging machine footprint varies according to different models and configurations, generally ranging from a few dozen square meters to several hundred square meters.
The control system of cheese packaging machine mainly includes PLC control and touch screen control, etc.
The electrical components used in the cheese packaging machine are mainly ABB, SIEMENS, Mitsubishi and other brands.
Cheese packaging machine materials generally use stainless steel and other materials that meet sanitary standards.
The production process of cheese packaging machine will involve the generation of waste and other issues that need to be properly handled to protect the environment.
Cheese packaging machine needs to be stored in a dry, ventilated, temperature-appropriate place to prevent the equipment from moisture, rust and other problems.
Cheese packaging machine in the transportation process need to pay attention to protect the structure of the equipment, wearing parts and other parts to prevent damage to the equipment.
Before installing the cheese packaging machine, the following issues need to be noted:
1. whether the conditions of the site meet the requirements of the equipment, including electricity, environment, space and other conditions.
2. whether it is necessary to modify the site to match the installation and use of the equipment.
3. whether the necessary installation tools and materials are prepared for the installation process
4. whether the installation is carried out in accordance with the requirements of the equipment manual to prevent damage to the equipment or safety accidents caused by improper installation.
Translated with DeepL
Cheese packaging machines require operators with a certain level of technical skills and operating experience to be able to operate, maintain and service the equipment properly. In addition, operators also need to understand the corresponding food hygiene and safety standards to ensure that the production process meets the requirements of relevant laws and regulations.