- Home
- Industries
- Liquid
Liquid Packaging Machine
Automatic liquid packaging machines are designed to handle a wide range of liquids, including thick creams, gels, sauces (with or without particulates), infusions (such as cannabis-infused, CBD, or tincture oil products), and even water. The machines are built with durability in mind, making them capable of packaging in wet conditions without rusting or malfunctioning. This means that even acidic liquids, like pasta sauces, will not interfere with the smooth operation of our equipment. In addition, our machines can handle a wide range of fillers, making it possible to pack almost any fluid in a flexible bag.
For liquids, we will do waterproof treatment for the table, attach sealing strips and apply glass glue. For high bubble liquids, we will also lower the feeding position and equip it with a servo.
Liquid Packaging Machine Choice

LIQUID POUCH FILLING AND SEALING MACHINE
Lintyco Rotating Premade Pouch Packaging Machine is very suitable for liquid packaging, and can pack almost all liquids on the market. Its main advantage is that you can use Premade Pouch. Well-designed packaging bags can enhance your brand recognition. Using Spout bags and other styles to pack liquids can greatly enhance the product. Usability, and our packaging speed is one of the fastest on the market.
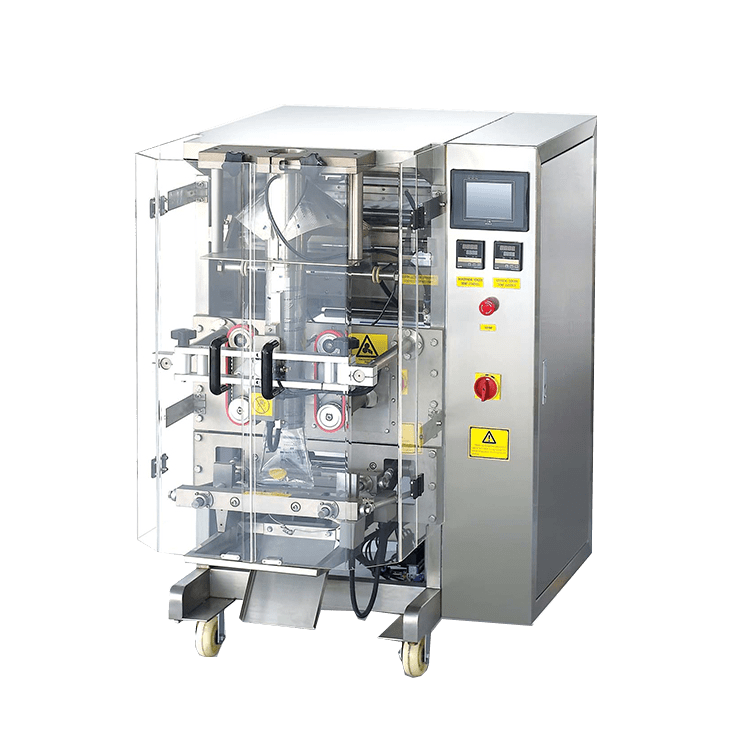
VERTICAL FORM FILL & SEAL LIQUID PACKING MACHINE
Lintyco Vertical Form Fill & Seal Machine can be an excellent choice for packaging certain common fluids, offering a low cost solution that does not compromise quality. This is especially true when it comes to small volume liquid sachet packing, such as cooking oil, shampoo, ketchup, and other similar products.
Playlist
There are several reasons why people choose doypack spout bags. First, they are convenient and easy to use, with a resealable spout that allows easy pouring and dispensing of the contents. In addition, they are lightweight and durable, making them a great choice for packaging a variety of products. Doypack spout bags are also eco-friendly, as they require less material to produce than traditional packaging options and are often made from recyclable materials. Finally, they offer excellent branding opportunities, with ample space for customization and branding.
Popular Bag Style
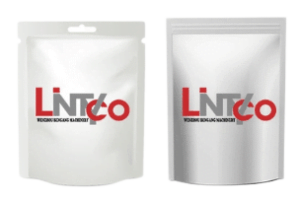
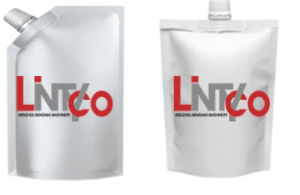
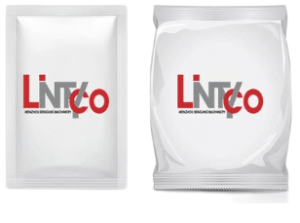
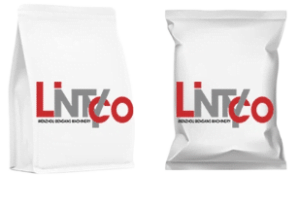
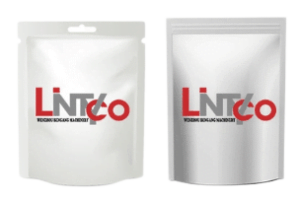
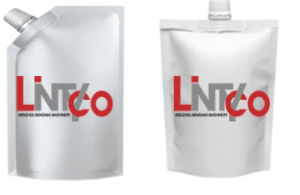
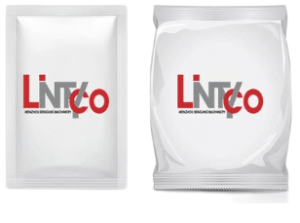
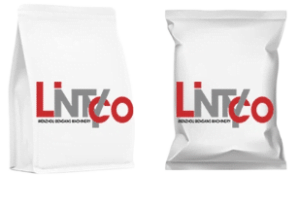
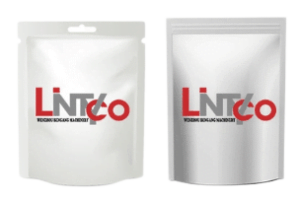
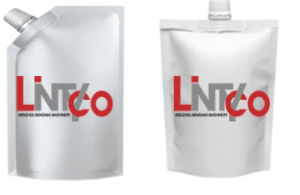
Ultimate Guide
Low Viscosity/Free-Flowing Liquids
- Examples: Water, alcohol, syrups
- Recommended Machines: Overflow and gravity filling machines
- These thin, water-like liquids freely flow into containers.
High Viscosity/Viscous Liquids
- Examples: Oils, creams, pastes
- Recommended Machines:
- Pump and piston fillers โ suitable for thick liquids that donโt pour easily
- Vacuum filling machines โ effective for filling viscous products and capturing every drop
Modern liquid filling machines offer flexibility to package nearly any type of liquid product with some machine adjustments for specific products. Examples of products filled into various industries include:
Food/Beverage โ waters, juices, sauces, oils and more.
Healthcare/Pharma โ vitamins, supplements, creams, lotions and solutions.
Cosmetics/Toiletries โ makeup, hair products, soaps and perfumes.
Chemicals โ paints, inks, solvents, polishes and cleaners.
Veterinary โ shampoos, treatments, supplements and creams.
Automotive โ lubricants, washes, polishes and liquids.
Home/Gardening โ cleaners, fertilizers, oils and fragrances.
Liquid fillers can be categorized by orientation, filling principle, automation level, and other factors critical to operations.
By Orientation
Rotary machines fill rapidly but waste more containers if issues arise during production. Inline systems allow easier issue resolution. Rotary units maximize outputs for large companies.
By Principle
Vacuum fillers gently draw viscous products. Volumetric systems precisely dispense quantities via gravity or pistons. Overflow ensures consistent levels rather than weights. Pumps propel thicker liquids. Net weight machines package to precise masses.
By Automation
Fully automatic machinery maximizes throughputs via integrated conveyors. Semi-automatic systems rely on manual placement but increase individual speeds. Manual units facilitate small-scale or remote applications without electricity.
Additional Considerations
Production volumes, product viscosities, container attributes, and operational requirements all influence the ideal solution. Proper machine selection streamlines packaging while minimizing waste. Please inquire about options matching your specific needs.
In summary, liquid filling machinery comes in various designs to suit diverse operating environments, capacities, and product handling needs. Analyzing classification factors leads to choosing the best equipment fit.
Popular formats include bottles, jars, pouches, bags-in-boxes and aseptic bag-in-cartons. Sizes range from ml to liter+ containers.
- Liquid Properties
- Viscosity โ thin/viscous?
- Temperature stability
- Particulates or other characteristics
Match the liquid to the optimal filling principle.
- Container Type
- Size/volume
- Material โ glass, plastic, metal?
- Clear or colored?
Select a machine suitable for your container.
- Production Needs
- Batch or continuous workflow?
- Volume/day or hour
- Consistency requirements
Higher automation for high volumes.
- Space and Budget
- Footprint
- Capital and operating costs
Consider space and budgetAllowances.
- Regulatory Compliance
- Cleaning/sanitizing needs
- Sealing/capping type
- Tracking and traceability
Choose a machine meeting regulations.
Doing your research upfront on these key selection criteria helps ensure you purchase the right-sized liquid filler solution for your specific packaging operation. Seek guidance from suppliers as needed.
Lintyco offer customized solution to design a machine tailored precisely to your unique liquid product and packaging needs.And we help you smooth startup and maximize performance.
Gravity, pump and pressure filling are common. Aseptic machines use sterile air or nitrogen filling. Some feature volumetric, weight-based or servo controls.
Rates vary by machine/package size but range from 50-5000+ packages/hour. Small tabletop machines fill 50-200 units/hr. Floor models reach 300-3000/hr.
You can get your free machine roi calculator here
Common checks are for fill weight/level, presence/tightness of caps/lids and package integrity/leak testing. Visual/camera inspections also performed.
Operation training and standard maintenance practices like periodic sanitation ensures long machine life. Automated models are easier to operate.
โ Cleaning โ Thoroughly clean all parts and surfaces that come into contact with the liquid on a regular schedule. Properly disassemble parts as needed.
โ Lubrication โ Lubricate moving parts like chains, gears, bearings according to the manual. Check for wear and replace if necessary.
โ Pump maintenance โ Inspect pump valves and seals for wear. Replace damaged or worn components.
โ Filter checks โ Inspect and clean filters that protect pumps from contamination on a scheduled basis.
โ Calibration โ Periodically calibrate fill level sensors and valves to ensure accurate, consistent filling.
โ Leak checks โ Inspect hoses, seals and connections regularly for leaks that could contaminate products.
โ Electrical checks โ Check terminals, wires and electrical components for corrosion or damage.
โ Safety systems โ Validate light curtains and sensors are working properly for safe operation.
โ Documentation โ Keep records of maintenance tasks, part replacements and errors logged.
โ Training โ Educate operators on basic maintenance procedures they can perform.
Liquid packing machine prices can vary significantly depending on the type of machine, features/options, capacity, and manufacturer. Here are some general price ranges for different liquid filling machine types:
Manual/Semi-Automatic Machines:
โ Entry-level tabletop models start around $5,000-$10,000
โ Floor/stand-alone models range from $10,000-$30,000
Automatic Inline Machines:
โ Small to medium systems with 4-12 filling heads are $30,000-$80,000
โ Larger machines with 12-24 heads range from $80,000-$150,000
Automatic Rotary/Carousel Machines:
โ Small machines with up to 24 stations start at $150,000
โ Medium machines with 24-48 stations are $150,000-$300,000
โ Large systems with 60+ stations range from $300,000-$500,000
Aseptic/Sterile Filling Machines:
โ These often require clean rooms and cost significantly more at $150,000-$500,000
Additional factors that impact price:
โ Product handling options (pumps, valves, etc)
โ Automation components
โ Container throughput capacity
โ Industry certification/compliance level
โ Custom engineering requirements
โ Regional taxes and duties