Oggi parlerò dell'ultimo progetto della nostra fabbrica cooperativa A'Saffa Foods. Imparerai a conoscere la sua storia e la fabbrica online di mangimi per bestiame e pollame
Benvenuti nel mangimificio A'Saffa Foods situato nel cuore di Salalah, Oman. Qui sarai testimone della dedizione guidata dall'esperienza di Van Alsen. A'Saffa Foods è stata fondata nel 2001 ed è cresciuta fino a diventare una delle principali aziende di pollame integrate verticalmente dell'Oman. Le sue attività principali sono concentrate nella regione di Salalah, che ospita impianti di produzione di pollame all'avanguardia e completamente integrati. La struttura integra perfettamente un incubatoio, un allevamento di polli da carne, un mangimificio e un impianto di lavorazione, tutti strategicamente posizionati in un unico sito.
A'Saffa ha preso la decisione strategica di aprire un nuovo mangimificio per aumentare la produzione in vari settori, tra cui allevamenti, incubatoi, mangimifici, macelli e lavorazione alimentare. Nel selezionare il fornitore ideale per il suo mangimificio, A'Saffa ha dato priorità a criteri quali durabilità, qualità ed efficienza energetica. Tenendo presente tutto ciò, Van Aarsen è stata la scelta perfetta per progettare e implementare un nuovo mangimificio da 50 tonnellate all'ora per A'Saffa Foods.
Alimentazione e dosaggio
Le materie prime vengono ricevute nella tramoggia di alimentazione e pulite da vagli rotanti e magneti. Da qui, le materie prime possono essere trasportate ai silos di mais, ai magazzini di soia o direttamente ai silos degli ingredienti. Dal contenitore di dosaggio, le materie prime vengono pesate e dosate in una macrobilancia di dosaggio da 6.000 kg. Il contenitore di scarico integrato garantisce uno scarico rapido delle parti pesate e riduce i tempi del ciclo batch. I minerali vengono ricevuti in grandi sacchi in una discarica separata nel magazzino adiacente all'edificio e trasportati meccanicamente al silo di dosaggio dei minerali.
Frantumazione e miscelazione
Dopo questo passaggio le materie prime entrano nella linea di macinazione e miscelazione. In due mulini a martelli GD1400, le materie prime vengono macinate con precisione per ottenere la dimensione e la struttura richieste. Il silo sotto il mulino a martelli è dotato di dispositivi antideflagranti per ridurre al minimo il rischio di polvere e potenziali scintille generati dal martello per garantire la sicurezza. Inoltre, gli ingredienti traccia confezionati in sacchetti vengono aggiunti manualmente in uno degli otto silos. Il peso massimo del lotto consentito per il sistema di microdosaggio è di 200 kg.
Miscelazione
Successivamente, il microassemblaggio viene dosato con precisione utilizzando una slitta azionata idraulicamente, consentendo una varietà di regolazioni alle impostazioni, alla velocità della slitta e alle aperture. Per i materiali con flussi impegnativi, quattro sili sono dotati di dispositivi di agitazione integrati. Inoltre, altri ingredienti possono essere introdotti tramite una scatola di additivi manuale situata sulla parte superiore del mixer. Tutti gli ingredienti della ricetta vengono miscelati perfettamente in un mixer MultiMix da 10.000 litri, garantendo una miscela omogenea. Aggiungere l'olio direttamente nel frullatore. Per prevenire la contaminazione, la tubazione del liquido è dotata di una funzione di spurgo dell'aria per evitare gocciolamenti dall'ugello durante il dosaggio del liquido.
Granulazione e condizionamento
La miscela viene convogliata dal miscelatore al silo polveri di una delle due linee di granulazione. La coclea dosatrice regola il trasporto del prodotto in base alla richiesta di carico del granulatore, inviandolo attraverso il contenitore a lunga conservazione al miscelatore di vapore. Mantenendo il pasto a una temperatura non inferiore a 85 gradi Celsius per almeno 3 minuti, tutti i potenziali agenti patogeni come la salmonella vengono uccisi, mantenendo il pasto igienico. Il pasto igienico e ben condizionato continua al granulatore CU900 XL dove viene compresso in granuli. Calcolati secondo la ricetta di A'Saffa, i due granulatori hanno una capacità prossima alle 30 tonnellate all'ora.
Calmarsi
I pellet vengono raffreddati fino a raggiungere la temperatura ambiente in un refrigeratore in controcorrente TK3000. Grazie al distributore rotante dei pellet, il prodotto viene raffreddato uniformemente prima di uscire dal meccanismo di scarico idraulico, mentre il livello effettivo del pellet viene misurato da un sensore di livello continuo di tipo ad ultrasuoni. Se necessario, le particelle possono essere frantumate. Dopo il processo di raffreddamento, i granuli e i trucioli vengono vagliati per eliminare la polvere e quindi riciclati in un contenitore sopra il granulatore. Infine, il pellet e il cippato vengono trasportati al silo di alimentazione finale. Qui vengono caricati su rimorchi per prodotti sfusi utilizzando soffietti di carico o inviati direttamente alla stazione di riempimento per essere confezionati in sacchi da 50 kg.
Linea di confezionamento alimentare di Lintyco
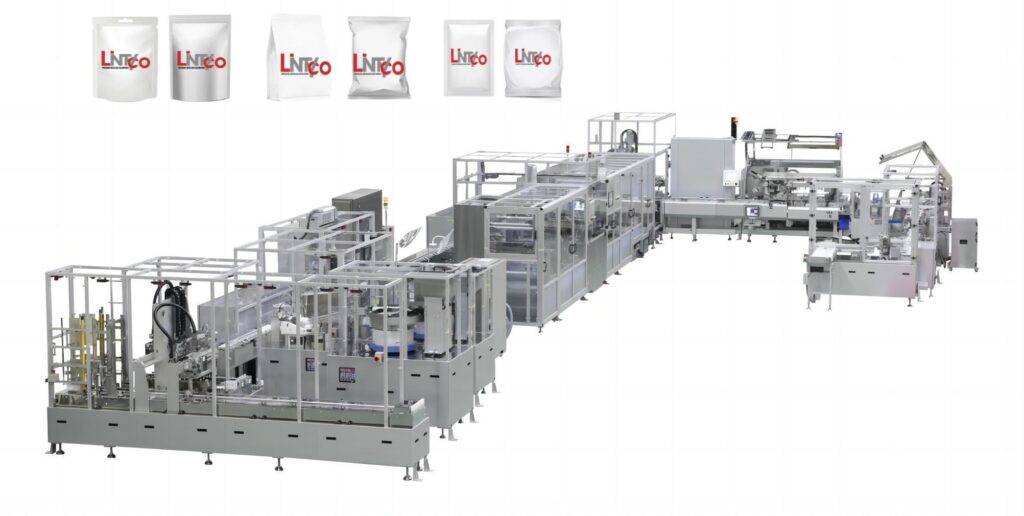
Lintico è un pioniere e leader nel macchine automatizzate per l'imballaggio alimentare E sistemi di imballaggio end-to-end. Le soluzioni di imballaggio innovative di Lintyco per prodotti alimentari, farmaceutici e altre applicazioni sono integrate da soluzioni avanzate per imballaggio secondario, confezionamento e inscatolamento, imballaggi sfusi e altro ancora. Che tu stia cercando una nuova macchina o una linea completa, o se desideri semplicemente aggiornare la tua attuale macchina confezionatrice, parla con Lintyco. In qualità di esperti del settore con oltre tre decenni di comprovata esperienza, Lintyco fornirà la soluzione ottimale supportata da consulenza e supporto eccellenti.