新しい自動化ソリューションを購入する前に試してみたいと思ったことはありませんか?これが仮想コミッショニングの背後にあるアイデアであり、自動化の未来となる可能性があります。
仮想コミッショニングを使用すると、理想的な自動化ソリューションの仮想モデルを作成できます。これらのソリューションをテストして微調整し、自動化テクノロジーが特定のプロセスでどのように機能するかを確認できます。
自動化ソリューションのコミッショニングは、複雑で時間のかかるプロセスとなる場合があります。仮想コミッショニングでは、ロボット シミュレーション テクノロジを使用して、その複雑さと時間の両方を軽減できます。自動化ソリューションをテストするために既存のマシンをオフラインにする必要がないため、不必要なダウンタイムが回避されます。
おそらく、仮想コミッショニングは今後も自動化プロセスの中核ステップであり続けると思われます。導入プロセスを合理化する方法を探している場合、このオプションが答えになるかもしれません。
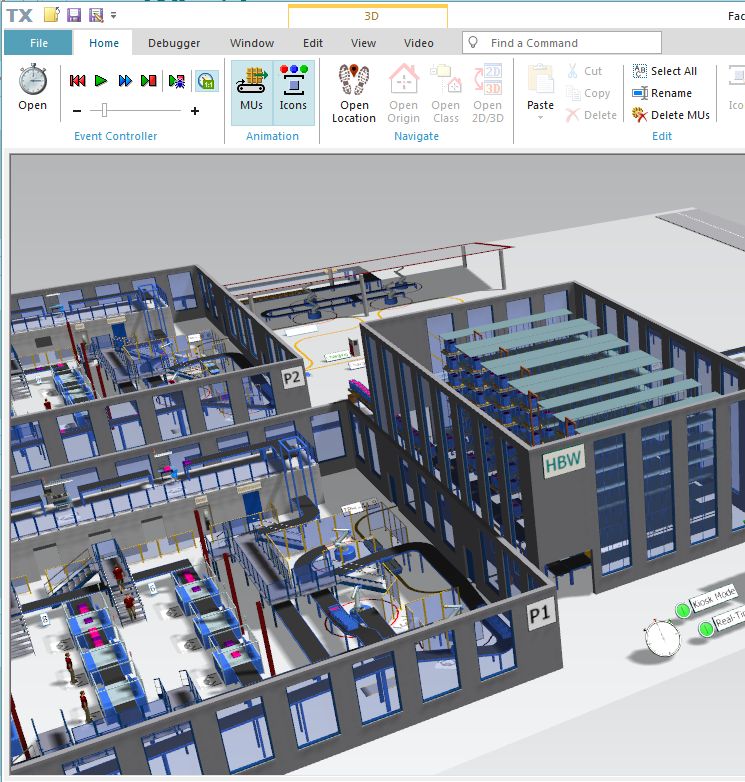
仮想コミッショニングとは何ですか?
仮想コミッショニングとは、物理ハードウェアを製造環境に導入する前に、シミュレーション テクノロジーを使用して自動化ソリューションを設計、インストール、テストすることです。たとえば、ロボット シミュレーション ソフトウェアを使用すると、不必要なダウンタイムを発生させることなくロボットの展開を最適化できます。
仮想試運転プロジェクトの中心となるのはシミュレーション ソフトウェアです。このソフトウェアには、使用される可能性のある自動化テクノロジーの仮想モデルに加え、システムの動作をテストするためのアルゴリズムと機能が含まれています。
ロボット ソリューションでは、同じシミュレーション ソフトウェアを使用して物理ロボットをプログラムできます。 RoboDK には、シミュレーション機能とオフライン プログラミング機能の両方が含まれています。シミュレーターでの展開のテストが完了したら、物理ロボットを接続し、プログラムをロボット ハードウェアに直接ダウンロードできます。
仮想コミッショニングと従来のコミッショニングの違い
仮想コミッショニングは本当に従来のコミッショニングとそれほど違いますか?
自動化プロジェクトをコミッショニングする 2 つのアプローチには、いくつかの重要な違いがあります。
従来のコミッショニングは通常、工場フロアなど、自動化ソリューションを導入する物理的な場所でオンサイトで行われます。手動によるトラブルシューティングのために、さまざまな物理ツールやテスト機器を持参します。これは、試運転プロジェクトの期間中、既存の製造プロセスの一部またはすべてを停止する必要がある可能性があり、コストがかかる可能性があることを意味します。
仮想コミッショニングでは、導入の大部分をリモートで実行し、現場に来るのは最後だけです。
また、従来の試運転プロセスでは時間がかかることが多く、オンサイトでの実装には大規模なチームが必要です。仮想コミッショニングを使用すると、小規模なチームまたは 1 人でも、導入の大部分をリモートで実行できます。
仮想コミッショニングはどのように機能しますか?
基本的な考え方は、自動化ソリューションのシミュレーションまたはデジタル ツインを作成することです。これは、プロセス内でマシン (複数可) がどのように動作するかを示す仮想モデルです。
この仮想モデルを使用してさまざまなシナリオをテストし、これが自動化ソリューションにどのような影響を与えるかを確認します。これは、物理環境に導入する前にソリューションを最適化するのに役立ちます。
ロボット シミュレーターを使用した仮想コミッショニングには、次の作業が含まれます。
- 生産ラインの関連部分の仮想モデルを作成またはインポートします。
- ロボット ライブラリからロボットのモデルを他の機器とともに読み込みます。
- 特定のアプリケーション向けのロボット プログラムを作成します。
- ロボット ソリューションを工場現場に展開する前に、ロボット ソリューションのさまざまな側面を最適化します。
この方法でコミッショニングに取り組むことで、管理されたリスクのない環境でソリューションをテストできます。
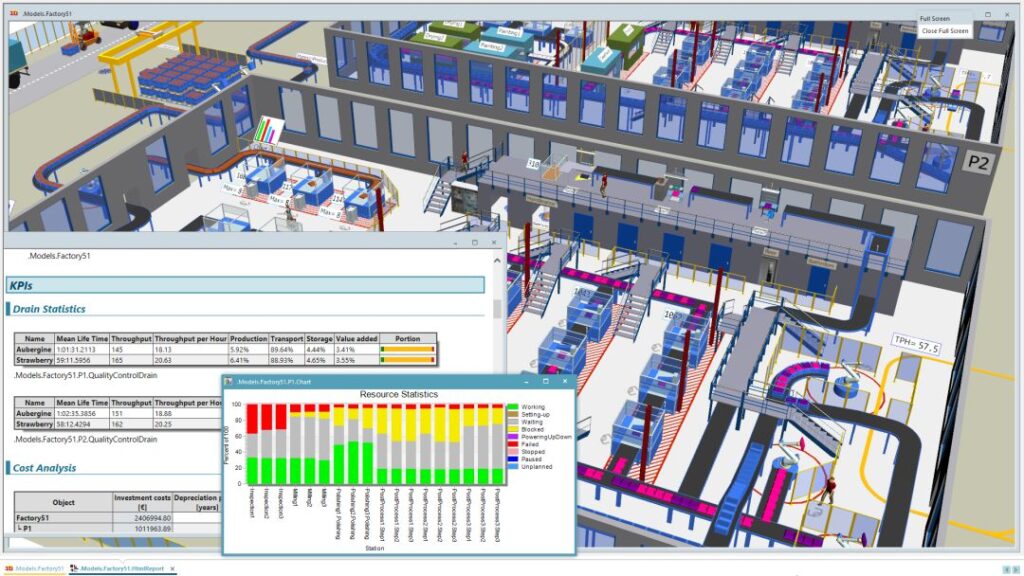
仮想コミッショニングの 5 つの独自の利点
仮想コミッショニングの 5 つの独自の利点を次に示します。
1. 効率的な導入
仮想コミッショニングにより、時間のかかるオンサイト作業の必要性が大幅に軽減されるため、導入の運用効率が向上します。これにより、コストのかかるダウンタイムを回避し、プロセス全体の効率が向上します。
2. より安全な自動化
仮想環境で自動化プロジェクトをシミュレートすることで、安全かつ制御された方法で潜在的な危険をテストできます。これは、従来の物理的な試運転プロセスで発生する可能性のある事故や怪我を回避するのに役立ちます。また、物理ハードウェアではテストできない危険な限界ケースをテストすることもできます。
3. チームコミュニケーションの改善
シミュレーターは、すべてのチーム メンバーが自動化ソリューションの変更を表示、理解し、提案するための共通のプラットフォームを提供できます。これはコミュニケーションを改善し、潜在的な誤解を避けるのに役立ちます。 RoboDK for Web を使用すると、同僚はシミュレーションを表示するためにソフトウェアをインストールする必要さえありません。
4. 変化に対する柔軟性
仮想試運転の大きな利点の 1 つは、生産プロセスの変更や調整が簡単であることです。制作を中断していないことを確認しながら、シミュレーターで新しいアイデアをすばやくテストできます。
5. ソリューションの理解を深める
最後に、シミュレーターで自動化ソリューションを開発すると、その仕組みをより深く理解できるようになります。仮想環境でテクノロジーを「試す」ことで、その可能性と限界についての実用的な知識をすぐに得ることができます。これは、現実世界でテクノロジーをより有効に活用するのに役立ちます。
仮想コミッショニングは自動化を変えるでしょうか?
デジタル ツールの人気が高まるにつれ、仮想コミッショニングは今後も定着していく可能性があります。
仮想コミッショニングは、多くのメーカーのロボット導入を制限していた自動化への参入障壁を打ち破るのに役立ちます。これにより、不必要なダウンタイムに伴うリスクを軽減しながら、誰でも自動化テクノロジーを製造プロセスに迅速かつ効率的に導入できるようになります。
仮想コミッショニングを使用してロボット テクノロジーを導入すると、自動化プロジェクトが成功する可能性が高まります。これにより、ロボット工学はソリューションとしてのリスクが軽減され、より価値のあるものになります。
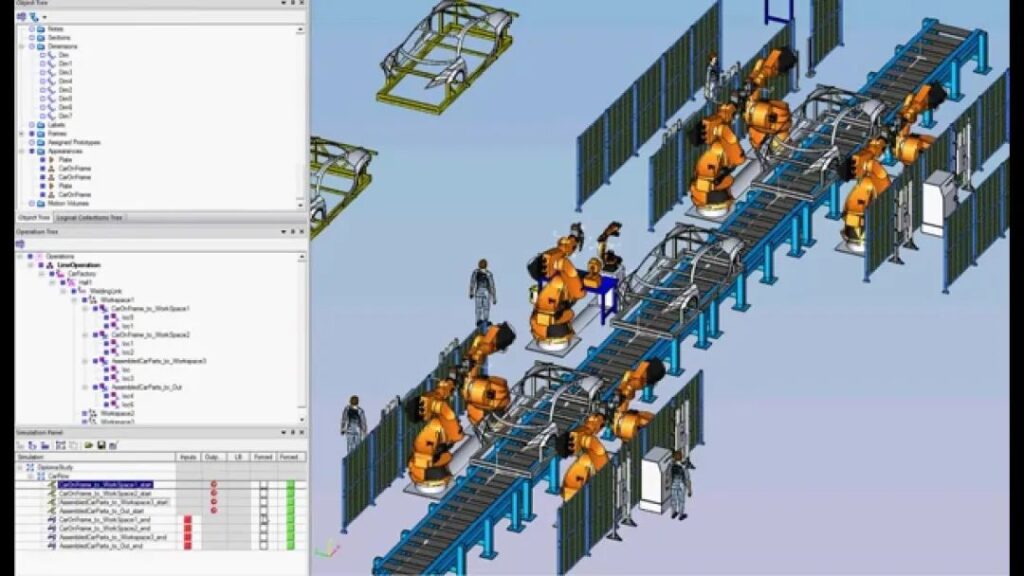
製薬施設の設計とエンジニアリングにおける技術トレンド
企業がコストの削減、リソースの完全な最適化、業務の合理化を目指す中、医薬品製造はテクノロジーの進歩に合わせて継続的に進化しています。これは設備の設計やエンジニアリングにも及びます。この記事では、製薬会社に大きな利益をもたらす、施設の設計とエンジニアリングに関連するいくつかの新しいテクノロジーのトレンドについて考察します。
仮想試運転
新しい製薬施設の建設と試運転には時間とコストがかかります。 PhRMA 新しい施設の建設には最大 1 TP4T20 億の費用がかかり、完成までには 5 年から 10 年かかると推定されています。これを念頭に置くと、運用をオンストリームにしてできるだけ早く投資収益率を生み出すために、試運転および建設プロセスのすべてのステップがスムーズ、効率的、かつコスト効率よく実行されることが重要です。
多くの場合、時間と資本の観点から見たコストのかなりの部分は、施設、ライン、および機器の試運転から直接発生します。施設の試運転にかかる全体的なコストを削減するには、施設や機器の設計、要件、構成に対する後期段階での変更や遅延を最小限に抑えるか、理想的には完全に排除する必要があります。これを解決するために、製薬メーカーは仮想コミッショニング、つまり従来の開発と仮想開発およびエミュレーションを使用したテストを組み合わせたアプローチに注目することができます。物理的なコミッショニングとは異なり、仮想コミッショニングは、ハードウェアを購入または構築するずっと前から開始できます。このアプローチにより、従来の試運転と比較して試運転時間を最大 40% 節約でき、リスクと不確実性が軽減され、安全性と機敏性が向上し、設計変更のコストが削減されます。
シミュレーション、エミュレーション、デジタルツイン
デジタル ツインは、物理エンティティと同期された現実世界の物理エンティティ、システム、またはプロセスを仮想的に表現したものです。デジタル ツインと観察可能な製造要素 (OME) は、通常、物理エンティティからデジタル ツインにセンサー データを伝播することによって同期されます。デジタル ツインはシミュレーションまたはエミュレーションで構築できますが、OME と同期する必要があります。同期されたエミュレーション/シミュレーションの頻度と忠実度は、それらが達成するように設計されたタスクに適切である必要があります。
デジタル ツインは、いくつかの異なる商用またはオープンソース ソフトウェア パッケージから構築できますが、物理要素、同期メカニズム、モデル/仮想表現 (通常は CAE/マルチフィジックス ソフトウェアから派生) を実行するために使用されるソフトウェア パッケージが必ず含まれます。デジタル ツインを作成するには、OME にとって重要な要素が仮想表現で正確に複製される必要があります。生産設備の場合、これには通常、アプリケーション固有のソフトウェアを実行する自動化システムに接続された、モーター、アクチュエーター、計測器などのプロセス システムまたはメカトロニクス システムの定義が含まれます。
生産設備にデジタル ツインを実装する価値は、すぐに観察できる以上の物理システムの状態を推定できる可能性があることです。これの一般的なアプリケーションには、ソフト センシング、適応型障害修正、モデル予測制御、予知保全などがあります。生産設備は、製造プロセス全体の大規模なデジタルツインに適合し、需要主導型のオンタイム製造をサポートできます。
仮想コミッショニング アプリケーションでは、物理機器が存在しない可能性があるため、デジタル ツインが不可能な場合があります。代わりに、生産設備のモデルが制御システムと並行して導入され、2 つが共同開発できるようになります。制御システムはコマンド出力やステータス フィードバック (ハードウェア イン ザ ループとして知られる) を通じてモデルと自然に対話できるため、制御システムは生産設備モデルをエミュレーションとみなします。この手法を成功させるには、生産設備モデルが物理システムの具体的な動作を正確に表現する必要があります。
エミュレーション ベースの仮想コミッショニングは、エラー回避とプロジェクト タイムラインの達成の観点から、プロジェクト リスクの貴重な軽減につながります。物理的な機器を使用せずにシナリオと設計の選択を徹底的にテストできるため、エンジニアは、スケジュールされたテスト機器に依存したり、オンになったりすることなく、アプリケーション固有のソフトウェア モジュール、レシピ構成、障害モードとリカバリ、ユーザー インターフェイスの有効性などのさまざまなシステム要素をテストおよび検証できます。サイト。その結果、仮想コミッショニングを採用するプロジェクトは、多くの場合、対面でのコミッショニング時間が短縮され、人や財産にとってより安全になります。
機器がコミッショニングされて検証されると、仮想コミッショニングからのエミュレーションは、物理機器に同期されたデジタル ツインとして使用を継続できます。モデルはすでに構築されているため、物理システムの理想化された表現としてすぐに役立ちます。エンジニアは、このデジタル ツインを使用して、設備設計、システム設計、生産ラインの運用、プラントと機械の要件などの要素を最適化できます。
コードとしてのインフラストラクチャ
IT/OT コンバージェンスの観点から見ると、仮想コミッショニングにより、アジャイル IT コンセプトを使用して OT 領域でコードとしてのインフラストラクチャなどのプロセスを開発できます。その目標は、コード開発とインフラストラクチャ構成の自動化に向けて進むことです。
これらの IT 概念の導入により、OT エンジニアのワークフローが根本的に変わります。従来の分散制御システム (DCS) の場合のように、システムとコードをゼロから構築するのではなく、エンジニアはアプリケーションの開発よりも自動化されたソフトウェア システムの保守に重点を置き、プロセスはアジャイル ソフトウェア開発の役割によく似たものになります。コードとインフラストラクチャ。エンド ユーザーにとって、これは、制御システムのインフラストラクチャのインストール、構成、パッチ適用という困難なタスクが自動化されたワークフローになることを意味する可能性があります。これにより、機械製造業者にとっては、エンジニアが関与することなく、顧客が選択したオプションに基づいて自動化インフラストラクチャとアプリケーション コードを動的に構築するための構成を送信して注文する注文処理システムが実現する可能性があります。
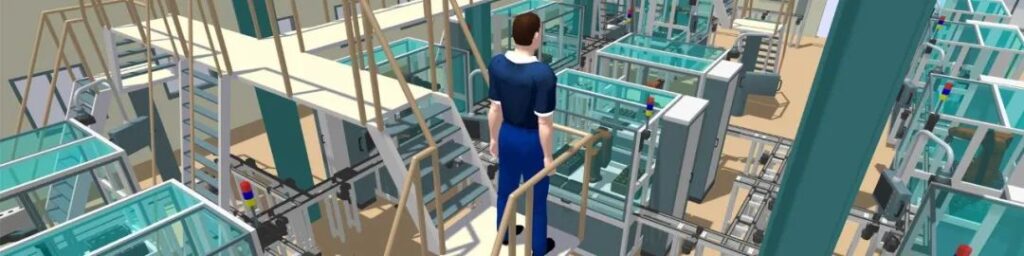
OEM機器のオーケストレーション
OEM 機器は、特定のプロセスに最適な機器ソリューションを選択して組み合わせる柔軟性を提供することで、最新のモジュール式医薬品製造プラントの基盤を形成します。 OEM 機器のコミッショニングと検証は、メーカーが事前に組み立てられ、目的に合わせてプログラムされたユニットを受け取るため、通常、より迅速なプロセスになります。さらに、OEM は通常、検証準備が整った状態で機器を供給するため、CGMP 施設での使用に適した機器の認定が容易になります。機器の構築やアプリケーション コードの開発を社内リソースやサードパーティに依存する必要はありません。ただし、さまざまな機器ベンダー間の接続規格やインターフェースの違いから課題が生じる可能性があり、複数の機器を統合制御システムに統合することが困難になります。ここで OEM 機器のオーケストレーションが役に立ちます。
オーケストレーション戦略の必要性
戦略的なアプローチと明確な仕様がなければ、OEM 機器を使用すると、自動化が断片化されてしまいます。この戦略の欠如は通常、エンドユーザー側の機器ベンダーとの協力が遅れていることが原因です。初期の機器調達プロセスで自動化が考慮されていない場合、エンジニアは機器の統合に苦労したり、統合の処理をエンジニアリング会社に依存したりすることがよくあります。後付けで機器をつなぎ合わせるこの後期プロセスでは、せいぜいプラント内のインターフェース機能が制限される可能性があります。最悪の場合、デジタル成熟度が上がらずに時間とコストがかかり、プロセス全体が裏目に出てしまう可能性があります。
これらの問題を解決するために、製薬メーカーは OEM 機器のオーケストレーションのための総合的な計画を採用し、施設の仕様と設計の初期段階でさまざまなコンポーネントを自動化および調整し、シームレスに連携できるようにすることができます。機器を購入する前に包括的な標準を確立することで、エンドユーザーは機器ベンダーと協力して作業することができ、OEM は自社の機器を統合自動化プラットフォームにどのように適合させるかについて差別化する機会を得ることができます。エンドユーザーにとって、これによりクロストレーニングが簡素化され、インターフェース、アラートシステム、診断、レシピ管理が標準化されます。これにより、コストが削減され、運用が合理化され、その結果、建設、試運転、施設の認定が迅速化されます。
標準化されたインターフェースの活用
エンドユーザーは、分散制御システム (DCS) または監視制御およびデータ取得 (SCADA) システムと統合するプラグアンドプロデュース機能を備えた OEM 機器を求めています。このプラグアンドプロデュース機能により、機器のインターフェイスやレシピ管理、ユーザー インターフェイス画面、監査証跡、異種機器にわたるアラーム管理などのコア自動化サービスが標準化されます。プラグアンドプロデュース標準は、これらすべての要素を系統的に接続し、NAMUR モジュール タイプ パッケージ (MTP) や最新のプロトコル (OPC ユニファイド アーキテクチャ (OPCUA) など) などの標準化されたインターフェイスを使用して調整します。これらの異なるプラットフォームをすべて統合すると、一貫性がもたらされ、統合にかかる時間と労力が節約され、プラグアンドプロデュースが将来の施設に実現可能なテクノロジーになります。
これらのテクノロジーは、組織間のコラボレーションや包括的な仕様によって行われるすべての作業を置き換えるのではなく、OEM オーケストレーションのための一貫した戦略の強化として見なされるべきです。機器をシームレスに統合して共通のサービスセットを提供するための魔法のボタンは存在せず、効果的な OEM オーケストレーション戦略にはエンドユーザーと機器およびテクノロジーベンダーとの建設的な関係が大きな役割を果たします。この状況を考えてみてください。標準化されたインターフェイスを備えたブラック ボックス機器だけで構築されたプラントは統合が早いかもしれませんが、多数のサポート契約の管理、さまざまなスペアパーツの管理、および不足のため、エンド ユーザーが長期サポートするのは困難でコストがかかります。 OEM 機器上のアプリケーション ソフトウェアの一貫性や、アプリケーション ソフトウェアへのアクセスさえも保証されます。
たくさんのメリット
簡単に言えば、OEM 機器のオーケストレーションにより、施設向けの統合自動化プラットフォームの作成作業が容易になります。これにより、最終的に市場投入までの時間が短縮され、エンドユーザーの総所有コストが削減されます。効果的なオーケストレーションにより、簡単なカスタマイズと拡張性、既存システムへの新しい機器の追加、将来のアップグレードと拡張のシームレスな統合を可能にする方法で、さまざまな OEM コンポーネントを統合できます。トラブルシューティングとメンテナンスを簡素化することで、ダウンタイムと平均修復時間 (MTTR) が短縮されます。
先進医療用医薬品
設備エンジニアリングに関連するもう 1 つの新たなトレンドは、高度な治療用医薬品 (ATMP) 分野に適合するための産業オートメーションの変化です。これらの治療法の多くは自己由来のものです。つまり、ある人から供給されて同じ人にフィードバックされることを意味します。これらの自己療法の生産量は非常に少なく、多くの場合ミリリットル単位です。既存のオートメーション システムは大規模な生産を目的として設計されているため、ここでのコンセプトは、ベンチトップ ユニットまたは機器で実行できるようにオートメーション テクノロジを小型化することです。これらのベンチトップ ユニットは、治療を行うための調整されたプロセス トレインに統合され、プロセスはより多くの個々の患者に対してより多くのプロセス トレインに対応できるようにスケール アウトできます。
この戦略の成功の鍵は、自動化ベンダーが自社のテクノロジーをスケールダウンして、同じ商用の既製ソフトウェアおよびハードウェア機能をベンチトップ機器に提供する意欲にあるでしょう。これは、プロセス開発 (PD) 分野からこれらの先進的な治療法の cGMP 製造への技術移転に必要な再作業の量を制限するために不可欠です。精度と患者の安全を確保するために、これらの異なる産業用機器や実験用機器をスケールダウンして柔軟に運用できる能力を持つオートメーション ベンダーとのコラボレーションが非常に重要です。
開始から完成まで
製薬会社は、生産性、効率、投資収益率を向上させ、競争力を維持するためにテクノロジーを積極的に導入しています。仮想コミッショニングや OEM 機器のオーケストレーションなどの取り組みは、新しい容量や機能の導入を促進するだけでなく、施設運用を最適化して最終的には適応性のある施設を実現するために採用されています。
仮想コミッショニングを利用すると、物理的な作業を開始する前に施設を設計、モデル化、エンジニアリング、テストできます。このアプローチにより、レイアウト、生産性、スループット、フロー、エネルギー効率などのさまざまな側面の最適化が可能になります。 OEM 機器のオーケストレーションによりプロセスが自動化され、インターフェイスが標準化されるため、施設向けの統合自動化プラットフォームの作成作業が容易になり、最終的に市場投入までの時間が短縮され、エンド ユーザーの総所有コストが削減されます。
新しいテクノロジーの力を活用する製薬会社は、開始から完了まで施設のプロセスを最適化するための設備が整います。
結論
バーチャルコミッショニングはオートメーションにおける技術進歩の最前線にあり、オートメーションソリューションをより効果的に統合することを目指す業界に革新的なアプローチを提供します。シミュレーション技術を活用することにより、仮想コミッショニングにより、企業は物理的な実装前にデジタル環境で自動化システムを設計、テスト、改良することができます。このプロセスにより、効率と安全性が向上するだけでなく、チームのコラボレーションと変更への適応力が向上し、ソリューションの機能と限界を包括的に理解できるようになります。
仮想コミッショニングと従来のコミッショニングの違いは、デジタル シミュレーションを通じて得られる進歩と効率を強調しています。仮想コミッショニングは、大規模なオンサイト活動の必要性を最小限に抑え、物理テストに関連するリスクを軽減し、展開プロセスを加速するため、自動化テクノロジーの導入を検討している業界にとって極めて重要な戦略となります。
製造におけるデジタルツールの統合の増加とシミュレーションソフトウェアの継続的な進化により、仮想コミッショニングは自動化プロジェクトの不可欠なコンポーネントになる準備が整っています。リスクを軽減し、ダウンタイムを削減することで自動化導入の障壁を打ち破り、高度な製造技術へのアクセスを民主化します。
業界が新しいテクノロジーの導入という課題に対処し続ける中、自動化ソリューションのよりスムーズで安全な、よりコスト効率の高い統合を促進する仮想コミッショニングの役割は、どれだけ強調してもしすぎることはありません。これは製造業におけるデジタル変革の力の証であり、仮想領域と物理的領域が融合して生産プロセスを最適化し、イノベーションを推進する未来を垣間見ることができます。
Alex Owen-Hill と John Hatzis がアイデアを共有してくれてありがとう。