Heb je er ooit van gedroomd om een nieuwe automatiseringsoplossing eerst uit te proberen voordat je hem kocht? Dit is het idee achter virtuele inbedrijfstelling... en het zou wel eens de toekomst van automatisering kunnen zijn.
Met virtuele inbedrijfstelling creëert u een virtueel model van uw ideale automatiseringsoplossingen. U kunt deze oplossingen testen, aanpassen en zien hoe de automatiseringstechnologie werkt met uw specifieke proces.
Het in bedrijf stellen van een automatiseringsoplossing kan een complex en tijdrovend proces zijn. Met virtuele inbedrijfstelling kunt u robotica-simulatietechnologie gebruiken om zowel de complexiteit als de tijd te verminderen. Het voorkomt onnodige downtime, omdat u uw bestaande machines niet offline hoeft te halen om de automatiseringsoplossing te testen.
Het lijkt erop dat virtuele inbedrijfstelling voortaan een kernstap in het automatiseringsproces zal blijven. Als u op zoek bent naar een manier om uw implementatieproces te stroomlijnen, is deze optie wellicht de oplossing.
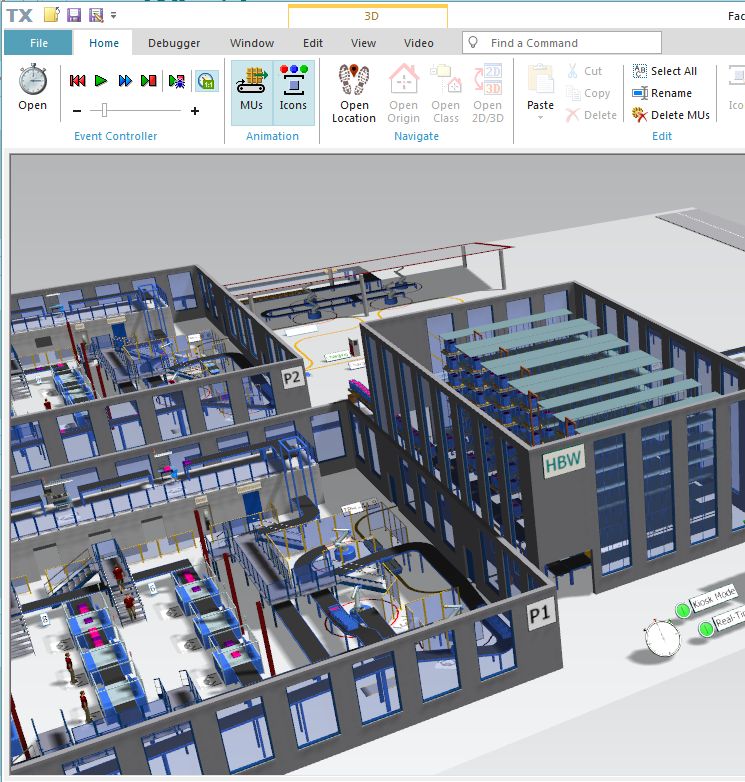
Wat is Virtuele Inbedrijfstelling?
Virtuele inbedrijfstelling is het gebruik van simulatietechnologie om automatiseringsoplossingen te ontwerpen, installeren en testen voordat de fysieke hardware in een productieomgeving wordt geïmplementeerd. Robotsimulatiesoftware kan bijvoorbeeld de inzet van een robot optimaliseren zonder onnodige downtime.
De kern van elk virtueel inbedrijfstellingsproject is de simulatiesoftware. Deze software bevat virtuele modellen van alle mogelijke automatiseringstechnologieën, evenals algoritmen en functionaliteit om de werking van uw systeem te testen.
Met robotoplossingen kunt u dezelfde simulatiesoftware gebruiken om de fysieke robot te programmeren. RoboDK bevat zowel simulatie- als offline programmeerfunctionaliteit. Nadat u uw implementatie in de simulator hebt getest, kunt u uw fysieke robot aansluiten en het programma rechtstreeks naar de robothardware downloaden.
Het verschil tussen virtuele en traditionele inbedrijfstelling
Is virtuele inbedrijfstelling echt zo anders dan traditionele inbedrijfstelling?
Er zijn enkele belangrijke verschillen tussen de twee benaderingen voor het in bedrijf stellen van een automatiseringsproject.
Traditionele inbedrijfstelling vindt doorgaans plaats op de fysieke locatie waar u de automatiseringsoplossing gaat implementeren, zoals uw fabrieksvloer. U neemt diverse fysieke gereedschappen en testapparatuur mee voor handmatige probleemoplossing. Dit betekent dat u mogelijk een deel of al uw bestaande productieprocessen moet stilleggen gedurende het inbedrijfstellingsproject, wat kostbaar kan zijn.
Bij virtuele inbedrijfstelling voert u het grootste deel van de implementatie op afstand uit en komt u pas helemaal op locatie.
Bovendien duurt het traditionele inbedrijfstellingsproces vaak langer en is er een groter team nodig voor implementatie op locatie. Met virtuele inbedrijfstelling kan een klein team, of zelfs één persoon, het grootste deel van de implementatie op afstand uitvoeren.
Hoe werkt virtuele inbedrijfstelling?
Het basisidee is om een simulatie of digitale tweeling van uw automatiseringsoplossing te creëren. Dit is een virtueel model dat laat zien hoe de machine (of machines) in uw proces zullen werken.
Met dit virtuele model kunt u verschillende scenario's testen om te zien hoe dit de automatiseringsoplossing beïnvloedt. Dit helpt u de oplossing te optimaliseren voordat u deze in de fysieke omgeving implementeert.
Virtuele inbedrijfstelling met een robotsimulator omvat:
- Het maken of importeren van virtuele modellen van de relevante onderdelen van uw productielijn.
- Modellen van uw robot laden uit de Robotbibliotheek, samen met eventuele andere apparatuur.
- Een robotprogramma maken voor uw specifieke toepassing.
- Optimaliseer de verschillende aspecten van uw robotoplossing voordat u deze op uw fabrieksvloer implementeert.
Door de inbedrijfstelling op deze manier aan te pakken, kunt u uw oplossing in een gecontroleerde en risicoloze omgeving testen.
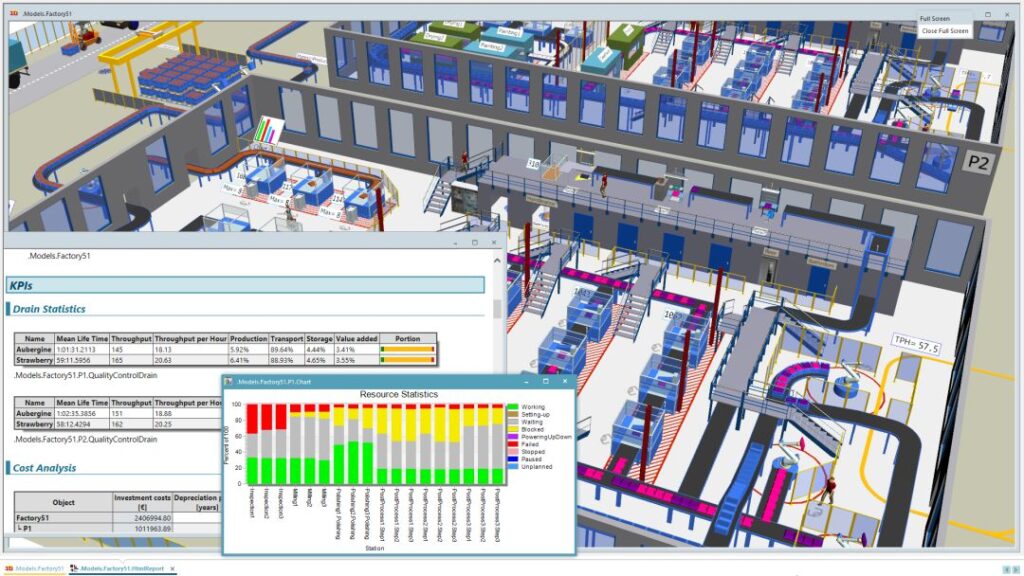
5 unieke voordelen van virtuele inbedrijfstelling
Hier zijn 5 unieke voordelen van virtuele inbedrijfstelling:
1. Efficiënte implementaties
Omdat virtuele inbedrijfstelling de noodzaak van tijdrovende activiteiten op locatie aanzienlijk vermindert, verbetert het de operationele efficiëntie van uw implementatie. Dit helpt u kostbare downtime te voorkomen en maakt uw proces over het algemeen efficiënter.
2. Veiligere automatisering
Door uw automatiseringsproject in een virtuele omgeving te simuleren, kunt u potentiële gevaren op een veilige en gecontroleerde manier testen. Dit helpt u ongevallen en letsel te voorkomen die zich kunnen voordoen bij een traditioneel fysiek inbedrijfstellingsproces. Het stelt u ook in staat om gevaarlijke grensgevallen te testen die met fysieke hardware onmogelijk te testen zouden zijn.
3. Verbeterde teamcommunicatie
Een simulator kan een gemeenschappelijk platform bieden voor al uw teamleden om uw automatiseringsoplossing te bekijken, te begrijpen en wijzigingen voor te stellen. Dit kan de communicatie verbeteren en mogelijke misverstanden voorkomen. Met RoboDK voor Web hoeven uw collega's de software niet eens te installeren om de simulatie te bekijken.
4. Flexibiliteit voor veranderingen
Een belangrijk voordeel van virtuele inbedrijfstelling is dat u eenvoudig wijzigingen of aanpassingen in uw productieproces kunt aanbrengen. U kunt snel nieuwe ideeën testen in de simulator, wetende dat u uw productie niet verstoort.
5. Beter begrip van de oplossing
Ten slotte kunt u door uw automatiseringsoplossing in een simulator te ontwikkelen, beter begrijpen hoe deze werkt. Door in een virtuele omgeving met de technologie te 'spelen', krijgt u snel inzicht in de mogelijkheden en beperkingen ervan. Dit helpt u de technologie in de echte wereld beter te benutten.
Zal Virtual Commissioning de automatisering veranderen?
Met de steeds toenemende populariteit van digitale hulpmiddelen lijkt het erop dat virtueel opdrachtgeverschap niet meer weg te denken is.
Virtuele inbedrijfstelling helpt de drempels voor automatisering te slechten die de acceptatie van robots voor veel fabrikanten hebben beperkt. Het stelt iedereen in staat om snel en efficiënt automatiseringstechnologieën in hun productieprocessen te implementeren en tegelijkertijd de risico's van onnodige downtime te verminderen.
Wanneer u uw robottechnologie inzet met virtuele inbedrijfstelling, vergroot u de kans op een succesvol automatiseringsproject. Dit maakt robotica als oplossing minder risicovol en waardevoller.
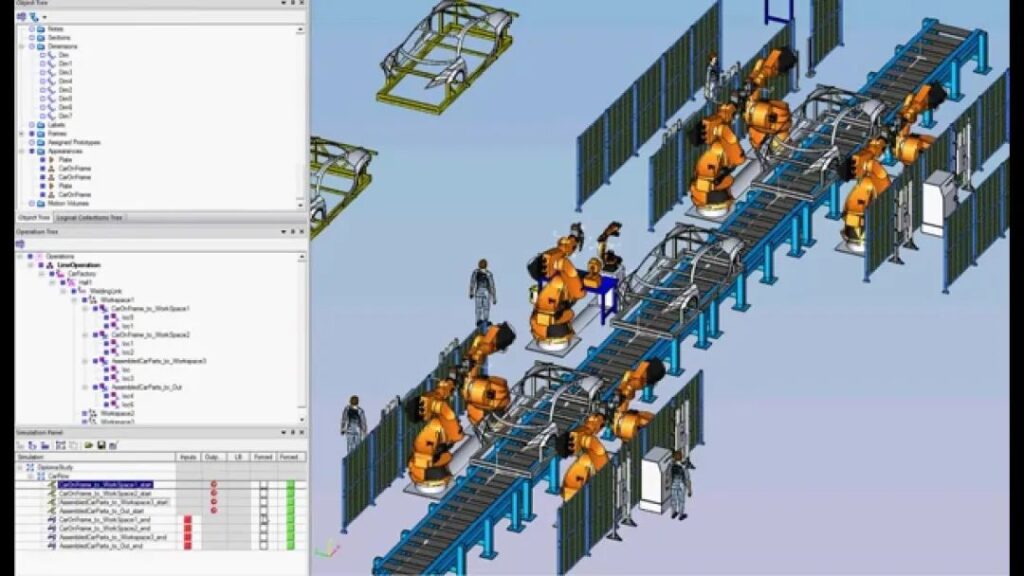
Technologische trends in het ontwerp en de engineering van farmaceutische faciliteiten
De farmaceutische productie ontwikkelt zich voortdurend mee met de technologische vooruitgang, omdat bedrijven kosten willen verlagen, middelen optimaal willen benutten en hun processen willen stroomlijnen. Dit geldt ook voor het ontwerp en de engineering van faciliteiten. Dit artikel onderzoekt verschillende opkomende technologische trends met betrekking tot het ontwerp en de engineering van faciliteiten die aanzienlijke voordelen opleveren voor farmaceutische bedrijven.
Virtuele inbedrijfstelling
De bouw en ingebruikname van nieuwe farmaceutische faciliteiten zijn tijdrovend en kostbaar. PhRMA schat dat de bouw van een nieuwe faciliteit tot $2 miljard kan kosten en 5 tot 10 jaar in beslag kan nemen. Daarom is het cruciaal dat elke stap in het inbedrijfstellings- en bouwproces soepel, efficiënt en kosteneffectief wordt uitgevoerd, zodat de werkzaamheden op gang komen en de investering zo snel mogelijk rendement oplevert.
Vaak komt een aanzienlijk deel van die kosten, qua tijd en kapitaal, rechtstreeks voort uit de inbedrijfstelling van faciliteiten, productielijnen en apparatuur. Wijzigingen of vertragingen in een laat stadium van het ontwerp, de vereisten en de configuraties van faciliteiten of apparatuur moeten worden geminimaliseerd of idealiter volledig worden geëlimineerd om de totale kosten van de inbedrijfstelling te verlagen. Om dit op te lossen, kunnen farmaceutische fabrikanten kiezen voor virtuele inbedrijfstelling, een aanpak die traditionele en virtuele ontwikkeling en testen combineert met behulp van emulatie. In tegenstelling tot fysieke inbedrijfstelling kan virtuele inbedrijfstelling lang voordat er hardware is aangeschaft of gebouwd, beginnen. Deze aanpak bespaart tot wel 40% aan inbedrijfstellingstijd in vergelijking met conventionele inbedrijfstelling, waardoor risico's en onzekerheid worden verminderd, de veiligheid en flexibiliteit worden verhoogd en de kosten voor ontwerpwijzigingen worden verlaagd.
Simulatie, emulatie en digitale tweelingen
Een digitale tweeling is een virtuele representatie van een fysieke entiteit, systeem of proces uit de echte wereld, die gesynchroniseerd is met de fysieke entiteit. De digitale tweeling en het waarneembare productie-element (OME) worden doorgaans gesynchroniseerd door de sensorgegevens van de fysieke entiteit naar de digitale tweeling te sturen. Digitale tweelingen kunnen bestaan uit simulaties of emulaties, maar moeten gesynchroniseerd zijn met de OME. De frequentie en nauwkeurigheid van de gesynchroniseerde emulaties/simulaties moeten geschikt zijn voor de taak waarvoor ze ontworpen zijn.
Digitale tweelingen kunnen worden gebouwd met behulp van verschillende commerciële of open-source softwarepakketten, maar bevatten altijd het fysieke element, een synchronisatiemechanisme en een softwarepakket dat het model/de virtuele representatie uitvoert (meestal afgeleid van CAE/multiphysics-software). Het creëren van een digitale tweeling vereist dat elementen die van belang zijn voor de OME nauwkeurig worden gerepliceerd in de virtuele representatie. Voor productieapparatuur omvat dit doorgaans de definitie van proces- of mechatronische systemen, inclusief motoren, actuatoren en instrumentatie, die zijn aangesloten op een automatiseringssysteem met applicatiespecifieke software.
De waarde van de implementatie van digitale tweelingen in productieapparatuur ligt in de mogelijkheid om de toestand van het fysieke systeem te schatten, verder dan wat direct waarneembaar is. Typische toepassingen hiervan zijn soft-sensing, adaptieve foutcorrectie, model-predictieve besturing en predictief onderhoud. Productieapparatuur kan worden opgenomen in een grotere digitale tweeling van een volledig productieproces ter ondersteuning van vraaggestuurde, tijdige productie.
Bij virtuele inbedrijfstellingstoepassingen is een digitale tweeling mogelijk niet mogelijk, omdat de fysieke apparatuur mogelijk niet bestaat. In plaats daarvan wordt een model van de productieapparatuur naast het besturingssysteem geïmplementeerd, zodat beide systemen samen kunnen worden ontwikkeld. Het besturingssysteem beschouwt het model van de productieapparatuur als een emulatie, omdat het besturingssysteem op natuurlijke wijze met het model kan communiceren via opdrachtuitvoer en statusfeedback (ook wel Hardware-In-the-Loop genoemd). Om deze techniek succesvol te laten zijn, moet het model van de productieapparatuur het concrete gedrag van het fysieke systeem nauwkeurig weergeven.
Emulatiegebaseerde virtuele inbedrijfstelling leidt tot een waardevolle vermindering van projectrisico's vanuit het perspectief van foutpreventie en het behalen van projectplanning. Omdat scenario's en ontwerpkeuzes grondig kunnen worden getest zonder fysieke apparatuur, kunnen engineers verschillende systeemelementen testen en verifiëren, waaronder applicatiespecifieke softwaremodules, receptconfiguratie, faalmodi en herstel, en de effectiviteit van de gebruikersinterface, zonder afhankelijk te zijn van geplande testapparatuur of aanwezigheid op locatie. Hierdoor worden projecten die gebruikmaken van virtuele inbedrijfstelling vaak uitgevoerd met minder tijd voor fysieke inbedrijfstelling en zijn ze over het algemeen veiliger voor mens en materieel.
Zodra de apparatuur in gebruik is genomen en gevalideerd, kan de emulatie van de virtuele ingebruikname worden voortgezet als een digitale tweeling die gesynchroniseerd is met de fysieke apparatuur. Omdat het model al is opgesteld, is het direct bruikbaar als een geïdealiseerde weergave van het fysieke systeem. Ingenieurs kunnen deze digitale tweeling gebruiken om onder andere het ontwerp van faciliteiten, systemen, productielijnactiviteiten en de eisen van installaties en machines te optimaliseren.
Infrastructuur-als-code
Vanuit het oogpunt van IT/OT-convergentie maakt virtuele inbedrijfstelling het mogelijk om flexibele IT-concepten in te zetten voor de ontwikkeling van processen zoals infrastructuur-als-code in de OT-ruimte. Het doel hiervan is om richting de automatisering van codeontwikkeling en infrastructuurconfiguratie te gaan.
De invoering van deze IT-concepten zal de workflows van OT-engineers fundamenteel veranderen. In plaats van systemen en code vanaf nul te bouwen, zoals het geval was met oudere gedistribueerde besturingssystemen (DCS), zal het proces veel meer lijken op een agile softwareontwikkelingsrol, waarbij engineers zich meer richten op het onderhouden van de geautomatiseerde softwaresystemen dan op het ontwikkelen van de applicatiecode en -infrastructuur. Voor eindgebruikers zou dit kunnen betekenen dat de lastige taken van het installeren, configureren en patchen van infrastructuur voor besturingssystemen een geautomatiseerde workflow worden. Voor machinebouwers zou dit kunnen resulteren in een orderverwerkingssysteem dat een configuratie verstuurt om dynamisch automatiseringsinfrastructuur en applicatiecode te bouwen op basis van de door de klant geselecteerde opties, zonder dat er een engineer bij betrokken is.
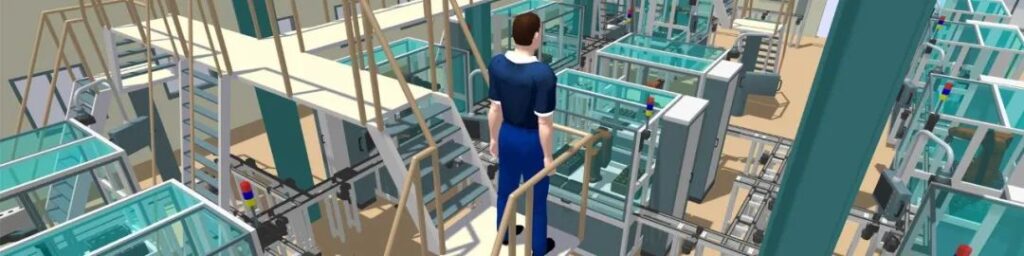
Orkestratie van OEM-apparatuur
OEM-apparatuur vormt de basis van moderne modulaire farmaceutische productiefaciliteiten door de flexibiliteit te bieden om de beste apparatuuroplossingen voor specifieke processen te kiezen en te combineren. Het in bedrijf stellen en valideren van OEM-apparatuur verloopt over het algemeen sneller, omdat fabrikanten voorgemonteerde, speciaal geprogrammeerde units ontvangen. Bovendien leveren OEM's apparatuur doorgaans in een validatieklare staat, waardoor het eenvoudig is om de apparatuur te kwalificeren voor gebruik in CGMP-faciliteiten. Er is geen noodzaak om te vertrouwen op interne resources of externe partijen voor de constructie van apparatuur en de ontwikkeling van applicatiecode. Verschillende connectiviteitsstandaarden en interfaces tussen verschillende apparatuurleveranciers kunnen echter uitdagingen opleveren, waardoor het moeilijk is om meerdere apparaten in één uniform besturingssysteem te integreren. Dit is waar OEM-apparatuurorkestratie om de hoek komt kijken.
De noodzaak van een orkestratiestrategie
Zonder een strategische aanpak en duidelijke specificaties leidt het gebruik van OEM-apparatuur tot gefragmenteerde automatiseringseilanden. Dit gebrek aan strategie is meestal te wijten aan late samenwerking met apparatuurleveranciers door de eindgebruiker. Wanneer automatisering niet wordt overwogen in het initiële aanschafproces van apparatuur, worstelen engineers vaak met de integratie van apparatuur of vertrouwen ze op ingenieursbureaus om de integratie af te handelen. Dit proces van het achteraf samenstellen van apparatuur in een laat stadium kan in het beste geval leiden tot beperkte interfacemogelijkheden binnen de fabriek. In het slechtste geval kan het hele proces averechts werken doordat het tijdrovend en kostbaar is en de digitale volwassenheid niet toeneemt.
Om deze problemen op te lossen, kunnen farmaceutische fabrikanten een holistisch plan voor de orkestratie van OEM-apparatuur hanteren om verschillende componenten te automatiseren en te coördineren, zodat ze al vroeg in de specificatie- en ontwerpfase van de faciliteit naadloos samenwerken. Door uitgebreide standaarden vast te stellen voordat apparatuur wordt aangeschaft, kan een eindgebruiker samenwerken met de leveranciers van de apparatuur. Dit geeft de OEM de mogelijkheid om zich te onderscheiden met betrekking tot hoe hun apparatuur past in een uniform automatiseringsplatform. Voor de eindgebruiker vereenvoudigt dit cross-training en standaardiseert het interfaces, waarschuwingssystemen, diagnostiek en receptbeheer. Dit verlaagt de kosten, stroomlijnt de bedrijfsvoering en resulteert in een snellere bouw, inbedrijfstelling en kwalificatie van de faciliteit.
Gebruikmaken van gestandaardiseerde interfaces
Eindgebruikers eisen OEM-apparatuur met plug-and-produce-functionaliteit die kan worden geïntegreerd met elk gedistribueerd besturingssysteem (DCS) of Supervisory Control and Data Acquisition (SCADA)-systeem. Deze plug-and-produce-functionaliteit standaardiseert kernautomatiseringsdiensten zoals apparatuurinterfaces en receptbeheer, gebruikersinterfaceschermen, audit trails en alarmbeheer voor verschillende apparaten. Een plug-and-produce-standaard verbindt al deze elementen systematisch en coördineert ze met behulp van gestandaardiseerde interfaces, zoals het NAMUR Module Type Package (MTP) en moderne protocollen, zoals OPC Unified Architecture (OPCUA). De integratie van al deze verschillende platformen zorgt voor consistentie, bespaart tijd en moeite bij de integratie en maakt plug-and-produce een haalbare technologie voor faciliteiten van de toekomst.
Deze technologieën moeten worden gezien als een aanvulling op een samenhangende strategie voor OEM-orkestratie, in plaats van al het werk te vervangen door samenwerking tussen organisaties en uitgebreide specificaties. Er bestaat geen magische knop om apparatuur naadloos te integreren en gemeenschappelijke sets van diensten te leveren, en de constructieve relaties van de eindgebruiker met hun apparatuur en technologieleveranciers spelen een belangrijke rol in een effectieve OEM-orkestratiestrategie. Denk eens aan deze situatie: een fabriek die volledig is opgebouwd uit black-boxapparatuur met een gestandaardiseerde interface is misschien snel te integreren, maar zou voor een eindgebruiker moeilijk en kostbaar zijn om op de lange termijn te ondersteunen vanwege het beheer van talloze supportcontracten, uiteenlopende reserveonderdelen en een gebrek aan consistentie in, of zelfs toegang tot, applicatiesoftware op de OEM-apparatuur.
Een veelvoud aan voordelen
Simpel gezegd, de orkestratie van OEM-apparatuur vergemakkelijkt het creëren van een uniform automatiseringsplatform voor een faciliteit. Dit leidt uiteindelijk tot een snellere time-to-market en lagere totale eigendomskosten voor de eindgebruiker. Effectieve orkestratie maakt de integratie van verschillende OEM-componenten mogelijk op een manier die eenvoudige aanpassing en schaalbaarheid mogelijk maakt, de toevoeging van nieuwe apparatuur aan bestaande systemen en naadloze integratie van toekomstige upgrades en uitbreidingen. Downtime en Mean Time To Repair (MTTR) worden verminderd door vereenvoudigde probleemoplossing en onderhoud.
Geneesmiddelen voor geavanceerde therapie
Een andere opkomende trend met betrekking tot facility engineering is de verandering van industriële automatisering om te passen in de markt voor geavanceerde therapeutische geneesmiddelen (ATMP's). Veel van deze therapieën zijn autoloog, wat betekent dat ze van één persoon afkomstig zijn en vervolgens aan diezelfde persoon worden teruggekoppeld. De productievolumes voor deze autologe therapieën zijn zeer klein, vaak in milliliters. Bestaande automatiseringssystemen zijn ontworpen om op grotere schaal te produceren, dus het concept hier is om de automatiseringstechnologieën te miniaturiseren zodat ze op benchtop-units of instrumenten kunnen draaien. Deze benchtop-units kunnen vervolgens worden georkestreerd tot een gecoördineerde procestrein om de therapie te produceren, waarbij het proces kan worden opgeschaald om meer procestreinen voor meer individuele patiënten mogelijk te maken.
De sleutel tot succes van deze strategie ligt in de bereidheid van de automatiseringsleverancier om zijn technologie te verkleinen en dezelfde commerciële, kant-en-klare software- en hardwaremogelijkheden te bieden voor benchtop-apparatuur. Dit is essentieel om de hoeveelheid nabewerking te beperken die nodig is voor de technologieoverdracht van de procesontwikkelingsafdeling (PD) naar cGMP-productie voor deze geavanceerde therapieën. Samenwerking met een automatiseringsleverancier die kan verkleinen en flexibel kan opereren in deze uiteenlopende reeksen industriële en laboratoriumapparatuur om de nauwkeurigheid en patiëntveiligheid te garanderen, is cruciaal.
Van begin tot eind
Farmaceutische bedrijven implementeren actief technologieën om de productiviteit, efficiëntie en het rendement op investeringen te verbeteren en hun concurrentievoordeel te behouden. Initiatieven zoals virtuele inbedrijfstelling en OEM-apparatuurorkestratie worden omarmd om de introductie van nieuwe capaciteit en mogelijkheden te versnellen en de bedrijfsvoering te optimaliseren om uiteindelijk een adaptieve faciliteit te bereiken.
Met behulp van virtuele inbedrijfstelling kunnen faciliteiten worden ontworpen, gemodelleerd, ontwikkeld en getest voordat de fysieke werkzaamheden beginnen. Deze aanpak maakt optimalisatie van verschillende aspecten mogelijk, zoals lay-out, productiviteit, doorvoer, flow en energie-efficiëntie. De orkestratie van OEM-apparatuur automatiseert processen en standaardiseert interfaces, wat het creëren van een uniform automatiseringsplatform voor een faciliteit vergemakkelijkt, wat uiteindelijk leidt tot een snellere time-to-market en lagere totale eigendomskosten voor de eindgebruiker.
Farmaceutische bedrijven die de kracht van nieuwe technologieën benutten, zijn beter toegerust om hun facilitaire processen te optimaliseren, van begin tot eind.
Conclusie
Virtuele inbedrijfstelling staat voorop in de technologische vooruitgang in automatisering en biedt een transformatieve aanpak voor sectoren die automatiseringsoplossingen effectiever willen integreren. Door gebruik te maken van simulatietechnologie stelt virtuele inbedrijfstelling bedrijven in staat om automatiseringssystemen in een digitale omgeving te ontwerpen, testen en verfijnen vóór de fysieke implementatie. Dit proces verbetert niet alleen de efficiëntie en veiligheid, maar bevordert ook een betere samenwerking en aanpassingsvermogen van teams aan veranderingen, waardoor een volledig inzicht in de mogelijkheden en beperkingen van de oplossing wordt gegarandeerd.
Het onderscheid tussen virtuele en traditionele inbedrijfstelling onderstreept de vooruitgang en efficiëntie die digitale simulaties opleveren. Virtuele inbedrijfstelling minimaliseert de noodzaak van uitgebreide activiteiten op locatie, vermindert de risico's die gepaard gaan met fysieke tests en versnelt het implementatieproces, waardoor het een cruciale strategie is voor industrieën die automatiseringstechnologieën willen implementeren.
Met de toenemende integratie van digitale tools in de productie en de voortdurende evolutie van simulatiesoftware, staat virtuele inbedrijfstelling op het punt een integraal onderdeel van automatiseringsprojecten te worden. Het doorbreekt barrières voor de implementatie van automatisering door risico's te beperken en downtime te verminderen, en democratiseert zo de toegang tot geavanceerde productietechnologieën.
Nu industrieën de uitdagingen van de implementatie van nieuwe technologieën blijven trotseren, kan de rol van virtuele inbedrijfstelling bij het faciliteren van een soepelere, veiligere en kosteneffectievere integratie van automatiseringsoplossingen niet genoeg worden benadrukt. Het is een bewijs van de kracht van digitale transformatie in de maakindustrie en biedt een blik op een toekomst waarin virtuele en fysieke domeinen samenkomen om productieprocessen te optimaliseren en innovatie te stimuleren.
Bedankt dat Alex Owen-Hill en John Hatzis dit idee deelden.