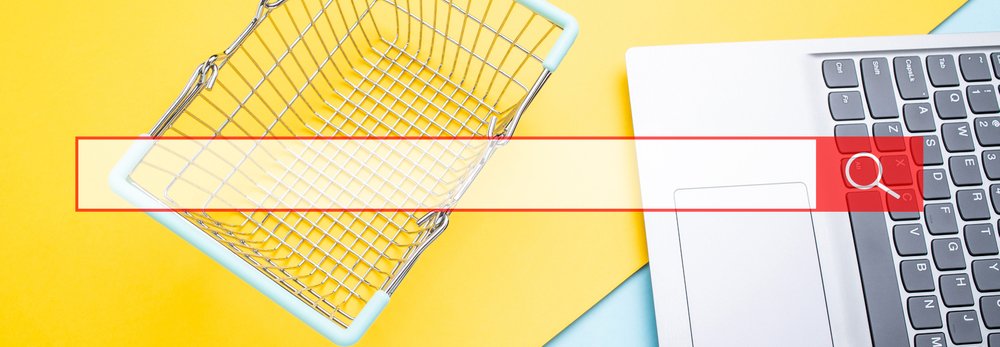
Samenvatting: De volautomatische krimpverpakkingsmachine is een sterk geautomatiseerd apparaat dat veel wordt gebruikt in sectoren zoals de farmaceutische industrie, de voedingsmiddelen- en drankenindustrie en de huishoudelijke chemicaliënindustrie. Krimpverpakkingen kunnen het materiaalgebruik en de arbeidskosten die gepaard gaan met doosverpakkingen aanzienlijk verminderen, waardoor ze economisch gezien belangrijk en essentieel zijn voor het diagnosticeren van storingen.
Trefwoorden: automatische verpakkingsmachine, werkingsprincipe, foutdiagnose
Automatisering in de verpakkingsindustrie verandert de manier waarop verpakkingsprocessen worden uitgevoerd, inclusief het verplaatsen van verpakkingscontainers en de verwerking van verpakkingsmaterialen. Het ontwerp en de installatie van geautomatiseerde, gecontroleerde verpakkingssystemen spelen een belangrijke rol bij het verbeteren van de productkwaliteit en de productie-efficiëntie, het elimineren van verwerkingsfouten en het verminderen van de arbeidsintensiteit. De volautomatische krimpfoliemachine is een sterk geautomatiseerd apparaat met een automatisch gecontroleerd verpakkingssysteem, dat de productie-efficiëntie en productkwaliteit aanzienlijk verbetert. Dit is met name belangrijk in sectoren zoals de voedingsmiddelen-, dranken-, farmaceutische en elektronica-industrie. Krimpfolieverpakkingen kunnen het materiaalgebruik en de arbeidskosten die gepaard gaan met doosverpakkingen aanzienlijk verminderen, waardoor ze economisch gezien van groot belang zijn.
Belangrijkste componenten en werkingsprincipes van verpakkingsmachines
Een volledig geautomatiseerde structurele oplossing bestaat uit verschillende componenten, waaronder eindarmmanipulatoren, materiaalverwerkingsapparatuur en identificatie- en verificatiesystemen. De werkingsprincipes zijn als volgt:
Eindarmmanipulatoren
Dit zijn apparaten die aan het uiteinde van een mechanische arm zijn bevestigd en van de ene naar de andere positie bewegen. Eindarmmanipulatoren worden gebruikt voor het grijpen van producten, het bepalen van de richting en het meten van prestatieparameters. Ze kunnen worden uitgevoerd als vacuümbekers met één type, vacuümbekers met meerdere typen of een combinatie van klemklauwen. In verpakkingstoepassingen worden eindarmmanipulatoren meestal ontworpen voor gebruik met vacuümbekers, klemklauwen of een combinatie van beide.
Materiaalbehandelingsapparaten
Materiaalverwerkings- en transportapparatuur zijn apparatuurtypen die nodig zijn voor het transport, de opslag en de controle van producten tijdens transmissie- en productieprocessen. Deze omvatten elektrische transportbanden, monorailkranen, automatisch geleide voertuigen en mechanische armen. Een typisch materiaalverwerkingssysteem omvat een invoerband, etiketteermachines, barcodelezers, automaten en uitvoerbanden. Een gebruiksvriendelijke grafische interface biedt een eenvoudig te bedienen platform voor het weergeven van palletstapeling. Afhankelijk van het aantal gecontroleerde productie-eenheden grijpt, verplaatst en plaatst (stapelt) de mechanische arm elke verpakkingscontainer (doos, krat, vat, blik, enz.) op de juiste palletpositie. Factoren waarmee rekening moet worden gehouden tijdens materiaalverwerking en -transport in het verpakkingsproces zijn onder andere de vorm, het gewicht en de materiaaleigenschappen van het product, de transportsnelheid, -afstand en -richting, het vereiste controleniveau bij aansluiting op andere apparatuur en de flexibiliteit voor het opnieuw vormen van componenten, indien nodig.
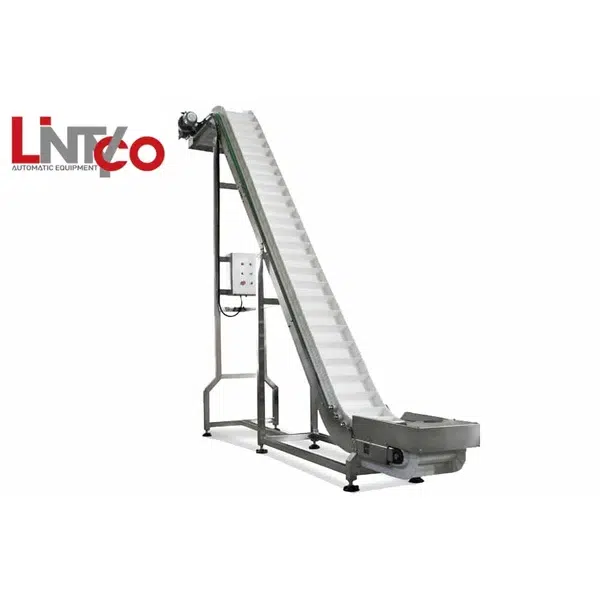
Identificatie- en verificatiesystemen
Het vermogen om producten te identificeren, verifiëren en nauwkeurig te volgen is een essentieel onderdeel geworden van het gehele verpakkingssysteem. Identificatiemethoden kunnen gebruikmaken van traditionele barcodes of radiofrequentie (RF)-sensoren, die pallets of individuele producten kunnen volgen. Een typische visuele barcodedetectiefunctie kan bevestigen dat elke barcode overeenkomt met elk product. Barcodescanners en videoherkenningssystemen registreren en verifiëren daarom productlabels om volledige identificatie te garanderen. Online barcodeprinting en -verificatie zijn ook noodzakelijk. Visuele technologie, die effectieve en betrouwbare middelen biedt om de productkwaliteit te garanderen, kan worden gebruikt in verschillende verpakkingsscenario's, zoals productinspectie en -oriëntatie, vulniveau en telling, optische etikettering, tekstherkenning, verificatie van labelkopieën, labelregistratie en algemene tekst- en grafische verificatie (buiten de productielijn). Barcodesystemen identificeren producten op basis van producttype, datum- en netnummers en fabrikantnamen tijdens prepress- of inline-drukprocessen.
Diagnose en probleemoplossing van veelvoorkomende fouten
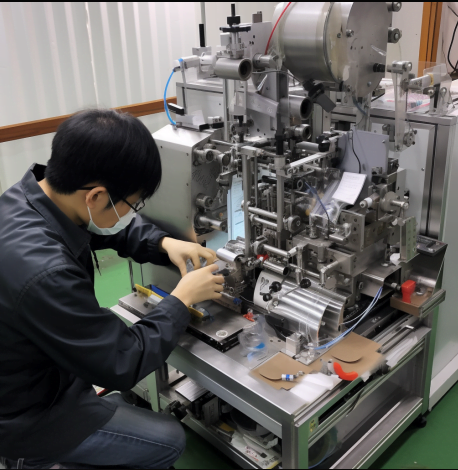
Materiaalbreuk
Deze storing wordt vaak veroorzaakt door de verbindingen van het verpakkingsmateriaal, overmatige bramen, defecte circuits van de papiertoevoermotor of slechte contactpunten met de naderingsschakelaar van de papiertoevoer.
Probleemoplossing:
(1) Verwijder defecte verpakkingsmaterialen.
(2) Controleer het motorcircuit van de papiertoevoer.
(3) Vervang de naderingsschakelaar.
Onvoldoende zakafdichting
Deze fout wordt vaak veroorzaakt door ongelijke binnenlagen van verpakkingsmateriaal, ongelijkmatige sealdruk of een lage sealtemperatuur.
Probleemoplossing:
(1) Verwijder defecte verpakkingsmaterialen.
(2) Pas de afdichtingsdruk aan.
(3) Verhoog de warmteafdichtingstemperatuur.
Onjuist afdichtingspad
Deze fout wordt vaak veroorzaakt doordat de heatsealer verkeerd is geplaatst.
Probleemoplossing: Pas de positie van de warmtesealer aan.
Onjuiste snijpositie van de zak of grote afwijking van de kleurmarkering
Oorzaak: Verkeerde positionering van de foto-elektrische schakelaar (sensor).
Probleemoplossing: Pas de positie van de foto-elektrische schakelaar (sensor) opnieuw aan.
Ongecontroleerde kleurmarkeringsuitlijning en foto-elektrische tracking
Deze storing wordt vaak veroorzaakt door naden of ruwe randen bij de verbindingen van verpakkingsmateriaal, vreemde voorwerpen in het vormtoestel waardoor het papier scheef komt, verpakkingsmateriaal dat uitsteekt van de geleidingsplaat van de foto-elektrische schakelaar, scheve uitlijning van het lichtpunt van de foto-elektrische schakelaar met de kleurmarkering, slechte gevoeligheid van de foto-elektrische schakelaar en onjuist gebruik van de helderheids- en donkerheidsinstellingen.
Probleemoplossing:
(1) Verwijder defecte verpakkingsmaterialen.
(2) Maak het vormtoestel schoon om een soepele papierbeweging te garanderen.
(3) Plaats het verpakkingsmateriaal in de geleideplaat.
(4) Pas de linker- en rechterpositie van de geleideplaat aan om de lichtvlek uit te lijnen met het kleurmerk.
(5) Vervang de foto-elektrische schakelaar en selecteer de juiste helderheids- en donkerheidsinstelling.
Afwijking van de grote zaklengte wanneer er geen kleurmarkeringsvolging wordt uitgevoerd (bijvoorbeeld wanneer de foto-elektrische schakelaar is uitgeschakeld)
Deze fout wordt vaak veroorzaakt door een verkeerde instelling van de taslengte, versleten wielpatronen waardoor er minder wrijving is en onvoldoende druk op de wielen.
Probleemoplossing:
(1) Verhoog de lengte-instelling van de tas zodat de werkelijke lengte van de tas gelijk is aan of iets langer is dan de standaardlengte van het kleurmerk.
(2) Vervang de wielen.
(3) Verhoog de druk op de wielen.
Onvolledig of gedeeltelijk snijden van de zak, wat resulteert in verbonden zakken
Deze fout wordt vaak veroorzaakt door onvoldoende druk tussen de twee snijbladen of door botte snijranden.
Probleemoplossing:
(1) Pas de druk tussen de snijbladen aan.
(2) Slijp of vervang de snijbladen.
De papiertoevoermotor draait niet of blijft draaien
Deze storing wordt vaak veroorzaakt doordat de papiertoevoerhendel vastzit, de naderingsschakelaar voor de papiertoevoer beschadigd is, een defecte opstartcondensator of een doorgebrande zekering.
Probleemoplossing:
(1) Los het probleem op dat de storing veroorzaakt.
(2) Vervang de naderingsschakelaar van de papiertoevoer.
(3) Vervang de opstartcondensator.
(4) Vervang de zekering.
Heatsealer warmt niet op of temperatuurregeling is verloren
Deze storing wordt vaak veroorzaakt door kapotte verwarmingselementen, storingen in het circuit, doorgebrande zekeringen, defecte temperatuurregelaars of onderbrekingen in het thermokoppel.
Probleemoplossing:
(1) Vervang de verwarmingselementen.
(2) Controleer het circuit.
(3) Vervang de zekering.
(4) Vervang de temperatuurregelaar.
(5) Vervang het thermokoppel.
Het niet kunnen trekken van de zak (de zaktrekmotor werkt niet)
Deze fout wordt vaak veroorzaakt door storingen in het circuit, schade aan de naderingsschakelaar voor het trekken van de zakken, storingen in de besturing van de automatische verpakkingsmachine of storingen in de aandrijving van de stappenmotor.
Probleemoplossing:
(1) Controleer het circuit en verhelp eventuele storingen.
(2) Vervang de naderingsschakelaar voor het trekken van de tas.
(3) Vervang de controller van de automatische verpakkingsmachine.
(4) Vervang de stappenmotordriver.
Conclusie
Om storingen in een automatische verpakkingsmachine snel op te lossen, is het essentieel om niet alleen de structuur en werkingsprincipes ervan te begrijpen, maar ook de grondoorzaken van de storingen te identificeren en een reeks probleemoplossingsmethoden te beheersen. Dit zorgt voor aanpassing aan verschillende situaties en maakt efficiënte storingsoplossing mogelijk. Aarzel niet om Neem contact met ons op als je er niet mee om kunt gaan
Lintyco is een pionier en leider in geautomatiseerde vulmachines En end-to-end verpakkingssystemenDe innovatieve verpakkingsoplossingen van Lintyco voor voedingsmiddelen, farmaceutische producten en andere toepassingen worden aangevuld met geavanceerde oplossingen voor secundaire verpakking, Inpakken & kartonneren, bulkverpakkingen en meer. Of u nu op zoek bent naar een nieuwe machine of een complete lijn, of gewoon uw huidige verpakkingsmachine wilt upgraden, neem contact op met Lintyco. Als experts in de branche met meer dan drie decennia aan bewezen expertise, biedt Lintyco de optimale oplossing, ondersteund door uitstekend advies en ondersteuning.