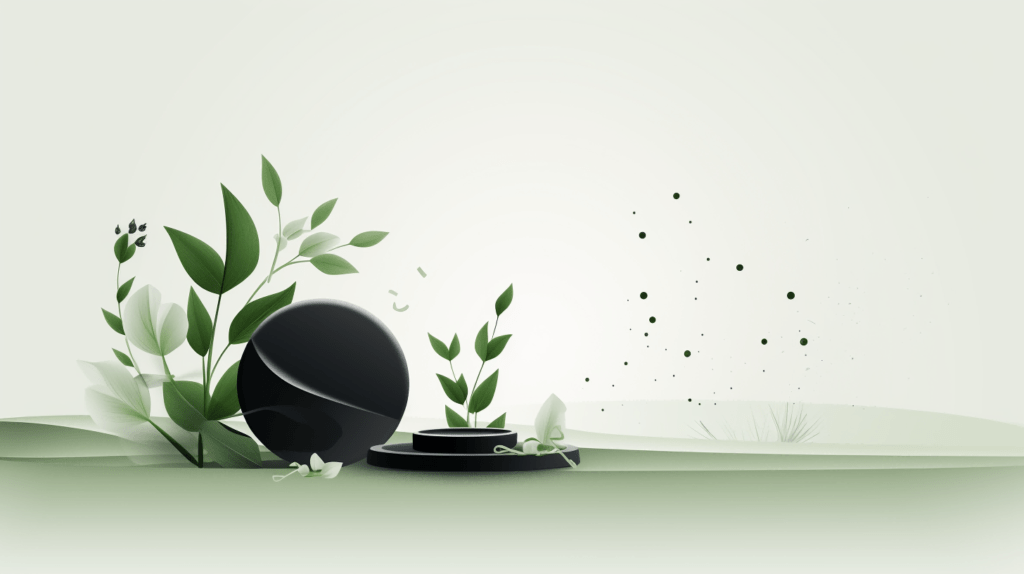
Follow Lintyco mechanical engineer with 20 years of experience, We will explain the types and benefits of a protein powder weighing and filling machine, how it works, and future trends. Let’s get started!
The nutritional supplement market has grown rapidly in recent years, especially in demand for easy-to-consume formats like protein powders. For a supplement brand to thrive, efficient manufacturing processes are key – and that includes high-quality packaging. Protein powder-filling machines help brands automate and speed up the process of putting powder in bags, pouches, and containers for final consumer sales.
Types of Protein Powder Bag Filling Machines
Different types of filling machines exist to suit the unique needs of protein powder brands.
Flow wrappers work by continuously wrapping premade bags around products passing on a conveyor belt. They excel at high speeds up to 150 products per minute, making them ideal for high-volume output. However, they offer limited customization.
Form fill seal machines form, fill, and seal products in a single process. They exhibit great flexibility in package sizes and designs while ensuring a sterile fill. Output rates range from 30 to 300 products per minute.
Vacuum pouch filling machines utilize air-tight pouch films that can be heat-sealed. They offer compact and lightweight packaging at a lower cost. Vacuum pouches can be filled using form fill seal or vertical fill machines.
Drum fillers fill premade multiwall bags or paper cartons. They feature simple, robust designs suitable for filling dusty products like protein powder. Output speed depends on fill quantity.
Auger fillers are ideal for free-flowing powders. An auger controls the fill quantity within a certain tolerance as the product flows into preformed bags that are then sealed.
Sachet machines vary in complexity but excel at producing small single-serve packs. They often integrate weighing, filling, and sealing in a single step.
Machine Type | Advantages | Disadvantages | Market Share(2022) | Price Range |
---|---|---|---|---|
Flow Wrappers | – High production speed for large-scale packaging | – Lower precision in powder filling | 18% | $10,000 – $50,000+ |
Form Fill Seal Machines | – Automation of packaging process without extra steps | – Adjusting and switching packaging sizes and shapes may take time and adjustments | 15% | $20,000 – $100,000+ |
Vacuum Pouches filling machine | – Provides oxidation and freshness protection | – Not suitable for loose protein powder | 20% | $5,000 – $30,000+ |
Drum Fillers | – Suitable for large-capacity packaging, ideal for industrial-scale production | – Less suitable for small packaging | 12% | $10,000 – $50,000+ |
Auger Fillers | – Offers high precision in powder filling | – Filling speed may be relatively slower | 20% | $5,000 – $30,000+ |
Sachet Machines | – Provides individual, portable packaging | – Less suitable for large-scale packaging | 22% | $2,000 – $10,000+ |
Please keep in mind that these price ranges are approximate and can vary. It’s recommended to contact suppliers or manufacturers for specific models and brands to get accurate pricing and more detailed information.
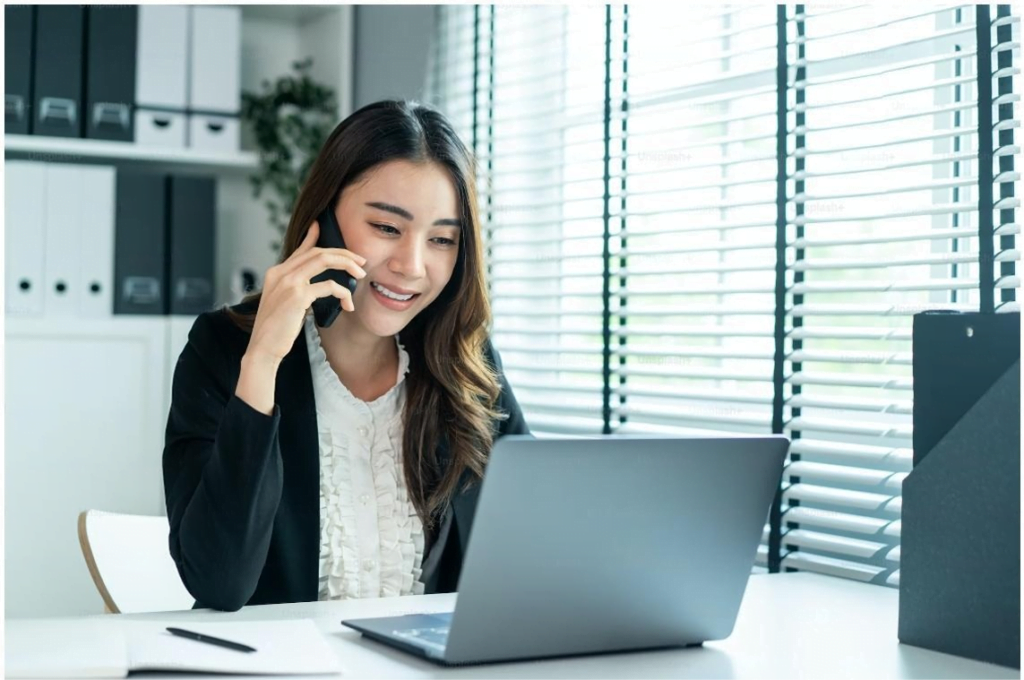
Benefits of Protein powder filling machines
Automated packing equipment brings numerous benefits:
Increased efficiency and output. Machines fill, weigh and seal at faster rates than manual labor, boosting production and reducing downtime.
Lower labour costs. Reduced reliance on manual packers lowers long-term costs, though initial investments may be higher.
Accuracy and consistency. Machines maintain precise fill weights within set tolerances, ensuring consistency batch to batch.
Contamination control. Automated lines minimize human contact with products, reducing risk of contamination.
Package customization. Some machines offer extensive flexibility in pouch sizes, bag designs, and product formats.
Extended shelf life. Properly filled and sealed packages help protect products and extend shelf life.
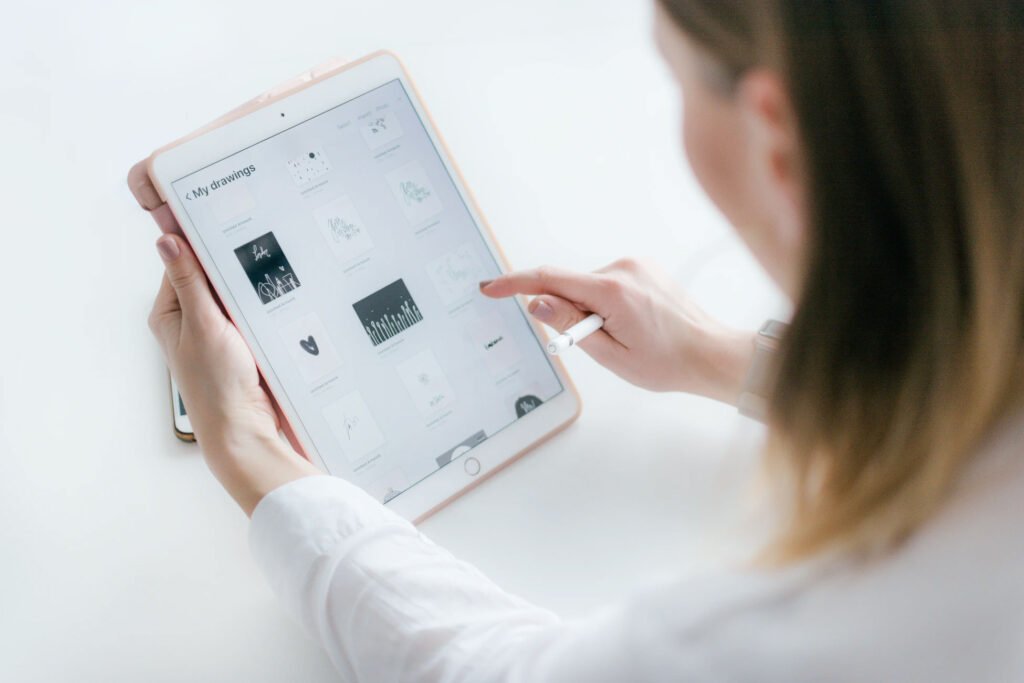
Essential maintenance tips for a protein powder filling machine
- Clean filters and screens regularly – This includes dust collectors, air filters, and any screens that collect powder buildup. Cleaning frequency depends on production volume but at least once a week is recommended.
- Lubricate moving parts – Lubricate wheels, chains, gears and other parts according to the manufacturer’s schedule. Use the recommended lubricants to avoid damaging parts.
- Check seal wires – For machines that use heat sealing, check the condition of seal wires regularly for wear and proper tension. Replace worn wires to maintain seal quality.
- Check bag alignment – Ensure bags and pouches are properly aligned on the machine before filling and sealing. Misalignment can cause fill errors and wasted product.
- Empty hoppers between runs – Empty powder buildup from hoppers, augers and chutes after each production run. This prevents clumping and bridging of powder that can affect fill consistency.
- Calibrate fill sensors – Fill sensors and weight monitoring equipment need periodic calibration to maintain accuracy. Follow the calibration schedule recommended by the manufacturer.
- Check bag integrity – Inspect filled bags after production runs to check for rips, leaks or other issues. This ensures your final product meets quality standards.
- Follow shutdown procedures – When powering down the machine for longer periods, follow manufacturer guidelines for draining parts, lubricating mechanisms and more. This prolongs the life of the equipment.
- Maintain spare parts inventory – Keep common spare parts like seals, sensors and screens on hand to minimize downtime due to part failures.
- Get professional servicing – Have a certified technician inspect and service the machine periodically or when unexpected issues arise. This helps catch potential problems before they cause major disruption.
With regular maintenance following the manufacturer’s guidelines, you can maximize the service life of your protein powder filling machine and maintain optimal performance. Be sure to train staff on proper maintenance and safety procedures to protect both the equipment and operators.
You can check maintenance here
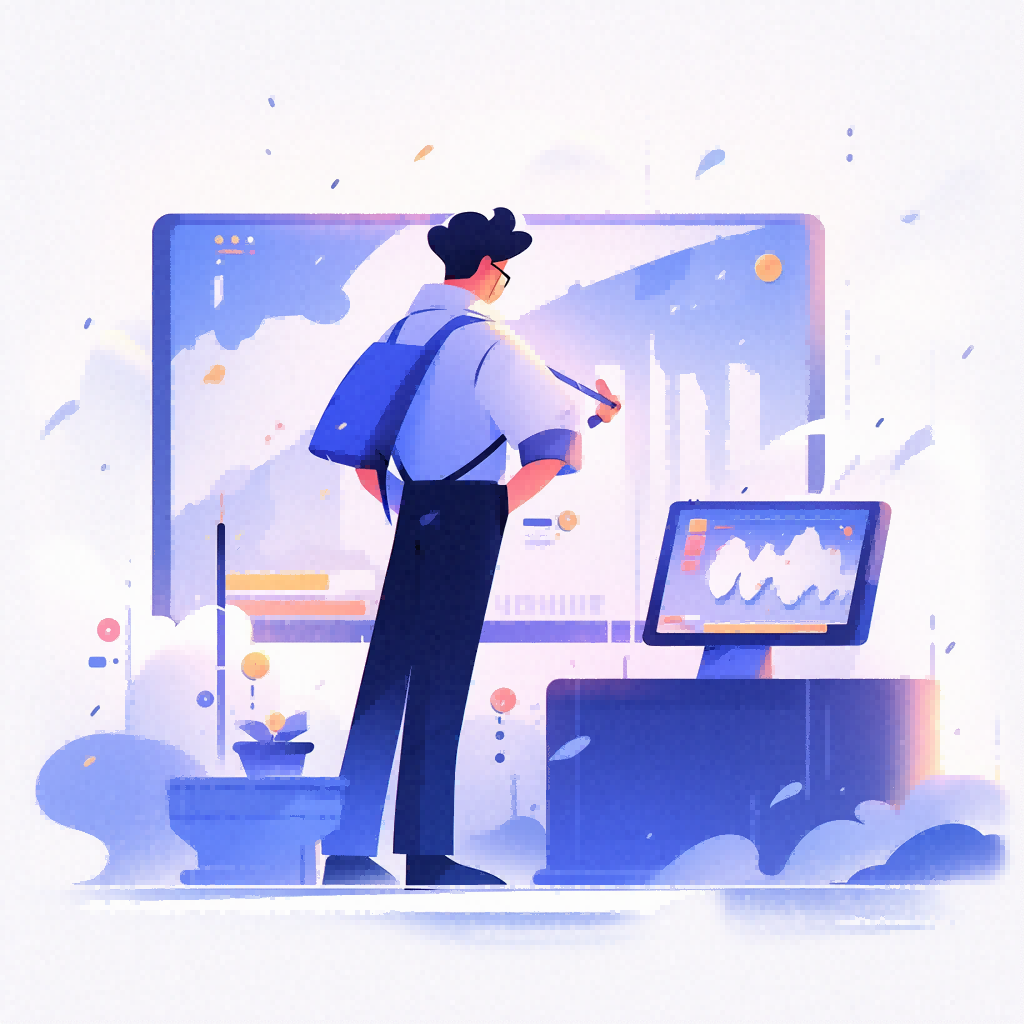
Ultimate Book to Choose the Right Protein powder filling machine
Factors to consider when selecting protein powder packing equipment:
Fill range. The range of fill weights the machine can accurately handle, from small to large.
Package options. Flexibility in bag sizes, pouch types, drum liners, cartons, and other formats.
Customization. Ability to modify package design elements like labels, material, and window panels.
Speed. Output rates measured in products per minute or hour depending on fill weight.
Costs. Purchase price and total cost of ownership including consumables, labor, and maintenance.
Maintenance. Ease of keeping the machine running and availability of parts and service support.
Different filling machines offer trade-offs between speed, versatility, and costs. Research brands’ offerings based on your priorities and production volumes. Test run demo units whenever possible to confirm machine performance meets your expectations.
How to Complete Packaging Line Integration
Integrating a protein powder filling machine into a complete packaging line can maximize efficiency and automation. Here are some key aspects of packaging line integration for protein powder brands:
Upstream conveying – Conveyor belts and lifts can feed bulk protein powder directly into the filling machine, reducing human handling. Screw, belt and pneumatic conveyors are common options.
Downstream conveying – Filled bags or pouches are then conveyed downstream to further packaging equipment using the same conveyor types. This provides a smooth transition between machines.
Labelling machines – Once packed, protein powder products typically require labeling. Inline labelers can be integrated to apply labels directly after filling to reduce manual labor.
Quality control systems – Checks like weight verifiers, leak detectors and x-ray inspection systems can be installed inline to catch any fill errors or defects immediately after packing.
Reject systems – Mechanisms that divert defective products away from the packaging line, either manually or automatically, help maintain quality control.
Control systems – PLC controllers or computer systems can be integrated to monitor and control the entire packaging line from a central point. They improve visibility and troubleshooting.
Line synchronization – Synchronizing equipment speeds and buffering between machines helps ensure a continuous flow of product through the packaging line with minimum delays or bottlenecks.
Validation systems – Integration of systems to validate fill weights, package integrity and label accuracy helps comply with FDA regulations and ensure product safety.
Automating these supporting processes around a filling machine can significantly improve packaging efficiency, consistency and compliance. However, integrating several pieces of equipment from different vendors also requires more system integration effort and validation. A holistic approach to line design is critical to maximize the benefits of packaging line integration.
With the right protein powder packaging solution, you can ensure consistent, high-quality products that represent your brand well – driving customer satisfaction and growth for your supplement business. Automated packers improve your fill rates, reduce costs, and free up resources for other value-adding tasks.
Lintyco is a pioneer and leader in automated Protein Powder Filling Machines and end-to-end packaging systems. Lintyco’s innovative packaging solutions for food, pharma, and other applications are complemented by advanced solutions for secondary packaging, wrapping & cartoning, bulk packaging, and more. Whether you are looking for a new machine or a complete line, or if you just want to upgrade your current packaging machine, talk to Lintyco. As experts of the industry with over three decades of proven expertise, Lintyco will provide the optimal solution backed by excellent consultancy and support.
FAQ
Q: What is a Protein Powder Weighing and Filling Machine?
A: It’s a specialized machine designed for accurately weighing and packaging protein powder in bulk, ensuring efficiency and reliability in the packaging process.
Q: How does this machine enhance packaging efficiency?
A: The machine automates the weighing and filling process, allowing for faster, more consistent, and accurate packaging of protein powder, thus improving overall efficiency.
Q: Can the machine handle different packaging sizes?
A: Generally, these machines are adaptable and can be calibrated to handle various sizes and types of packaging, depending on specific production needs.
Q: What industries benefit from using this type of machine?
A: The primary industry that benefits is the health and fitness supplement sector, especially businesses that produce and package protein powder.
Q: How does the machine ensure the reliability of packaging?
A: The machine typically features advanced technology for precise weighing and filling, quality control mechanisms, and robust construction for long-term reliability.