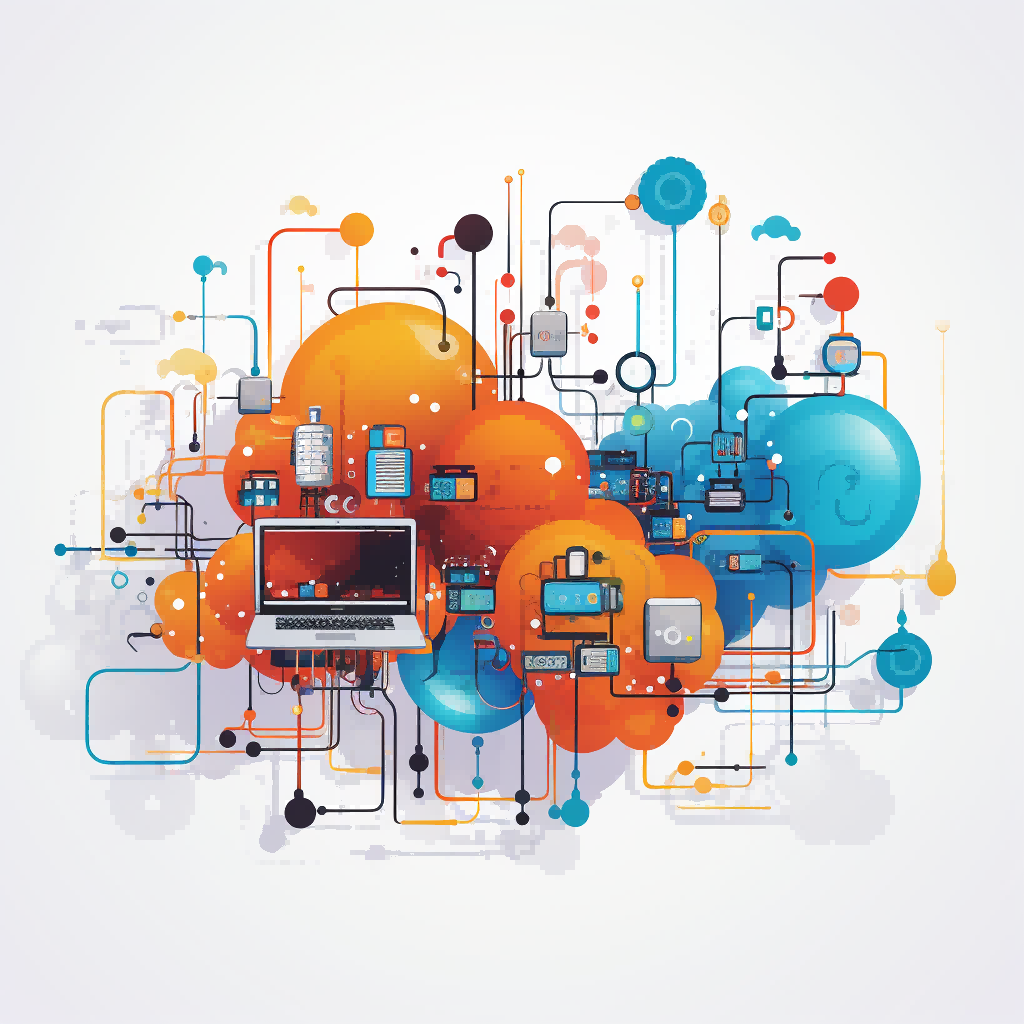
I have 20 years of experience as a mechanical engineer. I will explain the advantages of a sugar sachet packing machine, how it works, and future trends. Let’s get started!
Sugar sachet packing machines provide an efficient, accurate, hygienic, and cost-effective solution for commercial sugar sachet packaging needs. They play an important role in ensuring a reliable supply of single-serve sugar portions for the food service and hospitality sectors.
Benefits of using these machines
Convenience: They automate the laborious and time-consuming task of manually filling and sealing individual sugar sachets. This significantly improves production efficiency and output.
Accuracy: Small sugar packing machines can accurately weigh and fill the exact amount of sugar required into each sachet, ensuring consistency and reducing waste. This provides a better consumer experience.
Hygiene: The automatic filling and sealing process minimizes human contact, thereby reducing the risk of contamination and ensuring higher hygiene standards. This is important for food-grade packaging.
Cost savings: Sugar sachet packing machines enable mass production of sugar sachets at a lower cost per unit compared to manual packaging. This translates to cost savings for businesses.
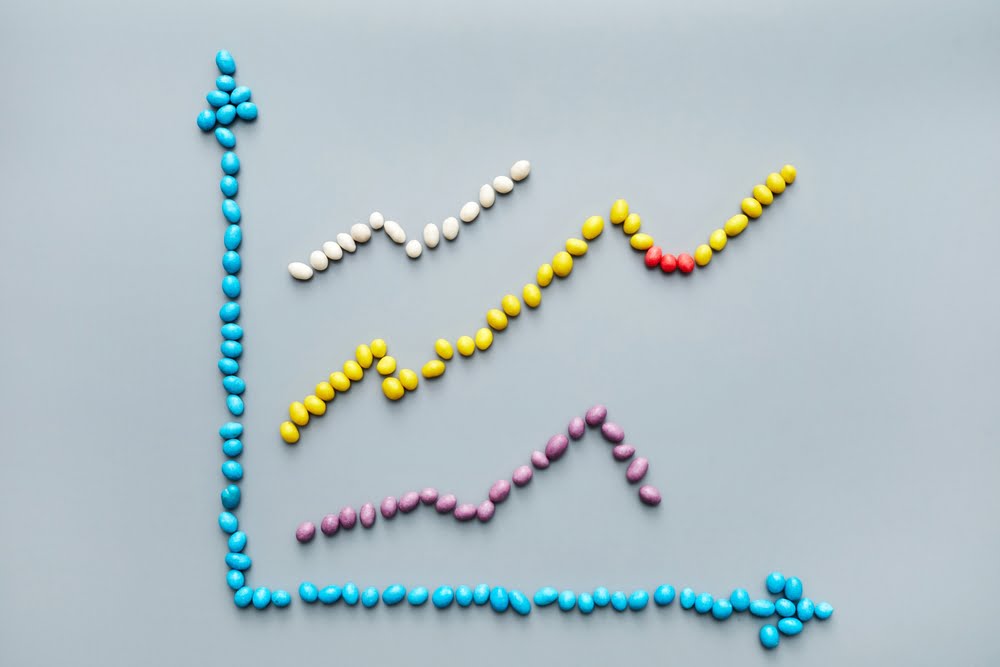
How Sugar Sachet Packing Machines Work
The key components of a sugar sachet packing machine are:
- A hopper or funnel to store the loose sugar.
- A weighing mechanism to accurately measure the amount of sugar required for each sachet. This is typically an electronic weighing scale connected to the machine.
- An automated feeding system that dispenses the measured amount of sugar into the sachets. This uses mechanisms like screw feeders, vibratory feeders, etc.
- Heat-sealing jaws and dies that seal the open end of the sachet after filling. The jaws apply heat and pressure to seal the sachet.
- A conveyor belt or chain system that moves the empty sachets into position for filling and then out after sealing.
- A control panel for the operator to input parameters like sugar quantity, speed of filling, etc.
The basic filling and sealing process works as follows:
- An empty sachet is placed on the conveyor and moved into the filling position.
- The weighing mechanism measures the required amount of sugar as per the set parameter.
- The feeding system dispenses the measured sugar into the open sachet in a few seconds using the automated mechanism.
- The sachet, now filled with the correct amount of sugar, is moved to the heat sealing section.
- The heat-sealing jaws apply heat and pressure to fuse the plastic material of the sachet and seal it shut, trapping the sugar inside.
- The sealed sachet then moves out of the machine via the conveyor.
- This process is repeated continuously to fill and seal a large number of sugar sachets with precision and consistency, demonstrating the benefits of automation provided by these machines.
Considerations for Choosing Sugar Sachet Packing Machines
Packaging speed – The speed at which the machine can fill and seal the sachets. Faster speeds mean higher output but reduced accuracy. Consider your production volume requirements.
Sachet size – The machine should be able to accommodate the size of sachets you need in terms of length, width and depth. Larger sachets typically require larger machines.
Accuracy – The ability of the machine to accurately weigh and fill the sugar in each sachet. Look for machines with high resolution electronic weighing scales and precise feeding mechanisms.
Ease of use – Simple operation and adjustment of the machine for maintenance and changeover between sachet sizes. Machines with automatic settings reduce manual errors.
Capacity – The total number of sachets the machine can fill in an hour based on the cycle time and production speed. Ensure it matches your needs.
Material Handling – The machine should be able to handle the material of your sugar sachets without issues. Poly seal materials are most common.
Maintenance – Ease of accessing parts for cleaning and repairs. Look for machines with detachable parts to reduce downtime during maintenance.
Spare parts availability – Ensure spare parts for the machine you choose will be easily available locally to avoid production disruptions.
Price – Of course, consider your budget but don’t compromise too much on critical factors like accuracy and speed.
Tricks and Hacks for Optimizing Sugar Sachet Packaging
- Use sachets made of material that seals easily and cleanly. Poly seal or laminated polyethene work best as they can be sealed quickly with heat. Avoid sticking or tearing issues.
- Keep the feeding system and weighing mechanism clean and well-lubricated to ensure accurate and jam-free filling of sugar. Conduct regular maintenance checks.
- Calibrate the weighing scale regularly to maintain the specified filling accuracy. Check and adjust the scale calibration as needed.
- Automate the insertion of empty sachets on the conveyor to speed up the packaging process. Look for machines with integrated sachet placement mechanisms.
- Install sensors to detect missing or faulty sachets to reduce waste. The machine can then stop the conveyor and alert operators.
- Adopt intelligent control systems that can self-adjust the filling quantity and rate based on real-time weighing data. This ensures consistent accuracy.
- Integrate check weighing systems that randomly weigh sealed sachets and detect underfilled or overfilled packs. Non-compliant packs can be rejected.
- Install air blowers to remove excess sugar from the sachet after filling. This helps achieve the accurate net fill weight and reduces giveaways.
- Consider auto-resetting or jogging controls that allow the machine to resume operation after faults without requiring a manual reset. This avoids production stops.
- Automate maintenance tasks using features like automatic lubrication systems and self-cleaning mechanisms. This minimizes downtime for maintenance.
Applications and Benefits of Sugar Sachet Packing Machines
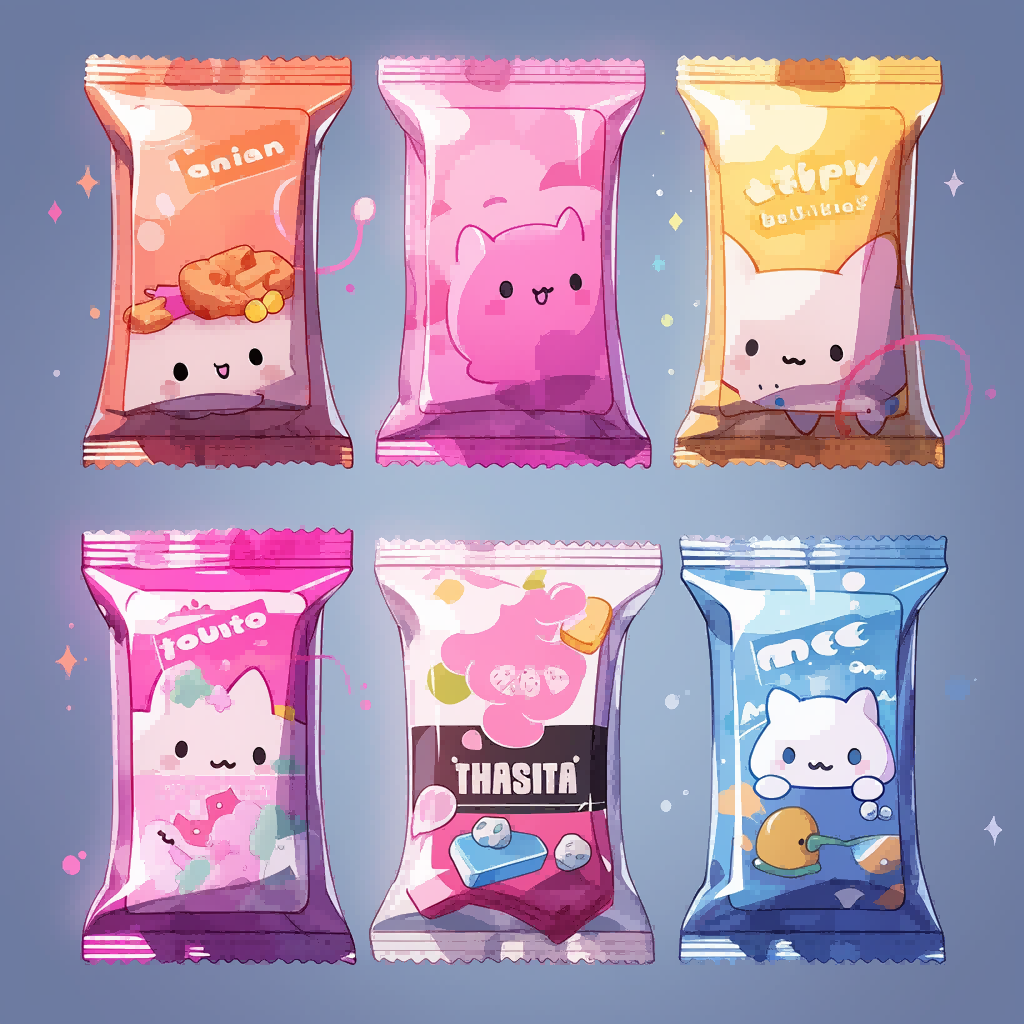
Application
- Hotels – Sugar sachets are commonly provided in hotel rooms for tea and coffee. Sugar sachet packing machines help produce these individual portion packs efficiently for large hotel chains.
- Cafes and restaurants – Many cafes and dine-in restaurants provide sugar sachets on tables for customers to add sugar to coffee and tea. These machines can produce the required number of sachets easily.
- Quick service restaurants – Fast food chains and takeaway joints also use sugar sachets for beverages. The machines ensure consistent filling and hygienic packaging at high speed.
- Retail – Pre-packaged sugar sachets are sold in retail stores for home use. Sugar sachet packing machines enable the commercial production of these retail sugar sachets.
Benefits:
Portion control – The machines can accurately fill and seal the precise amount of sugar required as a single-serve portion. This avoids over-sugaring of beverages and waste.
Convenience – Packaged sugar sachets provide convenience to customers who can simply tear and add the sugar to their cup, without using teaspoons.
Hygiene – The automated filling and sealing process minimizes human contact, thereby reducing the risk of contamination and ensuring hygienic sugar sachets.
Shelf life – Packaging sugar helps extend its shelf life by preventing the absorption of moisture from the air. This improves the storability and usability of unused sachets.
Cost savings – The machines provide a more economical solution for mass-producing sugar sachets compared to manual packaging methods. This translates to lower costs per sachet.
Future Trends in Sugar Sachet Packing Machines
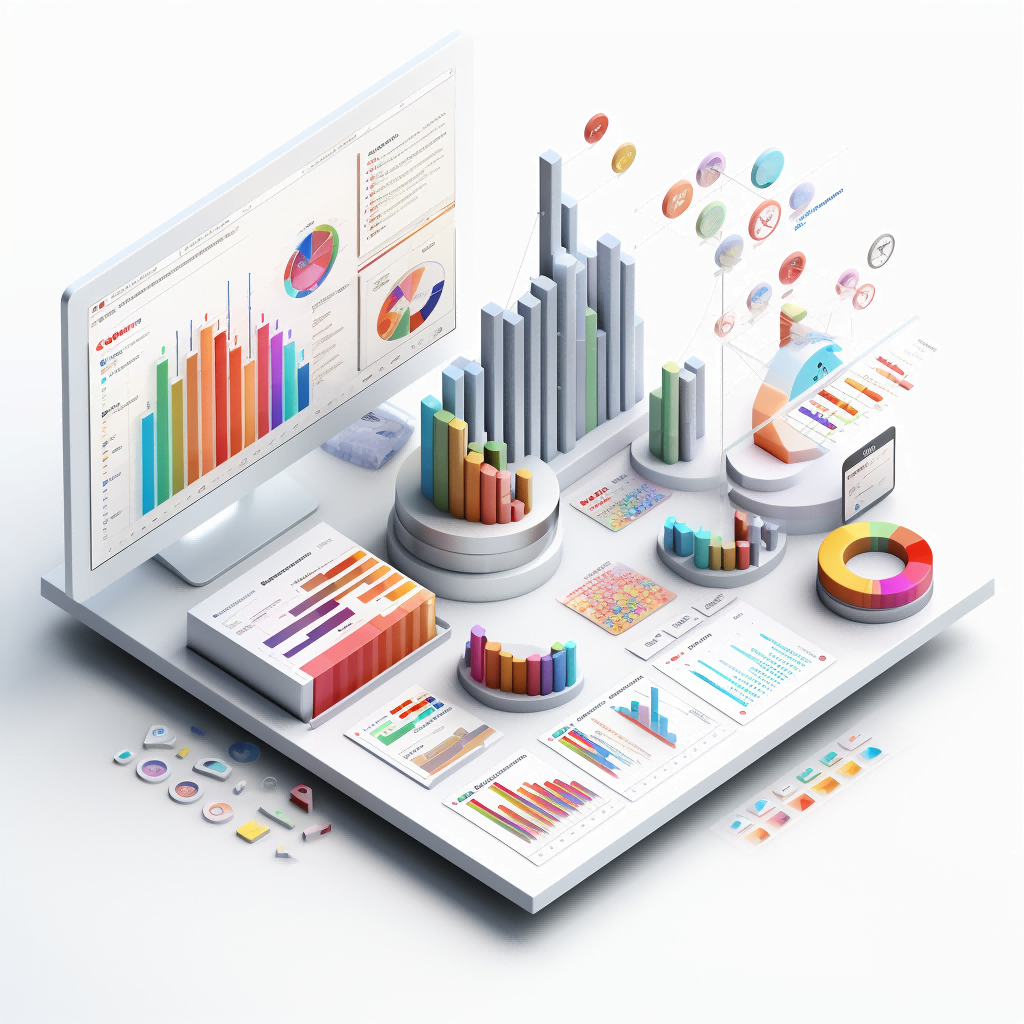
- Integration with the Internet of Things (IoT) – More machines will be connected to the Internet and offer remote monitoring capabilities. This allows real-time tracking of production data and remote assistance by service technicians.
- Sustainability focus – There will be a greater emphasis on reducing material waste and environmental impact through features like automatic detection and rejection of faulty sachets to minimize reject rates. Some machines may offer biodegradable packaging options.
• Advanced analytics and AI – Sugar sachet packing machines will increasingly use data analytics and artificial intelligence to optimize performance. Features like automatic calibration, variance detection and predictive maintenance will become common.
• Increased automation and customization – There will be a shift towards highly automated machines that require minimum human intervention during operation. More configurable options will also be available to customize the machines for specific needs.
- Enhanced food safety features – More machines will offer features to improve food safety and compliance with regulatory standards. This includes check weighing, metal detection, reject mechanisms for contaminated sachets and seamless traceability.
- Digital quality assurance – The use of digital technologies to improve quality assurance in sugar sachet packaging will increase. For example, using machine vision and image analysis to detect defects in sealed sachets.
- Adoption of innovative materials – Sugar sachet machines may support the use of novel materials like bioplastics, edible films and eco-friendly pouches to reduce the carbon footprint of packaging.
FAQ
Q: What are the advantages of sugar sachet packing machines?
A: They offer efficiency in production, precise filling, enhanced hygiene standards, and cost-effectiveness in commercial sugar sachet packaging.
Q: What considerations are important when choosing sugar sachet packing machines?
A: Consider packaging speed, sachet size compatibility, filling accuracy, ease of use, overall capacity, material handling capabilities, maintenance requirements, availability of spare parts, and budget.
Q: How do sugar sachet packing machines work?
A: They typically involve a hopper for sugar storage, an electronic weighing scale for measurement, an automated feeding system for dispensing, heat-sealing jaws for sealing sachets, and a conveyor belt for movement.
Conclusion
Sugar sachet packing machines play an important role in the food packaging industry by providing an automated solution for commercial sugar sachet production. Their benefits of convenience, consistency, hygiene and cost-effectiveness make them an invaluable resource for hospitality, food service and retail businesses that need individually packaged sugar portions.
I encourage readers to share their own experiences using or maintaining sugar sachet packing machines and explore further advancements and innovations in this field. With appropriate research and considerations, these machines can greatly improve sugar sachet packaging operations.
Lintyco is a pioneer and leader in automated Sugar Bagging Machines and end-to-end packaging systems. Lintyco’s innovative packaging solutions for food, pharma, and other applications are complemented by advanced solutions for secondary packaging, wrapping & cartoning, bulk packaging, and more. Whether you are looking for a new machine or a complete line, or if you just want to upgrade your current packaging machine, talk to Lintyco. As experts of the industry with over three decades of proven expertise, Lintyco will provide the optimal solution backed by excellent consultancy and support.