With the passing of time, liquid packaging machines have become an irreplaceable part of various industries, such as food and beverages, pharmaceuticals and personal care products. Liquid packaging machines are mainly divided into two types, flexible liquid packaging and rigid liquid packaging. The former is mainly packaged in bags, while the latter is mainly in bottles and jars. In the article that follows, you can learn about liquid packaging machine categories, maintenance methods and how to help you choose the practical packaging machine.
Types of Liquid Packaging Machinery
The most common types of liquid packaging solution are bottle filler machine, pouch filler machine and tube filler machine.
- Bottle filler machines are used to fill liquids into glass or plastic bottles at high speeds. They are commonly found in the beverage industry filling juices, waters, sodas and more.
- Pouch filler machines are designed to fill liquids into flexible pouches or bags. They are widely used for food products like soups, sauces and baby food.
- Tube filler machines are specialized machines that precisely fill liquids into tubes, typically for personal care products like toothpaste, lotions and shampoos.
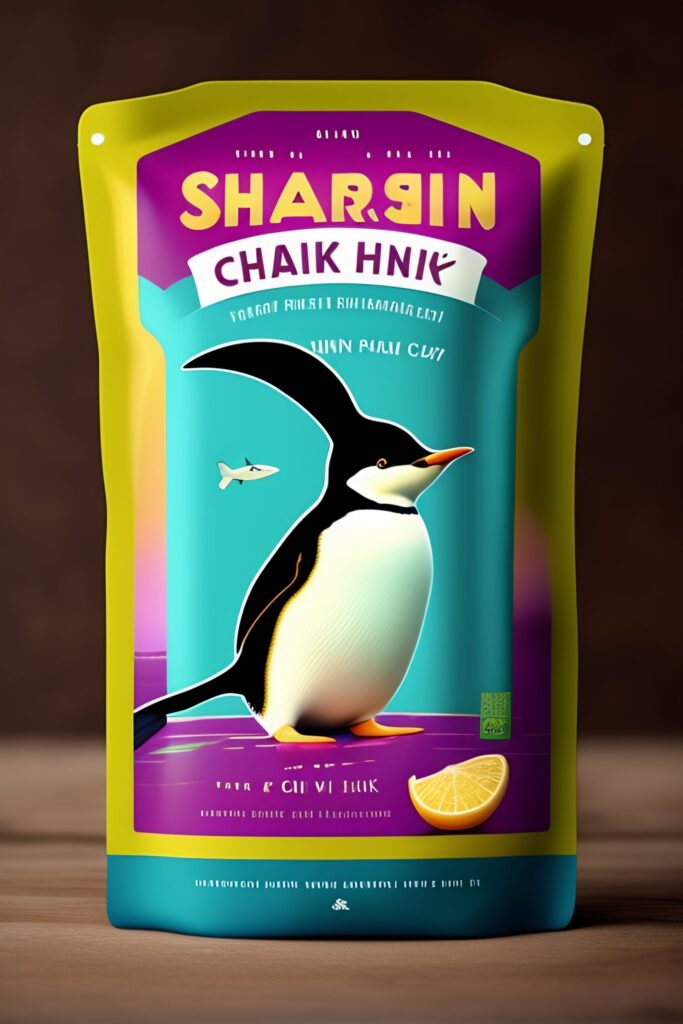
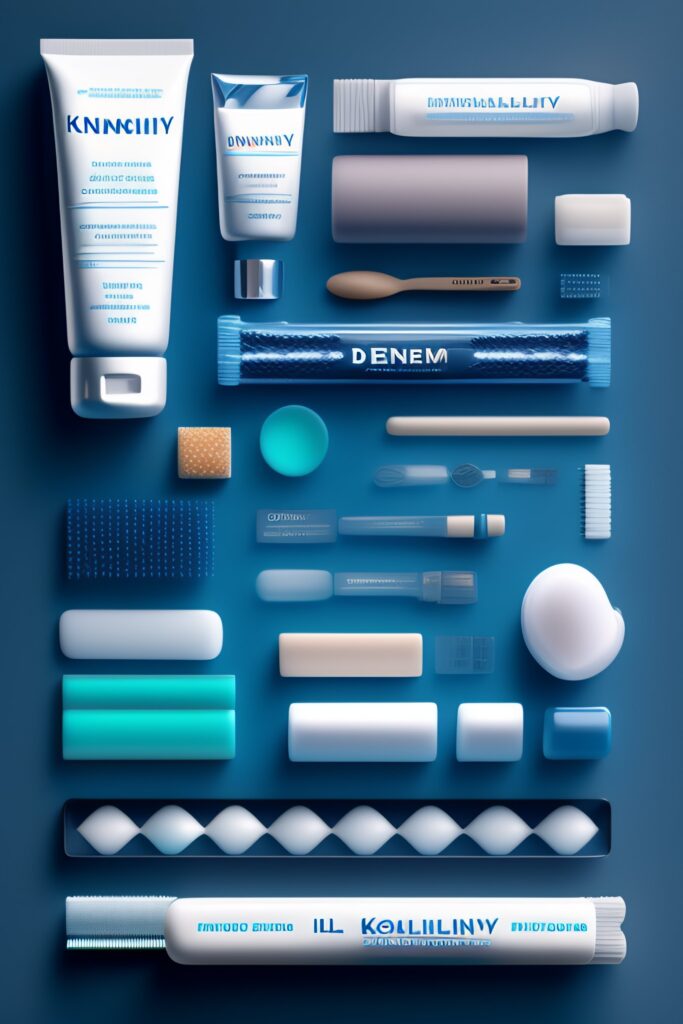
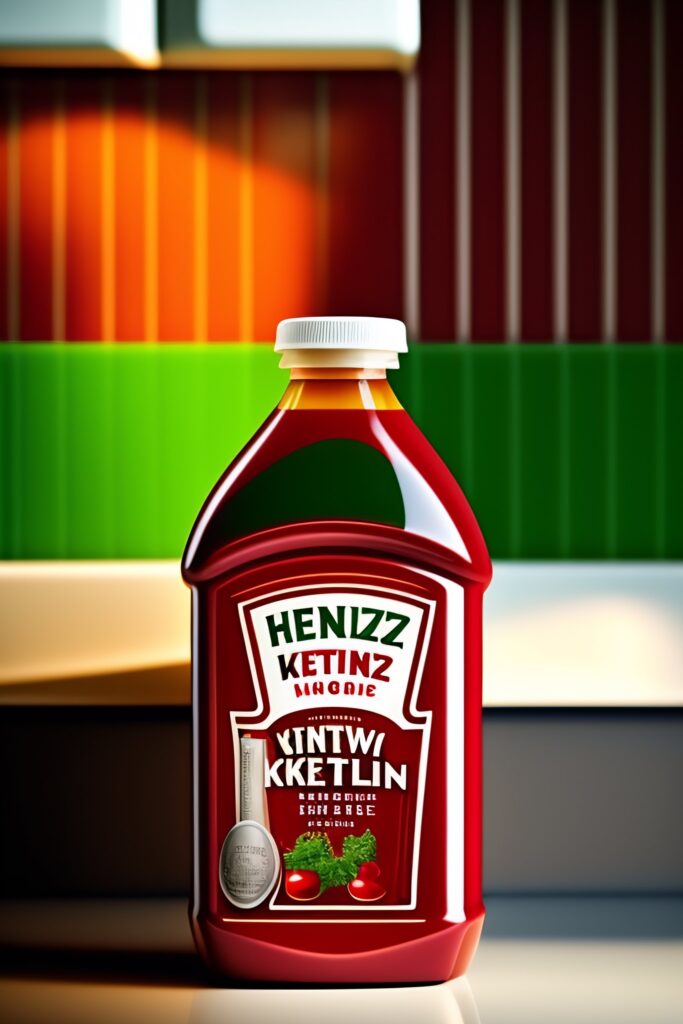
Key Features to Look for in Liquid Packaging Machinery
When evaluating liquid packaging machines, look for:
- High fill speeds: Measured in bottles/pouches per minute. Faster speeds mean higher productivity.
- Accuracy: Precision fills volume control to minimize product waste.
- Flexibility: Ability to handle different packaging types and fill volumes.
- Ease of use: Simple operation and interface to minimize training requirements.
The Role of Automation in Liquid Packaging
Automated liquid packaging machines offer many benefits like consistent accuracy, higher throughput and reduced labor costs. Emerging technologies around machine vision, smart sensors and robotics are driving greater automation in liquid packaging. You can refer to the global forecast for liquid packaging machines
How does the Liquid Pouch Packaging Machine work
Step | Description |
---|---|
1 | Transfer the liquid material to the measuring device through the feeding tube |
2 | Place the packaging material on the bag maker and seal it into an empty bag by the heat sealing device |
3 | Pull the empty bag to the filling port by the traction device and inject the measured liquid material into the bag |
4 | Seal the filled bag by the heat sealing device and print the date, batch number and other information |
5 | Cut the sealed bag by the cutter device and form the finished packaging bag |
6 | Discharge the finished packaging bag through the outlet and collect or transport it to the next process |
How does the Bottle Liquid Filling Machine work
Step | Description |
---|---|
1 | The empty bottles are transferred by the air conveyor to the rinsing-filling-capping 3-in-1 machine by the bottle dialing wheel |
2 | The bottle clamp on the rotary plate of the rinsing machine clamps the bottle mouth and flips it 180°, making the bottle mouth downward |
3 | In a specific area of the rinsing machine, the rinsing nozzle sprays rinsing water to rinse the inner wall of the bottle |
4 | After rinsing and draining, the bottle clamp clamps the bottle mouth along the guide rail and flips it 180°, making the bottle mouth upward |
5 | The cleaned bottles are exported by the bottle dialing wheel from the rinsing machine and transferred to the filling machine |
6 | The bottles entering the filling machine are clamped by the bottle neck plate and lifted by the cam, and then the filling valve is opened by the bottle mouth |
7 | Filling adopts gravity filling method |
8 | After filling, the bottle mouth drops and leaves the filling valve, and the bottle is transferred to the capping machine by the bottle neck transition dialing wheel |
9 | The anti-rotation knife on the capping machine clamps the bottle neck to keep the bottle upright and prevent rotation |
10 | The capping head on the capping machine keeps rotating and revolving, and realizes actions such as cap grabbing, cap covering, capping, and cap releasing under the action of the cam |
11 | The finished bottles are transferred from the capping machine to the outlet conveyor chain by the bottle outlet dialing wheel, and then transported out of the 3-in-1 machine |
How does the Tube Sealing Machine work
Step | Description |
---|---|
1 | Transfer the hose to the filling and sealing machine by the conveyor belt |
2 | Use the photoelectric sensor to detect the hose position and orientation |
3 | Use the manipulator to grab the hose and insert it into the filling and sealing station |
4 | Use the piston pump or peristaltic pump to fill the liquid material into the hose according to the preset volume |
5 | Use the heating device to seal the hose tail by folding, crimping or ultrasonic welding |
6 | Use the inkjet printer or embossing device to print the date, batch number and other information on the hose tail |
7 | Use the manipulator to take out the finished hose and transfer it to the next process or collect it |
Maintenance and Troubleshooting Tips for Liquid Packaging Machinery
Proper maintenance and quick troubleshooting keep liquid packaging machines running optimally. Have procedures in place for preventative maintenance and inspect machines for issues like clogs, leaks and bubbles in the fill. Keep spare parts on hand for quick repairs.
you can check the maintenance file below
Maintenance detail for premade pouch fill&seal packaging machine
Maintenance detail for your VFFS packaging machine?
How to Choose the Right Liquid Packaging Machinery for Your Business
Several factors must be considered when selecting the right liquid packaging machinery for your needs:
Production capacity: How many bottles, pouches or tubes do you need to fill per minute? Match your required output with the machine’s fill speed.
Product type: Liquid types range from water to syrup to viscous lotions. Choose a machine compatible with your specific product.
Packaging material: Glass or plastic bottles? Pouches or tubes? Ensure the machine can handle your packaging materials.
Budget: Consider your budgetary constraints to narrow options to affordably meet your needs.
ROI: Calculate the machine’s return on investment potential based on factors like increased output and labor savings. Aim for an ROI period of 1-3 years. Get your FREE Packaging Equipment ROI Calculator
Supplier: Work with a reputable packaging machinery company that can provide the right machine for your application and offer support over the lifetime of the equipment.
Conclusion
Selecting the appropriate liquid packaging machinery for your specific production needs, product types, and budgetary constraints is essential for a successful packaging operation. Work closely with a trusted supplier to evaluate options based on your requirements and goals. if you have any questions,do not hesitate to contact us