Have you ever wished you could just try out a new automation solution before you bought it? This is the idea behind virtual commissioning… and it may be the future of automation.
With virtual commissioning, you create a virtual model of your ideal automation solutions. You can test out those solutions, tweak them, and see how the automation technology will work with your specific process.
Commissioning any automation solution can be a complex and time-consuming process. With virtual commissioning, you can use robotic simulation technology to reduce both that complexity and the time. It avoids unnecessary downtime because you don’t have to take your existing machines offline to test the automation solution.
It seems likely that virtual commissioning will remain a core step in the automation process from now on. If you are looking for a way to streamline your deployment process, this option may be the answer.
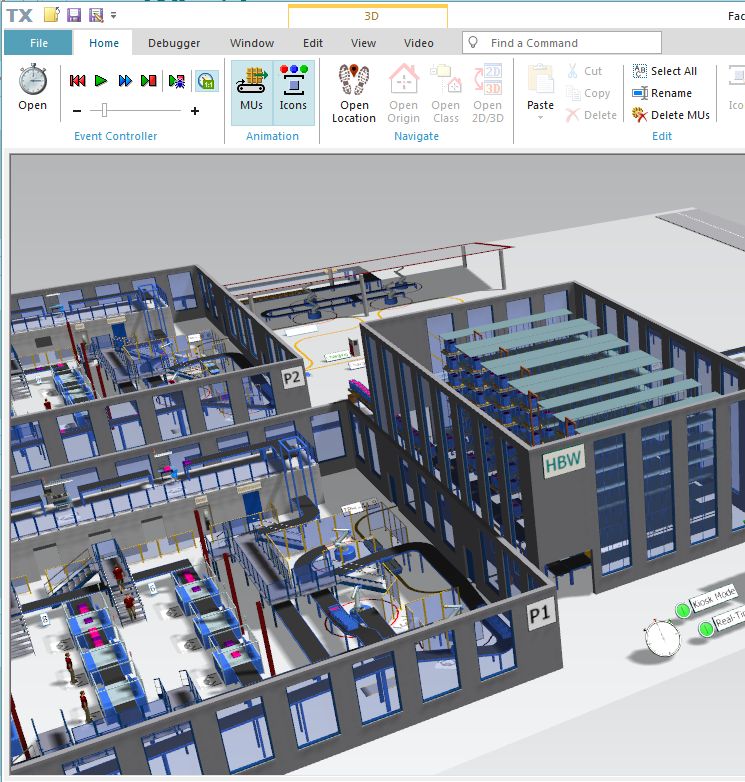
What is Virtual Commissioning?
Virtual commissioning is the use of simulation technology to design, install, and test automation solutions before deploying the physical hardware into a manufacturing environment. For example, robotic simulation software can optimize a robot’s deployment without unnecessary downtime.
At the center of any virtual commissioning project is the simulation software. This software will include virtual models of any automation technology that might be used, as well as algorithms and functionality to test the operation of your system.
With robotic solutions, you can use the same simulation software to program the physical robot. RoboDK includes both simulation and offline programming functionalities. Once you have finished testing your deployment in the simulator, you can connect your physical robot and download the program directly to the robotic hardware.
The Difference Between Virtual and Traditional Commissioning
Is virtual commissioning really that different from traditional commissioning?
There are a few key differences between the two approaches to commissioning an automation project.
Traditional commissioning typically occurs on-site at the physical location where you will deploy the automation solution, such as your factory floor. You bring various physical tools and testing equipment for manual troubleshooting. This means that you may have to shut down some or all of your existing manufacturing processes for the duration of the commissioning project, which can be costly.
With virtual commissioning, you perform most of the deployment remotely, only coming on site at the very end.
Also, the traditional commissioning process often takes longer and requires a larger team for on-site implementation. With virtual commissioning, a small team or even a single person can do most of the deployment remotely.
How Does Virtual Commissioning Work?
The basic idea is to create a simulation or digital twin of your automation solution. This is a virtual model showing how the machine (or machines) will work in your process.
You use this virtual model to test out different scenarios to see how this will affect the automation solution. This helps you to optimize the solution before you take it to the physical environment.
Virtual commissioning with a robot simulator involves:
- Creating or importing virtual models of the relevant parts of your production line.
- Loading models of your robot from the Robot Library, along with any other equipment.
- Creating a robot program for your specific application.
- Optimizing the various aspects of your robotic solution before deploying it to your factory floor.
By approaching commissioning in this way, you can test your solution in a controlled, risk-free environment.
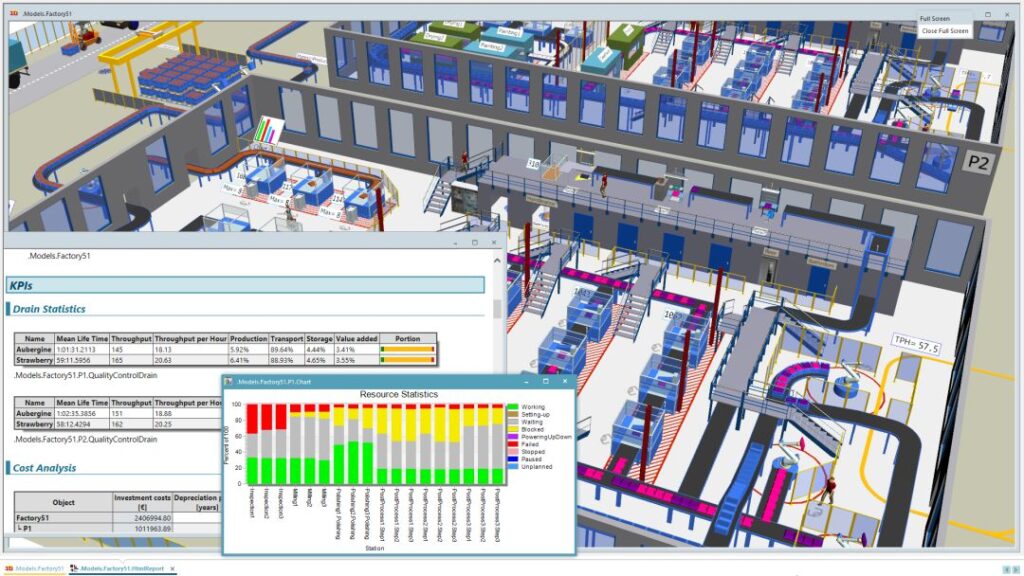
5 Unique Benefits of Virtual Commissioning
Here are 5 unique benefits of virtual commissioning:
1. Efficient Deployments
As virtual commissioning significantly reduces the need for time-consuming on-site activities, it improves the operational efficiency of your deployment. This helps you avoid costly downtime and makes your process more efficient overall.
2. Safer Automation
By simulating your automation project in a virtual environment, you can test potential hazards in a safe and controlled way. This helps you to avoid accidents and injuries that may occur in a traditional physical commissioning process. It also allows you to test hazardous limit cases that would be impossible to test with physical hardware.
3. Improved Team Communication
A simulator can provide a common platform for all your team members to view, understand, and suggest changes to your automation solution. This can help to improve communication and avoids potential misunderstandings. With RoboDK for Web, your colleagues don’t even need to install the software to view the simulation.
4. Flexibility to Changes
One significant benefit of virtual commissioning is that it is easy to make changes or adjustments to your production process. You can quickly test new ideas in the simulator, safely knowing that you are not disrupting your production.
5. Better Understanding of the Solution
Finally, developing your automation solution in a simulator allows you to better understand how it works. By “playing” with the technology in the virtual environment, you will quickly gain a working knowledge of its possibilities and limitations. This helps you make better use of the technology in the real world.
Will Virtual Commissioning Change Automation?
With the ever-increasing popularity of digital tools, it seems likely that virtual commissioning is here to stay.
Virtual commissioning helps to break down the entry barriers to automation that have restricted robot adoption for many manufacturers. It can allow anyone to quickly and efficiently deploy automation technologies to their manufacturing processes while reducing the risks associated with unnecessary downtime.
When you deploy your robotic technology with virtual commissioning, you increase your chances that the automation project will be a success. This makes robotics less risky as a solution and more valuable.
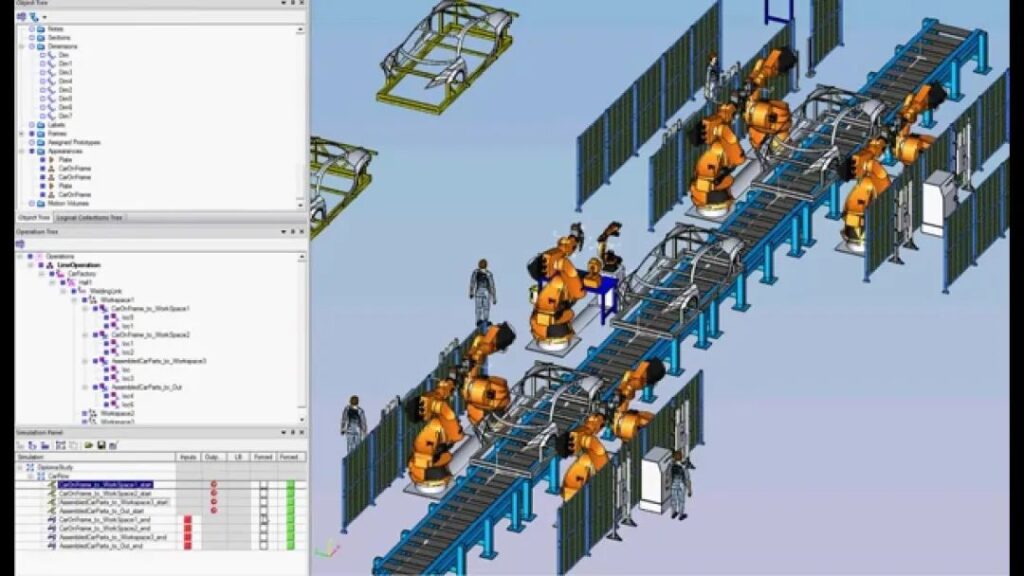
Technology trends in pharma facility design and engineering
Pharma manufacturing is continually evolving in step with advances in technology, as companies seek to reduce costs, fully optimize resources, and streamline operations. This extends to the design and engineering of facilities. This article explores several emerging technology trends relating to facility design and engineering that significantly benefit pharma companies.
Virtual commissioning
The construction and commissioning of new pharma facilities are time and cost intensive. PhRMA estimates that building a new facility can cost up to $2 billion and take anywhere from 5 to 10 years to complete. With this in mind, it’s critical every step in the commissioning and construction process is executed smoothly, efficiently, and cost-effectively so that operations are onstream and generate a return on investment as quickly as possible.
Often a significant part of that cost in terms of time and capital comes directly from facility, line, and equipment commissioning. Late-stage changes or delays to the facility or equipment design, requirements, and configurations must be minimized or ideally, eliminated completely to reduce the overall cost of facility commissioning. To solve this, pharma manufacturers can look to virtual commissioning, an approach that combines traditional and virtual development and testing using emulation. Unlike physical commissioning, virtual commissioning can commence long before any hardware is purchased or constructed. This approach enables savings of up to 40% in commission time compared to conventional commissioning, reducing risk and uncertainty, offering increased safety and agility, and reducing costs for design changes.
Simulation, emulation and digital twins
A digital twin is a virtual representation of a real-world physical entity, system, or process that is synchronized with the physical entity. The digital twin and the observable manufacturing element (OME) are typically synchronized through propagating the sensor data from the physical entity to the digital twin. Digital twins can be built of either simulations or emulations but are required to have synchronization with the OME. The frequency and fidelity of the synchronized emulations/simulations must be appropriate for the task they are designed to accomplish.
Digital twins can be built from several different commercial or open-source software packages but always include the physical element, a synchronization mechanism, and a software package used that runs the model/virtual representation (usually derived from CAE/multiphysics software). Creating a digital twin requires that elements of interest for the OME be accurately replicated in the virtual representation. For production equipment, this typically involves the definition of process or mechatronics systems, including motors, actuators, instrumentation, connected to an automation system running application specific software.
The value of implementing digital twins with production equipment is the potential to estimate the state of the physical system beyond what is immediately observable. Typical applications of this include soft-sensing, adaptive fault correction, model-predictive control, and predictive maintenance. Production equipment can fit into a larger digital twin of an entire manufacturing process to support demand driven on-time manufacturing.
In virtual commissioning applications, a digital twin may not be possible since the physical equipment may not exist. Instead, a model of the production equipment is deployed alongside the control system, so that the two can be co-developed. The control system considers the production equipment model an emulation, since the control system can interact naturally with the model through command outputs and status feedback (known as Hardware-In-the-Loop). For this technique to be successful, the production equipment model needs to accurately represent the concrete behavior of the physical system.
Emulation-based virtual commissioning leads to a valuable reduction in project risk from the perspectives of error avoidance and achieving project timelines. As scenarios and design choices can be thoroughly tested without physical equipment, engineers can test and verify various system elements including application-specific software modules, recipe configuration, failure modes and recovery, and user interface efficacy without depending on scheduled test equipment or being on-site. As a result, projects which employ virtual commissioning are often deployed with less in-person commissioning time and are generally safer for people and property.
Once the equipment is commissioned and validated, the emulation from virtual commissioning can continue its use as the digital twin synchronized to the physical equipment. Since the model is already constructed, it is immediately useful as an idealized representation of the physical system. Engineers can use this digital twin to optimize facility design, system design, production line operations, and plant and machinery requirements, among other elements.
Infrastructure-as-code
From an IT/OT convergence angle, virtual commissioning enables the use of agile IT concepts to develop processes such as infrastructure-as-code in the OT space, the goal being to move towards the automation of code development and infrastructure configuration.
The adoption of these IT concepts will fundamentally change the workflows of OT engineers. Instead of building systems and code from scratch, as was the case with legacy distributed control systems (DCS), the process will look a lot more like an agile software development role, with engineers focusing more on maintaining the automated software systems than developing the application code and infrastructure. For end users, this could mean that the arduous tasks of installing, configuring, and patching infrastructure for control systems would become an automated workflow. For machine builders, this could result in an order processing system that sends a configuration to dynamically build automation infrastructure and application code to order based on the options selected by the customer without an engineer involved.
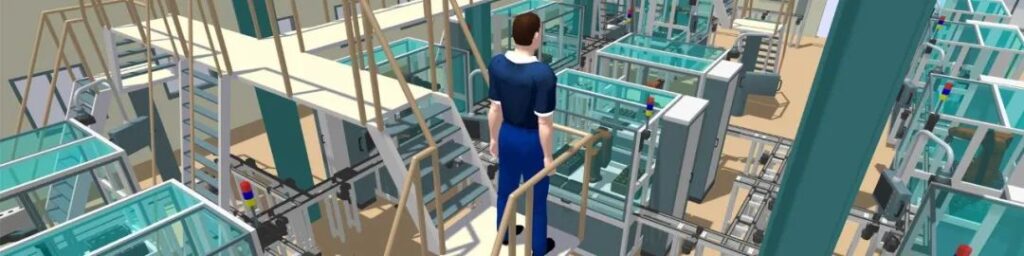
OEM equipment orchestration
OEM equipment forms the foundation of modern modular pharmaceutical manufacturing plants by providing the flexibility to choose and combine the best equipment solutions for specific processes. Commissioning and validating OEM equipment is generally a faster process as manufacturers receive pre-assembled, purpose-programmed units. Furthermore, OEMs typically supply equipment in a validation-ready state, making it easy to qualify the equipment for use in CGMP facilities. There is no need to rely on internal resources or third parties for equipment construction and application code development. However, challenges can arise from different connectivity standards and interfaces among various equipment vendors, making it difficult to integrate multiple pieces of equipment into a unified control system. This is where OEM equipment orchestration comes into play.
The need for an orchestration strategy
Without a strategic approach and clear specifications, the use of OEM equipment results in fragmented islands of automation. This lack of a strategy is usually due to late collaboration with equipment vendors on the part of the end user. When automation is not considered in the initial equipment procurement process, engineers often struggle to integrate equipment or rely on engineering firms to handle the integration. This late-stage process of piecing equipment together as an afterthought can lead to limited interface capability within the plant at best. At worst, the whole process can backfire by being time-consuming and costly for no increase in digital maturity.
To solve these issues, pharma manufacturers can adopt a holistic plan for OEM equipment orchestration to automate and coordinate various components to work seamlessly together early in the facility specification and design phases. Having comprehensive standards established before any equipment is purchased allows an end user to work collaboratively with their equipment vendors, giving the OEM the opportunity to differentiate themselves on how their equipment can fit into a unified automation platform. For the end user, this simplifies cross-training and standardizes interfaces, alert systems, diagnostics, and recipe management. This reduces costs, streamlines operations, and results in faster construction, commissioning, and facility qualification.
Leveraging standardized interfaces
End users are demanding OEM equipment that comes with plug-and-produce capability to integrate with any distributed control system (DCS) or Supervisory Control and Data Acquisition (SCADA) system. This plug-and-produce capability standardizes core automation services such as equipment interfaces and recipe management, user interface screens, audit trails, and alarm management across disparate equipment. A plug-and-produce standard systematically connects all these elements and coordinates them using standardized interfaces, like the NAMUR module type package (MTP) and modern protocols, like OPC Unified Architecture(OPCUA). Integrating all these disparate platforms together brings consistency, saves time and effort on integration, and makes plug-and-produce a feasible technology for facilities of the future.
These technologies should be viewed as an augmentation to a cohesive strategy for OEM orchestration rather than replacing all the work done with collaboration between organizations and comprehensive specifications. No magic button exists to integrate equipment together seamlessly to deliver common sets of services and the end user’s constructive relationships with their equipment and technology vendors play a big part in an effective OEM orchestration strategy. Think about this situation, a plant built entirely with black box equipment with a standardized interface might be fast to integrate but would be difficult and costly for an end user to support long term due to managing numerous support contracts, disparate spare parts, and a lack of consistency in or even access to application software on the OEM equipment.
A multitude of benefits
Put simply, the orchestration of OEM equipment facilitates the work of creating a unified automation platform for a facility. This ultimately leads to a faster time to market and lower total cost of ownership for the end user. Effective orchestration enables the integration of different OEM components in a way that allows for easy customization and scalability, new equipment addition into existing systems, and seamless integration of future upgrades and expansions. Downtime and Mean Time To Repair (MTTR) are reduced through simplified troubleshooting and maintenance.
Advanced therapy medicinal products
Another emerging trend relating to facility engineering is the change of industrial automation to fit into the advanced therapy medicinal products (ATMP) space. Many of these therapies are autologous, meaning they’re sourced from a person and then fed back to the same person. The production volumes for these autologous therapies are very small, often in milliliters. Existing automation systems are designed to produce at larger scales, so the concept here is to miniaturize the automation technologies to run on bench-top units or instruments. These bench-top units can then be orchestrated into a coordinated process train to make the therapy, with the process scaling out to accommodate more process trains for more individual patients.
The key to success for this strategy is going to be in the automation vendor’s willingness to scale down their technology to offer the same commercial off-the-shelf software and hardware capabilities for bench-top equipment. This will be vital to limit the amount of rework necessary for the tech transfer from the process development (PD) space to cGMP manufacturing for these advanced therapies. Collaboration with an automation vendor who has the ability to scale down and operate flexibly across these disparate trains of industrial and laboratory equipment to ensure accuracy and patient safety is crucial.
From inception to completion
Pharma companies are actively adopting technologies to enhance productivity, efficiency, and return on investment and maintain a competitive edge. Initiatives like virtual commissioning and OEM equipment orchestration are being embraced to expedite the introduction of new capacity and capabilities, as well as optimize facility operations to eventually reach an adaptive facility.
Utilizing virtual commissioning, facilities can be designed, modeled, engineered and tested before physical work begins. This approach enables the optimization of various aspects such as layout, productivity, throughput, flow and energy efficiency. The orchestration of OEM equipment automates processes and standardizes interfaces, which facilitates the work of creating a unified automation platform for a facility that will ultimately lead to a faster time to market and lower total cost of ownership for the end user.
Pharma companies that leverage the power of new technologies will be better equipped to optimize facility processes from inception to completion.
Conclusion
Virtual commissioning stands at the forefront of technological advancements in automation, offering a transformative approach for industries aiming to integrate automation solutions more effectively. By leveraging simulation technology, virtual commissioning enables businesses to design, test, and refine automation systems in a digital environment before physical implementation. This process not only enhances efficiency and safety but also fosters better team collaboration and adaptability to changes, ensuring a comprehensive understanding of the solution’s capabilities and limitations.
The distinction between virtual and traditional commissioning underscores the advancements and efficiencies gained through digital simulations. Virtual commissioning minimizes the need for extensive on-site activities, reduces the risks associated with physical testing, and accelerates the deployment process, making it a pivotal strategy for industries looking to adopt automation technologies.
With the increasing integration of digital tools in manufacturing and the continuous evolution of simulation software, virtual commissioning is poised to become an integral component of automation projects. It breaks down barriers to automation adoption by mitigating risks and reducing downtime, thus democratizing access to advanced manufacturing technologies.
As industries continue to navigate the challenges of adopting new technologies, the role of virtual commissioning in facilitating a smoother, safer, and more cost-effective integration of automation solutions cannot be overstated. It is a testament to the power of digital transformation in manufacturing, offering a glimpse into a future where virtual and physical realms converge to optimize production processes and drive innovation.
Thanks for Alex Owen-Hill and John Hatzis share the idea.