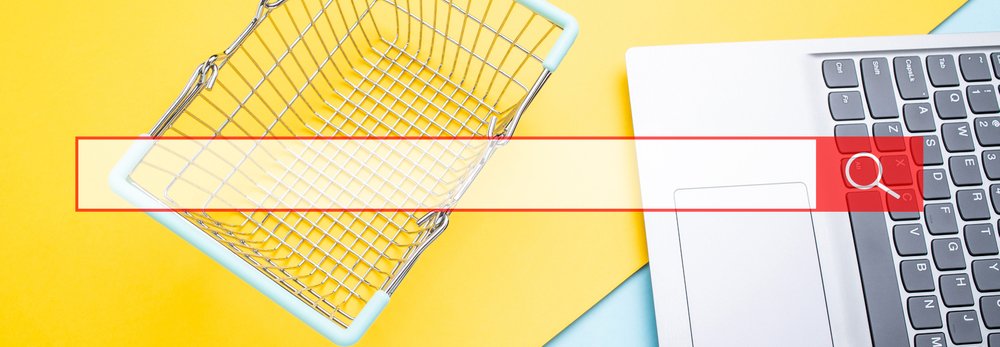
Abstract: The fully automatic shrink packaging machine is a highly automated device widely used in industries such as pharmaceuticals, food and beverages, and household chemicals. Shrink packaging can greatly reduce the use of materials and labour costs associated with box packaging, making it economically significant and essential for diagnosing faults.
Keywords: automatic packaging machine, working principle, fault diagnosis
Automation in the packaging industry is changing the way packaging processes are carried out, including the movement of packaging containers and processing of packaging materials. The design and installation of automated control packaging systems play a significant role in improving product quality, and production efficiency, eliminating processing errors, and reducing labour intensity. The fully automatic shrink packaging machine is a highly automated device that implements an automatic control packaging system, which greatly improves production efficiency and product quality. It is particularly important in industries such as food, beverages, pharmaceuticals, electronics, etc. Shrink film packaging can significantly reduce the use of materials and labour costs associated with box packaging, making it economically significant.
Main Components and Working Principles of Packaging Machine
A complete automated structural solution consists of various components, including end-arm manipulators, material handling devices, and identification and verification systems. The working principles are as follows:
End-arm Manipulators
These are devices connected to the end of a mechanical arm that move from one position to another. End-arm manipulators are used for product gripping, directional movement, and sensing performance parameters. They can be structured as single-type vacuum cups, series-type vacuum cups, or an arrangement of clamping claws. In packaging applications, end-arm manipulators are usually designed to use vacuum cups, clamping claws, or a combination of both.
Material Handling Devices
Material handling and conveying devices are types of equipment required for the transportation, storage, and control of products during transmission and manufacturing processes. They include power conveyors, monorail cranes, automated guided vehicles, and mechanical arms. A typical material handling system includes a belt input conveyor, labelling machinery, barcode readers, automatic devices, and output conveyors. A user-friendly graphical interface provides an easily operable platform for depicting pallet stacking. Depending on the number of controlled production units, the mechanical arm grabs, moves, and places (stacks) each packaging container (box, crate, drum, can, etc.) in the correct pallet position. Factors to consider during material handling and conveying in the packaging process include product shape, weight, and material properties, transportation speed, distance, and direction, required control level when connecting to other devices, and flexibility for component reformation if necessary.
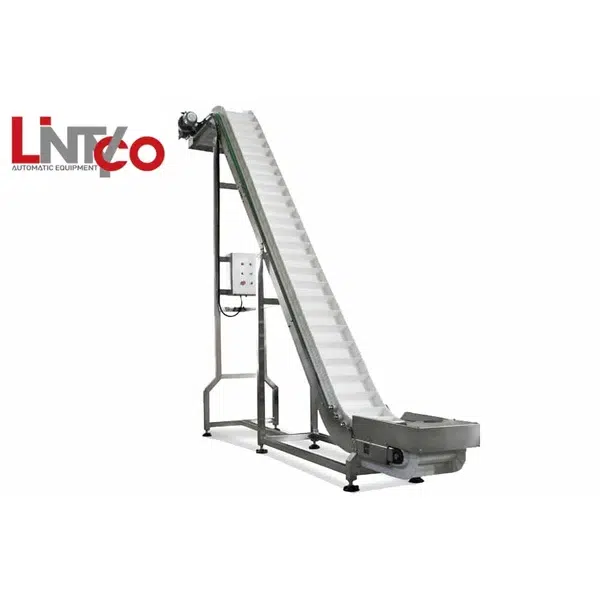
Identification and Verification Systems
The ability to identify, verify, and accurately track products has become an essential part of the entire packaging system. Identification methods can use traditional barcodes or radio frequency (RF) sensors, which can track pallets or individual products. A typical visual barcode detection capability can confirm that each barcode corresponds to each product. Therefore, barcode scanners and video recognition systems record and verify product labels to ensure complete identification. Online barcode printing and verification are also necessary. Vision technology, which provides effective and reliable means to ensure product quality, can be used in various packaging scenarios, such as product inspection and orientation, fill level and counting, optical labelling, text recognition, label copy verification, label recording, and overall text and graphics verification (off the production line). Barcode systems identify products based on product type, date and area codes, and manufacturer names during prepress or inline printing processes.
Common Fault Diagnosis and Troubleshooting
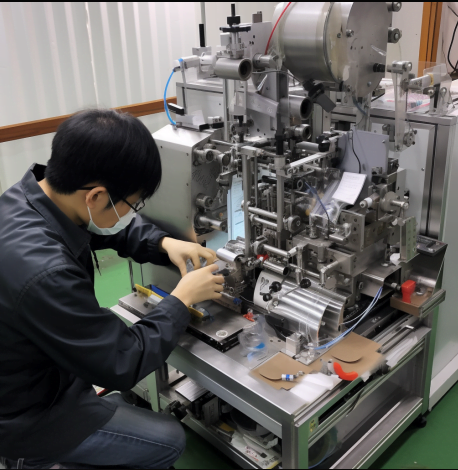
Material Breakage
This fault is often caused by packaging material joints, excessive burrs, faulty paper supply motor circuits, or poor circuit contacts with the paper supply proximity switch.
Troubleshooting:
(1) Remove defective packaging materials.
(2) Check the paper supply motor circuit.
(3) Replace the proximity switch.
Inadequate Bag Sealing
This fault is often caused by uneven inner layers of packaging materials, uneven sealing pressure, or low sealing temperature.
Troubleshooting:
(1) Remove defective packaging materials.
(2) Adjust the sealing pressure.
(3) Increase the heat sealing temperature.
Incorrect Sealing Path
This fault is often caused by the misplacement of the heat sealer.
Troubleshooting: Readjust the position of the heat sealer.
Incorrect Bag Cutting Position or Large Deviation from the Color Mark
Cause: Incorrect positioning of the photoelectric switch (sensor).
Troubleshooting: Readjust the position of the photoelectric switch (sensor).
Uncontrolled Color Mark Alignment and Photoelectric Tracking
This fault is often caused by packaging material joints with seams or rough edges, foreign objects in the forming device causing paper misalignment, packaging material protruding from the guide plate of the photoelectric switch, misalignment of the photoelectric switch’s light spot with the colour mark, poor sensitivity of the photoelectric switch, and incorrect use of brightness and darkness adjustments.
Troubleshooting:
(1) Remove defective packaging materials.
(2) Clean the forming device to ensure smooth paper movement.
(3) Insert the packaging material into the guide plate.
(4) Adjust the left and right position of the guide plate to align the light spot with the colour mark.
(5) Replace the photoelectric switch and select the appropriate brightness and darkness adjustment.
Large Bag Length Deviation When Color Mark Tracking is Not Performed (i.e., when the photoelectric switch is turned off)
This fault is often caused by inappropriate bag length settings, worn-out wheel patterns resulting in reduced friction, and insufficient pressure on the wheels.
Troubleshooting:
(1) Increase the bag length setting to make the actual bag length equal to or slightly longer than the standard length of the color mark.
(2) Replace the wheels.
(3) Increase the pressure on the wheels.
Incomplete Bag Cutting or Partial Cutting Resulting in Connected Bags
This fault is often caused by insufficient pressure between the two cutting blades or dull blade edges.
Troubleshooting:
(1) Adjust the pressure between the cutting blades.
(2) Sharpen or replace the cutting blades.
The paper Supply Motor Does Not Rotate or Keeps Rotating
This fault is often caused by the paper supply control lever getting stuck, damage to the paper supply proximity switch, a damaged startup capacitor, or a blown fuse.
Troubleshooting:
(1) Resolve the issue causing the jam.
(2) Replace the paper supply proximity switch.
(3) Replace the startup capacitor.
(4) Replace the fuse.
Heat Sealer Does Not Heat Up or Temperature Control is Lost
This fault is often caused by damaged heating elements, circuit malfunctions, blown fuses, malfunctioning temperature controllers, or open circuits in the thermocouple.
Troubleshooting:
(1) Replace the heating elements.
(2) Check the circuit.
(3) Replace the fuse.
(4) Replace the temperature controller.
(5) Replace the thermocouple.
Failure to Pull the Bag (Bag-pulling Motor Not Operating)
This fault is often caused by circuit malfunctions, damage to the bag-pulling proximity switch, faults in the automatic packaging machine controller, or driver malfunctions in the stepper motor.
Troubleshooting:
(1) Check the circuit and eliminate any faults.
(2) Replace the bag-pulling proximity switch.
(3) Replace the automatic packaging machine controller.
(4) Replace the stepper motor driver.
Conclusion
To quickly troubleshoot faults in an automatic packaging machine, it is essential not only to understand its structure and working principles but also to identify the root causes of the faults and master a set of troubleshooting methods. This ensures adaptability to various situations and enables efficient fault resolution. Do not hesitate to contact us if you can not deal with
Lintyco is a pioneer and leader in automated filling machines and end-to-end packaging systems. Lintyco’s innovative packaging solutions for food, pharma, and other applications are complemented by advanced solutions for secondary packaging, wrapping & cartoning, bulk packaging, and more. Whether you are looking for a new machine or a complete line, or if you just want to upgrade your current packaging machine, talk to Lintyco. As experts of the industry with over three decades of proven expertise, Lintyco will provide the optimal solution backed by excellent consultancy and support.